Understanding the PCB Manufacturing Process
Before diving into specific tips, it is crucial to have a thorough understanding of the PCB manufacturing process. The process typically involves the following steps:
- Design and Layout
- Material Selection
- Fabrication
- Assembly
- Testing and Inspection
- Packaging and Shipping
Each step requires careful planning, execution, and quality control to ensure the final product meets the required specifications and standards.
Tip 1: Invest in Advanced Design Tools
The Importance of PCB Design Software
Investing in advanced PCB design software is essential for OEM PCB manufacturers to streamline their design process and minimize errors. Some popular PCB design software include:
- Altium Designer
- Cadence OrCAD
- Mentor Graphics PADS
- Eagle PCB
These software tools offer features such as schematic capture, layout editing, design rule checking (DRC), and 3D visualization, which can significantly improve the efficiency and accuracy of the PCB design process.
Benefits of Using Advanced PCB Design Software
Benefit | Description |
---|---|
Increased Efficiency | Advanced PCB design software automates many tasks, reducing design time and effort. |
Improved Accuracy | Design rule checking and other features help identify and prevent errors early in the design process. |
Better Collaboration | Many PCB design software tools offer collaboration features, allowing team members to work together seamlessly. |
Enhanced Visualization | 3D visualization capabilities provide a better understanding of the final product, helping to identify potential issues before manufacturing. |
Tip 2: Optimize Material Selection
Choosing the Right PCB Materials
Selecting the appropriate materials for your PCB is crucial for ensuring the performance, reliability, and cost-effectiveness of the final product. Some factors to consider when choosing PCB materials include:
- Dielectric constant
- Thermal conductivity
- Coefficient of thermal expansion (CTE)
- Moisture resistance
- Cost
Common PCB materials include:
- FR-4
- High-Tg FR-4
- Polyimide
- PTFE
- Ceramic
The Impact of Material Selection on PCB Performance
Material Property | Impact on PCB Performance |
---|---|
Dielectric Constant | Affects signal integrity and impedance control |
Thermal Conductivity | Influences heat dissipation and thermal management |
CTE | Impacts reliability and durability under temperature fluctuations |
Moisture Resistance | Determines the PCB’s ability to withstand humid environments |
Choosing the right materials based on the specific requirements of your PCB application can optimize performance and reliability while minimizing costs.
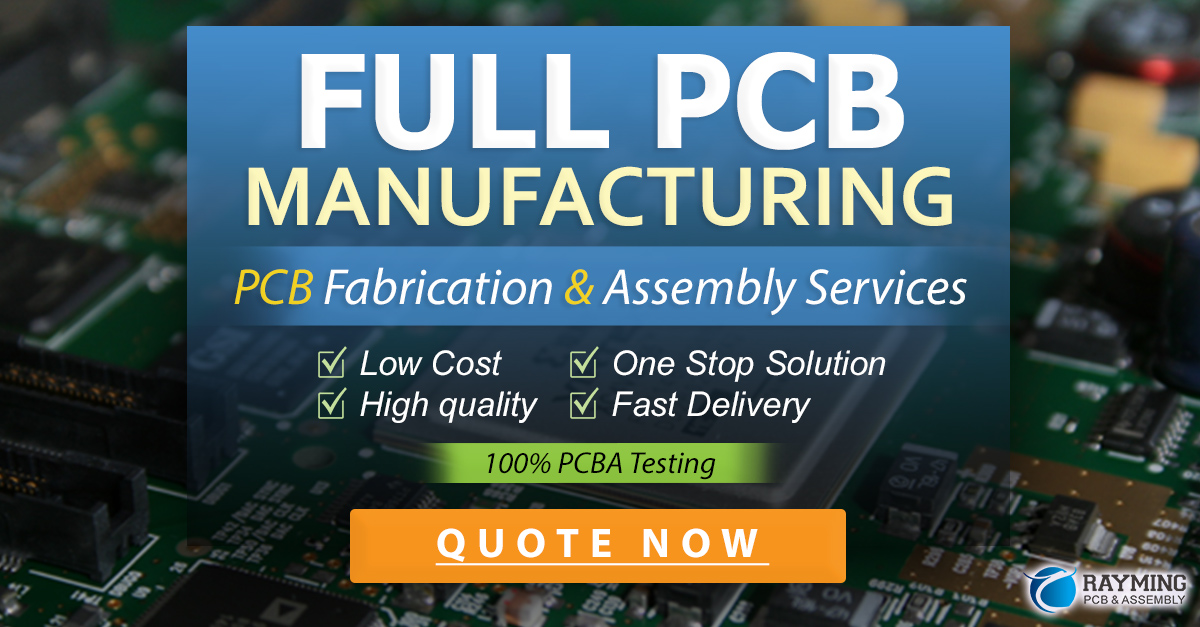
Tip 3: Implement Lean Manufacturing Principles
What is Lean Manufacturing?
