What is Wave Soldering?
Wave soldering is a bulk soldering process used in the production of PCBs. In this process, a PCB is passed over a molten solder wave, which solders the electronic components to the board. The solder wave is created by pumping molten solder through a nozzle, forming a standing wave of solder. The PCB is then passed over this wave, allowing the solder to come into contact with the components and the board, creating a strong electrical and mechanical bond.
The Wave Soldering Process
The wave soldering process consists of several steps:
- Flux Application: A flux is applied to the PCB to remove oxides and improve the wettability of the solder.
- Preheating: The PCB is preheated to activate the flux and prevent thermal shock when it comes into contact with the molten solder.
- Soldering: The PCB is passed over the solder wave, allowing the molten solder to come into contact with the components and the board.
- Cooling: The PCB is cooled to allow the solder to solidify and form a strong bond between the components and the board.
- Cleaning: Any excess flux or solder is removed from the PCB using a cleaning agent.
Advantages of Wave Soldering
Wave soldering offers several advantages over other soldering methods:
- Efficiency: Wave soldering is a fast and efficient process that can solder a large number of components to a PCB in a short amount of time.
- Reliability: Wave soldering produces consistent and reliable solder joints, ensuring a high-quality finished product.
- Cost-Effective: Wave soldering is a cost-effective method of soldering, as it requires less manual labor and can produce a large number of PCBs quickly.
Disadvantages of Wave Soldering
Despite its advantages, wave soldering also has some disadvantages:
- Limited Flexibility: Wave soldering is not suitable for all types of components, especially those that are sensitive to heat or have a low profile.
- Solder Bridges: Wave soldering can sometimes result in solder bridges, which are unwanted connections between two or more solder joints.
- Thermal Shock: The sudden change in temperature during the soldering process can cause thermal shock, which can damage the components or the PCB.
Choosing a Wave Soldering PCB Assembly Company
When choosing a wave soldering PCB assembly company, there are several factors to consider:
Experience and Expertise
It is important to choose a company with extensive experience and expertise in wave soldering PCB assembly. Look for a company that has been in business for several years and has a proven track record of producing high-quality PCBs.
Equipment and Technology
The equipment and technology used by the company can greatly impact the quality of the finished product. Look for a company that uses state-of-the-art equipment and technology to ensure the highest quality PCBs.
Quality Control
Quality control is crucial in the production of PCBs. Look for a company that has a strict quality control process in place to ensure that each PCB meets the highest standards of quality.
Customer Service
Good customer service is essential when working with a wave soldering PCB assembly company. Look for a company that is responsive to your needs and provides excellent communication throughout the manufacturing process.
Pricing
Pricing is always a consideration when choosing a wave soldering PCB assembly company. However, it is important to remember that the lowest price may not always be the best option. Look for a company that offers competitive pricing while still maintaining high standards of quality and customer service.
Top Wave Soldering PCB Assembly Companies
There are many wave soldering PCB assembly companies to choose from, but some stand out from the rest. Here are a few of the top wave soldering PCB assembly companies:
Company | Location | Years in Business | Specialties |
---|---|---|---|
Sunstone Circuits | Oregon, USA | 50+ | Prototype and low-volume PCBs |
Sierra Circuits | California, USA | 30+ | High-density interconnect (HDI) PCBs |
PCBWay | Shenzhen, China | 10+ | Low-cost, high-quality PCBs |
Advanced Circuits | Colorado, USA | 30+ | Quick-turn PCBs |
Seeed Studio | Shenzhen, China | 10+ | Open-source hardware and PCBs |
These companies have a proven track record of producing high-quality PCBs using wave soldering and other manufacturing techniques.
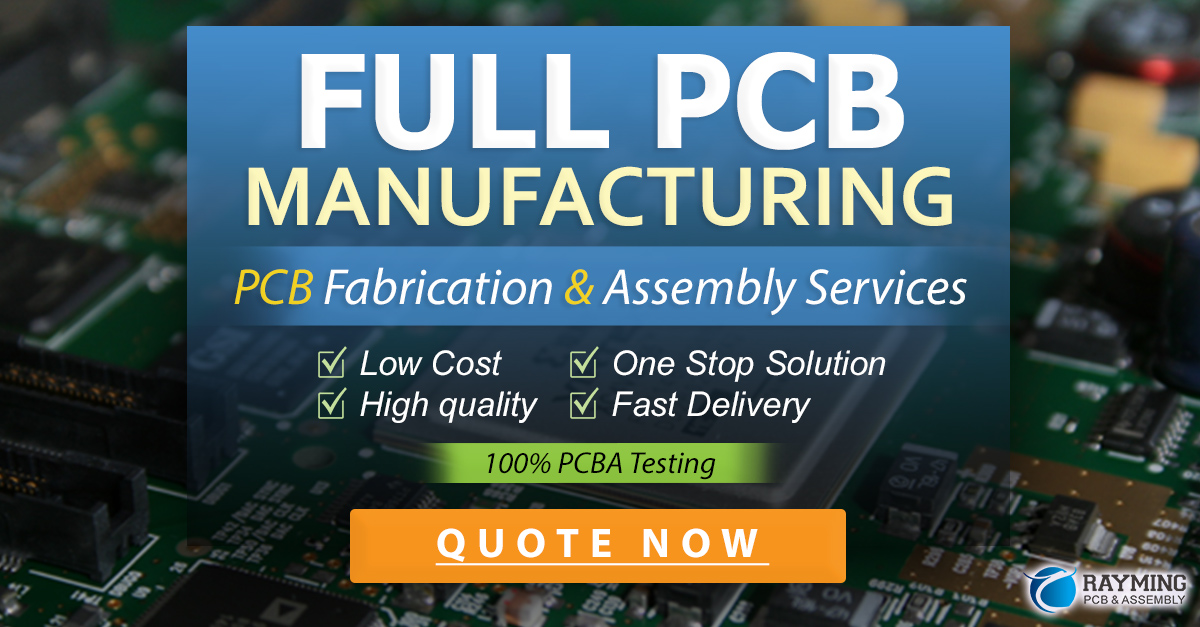
Frequently Asked Questions (FAQ)
1. What is the difference between wave soldering and reflow soldering?
Wave soldering is a bulk soldering process that involves passing a PCB over a molten solder wave, while reflow soldering involves applying solder paste to the PCB and then heating it in an oven to melt the solder and bond the components to the board.
2. Can wave soldering be used for surface mount components?
Yes, wave soldering can be used for surface mount components, but it requires specialized equipment and techniques to ensure that the components are properly soldered to the board.
3. How long does the wave soldering process take?
The wave soldering process typically takes a few minutes per PCB, depending on the size and complexity of the board.
4. What kind of flux is used in wave soldering?
The most common types of flux used in wave soldering are water-soluble flux and no-clean flux. Water-soluble flux requires cleaning after soldering, while no-clean flux does not.
5. How can I ensure the quality of my PCBs when using a wave soldering PCB assembly company?
To ensure the quality of your PCBs, choose a reputable company with experience and expertise in wave soldering PCB assembly. Look for a company that uses state-of-the-art equipment and technology, has a strict quality control process in place, and provides excellent customer service.
Conclusion
Wave soldering is a crucial process in the manufacturing of PCBs. It is a fast, efficient, and cost-effective method of soldering electronic components to a PCB. When choosing a wave soldering PCB assembly company, it is important to consider factors such as experience and expertise, equipment and technology, quality control, customer service, and pricing. By choosing a reputable company with a proven track record of producing high-quality PCBs, you can ensure that your PCBs are manufactured to the highest standards of quality and reliability.
Leave a Reply