Introduction to Transparent PCBs
Transparent PCBs, also known as clear or see-through circuit boards, are a revolutionary development in the field of electronics. Unlike traditional printed circuit boards (PCBs) that are made from opaque materials like FR-4, transparent PCBs are fabricated using optically clear substrates that allow light to pass through. This unique property opens up a wide range of applications and design possibilities in various industries, including consumer electronics, automotive, aerospace, and medical devices.
What are Transparent PCBs?
Transparent PCBs are circuit boards that use transparent materials as the base substrate instead of the typical opaque materials like FR-4. These transparent materials, such as glass, polyethylene terephthalate (PET), or polyimide (PI), have high optical transmissivity, allowing light to pass through the board while maintaining the necessary electrical and mechanical properties required for reliable circuit operation.
Advantages of Transparent PCBs
-
Optical Clarity: The most obvious advantage of transparent PCBs is their ability to allow light to pass through the board. This property enables the integration of light-based features, such as backlighting, displays, or optical sensors, directly into the PCB design.
-
Design Flexibility: Transparent PCBs offer greater design flexibility by allowing for the placement of components on both sides of the board without obscuring visibility. This feature is particularly useful in applications where space is limited, such as wearable devices or compact electronics.
-
Aesthetics: The see-through nature of transparent PCBs can enhance the visual appeal of electronic devices. They can be used to create striking designs, showcase internal components, or add a futuristic touch to products.
-
Improved Inspection: With transparent PCBs, visual inspection of the board and its components becomes much easier. This can facilitate quality control processes, troubleshooting, and failure analysis.
-
Light Weight: Transparent materials used in PCBs, such as PET or PI, are often lighter than traditional FR-4. This weight reduction can be beneficial in applications where every gram counts, such as in aerospace or portable devices.
Materials Used in Transparent PCBs
Transparent Substrates
Several transparent materials can be used as substrates for transparent PCBs. Each material has its own set of properties and advantages:
-
Glass: Glass is a popular choice for transparent PCBs due to its excellent optical clarity, high thermal stability, and good electrical insulation properties. However, glass is brittle and requires careful handling during manufacturing and assembly processes.
-
Polyethylene Terephthalate (PET): PET is a lightweight, flexible, and cost-effective transparent material. It offers good optical clarity and has a lower dielectric constant compared to glass. PET is commonly used in applications that require flexibility, such as wearable devices or flexible displays.
-
Polyimide (PI): PI is a high-performance polymer that combines excellent thermal stability, mechanical strength, and electrical insulation properties. It is often used in demanding applications, such as aerospace or high-temperature environments. PI films can be made transparent and are suitable for flexible transparent PCBs.
Transparent Conductive Materials
To create conductive traces and pads on transparent PCBs, special transparent conductive materials are used. These materials allow for the flow of electricity while maintaining optical transparency:
-
Indium Tin Oxide (ITO): ITO is a widely used transparent conductive material composed of indium, tin, and oxygen. It offers excellent optical transparency and good electrical conductivity. ITO is commonly deposited as a thin film on transparent substrates using techniques like sputtering or evaporation.
-
Silver Nanowires: Silver nanowires are ultra-thin, highly conductive wires that can be deposited on transparent substrates to create transparent conductive patterns. They offer high optical transparency and excellent electrical conductivity, making them a promising alternative to ITO.
-
Graphene: Graphene, a single layer of carbon atoms arranged in a hexagonal lattice, has emerged as a potential transparent conductive material. It exhibits exceptional electrical conductivity and optical transparency, although its large-scale production and patterning remain challenging.
Manufacturing Process of Transparent PCBs
The manufacturing process of transparent PCBs differs from that of traditional PCBs due to the unique properties of the transparent materials used. Here are the key steps involved in the fabrication of transparent PCBs:
-
Substrate Preparation: The transparent substrate, such as glass, PET, or PI, is cleaned and prepared for the subsequent processes. This may involve surface treatment, such as plasma or chemical cleaning, to improve adhesion.
-
Conductive Layer Deposition: A transparent conductive material, such as ITO or silver nanowires, is deposited onto the substrate using techniques like sputtering, evaporation, or spin coating. The thickness and uniformity of the conductive layer are carefully controlled to ensure optical transparency and electrical performance.
-
Patterning: The desired circuit pattern is transferred onto the conductive layer using photolithography or laser direct imaging. A photoresist is applied, exposed to light through a mask, and developed to create the desired pattern.
