Introduction to PCB Lamination and Sequential Lamination
Printed Circuit Board (PCB) lamination is a critical process in the manufacturing of multi-layer PCBs. It involves bonding multiple layers of PCB material together using heat, pressure, and adhesive to create a single, solid board. The lamination process ensures that the layers are properly aligned, and the board has the desired thickness and mechanical strength.
Sequential lamination, also known as step lamination or multiple lamination, is a technique used in the production of complex multi-layer PCBs. In this process, the PCB is built up in stages, with each stage involving the lamination of a subset of layers. This approach allows for greater flexibility in the design and enables the incorporation of unique features such as embedded components, blind and buried vias, and high-density interconnects.
Advantages of Sequential Lamination
Sequential lamination offers several advantages over traditional PCB lamination techniques:
-
Design Flexibility: Sequential lamination allows for the creation of complex PCB designs with multiple layers, embedded components, and high-density interconnects.
-
Improved Signal Integrity: By laminating subsets of layers in stages, sequential lamination minimizes the impact of thermal expansion and contraction on the PCB, resulting in better signal integrity.
-
Reduced Manufacturing Costs: Sequential lamination enables the use of less expensive materials for non-critical layers, reducing overall manufacturing costs.
-
Enhanced Reliability: The staged approach to lamination reduces the risk of delamination and improves the overall reliability of the PCB.
Trends in Sequential Lamination
High-Density Interconnects (HDI)
High-Density Interconnects (HDI) are becoming increasingly popular in PCB design, particularly in applications requiring miniaturization and high performance. HDI PCBs feature finer trace widths, smaller vias, and higher layer counts than traditional PCBs. Sequential lamination is an essential technique for manufacturing HDI PCBs, as it allows for the precise control of layer alignment and the incorporation of micro-vias.
Embedded Components
Embedded components, such as resistors, capacitors, and inductors, are increasingly being used in PCB design to reduce board size and improve performance. Sequential lamination enables the integration of these components within the PCB stack-up, minimizing the need for surface-mount components and reducing the overall board size.
Advanced Materials
The use of advanced materials, such as low-loss dielectrics and high-performance laminates, is becoming more common in PCB manufacturing. These materials offer improved electrical and thermal properties, enabling the design of high-speed, high-frequency PCBs. Sequential lamination allows for the selective use of these materials in critical layers, optimizing performance while managing costs.
Thermal Management
As PCBs become more complex and power-dense, thermal management is becoming an increasingly important consideration in PCB design. Sequential lamination enables the incorporation of thermal management features, such as embedded heat spreaders and thermal vias, to dissipate heat and maintain optimal operating temperatures.
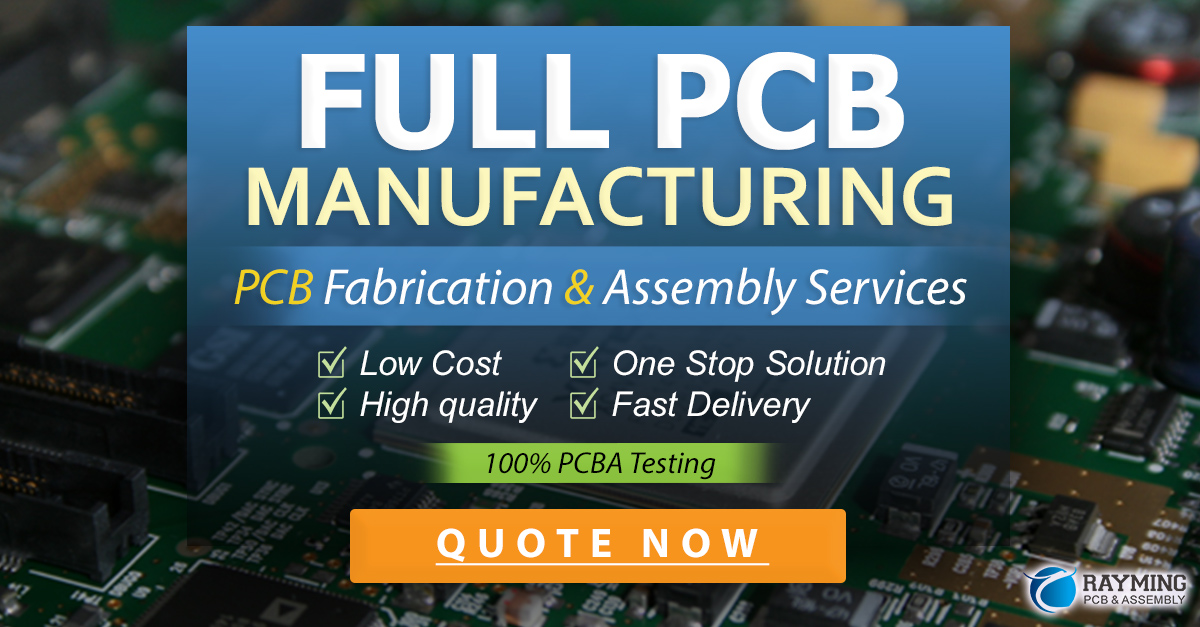
Techniques for Sequential Lamination
Layer Stack-up Design
Effective layer stack-up design is critical for successful sequential lamination. The stack-up should be designed to optimize signal integrity, minimize crosstalk, and ensure proper layer alignment. Factors to consider include:
- Material selection
- Layer thickness
- Copper weight
- Dielectric constant
- Impedance control
Layer | Material | Thickness (mm) | Copper Weight (oz) |
---|---|---|---|
1 | FR-4 | 0.1 | 0.5 |
2 | FR-4 | 0.2 | 1.0 |
3 | Rogers | 0.3 | 0.5 |
4 | FR-4 | 0.2 | 1.0 |
5 | FR-4 | 0.1 | 0.5 |
Lamination Cycle Optimization
The lamination cycle is a critical factor in the success of sequential lamination. The cycle must be optimized to ensure proper bond strength, minimize thermal stress, and prevent delamination. Factors to consider include:
- Lamination temperature
