1. Choose the Right PCB Assembly Partner
Selecting a reliable and experienced PCB assembly partner is essential for the success of your project. Consider the following factors when choosing a PCB assembly service provider:
- Experience and expertise in PCB assembly
- Quality control processes and certifications (e.g., ISO 9001, IPC standards)
- Technical capabilities and equipment
- Customer support and communication
- Turnaround time and pricing
Key Points to Consider When Selecting a PCB Assembly Partner
Factor | Importance |
---|---|
Experience and expertise | Ensures high-quality assembly and ability to handle complex projects |
Quality control processes & certifications | Guarantees adherence to industry standards and consistent quality |
Technical capabilities and equipment | Determines the range of services and the ability to meet specific project requirements |
Customer support and communication | Facilitates smooth collaboration and timely resolution of issues |
Turnaround time and pricing | Impacts project timeline and budget |
2. Provide Accurate and Complete Documentation
To ensure a smooth PCB assembly process, it is crucial to provide your assembly partner with accurate and complete documentation. This includes:
- Bill of Materials (BOM): A comprehensive list of all components required for the assembly, including part numbers, quantities, and specifications.
- Gerber files: The industry-standard format for PCB design files, which includes information on the PCB layers, drill holes, and component placement.
- Assembly drawings: Detailed illustrations that provide guidance on component placement, orientation, and any special assembly instructions.
Essential Documents for PCB Assembly
Document | Purpose |
---|---|
Bill of Materials | Ensures all required components are available and ordered correctly |
Gerber files | Provides the necessary information for PCB fabrication and assembly |
Assembly drawings | Guides the assembly process and ensures correct component placement and orientation |
3. Design for Manufacturability (DFM)
Designing your PCB with manufacturability in mind is essential for successful assembly. Follow these DFM guidelines to optimize your design:
- Adhere to the minimum trace width and spacing requirements specified by your PCB manufacturer
- Ensure adequate clearance between components to allow for efficient assembly
- Use standardized component sizes and packages whenever possible
- Avoid placing components too close to the edge of the board
- Consider the assembly process when designing the component layout (e.g., placement for automated assembly)
DFM Checklist
- [ ] Minimum trace width and spacing requirements met
- [ ] Adequate clearance between components
- [ ] Standardized component sizes and packages used
- [ ] Components placed away from board edges
- [ ] Component layout optimized for assembly process
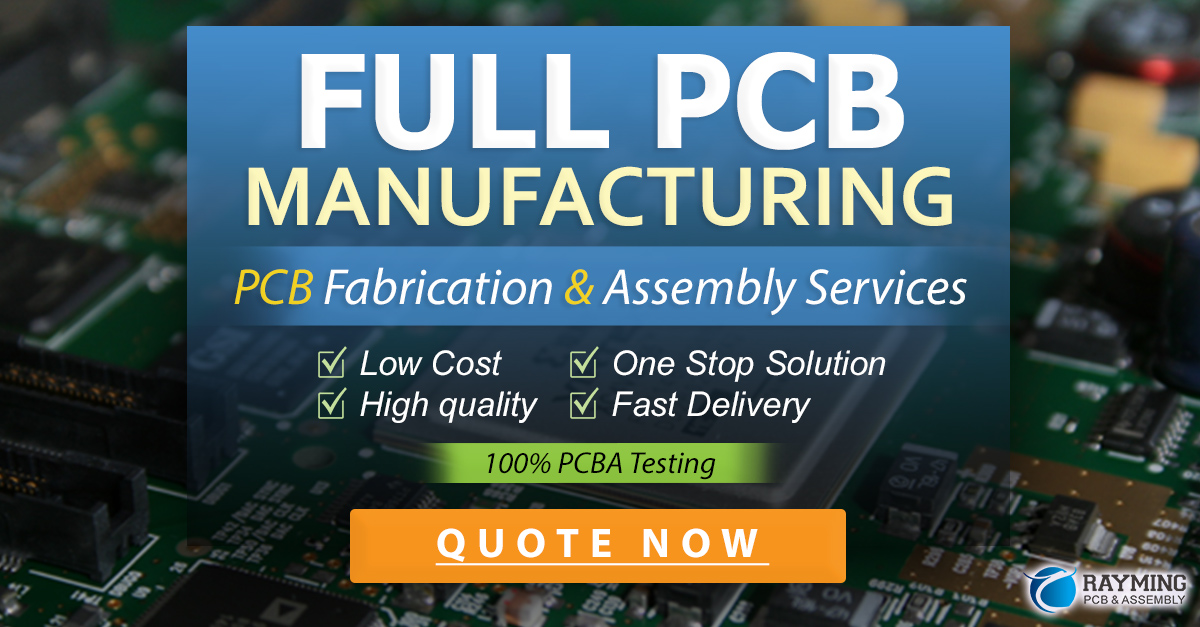
4. Conduct a Design Review
Before starting the PCB assembly process, it is essential to conduct a thorough design review. This review should involve both your internal team and your PCB assembly partner. The purpose of the design review is to:
- Identify and address any potential design issues that may impact assembly
- Ensure the design meets all required specifications and standards
- Optimize the design for manufacturability and assembly efficiency
- Verify that all necessary documentation is complete and accurate
Design Review Checklist
- [ ] Design reviewed by internal team and PCB assembly partner
- [ ] Potential design issues identified and addressed
- [ ] Design meets all required specifications and standards
- [ ] Design optimized for manufacturability and assembly efficiency
- [ ] Documentation complete and accurate
5. Use High-Quality Components
The quality of the components used in your PCB assembly directly impacts the performance and reliability of the final product. To ensure the best results, follow these guidelines:
- Source components from reputable suppliers with a proven track record of quality
- Verify that all components meet the required specifications and tolerances
- Use components that are suitable for the intended operating environment (e.g., temperature, humidity)
