Introduction to Through-hole PCB Technology
Through-hole technology (THT) is a method of printed circuit board (PCB) fabrication where components are mounted by inserting their leads through drilled holes in the board and soldering them to pads on the opposite side. This technology has been a staple in the electronics industry for decades, despite the growing popularity of surface mount technology (SMT). Through-hole PCBs offer several advantages, such as superior mechanical stability, ease of manual assembly, and the ability to handle high-power components.
Advantages of Through-hole PCB Technology
- Mechanical stability: Through-hole components are firmly anchored to the board, making them resistant to vibration and physical stress.
- Ease of manual assembly: Through-hole components are easier to handle and solder manually compared to their SMT counterparts.
- High-power handling: Through-hole components can dissipate heat more effectively due to their larger size and stronger connections to the board.
- Prototyping: Through-hole technology is often preferred for prototyping and low-volume production due to its simplicity and lower setup costs.
Disadvantages of Through-hole PCB Technology
- Size: Through-hole components are generally larger than SMT components, which can limit the board’s component density and overall size reduction.
- Drilling: The need for drilled holes in the board adds an extra manufacturing step and can increase production time and costs.
- Automated assembly: Through-hole components are less suitable for high-volume, automated assembly processes compared to SMT components.
- Signal integrity: The longer leads of through-hole components can introduce unwanted inductance and capacitance, which can affect high-frequency signal integrity.
Through-hole PCB Manufacturing Process
The manufacturing process for through-hole PCBs involves several key steps, including board design, drilling, plating, component insertion, and soldering.
1. Board Design
The first step in through-hole PCB manufacturing is designing the board layout using electronic design automation (EDA) software. The designer must consider factors such as component placement, hole sizes, pad sizes, and trace routing to ensure optimal performance and manufacturability.
2. Drilling
Once the board design is finalized, the next step is to drill holes in the PCB substrate for component leads. This process is typically carried out using computer numerical control (CNC) drilling machines, which can precisely drill holes of various sizes and patterns based on the design files.
3. Plating
After drilling, the holes are plated with a conductive material, usually copper, to create electrical connections between the layers of the PCB. This process involves several sub-steps:
a. Desmearing: Removing any resin smear from the drilled holes to ensure proper adhesion of the plating material.
b. Electroless copper deposition: Applying a thin layer of copper to the hole walls using a chemical process.
c. Electrolytic copper plating: Building up the copper layer to the desired thickness using an electric current.
4. Component Insertion
Once the board is plated, the through-hole components are inserted into their respective holes. This process can be done manually for low-volume production or prototyping, or using automated insertion machines for high-volume production.
5. Soldering
The final step in the manufacturing process is soldering the component leads to the pads on the opposite side of the board. This creates a strong mechanical and electrical connection between the components and the PCB. Soldering can be done manually using a soldering iron or using automated wave soldering or selective soldering machines for high-volume production.
Types of Through-hole Components
Through-hole components come in various packages and sizes to accommodate different design requirements. Some common types of through-hole components include:
- Dual In-line Package (DIP): A rectangular package with two parallel rows of leads, commonly used for integrated circuits (ICs) and sockets.
- Single In-line Package (SIP): Similar to DIP but with only one row of leads, often used for resistor networks and connectors.
- Radial Lead: Components with leads extending from the body in a circular pattern, such as capacitors and inductors.
- Axial Lead: Components with leads extending from opposite ends of the body, such as resistors and diodes.
Component Type | Description | Typical Applications |
---|---|---|
DIP | Rectangular package with two parallel rows of leads | ICs, sockets |
SIP | Rectangular package with one row of leads | Resistor networks, connectors |
Radial Lead | Leads extend from the body in a circular pattern | Capacitors, inductors |
Axial Lead | Leads extend from opposite ends of the body | Resistors, diodes |
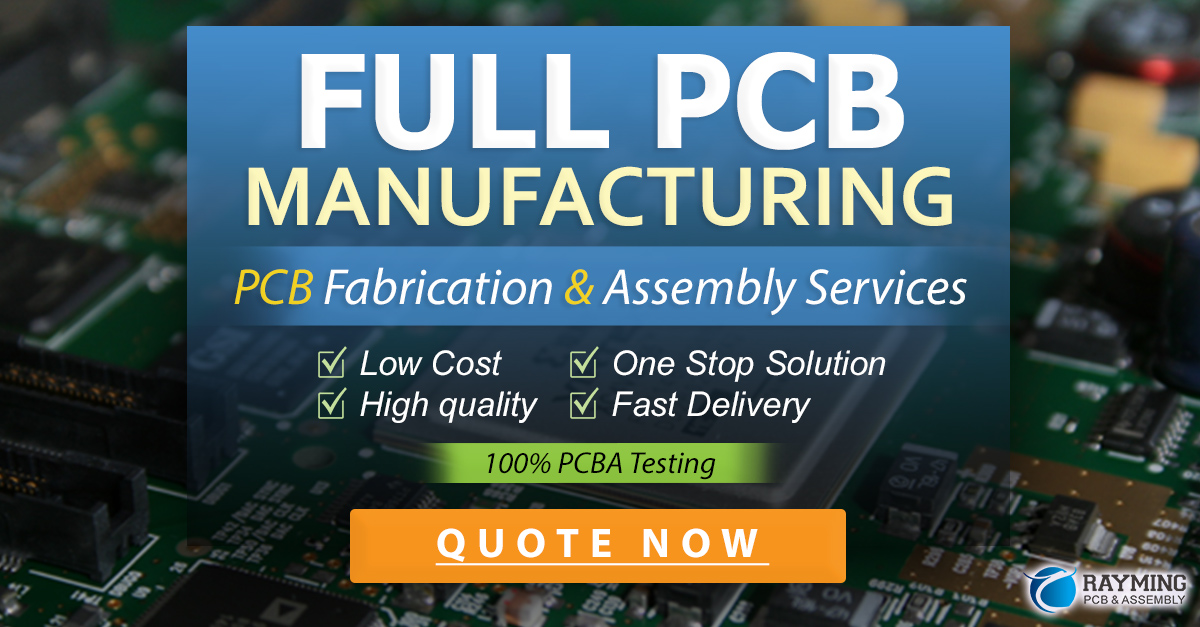
Through-hole PCB Design Considerations
When designing through-hole PCBs, several key factors must be considered to ensure optimal performance and manufacturability:
1. Hole Size and Pad Size
The hole size and pad size must be appropriately selected based on the component lead diameter and the required mechanical strength. A general rule of thumb is to make the hole diameter about 0.2-0.3 mm larger than the lead diameter, and the pad diameter about 0.5-0.7 mm larger than the hole diameter.
