Table of Contents
- Introduction
- Bare Board Testing
- Continuity Test
- Isolation Test
- Resistance Test
- In-Circuit Testing (ICT)
- Analog In-Circuit Testing
- Digital In-Circuit Testing
- Advantages and Disadvantages of ICT
- Functional Testing
- Types of Functional Testing
- Boundary Scan Testing
- e-Testing“>Flying Probe Testing
- Burn-In Testing
- Automated Optical Inspection (AOI)
- X-Ray Inspection
- Frequently Asked Questions (FAQ)
- Conclusion
Introduction
PCB Electrical Tests are crucial in ensuring that the manufactured PCBs meet the required specifications and function as intended. These tests can be performed at various stages of the manufacturing process, from the bare board stage to the final assembly stage. By conducting these tests, manufacturers can identify and rectify issues early in the process, reducing the risk of product failures and recalls.
Bare Board Testing
Bare board testing is performed on the PCB before any components are mounted. This type of testing ensures that the PCB’s copper traces, vias, and pads are properly connected and insulated. The three main tests performed during bare board testing are:
Continuity Test
A continuity test verifies that all the intended connections on the PCB are present and that there are no unintended short circuits between traces. This test is typically performed using a specialized Continuity Tester or a multimeter.
Isolation Test
An isolation test checks for any unintended connections or leakage between copper traces that should be electrically isolated from each other. This test helps identify potential short circuits that could cause the PCB to malfunction.
Resistance Test
A resistance test measures the resistance of the PCB’s copper traces to ensure that they meet the specified values. This test helps identify any traces that are too thin or too thick, which could lead to performance issues or even failure of the PCB.
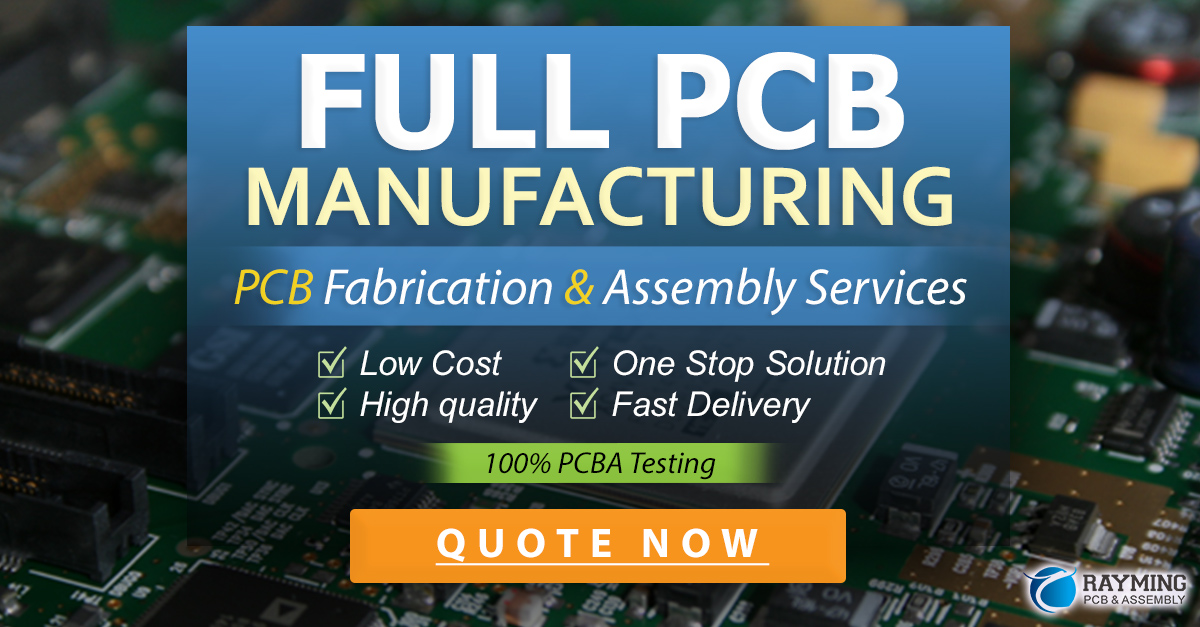
In-Circuit Testing (ICT)
In-circuit testing is performed after the components have been mounted on the PCB. This type of testing verifies that each component on the PCB is functioning correctly and is properly connected to the circuit. ICT can be divided into two categories:
Analog In-Circuit Testing
Analog ICT focuses on testing the analog components on the PCB, such as resistors, capacitors, and inductors. This test measures the components’ values and compares them to the expected values specified in the design.