- Consider the lifecycle of the components and choose parts with adequate availability and long-term support
Component Selection Checklist
- [ ] Components sourced from reputable suppliers
- [ ] Components meet required specifications and tolerances
- [ ] Components suitable for intended operating environment
- [ ] Component lifecycle and availability considered
6. Implement Proper Handling and Storage Procedures
Proper handling and storage of PCBs and components are critical to ensuring successful assembly. Follow these best practices:
- Store PCBs and components in a clean, dry, and temperature-controlled environment
- Use electrostatic discharge (ESD) protection measures when handling PCBs and sensitive components
- Implement first-in, first-out (FIFO) inventory management to ensure components are used within their shelf life
- Regularly inspect stored PCBs and components for signs of damage or deterioration
Handling and Storage Best Practices
Practice | Benefit |
---|---|
Clean, dry, temperature-controlled storage | Prevents damage and deterioration of PCBs and components |
ESD protection measures | Protects sensitive components from electrostatic discharge damage |
FIFO inventory management | Ensures components are used within their shelf life, reducing the risk of failures |
Regular inspection of stored items | Allows for early detection and replacement of damaged or deteriorated components |
7. Implement Robust Quality Control Processes
Implementing robust quality control processes throughout the PCB assembly process is essential for ensuring consistent, high-quality results. Key quality control measures include:
- Automated optical inspection (AOI) to detect component placement and soldering issues
- X-ray inspection for hidden solder joints and complex assemblies
- In-circuit testing (ICT) to verify the functionality of individual components and circuits
- Functional testing to ensure the overall performance of the assembled PCB
- Visual inspection by trained operators to identify any visible defects or issues
Quality Control Process Overview
Process | Purpose |
---|---|
Automated optical inspection (AOI) | Detects component placement and soldering issues |
X-ray inspection | Inspects hidden solder joints and complex assemblies |
In-circuit testing (ICT) | Verifies the functionality of individual components and circuits |
Functional testing | Ensures the overall performance of the assembled PCB |
Visual inspection | Identifies any visible defects or issues |
8. Establish Clear Communication Channels
Clear and effective communication between your team and your PCB assembly partner is crucial for project success. Establish communication channels and protocols that facilitate:
- Regular project updates and status reports
- Timely resolution of any issues or concerns
- Efficient exchange of information and documentation
- Collaboration on design improvements and optimization
Communication Best Practices
- Schedule regular project update meetings or calls
- Use a shared project management platform to track progress and share information
- Designate key points of contact within your team and your PCB assembly partner’s team
- Document all important decisions, changes, and agreements
9. Plan for Testing and Validation
Proper testing and validation of your assembled PCBs are essential for ensuring they meet all required specifications and perform as intended. Work with your PCB assembly partner to develop a comprehensive testing and validation plan that includes:
- In-circuit testing (ICT) to verify the functionality of individual components and circuits
- Functional testing to ensure the overall performance of the assembled PCB
- Environmental testing (e.g., temperature, humidity, vibration) to validate the PCB’s performance under real-world conditions
- Compliance testing to ensure the PCB meets all relevant industry standards and regulations
Testing and Validation Checklist
- [ ] In-circuit testing (ICT) plan developed
- [ ] Functional testing plan developed
- [ ] Environmental testing requirements identified
- [ ] Compliance testing requirements identified
- [ ] Testing and validation schedule established
10. Foster a Culture of Continuous Improvement
