Introduction to Copper PCBs
Printed Circuit Boards (PCBs) are the backbone of modern electronics. They provide a platform for electrical components to be mounted and interconnected, enabling the creation of complex circuits and systems. One crucial aspect of PCB design is the choice of materials, particularly the copper layer thickness. Thick copper PCBs have gained popularity in recent years due to their unique properties and advantages in certain applications.
What are Thick Copper PCBs?
Thick copper PCBs, also known as heavy copper PCBs, are printed circuit boards that feature copper layers thicker than the standard 1 oz (35 μm) used in most PCBs. These boards typically have copper thicknesses ranging from 2 oz (70 μm) to 20 oz (700 μm) or even more in some cases. The increased copper thickness provides several benefits, such as improved current carrying capacity, better heat dissipation, and enhanced mechanical strength.
Applications of Thick Copper PCBs
Thick copper PCBs find applications in various industries and domains where high current, high power, or thermal management is crucial. Some common applications include:
- Power electronics: Thick copper PCBs are extensively used in power supply units, motor drives, inverters, and other power-intensive applications.
- Automotive electronics: In the automotive industry, thick copper PCBs are employed in high-current systems like starter motors, alternators, and battery management systems.
- LED lighting: LED lighting applications often require thick copper PCBs to handle the high current demands and ensure efficient heat dissipation.
- Industrial control systems: Thick copper PCBs are used in industrial Control Panels, sensors, and actuators to withstand harsh environments and handle high currents.
- Aerospace and defense: In aerospace and defense applications, thick copper PCBs provide the necessary reliability and robustness to withstand extreme conditions and ensure optimal performance.
Advantages of Thick Copper PCBs
Improved Current Carrying Capacity
One of the primary advantages of thick copper PCBs is their enhanced current carrying capacity. As the copper thickness increases, the cross-sectional area of the copper traces also increases, allowing them to handle higher currents without overheating or experiencing voltage drops. This is particularly important in power-intensive applications where high current flows are common.
The relationship between copper thickness and current carrying capacity can be approximated using the following formula:
I = kΔT0.44A0.725
Where:
– I is the maximum allowable current (in Amps)
– ΔT is the temperature rise above ambient (in °C)
– A is the cross-sectional area of the copper trace (in mils2)
– k is a constant that depends on the copper thickness (typically 0.048 for 1 oz copper)
By increasing the copper thickness, the cross-sectional area (A) of the traces increases, resulting in a higher maximum allowable current (I) for a given temperature rise (ΔT).
Enhanced Heat Dissipation
Thick copper PCBs also offer improved heat dissipation capabilities. As electronic components generate heat during operation, it is crucial to efficiently dissipate that heat to prevent overheating and ensure reliable performance. The increased copper thickness provides a larger surface area and thermal mass, allowing for better heat spreading and conduction.
The thermal conductivity of copper (approximately 400 W/mK) is much higher than that of the PCB substrate material (typically around 0.3 W/mK for FR-4). By having thicker copper layers, the heat generated by components can be quickly conducted away from the source and spread across the board, reducing localized hot spots and improving overall thermal management.
Improved Mechanical Strength
Thick copper PCBs also offer enhanced mechanical strength and durability compared to standard PCBs. The increased copper thickness provides additional rigidity and resistance to bending, twisting, and other mechanical stresses. This is particularly advantageous in applications where the PCB is subjected to vibrations, shocks, or harsh environmental conditions.
The improved mechanical strength of thick copper PCBs can help prevent issues such as trace cracking, delamination, and component detachment, leading to increased reliability and longer product lifetimes.
Design Considerations for Thick Copper PCBs
Trace Width and Spacing
When designing thick copper PCBs, it is important to consider the trace width and spacing to ensure proper current carrying capacity and signal integrity. As the copper thickness increases, the minimum trace width and spacing also need to be adjusted accordingly.
The following table provides general guidelines for minimum trace width and spacing based on copper thickness:
Copper Thickness (oz) | Minimum Trace Width (mm) | Minimum Spacing (mm) |
---|---|---|
1 | 0.15 | 0.15 |
2 | 0.20 | 0.20 |
3 | 0.25 | 0.25 |
4 | 0.30 | 0.30 |
6 | 0.40 | 0.40 |
8 | 0.50 | 0.50 |
10 | 0.60 | 0.60 |
It is important to note that these are general guidelines, and the actual trace width and spacing requirements may vary depending on the specific application, PCB material, and manufacturing capabilities. It is always recommended to consult with the PCB manufacturer and adhere to their design rules and guidelines.