-
Etching: The exposed conductive layer is etched away using chemical or physical methods, leaving behind the desired circuit traces and pads.
-
Insulation and Protection: A transparent insulating layer, such as a clear solder mask or a transparent dielectric coating, is applied to protect the circuit traces and provide electrical insulation.
-
Drilling and Cutting: Holes for through-hole components or vias are drilled using laser or mechanical drilling techniques. The board is then cut to the desired shape and size.
-
Assembly: Components are mounted onto the transparent PCB using specialized transparent adhesives or low-temperature soldering techniques to minimize thermal stress on the transparent substrate.
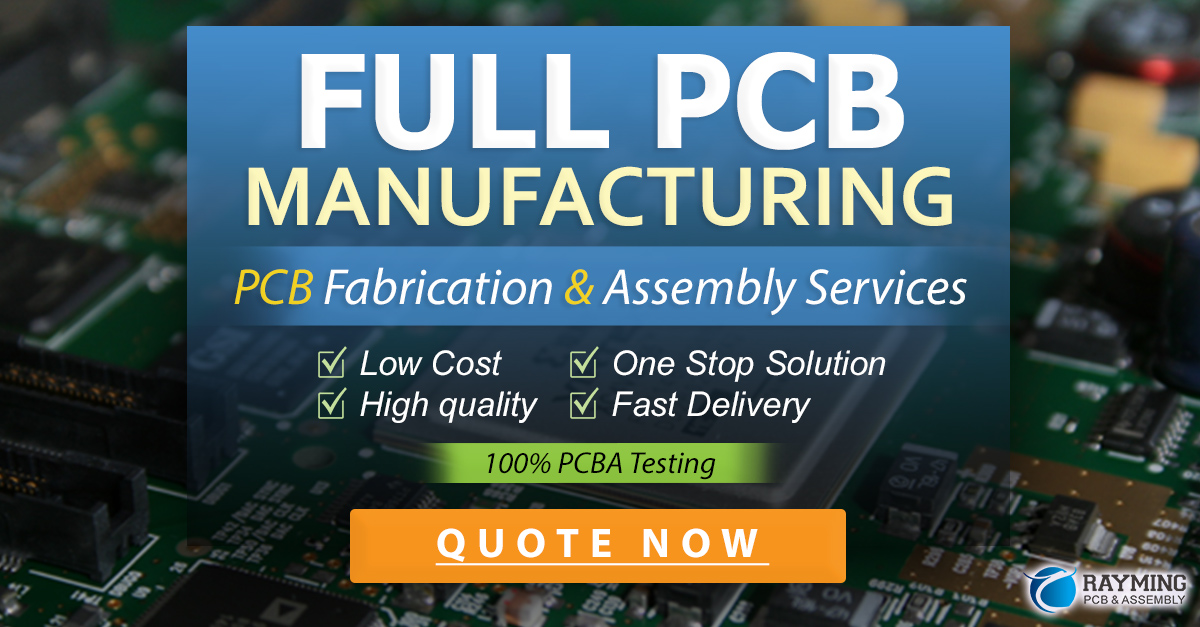
Applications of Transparent PCBs
Transparent PCBs find applications in various industries and products where optical transparency and electronic functionality are desired:
-
Displays and Touchscreens: Transparent PCBs are used in the manufacturing of displays and touchscreens, enabling the integration of touch sensors, backlighting, and other electronic components within the display module.
-
Wearable Devices: The combination of transparency and flexibility offered by transparent PCBs is ideal for wearable devices, such as smart glasses, fitness trackers, or smart clothing. The see-through nature of the PCBs allows for seamless integration with the device’s aesthetics.
-
Automotive and Aerospace: Transparent PCBs can be used in automotive and aerospace applications, such as head-up displays (HUDs), instrument panels, or cockpit displays. They enable the projection of information onto transparent surfaces while maintaining visibility.
-
Medical Devices: In medical devices, transparent PCBs can be used in applications that require visual monitoring or optical sensing. For example, they can be integrated into microfluidic devices for real-time observation of fluid flow or in optogenetic stimulation devices for neuroscience research.
-
Smart Buildings: Transparent PCBs can be incorporated into smart building systems, such as interactive windows or transparent solar panels. They enable the integration of electronic functionality while preserving the aesthetic and optical properties of the building materials.