Continuously improving your PCB assembly process is essential for staying competitive and ensuring long-term success. Foster a culture of continuous improvement by:
- Regularly reviewing and analyzing assembly process data to identify areas for optimization
- Encouraging open communication and feedback from all stakeholders involved in the assembly process
- Investing in employee training and development to enhance skills and knowledge
- Staying up-to-date with industry trends, best practices, and emerging technologies
- Collaborating with your PCB assembly partner to implement process improvements and innovations
Continuous Improvement Strategies
Strategy | Benefit |
---|---|
Regular process data review and analysis | Identifies areas for optimization and improvement |
Open communication and feedback | Encourages stakeholder engagement and ideas for improvement |
Employee training and development | Enhances skills and knowledge, leading to better assembly outcomes |
Industry trend and best practice adoption | Ensures the assembly process remains competitive and up-to-date |
Collaboration with PCB assembly partner | Facilitates the implementation of process improvements and innovations |
By following these top 10 tips, you can ensure the success of your PCB assembly projects, minimize the risk of costly errors and delays, and achieve high-quality results consistently.
Frequently Asked Questions (FAQ)
-
What is the importance of choosing the right PCB assembly partner?
Choosing the right PCB assembly partner is crucial for the success of your project. An experienced and reliable partner will have the necessary expertise, equipment, and quality control processes to ensure high-quality assembly and timely delivery. They can also provide valuable guidance and support throughout the assembly process, helping you optimize your design and avoid potential issues. -
Why is Design for Manufacturability (DFM) important in PCB assembly?
Designing your PCB with manufacturability in mind is essential for successful assembly. By following DFM guidelines, you can optimize your design for the assembly process, minimizing the risk of errors, delays, and cost overruns. DFM considerations include adhering to minimum trace width and spacing requirements, ensuring adequate clearance between components, using standardized component sizes and packages, and optimizing the component layout for automated assembly. -
How can I ensure the quality of the components used in my PCB assembly?
To ensure the quality of the components used in your PCB assembly, it is important to source them from reputable suppliers with a proven track record of quality. Verify that all components meet the required specifications and tolerances and are suitable for the intended operating environment. Consider the lifecycle of the components and choose parts with adequate availability and long-term support. Regularly inspect stored components for signs of damage or deterioration. -
What are some key quality control processes in PCB assembly?
Key quality control processes in PCB assembly include automated optical inspection (AOI) to detect component placement and soldering issues, X-ray inspection for hidden solder joints and complex assemblies, in-circuit testing (ICT) to verify the functionality of individual components and circuits, functional testing to ensure the overall performance of the assembled PCB, and visual inspection by trained operators to identify any visible defects or issues. -
How can I foster a culture of continuous improvement in my PCB assembly process?
Fostering a culture of continuous improvement in your PCB assembly process involves regularly reviewing and analyzing assembly process data to identify areas for optimization, encouraging open communication and feedback from all stakeholders, investing in employee training and development, staying up-to-date with industry trends and best practices, and collaborating with your PCB assembly partner to implement process improvements and innovations. By continuously seeking opportunities for improvement, you can ensure your PCB assembly process remains efficient, competitive, and able to consistently deliver high-quality results.
Leave a Reply