Understanding the Challenges in Automotive PCB Assembly
Before diving into the innovative strategies, it is essential to understand the unique challenges faced by the automotive PCB assembly industry. Some of the key challenges include:
- Harsh operating conditions: Automotive PCBs are exposed to extreme temperatures, vibrations, and moisture, which can affect their performance and reliability.
- Miniaturization: As vehicles become more compact and feature-rich, PCBs need to be smaller and more densely populated with components.
- High-reliability requirements: Automotive PCBs must meet strict quality and reliability standards to ensure passenger safety and minimize the risk of failures.
- Cost pressure: The automotive industry is highly competitive, and manufacturers are constantly seeking ways to reduce costs without compromising on quality.
Innovative Strategies for Automotive PCB Assembly
1. Adopting Advanced Materials and Coatings
One of the key strategies for improving automotive PCB performance is the use of advanced materials and coatings. Some examples include:
- High-temperature laminates: These materials can withstand higher operating temperatures, making them suitable for applications such as engine control units and exhaust systems.
- Low-loss dielectrics: These materials minimize signal loss and improve signal integrity, which is crucial for high-speed communication systems like ADAS and infotainment.
- Conformal coatings: Applying conformal coatings to PCBs can protect them from moisture, dust, and other environmental factors, enhancing their durability and reliability.
Material/Coating | Benefits | Applications |
---|---|---|
High-temp laminates | Withstands high temperatures | Engine control units, exhaust systems |
Low-loss dielectrics | Minimizes signal loss, improves signal integrity | ADAS, infotainment systems |
Conformal coatings | Protects from moisture, dust, and other factors | Various automotive PCBs |
2. Implementing Automated Optical Inspection (AOI)
Automated Optical Inspection (AOI) is a powerful technology that can significantly improve the quality control process in automotive PCB assembly. AOI systems use high-resolution cameras and advanced algorithms to detect defects, such as solder bridges, missing components, and incorrect component placement. The benefits of implementing AOI in automotive PCB assembly include:
- Faster and more accurate defect detection compared to manual inspection
- Reduced reliance on human operators, minimizing the risk of human error
- Increased throughput and productivity
- Improved product quality and reliability
3. Utilizing 3D Printing for Rapid Prototyping
3D printing technology has revolutionized the way prototypes are created in various industries, including automotive PCB assembly. By utilizing 3D printing, manufacturers can:
- Quickly create physical prototypes of PCBs and enclosures
- Test and validate designs before mass production
- Reduce lead times and costs associated with traditional prototyping methods
- Iterate and optimize designs based on feedback from prototype testing
4. Implementing Lean Manufacturing Principles
Lean manufacturing is a systematic approach to identifying and eliminating waste in the production process. By adopting lean principles in automotive PCB assembly, manufacturers can:
- Streamline the assembly process and reduce non-value-added activities
- Improve production flow and minimize work-in-progress (WIP) inventory
- Enhance communication and collaboration among team members
- Continuously improve processes through kaizen events and problem-solving sessions
5. Investing in Workforce Training and Development
A skilled and knowledgeable workforce is essential for ensuring high-quality automotive PCB assembly. Manufacturers should invest in comprehensive training and development programs to:
- Keep employees up-to-date with the latest technologies and best practices
- Foster a culture of continuous learning and improvement
- Enhance problem-solving skills and encourage innovation
- Improve employee engagement and job satisfaction
6. Collaborating with Suppliers and Industry Partners
Collaboration is key to driving innovation in automotive PCB assembly. Manufacturers should actively engage with their suppliers and industry partners to:
- Share knowledge and best practices
- Jointly develop new technologies and solutions
- Optimize supply chain processes and reduce lead times
- Leverage collective expertise to address industry challenges
Frequently Asked Questions (FAQ)
-
Q: What are the benefits of using advanced materials and coatings in automotive PCBs?
A: Advanced materials and coatings, such as high-temperature laminates, low-loss dielectrics, and conformal coatings, can improve the performance and reliability of automotive PCBs. They enable PCBs to withstand harsh operating conditions, minimize signal loss, and protect against environmental factors. -
Q: How does Automated Optical Inspection (AOI) improve the quality control process in automotive PCB assembly?
A: AOI systems use high-resolution cameras and advanced algorithms to detect defects in PCBs, such as solder bridges, missing components, and incorrect component placement. This technology enables faster and more accurate defect detection compared to manual inspection, reducing the risk of human error and improving product quality. -
Q: What role does 3D printing play in automotive PCB assembly?
