Understanding the Importance of BOM and CPL Data in Manufacturing
In the world of manufacturing, two critical components play a vital role in ensuring the smooth production of goods: the Bill of Materials (BOM) and the Component Parts List (CPL). These documents serve as the backbone of any manufacturing process, providing essential information about the raw materials, components, and assemblies required to create a finished product.
What is a Bill of Materials (BOM)?
A Bill of Materials (BOM) is a comprehensive list of all the raw materials, sub-assemblies, intermediate assemblies, sub-components, parts, and the quantities of each needed to manufacture an end product. It is a hierarchical document that provides a clear understanding of the product structure and the relationships between its components.
BOM Level | Component | Quantity |
---|---|---|
1 | Final Product | 1 |
2 | Sub-assembly A | 1 |
3 | – Part A1 | 2 |
3 | – Part A2 | 1 |
2 | Sub-assembly B | 1 |
3 | – Part B1 | 3 |
3 | – Part B2 | 4 |
2 | Part C | 2 |
The Significance of BOM in Manufacturing
The BOM serves several crucial purposes in the manufacturing process:
-
Product Structure: It provides a clear and organized representation of the product structure, showing how each component relates to the others.
-
Procurement: The BOM helps in identifying the materials and components required for production, enabling efficient procurement planning.
-
Inventory Management: By providing accurate information about the required quantities of each component, the BOM aids in maintaining optimal inventory levels and avoiding stockouts or overstocking.
-
Cost Estimation: The BOM is used to calculate the total cost of production by considering the cost of each component and the associated labor and overhead expenses.
-
Quality Control: The BOM serves as a reference for quality control, ensuring that the correct components are used in the right quantities during production.
The Role of Component Parts List (CPL) in Manufacturing
The Component Parts List (CPL) is a document that complements the BOM by providing more detailed information about each component used in the manufacturing process. It includes specifications, supplier information, and other relevant data for each part.
Key Elements of a CPL
A typical CPL includes the following information for each component:
-
Part Number: A unique identifier for each component.
-
Description: A brief description of the component, including its function and characteristics.
-
Supplier Information: Details about the supplier of the component, such as name, contact information, and lead times.
-
Specifications: Technical specifications of the component, such as dimensions, material, and tolerances.
-
Quantity: The number of units of the component required for each unit of the final product.
Part Number | Description | Supplier | Specifications | Quantity |
---|---|---|---|---|
A1 | Aluminum Bracket | ABC Industries | 2″ x 3″, 6061 Aluminum, ±0.01″ | 2 |
A2 | Steel Bolt | XYZ Fasteners | M6 x 20mm, Grade 8.8 | 1 |
B1 | Plastic Gear | PQR Plastics | 20 teeth, Nylon, ±0.05mm | 3 |
B2 | Rubber Seal | LMN Rubber | 1″ OD, 0.5″ ID, Nitrile | 4 |
C | Circuit Board | EFG Electronics | 2″ x 4″, FR-4, Double-sided | 2 |
The Importance of CPL in Manufacturing
The CPL plays a significant role in several aspects of manufacturing:
-
Procurement: The CPL provides the necessary information for purchasing teams to source the required components from the right suppliers at the best prices.
-
Quality Assurance: By specifying the exact requirements for each component, the CPL helps ensure that the purchased parts meet the desired quality standards.
-
Inventory Management: The CPL aids in maintaining accurate inventory records and tracking the availability of components.
-
Supplier Management: The supplier information in the CPL helps in managing relationships with suppliers, negotiating contracts, and ensuring timely delivery of components.
Integrating BOM and CPL Data for Efficient Manufacturing
To optimize the manufacturing process, it is essential to integrate the information from the BOM and CPL effectively. Here are some tips and tricks for managing BOM and CPL data:
1. Use a Centralized Database
Maintain a centralized database that stores both BOM and CPL information. This ensures that all relevant data is easily accessible and updates can be made efficiently.
2. Implement Version Control
Establish a version control system for BOMs and CPLs to track changes and maintain a history of revisions. This helps in identifying the most up-to-date information and avoiding confusion.
3. Automate Data Entry
Utilize automation tools to streamline the process of entering and updating BOM and CPL data. This reduces the risk of manual errors and saves time.
4. Integrate with Other Systems
Integrate the BOM and CPL database with other systems, such as Enterprise Resource Planning (ERP) or Product Lifecycle Management (PLM) software. This enables seamless data flow and ensures consistency across different departments.
5. Conduct Regular Audits
Perform regular audits of the BOM and CPL data to ensure accuracy and completeness. This helps in identifying and rectifying any discrepancies or outdated information.
