Introduction to PCB Assembly for Power Supplies
PCB assembly is a critical process in the manufacturing of power supplies. The quality and reliability of the assembled PCB directly impact the performance and longevity of the power supply unit. In this comprehensive guide, we will discuss the top guidelines for ensuring successful power supply PCB assembly.
Understanding the Importance of PCB Assembly in Power Supplies
Power supplies are essential components in various electronic devices, converting electrical power from a source to the desired voltage and current required by the connected load. The PCB serves as the foundation for mounting and interconnecting the electronic components that make up the power supply circuit. Proper PCB assembly is crucial for several reasons:
- Ensuring reliable electrical connections
- Minimizing signal interference and noise
- Facilitating efficient heat dissipation
- Enabling easy maintenance and troubleshooting
Key Considerations for Power Supply PCB Design
Before diving into the assembly process, it is essential to understand the importance of a well-designed PCB. The design phase lays the groundwork for a successful assembly and ultimately determines the performance and reliability of the power supply.
Choosing the Right PCB Material
The choice of PCB material is critical in power supply applications. The most common materials used are:
- FR-4: A glass-reinforced epoxy laminate, offering good electrical insulation and mechanical stability.
- Aluminum: Used for its excellent thermal conductivity, helping to dissipate heat generated by power components.
- Ceramic: Offers high thermal conductivity and electrical insulation, ideal for high-power applications.
Consider the specific requirements of your power supply, such as operating temperature, power density, and environmental conditions, when selecting the PCB material.
Designing for Manufacturability (DFM)
Designing for manufacturability (DFM) is a crucial aspect of PCB design. It involves adhering to guidelines that ensure the PCB can be efficiently and reliably manufactured. Some key DFM considerations include:
- Minimum trace width and spacing
- Pad sizes and shapes
- Drill hole sizes and spacing
- Solder mask and silkscreen clearances
Consult with your PCB manufacturer to obtain their specific DFM guidelines and incorporate them into your design.
Thermal Management Considerations
Power supplies often generate significant heat due to the high power density of the components. Proper thermal management is essential to ensure the longevity and reliability of the PCB assembly. Consider the following thermal management techniques:
- Copper pours: Use large copper pours on the PCB to dissipate heat from power components.
- Thermal vias: Incorporate thermal vias to transfer heat from the components to the opposite side of the PCB.
- Heatsinks: Use heatsinks to dissipate heat from critical components, such as power MOSFETs and regulators.
PCB Assembly Process for Power Supplies
With a well-designed PCB in hand, let’s explore the key steps involved in the assembly process.
Component Placement
Accurate component placement is essential for a successful PCB assembly. Follow these guidelines:
- Use a pick-and-place machine for precise and consistent component placement.
- Ensure proper orientation of polarized components, such as capacitors and diodes.
- Maintain recommended spacing between components to facilitate soldering and avoid interference.
- Use fiducials to align the PCB and components accurately.
Soldering Techniques
Soldering is the process of creating electrical and mechanical connections between components and the PCB. The two primary soldering techniques used in PCB assembly are:
- Wave Soldering:
- Suitable for through-hole components
- PCB is passed over a molten solder wave, creating connections
-
Requires proper flux application and temperature control
-
Reflow Soldering:
- Used for surface-mount components
- Solder paste is applied to the PCB pads using a stencil
- Components are placed on the solder paste
- PCB is heated in a reflow oven, melting the solder and creating connections
Choose the appropriate soldering technique based on the component types and PCB design.
Inspection and Quality Control
Thorough inspection and quality control are crucial to ensure the reliability and functionality of the assembled PCB. Implement the following inspection techniques:
- Visual Inspection:
- Check for proper component placement and orientation
- Look for solder bridges, cold solder joints, and insufficient solder
-
Verify the presence of all required components
-
Automated Optical Inspection (AOI):
- Use AOI machines to detect assembly defects automatically
- Identifies missing components, misaligned components, and solder issues
-
Provides fast and accurate inspection results
-
X-Ray Inspection:
- Used for inspecting hidden solder joints, such as those under Ball Grid Array (BGA) components
- Detects voids, cracks, and other defects in the solder joints
Establish a comprehensive quality control process to catch and rectify any assembly issues before the power supply is put into operation.