- Lamination pressure
- Dwell time
- Cooling rate
Parameter | Value |
---|---|
Temperature | 180°C |
Pressure | 300 psi |
Dwell Time | 60 min |
Cooling Rate | 10°C/min |
Registration and Alignment
Proper registration and alignment of layers is essential for the success of sequential lamination. Misalignment can result in poor electrical performance, reduced reliability, and increased manufacturing costs. Techniques for ensuring proper alignment include:
- Use of registration holes and pins
- Optical alignment systems
- Automatic registration control (ARC)
Void Reduction
Voids, or air pockets, can form between layers during the lamination process, leading to reduced bond strength and increased risk of delamination. Techniques for reducing voids include:
- Proper prepreg conditioning
- Use of vacuum lamination
- Optimized lamination cycle parameters
Case Studies
Case Study 1: High-Speed Digital PCB
A high-speed digital PCB was designed and manufactured using sequential lamination. The PCB featured:
- 12 layers
- Impedance-controlled traces
- Blind and buried vias
- Embedded decoupling capacitors
The use of sequential lamination allowed for the optimization of the layer stack-up, the incorporation of embedded components, and the precise control of impedance. The resulting PCB demonstrated excellent signal integrity and reliable performance.
Case Study 2: RF PCB with Embedded Antennas
An RF PCB with embedded antennas was designed and manufactured using sequential lamination. The PCB featured:
- 8 layers
- Low-loss dielectric materials
- Embedded microstrip antennas
- High-density interconnects
Sequential lamination enabled the integration of the antennas within the PCB stack-up, minimizing the need for external components and reducing the overall board size. The use of low-loss materials and optimized lamination parameters ensured excellent RF performance.
FAQ
1. What is the difference between sequential lamination and traditional PCB lamination?
In traditional PCB lamination, all layers are laminated together in a single step. Sequential lamination, on the other hand, involves laminating subsets of layers in stages, allowing for greater design flexibility and the incorporation of unique features.
2. What are the benefits of using sequential lamination in PCB manufacturing?
Sequential lamination offers several benefits, including:
- Improved signal integrity
- Increased design flexibility
- Reduced manufacturing costs
- Enhanced reliability
3. What factors should be considered when designing a layer stack-up for sequential lamination?
When designing a layer stack-up for sequential lamination, factors to consider include:
- Material selection
- Layer thickness
- Copper weight
- Dielectric constant
- Impedance control
4. How can voids be reduced during the sequential lamination process?
Voids can be reduced during the sequential lamination process by:
- Properly conditioning prepregs
- Using vacuum lamination
- Optimizing lamination cycle parameters
5. What are some applications that benefit from the use of sequential lamination?
Applications that benefit from the use of sequential lamination include:
- High-speed digital PCBs
- RF and microwave PCBs
- PCBs with embedded components
- HDI PCBs
- PCBs requiring advanced thermal management
Conclusion
Sequential lamination is a powerful technique for the manufacturing of complex, high-performance PCBs. By laminating subsets of layers in stages, sequential lamination enables greater design flexibility, improved signal integrity, and enhanced reliability. As PCB designs continue to push the boundaries of complexity and performance, sequential lamination will play an increasingly important role in the manufacturing process.
To successfully implement sequential lamination, designers and manufacturers must consider a range of factors, including layer stack-up design, lamination cycle optimization, registration and alignment, and void reduction. By carefully optimizing these parameters, and leveraging advanced materials and techniques, PCB manufacturers can produce boards that meet the most demanding requirements of today’s high-performance applications.
Leave a Reply