Introduction to Custom PCBs
Custom Printed Circuit Boards (PCBs) are designed and manufactured specifically for a particular application or project, rather than being a generic, off-the-shelf solution. These boards offer numerous advantages over standard PCBs, but they also come with certain limitations. In this comprehensive article, we will explore the benefits and drawbacks of custom PCBs to help you make an informed decision for your next electronics project.
Benefits of Custom PCBs
1. Tailored to Specific Requirements
One of the primary advantages of custom PCBs is that they are designed to meet the specific requirements of your project. This means that you can optimize the board layout, component placement, and overall functionality to suit your needs perfectly. Custom PCBs allow for greater flexibility in design, enabling you to incorporate unique features and form factors that may not be possible with standard boards.
2. Improved Performance and Reliability
Custom PCBs are engineered with your specific application in mind, which often leads to improved performance and reliability compared to generic boards. By carefully selecting materials, components, and layout techniques, you can minimize signal interference, reduce power consumption, and enhance thermal management. This results in a more robust and efficient system that is less prone to failures and downtime.
3. Cost-Effective for Large-Scale Production
While custom PCBs may have higher upfront costs due to design and setup fees, they can be highly cost-effective for large-scale production runs. By optimizing the board layout and component selection, you can reduce material costs and minimize assembly time. Additionally, custom PCBs can be designed to fit into existing enclosures or systems, eliminating the need for costly modifications or adaptations.
4. Intellectual Property Protection
Custom PCBs offer a level of intellectual property protection that is not possible with standard, off-the-shelf boards. By designing your own PCB, you can keep critical aspects of your technology confidential and prevent competitors from easily replicating your product. This is particularly important for innovative or proprietary applications where maintaining a competitive edge is crucial.
5. Reduced Size and Weight
Custom PCBs can be designed to minimize size and weight, which is essential for applications where space is limited or portability is a concern. By carefully selecting components and optimizing the layout, you can create compact and lightweight boards that meet your specific requirements. This is particularly beneficial for wearable devices, mobile electronics, and aerospace applications.
Limitations of Custom PCBs
1. Higher Upfront Costs
One of the main drawbacks of custom PCBs is the higher upfront costs associated with design and setup. Creating a custom board requires specialized knowledge and tools, which can be expensive. Additionally, manufacturers often charge setup fees for custom orders, as they need to configure their production lines specifically for your design. These costs can be prohibitive for small-scale projects or prototypes.
2. Longer Lead Times
Custom PCBs typically have longer lead times compared to standard, off-the-shelf boards. The design, review, and manufacturing process can take several weeks or even months, depending on the complexity of the board and the manufacturer’s workload. This can be a significant disadvantage for projects with tight deadlines or rapidly evolving requirements.
3. Minimum Order Quantities
Many PCB manufacturers impose minimum order quantities (MOQs) for custom boards, which can be a challenge for small businesses or individual makers. MOQs can range from a few dozen to several thousand units, depending on the complexity of the design and the manufacturer’s policies. This can result in excess inventory and tied-up capital, particularly for projects with uncertain demand.
4. Design Complexity and Expertise
Designing a custom PCB requires specialized skills and knowledge in electronics, PCB layout, and manufacturing processes. This can be a steep learning curve for those without prior experience, and mistakes in the design phase can lead to costly revisions and delays. Even for experienced designers, complex boards with high-speed signals, dense component placement, or advanced features can be challenging to create and optimize.
5. Limited Flexibility for Changes
Once a custom PCB design is finalized and sent for manufacturing, making changes can be difficult and expensive. Any modifications to the layout, component selection, or functionality may require a new set of prototypes and a revised manufacturing setup. This lack of flexibility can be a hindrance for projects with evolving requirements or unexpected issues discovered during testing.