Via Design
Via design is another critical aspect when working with thick copper PCBs. Vias are used to interconnect different layers of the PCB and provide electrical connectivity between components. In thick copper PCBs, the via design needs to be optimized to ensure proper current flow and minimize resistance.
Some key considerations for via design in thick copper PCBs include:
-
Via diameter: The via diameter should be large enough to accommodate the increased copper thickness and ensure reliable electrical connections. Larger via diameters may be necessary for thicker copper layers.
-
Via Plating: The via plating thickness should be sufficient to handle the high currents flowing through the vias. Insufficient plating can lead to voltage drops and increased resistance.
-
Via placement: Vias should be strategically placed to minimize the distance between components and reduce the overall current path length. This helps in reducing voltage drops and improving overall efficiency.
-
Thermal Vias: In applications where heat dissipation is critical, thermal vias can be used to transfer heat from components to the copper layers and eventually to the heatsink or cooling system. Thermal vias are typically placed directly under or near the heat-generating components.
Thermal Management
Thermal management is a key consideration when designing thick copper PCBs. While the increased copper thickness helps in heat dissipation, it is still important to implement proper thermal management techniques to ensure optimal performance and reliability.
Some thermal management strategies for thick copper PCBs include:
-
Heatsinks: Attaching heatsinks to high-power components can help in dissipating heat more efficiently. The thick copper layers provide a good thermal interface for heatsink attachment.
-
Thermal vias: As mentioned earlier, thermal vias can be used to transfer heat from components to the copper layers and eventually to the heatsink or cooling system.
-
Copper pours: Using copper pours or planes on the PCB can help in spreading the heat more evenly across the board. Copper pours act as heat spreaders and can be strategically placed to improve overall thermal performance.
-
Airflow management: Proper airflow management is crucial to ensure that the heat generated by components is effectively removed from the system. This can be achieved through the use of fans, vents, or other cooling solutions.
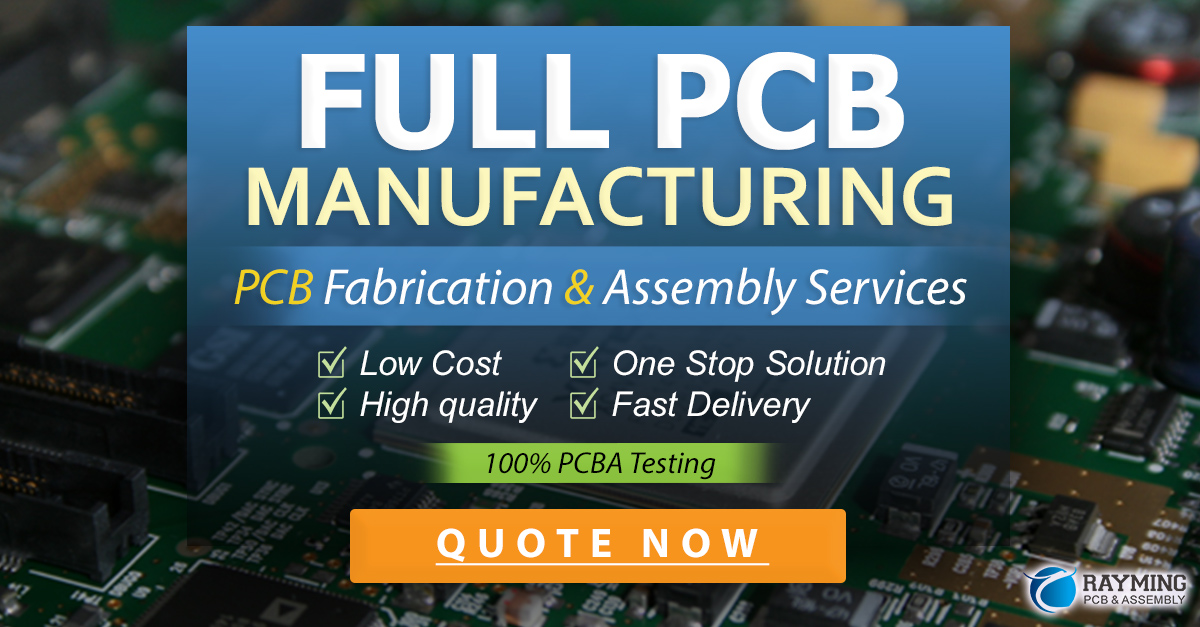
Manufacturing Process of Thick Copper PCBs
The manufacturing process of thick copper PCBs is similar to that of standard PCBs, with a few additional considerations and steps to accommodate the increased copper thickness.