Challenges and Future Developments
Despite the numerous advantages and applications of transparent PCBs, there are still some challenges and areas for future development:
-
Material Optimization: Ongoing research focuses on developing new transparent materials with improved optical, electrical, and mechanical properties. This includes the exploration of novel transparent conductive materials, such as carbon nanotubes or conductive polymers, to overcome the limitations of current options like ITO.
-
Manufacturing Processes: The manufacturing processes for transparent PCBs need to be further optimized to achieve higher yield, lower cost, and improved reliability. Advancements in patterning techniques, such as high-resolution photolithography or nanoimprint lithography, can enable the fabrication of finer circuit features.
-
Thermal Management: Transparent substrates often have lower thermal conductivity compared to traditional PCB materials, which can pose challenges in heat dissipation. Developing effective thermal management strategies, such as transparent heat spreaders or advanced cooling techniques, is crucial for the reliable operation of transparent PCBs in high-power applications.
-
Integration with Other Technologies: Transparent PCBs have the potential to be integrated with other emerging technologies, such as flexible electronics, printed electronics, or energy harvesting devices. Exploring these synergies can lead to innovative applications and products.
-
Standardization and Regulations: As transparent PCBs gain more widespread adoption, there is a need for industry standards and regulations to ensure consistency, reliability, and safety. Collaborative efforts among manufacturers, suppliers, and regulatory bodies will be essential to establish guidelines and best practices for transparent PCB design and production.
FAQ
-
Q: What is the main difference between transparent PCBs and traditional PCBs?
A: The main difference is the substrate material used. Transparent PCBs use optically clear materials like glass, PET, or PI, while traditional PCBs use opaque materials like FR-4. -
Q: Can transparent PCBs be made flexible?
A: Yes, transparent PCBs can be made flexible by using flexible transparent substrates like PET or PI films. This allows for the creation of flexible and see-through electronic devices. -
Q: What are the common applications of transparent PCBs?
A: Transparent PCBs are commonly used in applications such as displays and touchscreens, wearable devices, automotive and aerospace systems, medical devices, and smart buildings. -
Q: Are transparent PCBs more expensive than traditional PCBs?
A: Yes, transparent PCBs are generally more expensive than traditional PCBs due to the specialized materials and manufacturing processes involved. However, as the technology matures and demand increases, the cost is expected to decrease. -
Q: Can transparent PCBs be assembled using standard soldering techniques?
A: Transparent PCBs often require specialized assembly techniques, such as low-temperature soldering or the use of transparent adhesives, to minimize thermal stress on the transparent substrate and maintain optical clarity.
Conclusion
Transparent PCBs represent a significant advancement in the field of electronics, offering a unique combination of optical transparency and electronic functionality. By using see-through substrates and transparent conductive materials, these innovative circuit boards enable a wide range of applications across various industries, from consumer electronics to automotive, aerospace, and medical devices.
The development of transparent PCBs is driven by the increasing demand for seamless integration of electronics into products where aesthetics, light transmission, and visual monitoring are crucial. As research continues to optimize materials, manufacturing processes, and integration strategies, transparent PCBs are poised to revolutionize the way we design and interact with electronic devices.
However, challenges such as material limitations, manufacturing complexities, and the need for standardization must be addressed to fully realize the potential of transparent PCBs. Collaborative efforts among researchers, manufacturers, and industry stakeholders will be key to overcoming these hurdles and unlocking new possibilities in the realm of see-through electronics.
As the technology advances, transparent PCBs are expected to play a pivotal role in shaping the future of electronics, enabling the creation of visually stunning, optically integrated, and highly functional devices that blend seamlessly with their surroundings. With their unique properties and vast potential, transparent PCBs are set to transform the landscape of electronic design and open up exciting new frontiers in the world of technology.
Property | Transparent PCBs | Traditional PCBs |
---|---|---|
Substrate Material | Glass, PET, PI | FR-4, Polyimide |
Optical Transparency | High | Opaque |
Conductive Material | ITO, Silver Nanowires, Graphene | Copper |
Flexibility | Possible with PET or PI films | Limited |
Applications | Displays, Wearables, Automotive, Medical | General Electronics |
Cost | Higher | Lower |
Manufacturing Process | Specialized | Standard |
Assembly Techniques | Low-temperature soldering, Transparent adhesives | Standard soldering |
Leave a Reply