Lean manufacturing is a production methodology that focuses on minimizing waste and maximizing efficiency in the manufacturing process. The main principles of lean manufacturing include:
- Identifying and eliminating waste
- Continuous improvement
- Just-in-time (JIT) production
- Employee empowerment
- Customer focus
Applying Lean Manufacturing to PCB Production
Implementing lean manufacturing principles in PCB production can lead to significant improvements in efficiency, quality, and cost-effectiveness. Some ways to apply lean manufacturing in PCB manufacturing include:
- Value Stream Mapping: Identify and eliminate non-value-added activities in the production process.
- 5S: Organize the workspace to improve efficiency and reduce errors.
- Kaizen: Encourage continuous improvement through employee engagement and problem-solving.
- Kanban: Implement a visual system to manage inventory and production flow.
- Total Productive Maintenance (TPM): Maintain equipment to minimize downtime and improve quality.
By adopting lean manufacturing principles, OEM PCB manufacturers can streamline their processes, reduce waste, and improve overall productivity.
Tip 4: Invest in Automation and Industry 4.0 Technologies
The Role of Automation in PCB Manufacturing
Automation plays a crucial role in modern PCB manufacturing, offering benefits such as:
- Increased production speed
- Improved accuracy and consistency
- Reduced labor costs
- Enhanced safety
Some examples of automation in PCB manufacturing include:
- Automated optical inspection (AOI)
- Surface mount technology (SMT) placement machines
- Robotic soldering and assembly
- Automated testing and measurement systems
Industry 4.0 Technologies for PCB Manufacturing
Industry 4.0, also known as the Fourth Industrial Revolution, refers to the integration of advanced technologies such as the Internet of Things (IoT), artificial intelligence (AI), and big data analytics into manufacturing processes. Some Industry 4.0 technologies relevant to PCB manufacturing include:
- Smart factories with connected machines and sensors
- Predictive maintenance using machine learning algorithms
- Real-time production monitoring and optimization
- Digital twins for virtual prototyping and simulation
Investing in automation and Industry 4.0 technologies can help OEM PCB manufacturers stay competitive, improve efficiency, and deliver high-quality products consistently.
Tip 5: Prioritize Quality Control and Testing
The Importance of Quality Control in PCB Manufacturing
Quality control is essential in PCB manufacturing to ensure that the final products meet the required specifications and performance standards. Effective quality control helps to:
- Identify and prevent defects
- Reduce rework and scrap
- Improve customer satisfaction
- Maintain regulatory compliance
Implementing a Robust Quality Control System
To implement a robust quality control system, OEM PCB manufacturers should:
- Establish clear quality standards and specifications
- Implement in-process inspections and testing
- Use advanced testing equipment and techniques, such as flying probe testing and X-ray inspection
- Perform final functional testing and burn-in testing
- Maintain detailed quality records and traceability
- Continuously monitor and improve the quality control process
By prioritizing quality control and testing, OEM PCB manufacturers can minimize defects, reduce costs associated with rework and scrap, and build a reputation for delivering high-quality products.
Frequently Asked Questions (FAQ)
- What is the difference between an OEM and a contract manufacturer?
-
An OEM (Original Equipment Manufacturer) designs and manufactures products under its own brand name, while a contract manufacturer produces products according to the specifications provided by the OEM.
-
What are some common challenges faced by OEM PCB manufacturers?
-
Some common challenges include managing supply chain disruptions, keeping up with rapidly changing technologies, maintaining high quality standards, and controlling costs in a competitive market.
-
How can OEM PCB manufacturers ensure the security of their intellectual property?
-
OEM PCB manufacturers can protect their intellectual property by implementing non-disclosure agreements (NDAs), using secure data storage and transfer methods, and carefully screening and monitoring their suppliers and partners.
-
What certifications are important for OEM PCB manufacturers?
-
Some important certifications for OEM PCB manufacturers include ISO 9001 (Quality Management Systems), ISO 14001 (Environmental Management Systems), IATF 16949 (Automotive Quality Management Systems), and UL (Underwriters Laboratories) certification for safety and compliance.
-
How can OEM PCB manufacturers stay competitive in a global market?
- OEM PCB manufacturers can stay competitive by continuously innovating, adopting new technologies, optimizing their processes for efficiency and quality, building strong relationships with customers and suppliers, and focusing on niche markets or value-added services.
In conclusion, OEM PCB manufacturing is a complex and demanding industry that requires a combination of technical expertise, operational excellence, and strategic planning. By following the tips outlined in this article – investing in advanced design tools, optimizing material selection, implementing lean manufacturing principles, adopting automation and Industry 4.0 technologies, and prioritizing quality control and testing – OEM PCB manufacturers can position themselves for success in a highly competitive global market.
Leave a Reply