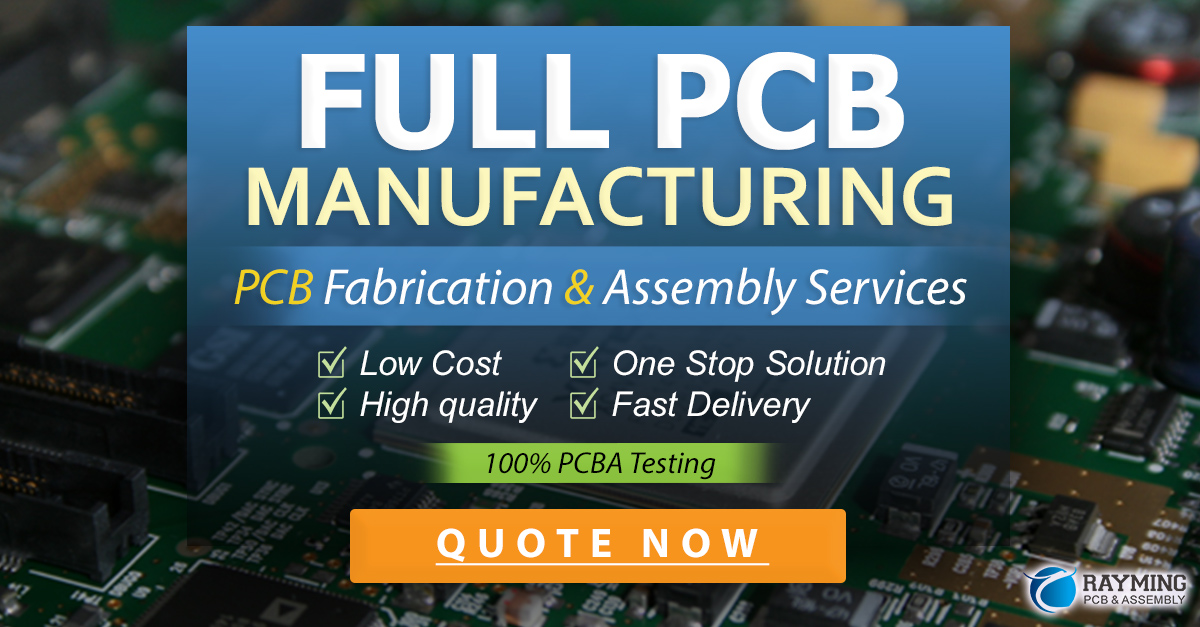
Testing and Verification
After the PCB assembly is complete, it is essential to perform thorough testing and verification to ensure the power supply functions as intended.
Functional Testing
Conduct functional tests to verify the power supply’s performance under various operating conditions. Some key tests include:
- Output voltage and current measurement
- Load regulation testing
- Line regulation testing
- Ripple and noise measurement
- Efficiency measurement
Use calibrated test equipment and follow established test procedures to ensure accurate and repeatable results.
Safety and Compliance Testing
Power supplies must adhere to safety and regulatory standards to ensure user safety and electromagnetic compatibility. Perform the necessary safety and compliance tests, such as:
- Dielectric withstand voltage (Hipot) testing
- Insulation resistance testing
- Leakage current testing
- Electromagnetic compatibility (EMC) testing
Consult the relevant standards and regulations for your target market to determine the specific testing requirements.
Best Practices for PCB Assembly Troubleshooting
Despite following the guidelines and best practices, issues can still arise during the PCB assembly process. Here are some tips for troubleshooting common assembly problems:
- Solder Bridges:
- Use a soldering iron with a fine tip to remove excess solder
-
Apply flux and carefully drag the soldering iron tip between the bridged pads
-
Cold Solder Joints:
- Reheat the joint with a soldering iron and apply fresh solder
-
Ensure proper temperature and soldering technique
-
Component Misalignment:
- Gently lift the component using tweezers or a soldering iron
-
Reposition the component and reflow the solder joints
-
Insufficient Solder:
- Apply additional solder to the joint using a soldering iron
-
Ensure proper solder coverage and joint formation
-
Overheated Components:
- Use a heat sink or thermal management techniques to dissipate excess heat
- Verify the component’s temperature rating and adjust the soldering process accordingly
By understanding common assembly issues and their solutions, you can quickly resolve problems and ensure a reliable PCB assembly.
FAQs
-
Q: What is the difference between through-hole and surface-mount components?
A: Through-hole components have leads that are inserted into holes drilled in the PCB, while surface-mount components are placed directly on the surface of the PCB and soldered to pads. -
Q: How do I select the appropriate solder wire for PCB assembly?
A: Consider factors such as the solder alloy composition (e.g., lead-free or leaded), wire diameter, and flux type (e.g., rosin core or no-clean) based on your specific assembly requirements and regulatory standards. -
Q: What is the purpose of a solder stencil in PCB assembly?
A: A solder stencil is used to apply solder paste onto the PCB pads accurately and consistently. It ensures the correct amount of solder is deposited, facilitating the reflow soldering process for surface-mount components. -
Q: How can I prevent electrostatic discharge (ESD) damage during PCB assembly?
A: Implement ESD protection measures such as wearing grounded wrist straps, using ESD-safe mats and packaging, and maintaining a controlled environment with proper humidity levels. -
Q: What are the benefits of using an automated optical inspection (AOI) system in PCB assembly?
A: AOI systems provide fast and accurate inspection of assembled PCBs, detecting defects such as missing components, solder issues, and component misalignment. They improve quality control efficiency and help catch assembly issues early in the process.
PCB Material | Key Characteristics | Typical Applications |
---|---|---|
FR-4 | Good electrical insulation and mechanical stability | General-purpose power supplies |
Aluminum | Excellent thermal conductivity | High-power applications with heat dissipation requirements |
Ceramic | High thermal conductivity and electrical insulation | High-power and high-frequency applications |
Conclusion
Power supply PCB assembly is a critical process that requires careful planning, design considerations, and adherence to best practices. By understanding the key guidelines discussed in this article, you can ensure successful PCB assembly and achieve reliable and high-performing power supplies.
Remember to prioritize PCB design for manufacturability, implement effective thermal management techniques, and follow proper soldering and inspection procedures. Regularly review and update your assembly processes based on industry advancements and feedback from your manufacturing team.
By staying informed and continuously improving your PCB assembly practices, you can deliver top-quality power supplies that meet the demanding requirements of today’s electronic devices.
Leave a Reply