A: 3D printing technology allows manufacturers to quickly create physical prototypes of PCBs and enclosures. This enables them to test and validate designs before mass production, reduce lead times and costs associated with traditional prototyping methods, and iterate and optimize designs based on feedback from prototype testing. -
Q: How can lean manufacturing principles be applied to automotive PCB assembly?
A: Lean manufacturing principles focus on identifying and eliminating waste in the production process. By adopting lean principles, automotive PCB assembly manufacturers can streamline the assembly process, reduce non-value-added activities, improve production flow, minimize work-in-progress (WIP) inventory, and continuously improve processes through kaizen events and problem-solving sessions. -
Q: Why is collaboration with suppliers and industry partners important for innovation in automotive PCB assembly?
A: Collaboration with suppliers and industry partners allows automotive PCB assembly manufacturers to share knowledge and best practices, jointly develop new technologies and solutions, optimize supply chain processes, reduce lead times, and leverage collective expertise to address industry challenges. This collaborative approach is essential for driving innovation and staying competitive in the rapidly evolving automotive industry.
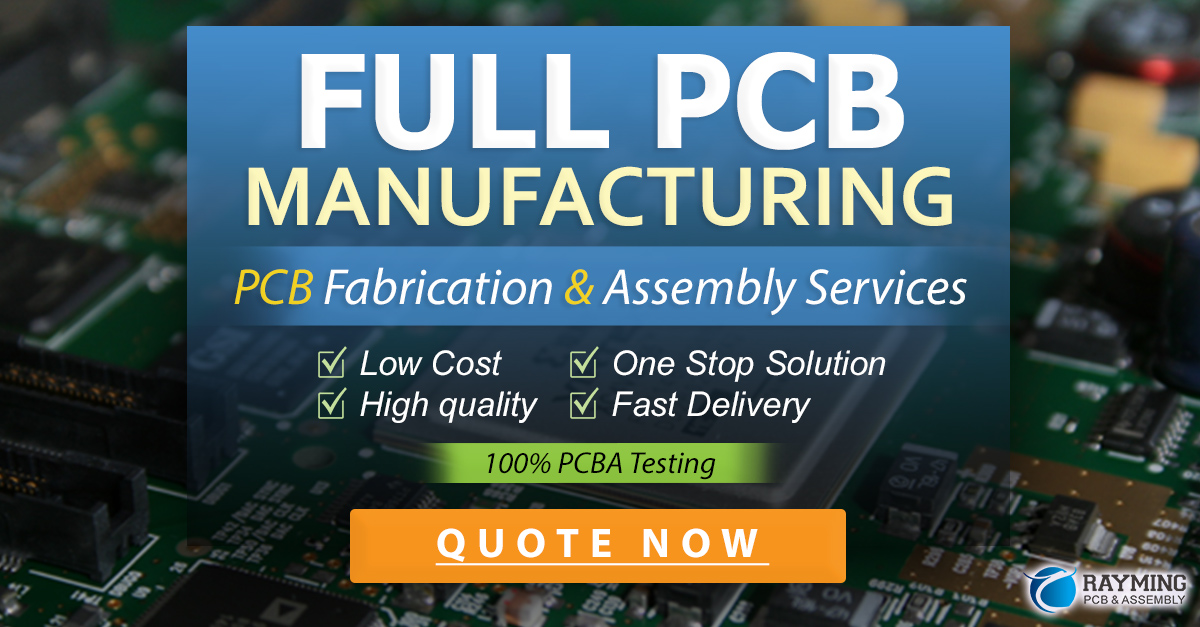
Conclusion
The automotive industry’s increasing demand for advanced electronics and technologies has put a spotlight on the importance of innovative strategies in automotive PCB assembly. By adopting advanced materials and coatings, implementing Automated Optical Inspection (AOI), utilizing 3D printing for rapid prototyping, implementing lean manufacturing principles, investing in workforce training and development, and collaborating with suppliers and industry partners, manufacturers can optimize their assembly processes, improve product quality, and reduce costs.
As the automotive industry continues to evolve, embracing these innovative strategies will be crucial for staying competitive and meeting the ever-changing needs of the market. By continuously seeking out new technologies and best practices, automotive PCB assembly manufacturers can position themselves as leaders in the industry and contribute to the development of safer, smarter, and more efficient vehicles.
Leave a Reply