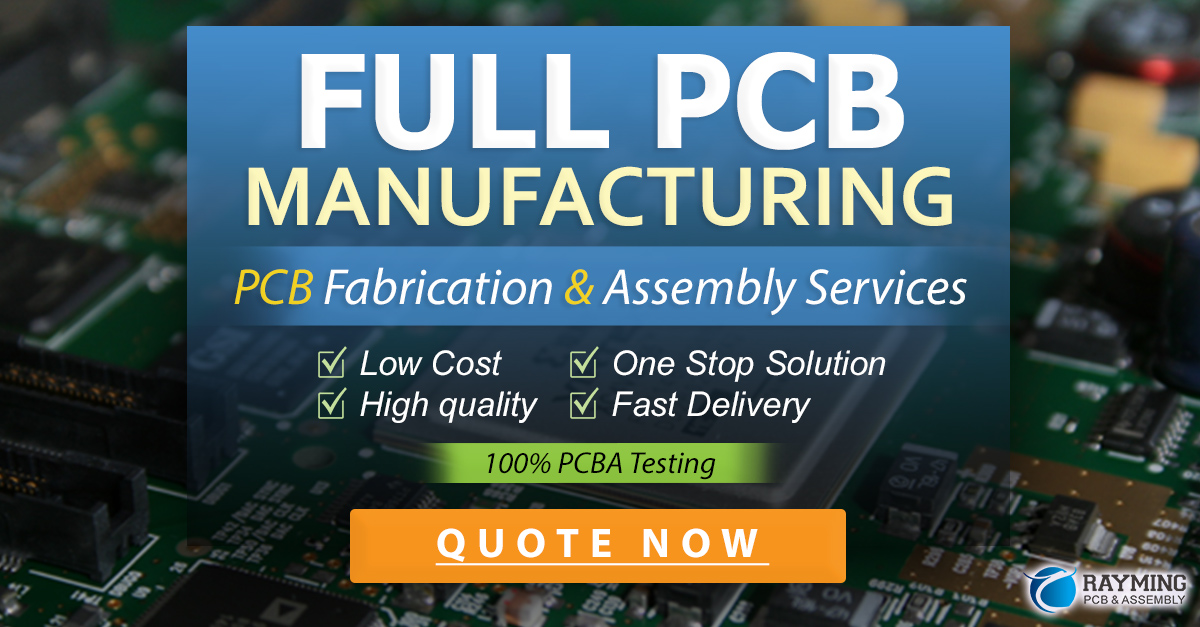
Comparison Table: Standard PCBs vs. Custom PCBs
Feature | Standard PCBs | Custom PCBs |
---|---|---|
Design Flexibility | Limited | High |
Performance | Average | Optimized |
Cost (Small-Scale) | Lower | Higher |
Cost (Large-Scale) | Higher | Lower |
Intellectual Property | Not Protected | Protected |
Size and Weight | Fixed | Customizable |
Upfront Costs | Lower | Higher |
Lead Times | Shorter | Longer |
Minimum Order Quantity | Lower | Higher |
Design Complexity | Lower | Higher |
Flexibility for Changes | Higher | Lower |
Frequently Asked Questions (FAQ)
1. When should I consider using a custom PCB?
Consider using a custom PCB when your project has specific requirements that cannot be met by standard, off-the-shelf boards. This may include unique form factors, high-performance demands, or proprietary features. Custom PCBs are also a good choice for large-scale production runs where optimizing costs and efficiency is crucial.
2. How much does it cost to design and manufacture a custom PCB?
The cost of designing and manufacturing a custom PCB varies widely depending on factors such as board complexity, materials, components, and order quantity. Design costs can range from a few hundred to several thousand dollars, while manufacturing costs can vary from a few dollars to hundreds of dollars per board. It’s essential to obtain quotes from multiple manufacturers and carefully consider your project’s budget and requirements.
3. What are the typical lead times for custom PCBs?
Lead times for custom PCBs can range from a few days to several months, depending on the complexity of the design, the manufacturer’s workload, and the order quantity. Simple boards with standard materials and features may have lead times of 1-2 weeks, while complex, high-density boards with specialized requirements can take 8-12 weeks or more. It’s important to communicate your timeline and requirements clearly with your chosen manufacturer to ensure a smooth and timely production process.
4. Can I design a custom PCB myself, or do I need to hire a professional?
Designing a custom PCB requires specialized skills and knowledge in electronics, PCB layout, and manufacturing processes. While it is possible to learn and do it yourself, the learning curve can be steep, and mistakes can be costly. If you have limited experience or are working on a complex, high-stakes project, it may be advisable to hire a professional PCB designer to ensure the best possible results.
5. How do I choose the right manufacturer for my custom PCB project?
When choosing a manufacturer for your custom PCB project, consider factors such as experience, capabilities, quality control processes, and customer support. Look for manufacturers with a proven track record in your specific industry or application, and request references or case studies to gauge their expertise. Obtain quotes from multiple manufacturers and carefully review their terms, conditions, and delivery timelines. Finally, ensure that your chosen manufacturer has robust quality control processes in place and offers reliable customer support to address any issues that may arise during the production process.
Conclusion
Custom PCBs offer numerous benefits, including tailored design, improved performance, cost-effectiveness for large-scale production, and intellectual property protection. However, they also come with certain limitations, such as higher upfront costs, longer lead times, minimum order quantities, design complexity, and limited flexibility for changes.
When deciding whether to use a custom PCB for your project, carefully consider your specific requirements, budget, timeline, and long-term goals. If your application demands high performance, unique features, or large-scale production, a custom PCB may be the best choice. However, if you have limited resources, tight deadlines, or evolving requirements, a standard PCB may be a more suitable option.
By understanding the benefits and limitations of custom PCBs, you can make an informed decision that balances your project’s needs with practical considerations. With careful planning, skilled design, and a reliable manufacturing partner, custom PCBs can help you create innovative, efficient, and successful electronic products.
Leave a Reply