2. Drill to Copper Clearance
Sufficient clearance must be maintained between the drilled holes and the copper traces to prevent short circuits and ensure proper insulation. The minimum drill to copper clearance depends on the PCB manufacturing process and the board’s voltage requirements.
3. Component Placement
Components should be placed on the board in a way that minimizes the overall board size, reduces the length of traces, and facilitates efficient assembly. It is also important to consider the component’s thermal dissipation requirements and the board’s mechanical constraints.
4. Trace Routing
Traces should be routed to minimize their length, avoid sharp angles, and maintain sufficient spacing between adjacent traces to reduce crosstalk and signal integrity issues. The trace width and thickness should be selected based on the current carrying requirements and the desired impedance.
Advantages of Combining Through-hole and Surface Mount Technology
While through-hole and surface mount technologies have their own distinct advantages, combining the two in a single PCB design can offer the best of both worlds. This approach, known as mixed-technology PCB assembly, allows designers to leverage the strengths of each technology to create more efficient and cost-effective boards.
1. Mechanical Stability and High-power Handling
Using through-hole components for mechanically critical parts or high-power components can provide the necessary stability and heat dissipation, while surface mount components can be used for the rest of the board to save space and reduce manufacturing costs.
2. Ease of Assembly and Rework
Through-hole components can be used for parts that may require manual assembly or rework, such as connectors or programming headers, while surface mount components can be used for the majority of the board to facilitate automated assembly.
3. Cost Optimization
By selectively using through-hole components where necessary and surface mount components elsewhere, designers can optimize the overall cost of the PCB assembly process. This can be particularly beneficial for high-volume production, where the cost savings can add up quickly.
Frequently Asked Questions (FAQ)
- What is the difference between through-hole and surface mount technology?
-
Through-hole technology involves mounting components by inserting their leads through drilled holes in the PCB and soldering them to pads on the opposite side. Surface mount technology, on the other hand, involves mounting components directly onto the surface of the PCB without the need for drilled holes.
-
When should I use through-hole technology instead of surface mount technology?
-
Through-hole technology is often preferred when mechanical stability, ease of manual assembly, or high-power handling are critical factors. It is also commonly used for prototyping and low-volume production due to its simplicity and lower setup costs.
-
Can through-hole and surface mount components be used together on the same PCB?
-
Yes, combining through-hole and surface mount components on the same PCB is known as mixed-technology PCB assembly. This approach allows designers to leverage the strengths of each technology to create more efficient and cost-effective boards.
-
What are the main steps involved in the through-hole PCB manufacturing process?
-
The main steps in through-hole PCB manufacturing include board design, drilling, plating, component insertion, and soldering.
-
How do I select the appropriate hole size and pad size for through-hole components?
- As a general rule, the hole diameter should be about 0.2-0.3 mm larger than the component lead diameter, and the pad diameter should be about 0.5-0.7 mm larger than the hole diameter. However, the exact sizes may vary depending on the specific component and the PCB manufacturing process.
Conclusion
Through-hole technology remains an important part of PCB fabrication, offering unique advantages such as mechanical stability, ease of manual assembly, and high-power handling. Despite the growing popularity of surface mount technology, through-hole PCBs continue to play a vital role in prototyping, low-volume production, and applications that require robust and reliable component mounting.
By understanding the through-hole PCB manufacturing process, the types of through-hole components available, and the key design considerations, engineers and designers can create effective and efficient PCBs that meet their specific requirements. Furthermore, by combining through-hole and surface mount technologies in a mixed-technology PCB assembly approach, they can leverage the strengths of each technology to optimize performance, cost, and manufacturability.
As the electronics industry continues to evolve, it is clear that through-hole technology will remain a valuable tool in the PCB fabrication toolkit, complementing surface mount technology to enable the development of increasingly sophisticated and reliable electronic devices.
Leave a Reply