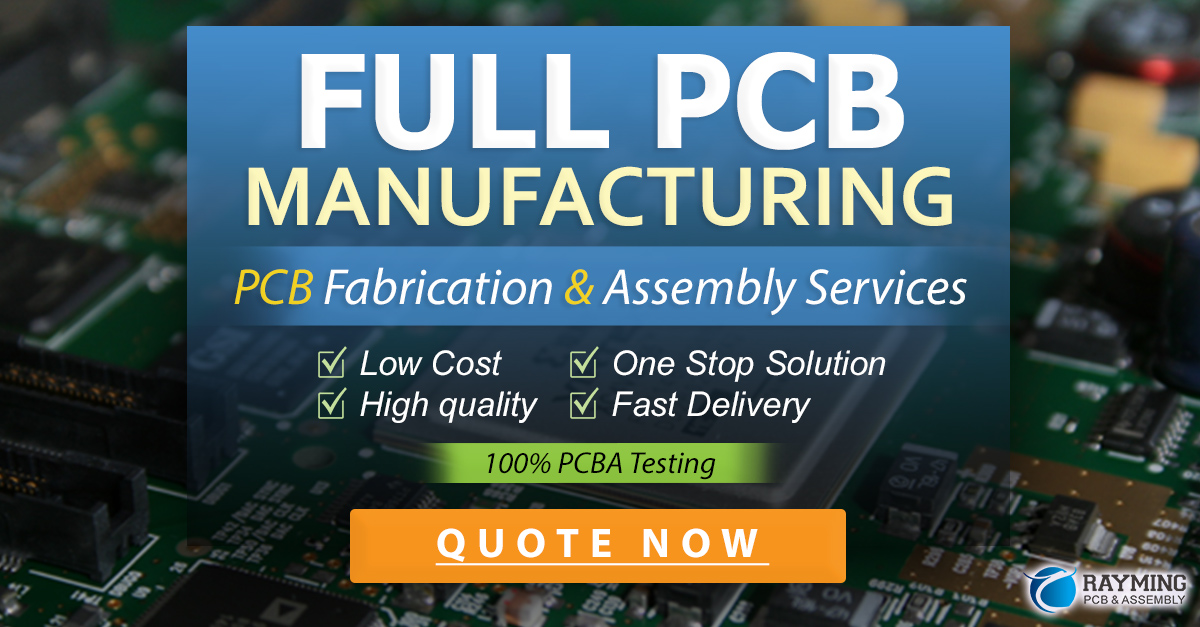
Case Study: Implementing BOM and CPL Best Practices
To illustrate the benefits of effective BOM and CPL management, let’s consider a case study of ABC Manufacturing Company.
Before implementing best practices, ABC Manufacturing faced several challenges:
- Inconsistent and outdated BOM and CPL data
- Frequent stockouts and overstocking of components
- Delays in production due to missing or incorrect parts
- Difficulty in tracking supplier performance and lead times
To address these issues, ABC Manufacturing took the following steps:
- Developed a centralized database for BOM and CPL information
- Implemented a version control system to track changes
- Automated data entry using barcode scanning and integration with their ERP system
- Conducted regular audits to ensure data accuracy and completeness
- Established key performance indicators (KPIs) to monitor supplier performance and lead times
The results were remarkable:
- Reduced stockouts by 35% and overstocking by 40%
- Improved on-time delivery of finished products by 25%
- Decreased production delays caused by missing or incorrect parts by 50%
- Enhanced supplier relationships and negotiated better contracts
By implementing these best practices, ABC Manufacturing streamlined their operations, reduced costs, and improved overall efficiency.
Frequently Asked Questions (FAQ)
-
What is the difference between a BOM and a CPL?
A BOM is a hierarchical list of all the components and materials required to manufacture a product, while a CPL provides detailed information about each component, such as specifications and supplier details. -
Why is it important to maintain accurate BOM and CPL data?
Accurate BOM and CPL data is essential for efficient procurement, inventory management, cost estimation, and quality control. It helps in avoiding production delays, stockouts, and overstocking, ultimately leading to cost savings and improved customer satisfaction. -
How can I ensure consistency between BOM and CPL data?
Maintaining a centralized database and implementing version control can help ensure consistency between BOM and CPL data. Regular audits and automated data entry can also minimize discrepancies. -
What are the benefits of integrating BOM and CPL data with other systems?
Integrating BOM and CPL data with ERP or PLM systems enables seamless data flow, reduces manual errors, and ensures consistency across different departments. It also facilitates better decision-making by providing real-time information. -
How often should I review and update BOM and CPL data?
It is recommended to review and update BOM and CPL data regularly, especially when there are changes in product design, suppliers, or specifications. The frequency of updates may vary depending on the complexity of the product and the dynamics of the supply chain.
Conclusion
Effective management of BOM and CPL data is crucial for the success of any manufacturing organization. By understanding the importance of these documents and implementing best practices for data management, companies can streamline their operations, reduce costs, and improve overall efficiency.
Investing in a centralized database, version control, automation, and regular audits can help ensure the accuracy and consistency of BOM and CPL data. Integrating this information with other systems, such as ERP or PLM software, further enhances the benefits by enabling seamless data flow and better decision-making.
By following the tips and tricks outlined in this article and learning from the success story of ABC Manufacturing, organizations can optimize their BOM and CPL management practices and achieve significant improvements in their manufacturing processes.
Leave a Reply