Introduction to PCB Wiring
Printed Circuit Board (PCB) wiring is a crucial aspect of electronic device manufacturing. It involves the process of connecting various components on a PCB using conductive traces, pads, and vias. Proper PCB wiring ensures the reliability, functionality, and longevity of the electronic device. In this article, we will discuss the essential tips and techniques for effective PCB wiring.
Understanding the Basics of PCB Wiring
PCB Layers and Their Functions
PCBs are made up of multiple layers, each serving a specific purpose. The most common PCB layers include:
Layer | Function |
---|---|
Copper Layer | Conducts electrical signals between components |
Substrate Layer | Provides mechanical support and insulation |
Solder Mask Layer | Protects the copper layer from oxidation and short circuits |
Silkscreen Layer | Contains text and symbols for component identification |
Types of PCB Wiring
There are two main types of PCB wiring:
- Through-Hole Wiring: Components are inserted into drilled holes and soldered on the opposite side of the board.
- Surface Mount Wiring: Components are placed directly on the surface of the PCB and soldered using solder paste.
PCB Wiring Materials
The choice of materials for PCB wiring depends on the specific requirements of the electronic device. Common materials include:
- Copper: The most widely used conductor in PCB wiring due to its excellent electrical conductivity and low cost.
- Gold: Used for high-reliability applications due to its corrosion resistance and excellent conductivity.
- Aluminum: A lightweight and cost-effective alternative to copper for some applications.
PCB Wiring Design Considerations
Schematic Design
The first step in PCB wiring is to create a schematic diagram that represents the electrical connections between components. The schematic should include:
- Component symbols and their values
- Power and ground connections
- Signal paths and their associated nets
PCB Layout Design
Once the schematic is complete, the next step is to design the PCB layout. The layout should consider:
- Component placement for optimal signal routing
- Trace width and spacing to minimize crosstalk and electromagnetic interference (EMI)
- Via placement and sizing for efficient signal transfer between layers
- Power and ground plane design for stable power distribution
Signal Integrity and EMI Reduction
To ensure signal integrity and reduce EMI, consider the following techniques:
- Use proper trace routing techniques, such as avoiding sharp bends and minimizing trace length
- Implement appropriate grounding strategies, such as using ground planes and proper grounding of components
- Use decoupling capacitors to reduce power supply noise and improve signal quality
- Implement shielding techniques, such as using shielded cables and enclosures, to minimize EMI
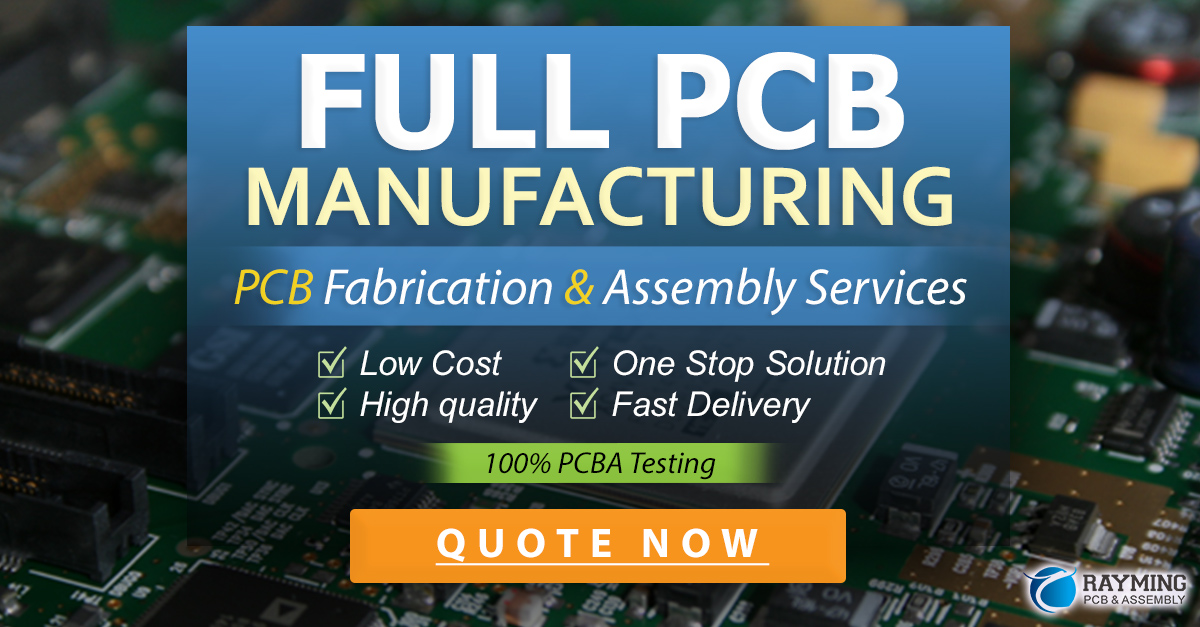
PCB Wiring Techniques
Soldering
Soldering is the process of joining two metal surfaces using a molten filler material (solder). Proper soldering techniques are essential for reliable PCB wiring. Some tips for effective soldering include:
- Use the appropriate solder alloy and flux for the application
- Control the soldering iron temperature to avoid damaging components or the PCB
- Use proper soldering techniques, such as keeping the soldering iron tip clean and applying the right amount of solder
Crimping
Crimping is the process of creating a solid mechanical and electrical connection between a wire and a connector. Proper crimping techniques ensure a reliable and secure connection. Some tips for effective crimping include:
- Use the appropriate crimping tool and die for the wire size and connector type
- Strip the wire to the correct length and insert it fully into the connector
- Apply the right amount of pressure when crimping to create a secure connection
Wire Harness Assembly
A wire harness is a group of wires or cables bundled together to transmit signals or power. Proper wire harness assembly is crucial for organizing and protecting the wires. Some tips for effective wire harness assembly include:
- Use the appropriate wire gauge and insulation for the application
- Route the wires to minimize strain and avoid sharp bends