Digital In-Circuit Testing
Digital ICT tests the digital components on the PCB, such as integrated circuits and microprocessors. This test verifies that the components are functioning correctly and that the signals between them are being transmitted and received as expected.
Advantages and Disadvantages of ICT
Advantages | Disadvantages |
---|---|
Early detection of component and assembly issues | Requires specialized and expensive test equipment |
High fault coverage | Test fixture development can be time-consuming |
Automated testing process | Limited access to components due to PCB layout and size |
Detailed diagnostic information | May not detect all functional defects |
Functional Testing
Functional testing is performed on the fully assembled PCB to verify that it functions as intended in its final application. This type of testing simulates real-world operating conditions and checks the PCB’s performance, functionality, and compatibility with other components in the system.
Types of Functional Testing
There are several types of functional testing, including:
- Power-on testing: Verifies that the PCB powers on and initializes correctly.
- Firmware testing: Checks the functionality of the PCB’s firmware and ensures that it meets the specified requirements.
- Connectivity testing: Verifies that the PCB communicates correctly with other components in the system, such as sensors, displays, or external devices.
- Environmental testing: Subjects the PCB to various environmental conditions, such as temperature, humidity, and vibration, to ensure that it functions correctly under these conditions.
Boundary Scan Testing
Boundary scan testing, also known as JTAG (Joint Test Action Group) testing, is a type of functional testing that uses a built-in test architecture to test the interconnections between digital components on the PCB. This test method allows for the verification of the PCB’s functionality without requiring physical access to the components.
Flying Probe Testing
Flying probe testing is an alternative to ICT that uses movable test probes to make contact with the PCB’s test points. This method is more flexible than ICT, as it does not require a dedicated test fixture. However, flying probe testing is generally slower than ICT and may not provide the same level of fault coverage.
Burn-In Testing
Burn-in testing involves subjecting the PCB to elevated temperatures and operating conditions for an extended period to identify any components that may fail prematurely. This type of testing helps identify components with manufacturing defects or design weaknesses that may not be apparent during normal testing.
Automated Optical Inspection (AOI)
Automated optical inspection uses cameras and image processing software to visually inspect the PCB for manufacturing defects, such as missing components, incorrect component placement, or solder joint issues. AOI can be performed at various stages of the manufacturing process, including pre- and post-reflow, and can help identify defects that may be difficult to detect using other testing methods.
X-Ray Inspection
X-ray inspection is used to examine the internal structure of the PCB and its components, particularly for hidden solder joints, such as those found in Ball Grid Array (BGA) packages. This non-destructive testing method helps identify issues like voids, bridges, or insufficient solder that may not be visible from the surface of the PCB.
Frequently Asked Questions (FAQ)
-
Q: What is the difference between bare board testing and in-circuit testing?
A: Bare board testing is performed on the PCB before any components are mounted, while in-circuit testing is performed after the components have been mounted on the PCB. Bare board testing focuses on verifying the PCB’s copper traces, vias, and pads, while in-circuit testing verifies the functionality and connection of the mounted components. -
Q: Is functional testing necessary if in-circuit testing has been performed?
A: Yes, functional testing is still necessary even if in-circuit testing has been performed. In-circuit testing verifies the functionality of individual components, while functional testing ensures that the PCB functions correctly as a whole in its final application. -
Q: Can automated optical inspection replace X-ray inspection?
A: No, automated optical inspection and X-ray inspection serve different purposes. AOI is used to visually inspect the surface of the PCB, while X-ray inspection is used to examine the internal structure of the PCB and its components, particularly for hidden solder joints. -
Q: What are the advantages of boundary scan testing over in-circuit testing?
A: Boundary scan testing does not require physical access to the components, making it suitable for testing PCBs with high-density layouts or hard-to-reach components. Additionally, boundary scan testing can be performed at various stages of the manufacturing process, including post-assembly and in-system testing. -
Q: How does burn-in testing help improve PCB reliability?
A: Burn-in testing helps identify components with manufacturing defects or design weaknesses that may not be apparent during normal testing. By subjecting the PCB to elevated temperatures and operating conditions for an extended period, burn-in testing can help identify components that may fail prematurely, allowing for their replacement before the PCB is shipped to the customer.
Conclusion
PCB electrical tests are essential in ensuring the quality, functionality, and reliability of manufactured PCBs. By performing various tests, such as bare board testing, in-circuit testing, functional testing, burn-in testing, automated optical inspection, and X-ray inspection, manufacturers can identify and rectify issues early in the production process. This helps reduce the risk of product failures and recalls, ultimately leading to higher customer satisfaction and lower overall costs. As PCB designs continue to become more complex, the importance of comprehensive electrical testing will only continue to grow.
Leave a Reply