- Use cable ties or lacing to bundle the wires securely
- Label the wires for easy identification and troubleshooting
PCB Wiring Testing and Inspection
Visual Inspection
Visual inspection is the first step in PCB wiring testing. It involves checking the PCB for any visible defects or anomalies, such as:
- Solder bridges or short circuits
- Cold solder joints or insufficient solder
- Damaged or missing components
- Incorrect component placement or orientation
Continuity Testing
Continuity testing is used to verify that there is a continuous electrical path between two points on the PCB. This can be done using a multimeter or a dedicated continuity tester. Some tips for effective continuity testing include:
- Set the multimeter to the continuity or resistance mode
- Place the probes on the two points to be tested
- Check for a low resistance reading (typically less than 1 ohm) to indicate continuity
Functional Testing
Functional testing involves powering up the PCB and verifying that it performs as expected. This includes checking for:
- Proper power supply voltages
- Correct signal levels and timing
- Proper operation of all components and features
PCB Wiring Best Practices
Use a Consistent Wiring Scheme
Using a consistent wiring scheme helps to ensure that the PCB is easy to understand and maintain. This includes:
- Using a consistent color coding scheme for power, ground, and signal wires
- Labeling all wires and components clearly
- Following industry-standard wiring conventions, such as the IPC-A-610 standard
Keep Wiring Neat and Organized
Keeping the PCB wiring neat and organized helps to minimize errors and makes the PCB easier to troubleshoot. Some tips for keeping wiring neat and organized include:
- Route wires in straight lines and avoid crossing them whenever possible
- Use cable ties or lacing to bundle wires together
- Keep wires as short as possible to minimize signal loss and interference
Document the Wiring Process
Documenting the PCB wiring process helps to ensure that the PCB can be easily replicated or modified in the future. This includes:
- Creating detailed wiring diagrams and schematics
- Taking photos or videos of the wiring process
- Writing clear and concise assembly instructions
FAQ
What is the difference between through-hole and surface mount wiring?
Through-hole wiring involves inserting component leads through holes drilled in the PCB and soldering them on the opposite side. Surface mount wiring involves placing components directly on the surface of the PCB and soldering them using solder paste.
What is the purpose of a solder mask on a PCB?
The solder mask is a protective layer that covers the copper traces on the PCB. It prevents short circuits and protects the copper from oxidation and damage during the soldering process.
What is the difference between crimping and soldering?
Crimping involves creating a mechanical and electrical connection between a wire and a connector using pressure. Soldering involves joining two metal surfaces using a molten filler material (solder) to create an electrical connection.
What is the purpose of a wire harness in PCB wiring?
A wire harness is a group of wires or cables bundled together to transmit signals or power. It helps to organize and protect the wires, making the PCB easier to assemble and maintain.
What are some common PCB wiring testing methods?
Common PCB wiring testing methods include visual inspection, continuity testing, and functional testing. Visual inspection involves checking the PCB for visible defects or anomalies. Continuity testing verifies that there is a continuous electrical path between two points on the PCB. Functional testing involves powering up the PCB and verifying that it performs as expected.
Conclusion
PCB wiring is a critical aspect of electronic device manufacturing that requires careful planning, design, and execution. By understanding the basics of PCB wiring, considering design factors such as signal integrity and EMI reduction, and following best practices for wiring techniques and testing, you can ensure that your PCB is reliable, functional, and long-lasting. Remember to always use high-quality materials, follow industry standards, and document your wiring process for future reference.
Leave a Reply