PCB Stackup
The PCB stackup refers to the arrangement of copper layers, dielectric materials, and other layers that make up the PCB. In thick copper PCBs, the stackup needs to be carefully designed to ensure proper electrical performance and mechanical stability.
A typical stackup for a thick copper PCB may include:
- Copper layers: The number and thickness of copper layers depend on the specific application requirements. Thick copper PCBs often have multiple copper layers with thicknesses ranging from 2 oz to 20 oz or more.
- Dielectric layers: The dielectric layers provide electrical insulation between the copper layers. The choice of dielectric material depends on factors such as the desired impedance, thermal properties, and manufacturability.
- Solder mask: The solder mask layer is applied on top of the outer copper layers to protect the copper traces and prevent short circuits during soldering.
- Silkscreen: The silkscreen layer is used for component labeling and marking on the PCB surface.
Copper Plating
The increased copper thickness in thick copper PCBs is achieved through a process called copper plating. There are two main methods for copper plating: electroless plating and electrolytic plating.
-
Electroless plating: In this method, the copper is deposited onto the PCB substrate through a chemical reaction without the use of an external electrical current. Electroless plating provides a uniform copper thickness across the board but is limited in terms of the maximum achievable thickness.
-
Electrolytic plating: Electrolytic plating involves the use of an electrical current to deposit copper onto the PCB substrate. This method allows for higher copper thicknesses and faster plating rates compared to electroless plating. However, it requires proper control of the plating parameters to ensure uniform Copper Distribution.
Etching and Finishing
After the copper plating process, the PCB undergoes etching to remove the unwanted copper and create the desired circuit patterns. The etching process for thick copper PCBs requires careful control to ensure accurate trace widths and spacing.
Once the etching is complete, the PCB undergoes various finishing processes, such as solder mask application, surface finish (e.g., HASL, ENIG, OSP), and silkscreen printing. These finishing steps help protect the copper traces, improve solderability, and enhance the overall appearance and functionality of the PCB.
Testing and Quality Control
To ensure the reliability and performance of thick copper PCBs, rigorous testing and quality control measures are implemented throughout the manufacturing process.
Some common testing methods for thick copper PCBs include:
-
Electrical testing: This involves testing the continuity, isolation, and electrical properties of the PCB to ensure proper functionality and adherence to design specifications.
-
Visual inspection: Visual inspection is performed to check for any surface defects, such as scratches, dents, or discolorations, and to verify the accuracy of the silkscreen and solder mask.
-
Microsectioning: Microsectioning involves cross-sectioning the PCB and examining the internal layers under a microscope to verify the copper thickness, plating quality, and layer alignment.
-
Thermal cycling: Thermal cycling tests are conducted to assess the PCB’s ability to withstand temperature variations and thermal stress. The PCB is subjected to multiple cycles of heating and cooling to simulate real-world operating conditions.
-
High-current testing: For thick copper PCBs designed for high-current applications, specialized testing is performed to verify the current carrying capacity and thermal performance under load conditions.
These testing methods help identify any potential issues or defects early in the manufacturing process, allowing for corrective actions to be taken before the PCBs are assembled and deployed in the final application.
Frequently Asked Questions (FAQ)
- What is the maximum copper thickness achievable in thick copper PCBs?
-
The maximum copper thickness in thick copper PCBs can reach up to 20 oz (700 μm) or even more in some special cases. However, the practical limit depends on the specific manufacturing capabilities and design requirements.
-
Are thick copper PCBs more expensive than standard PCBs?
-
Yes, thick copper PCBs are generally more expensive than standard PCBs due to the additional material costs and specialized manufacturing processes involved. The cost increase depends on factors such as the copper thickness, board size, and complexity of the design.
-
Can thick copper PCBs be used for high-frequency applications?
-
Thick copper PCBs are primarily used for high-current and thermal management applications. While they can be used in high-frequency applications, the increased copper thickness may introduce challenges related to impedance control and signal integrity. Careful design considerations and simulations are necessary to ensure optimal performance in high-frequency applications.
-
How does the increased copper thickness affect the PCB’s weight?
-
The increased copper thickness in thick copper PCBs results in a higher overall weight compared to standard PCBs. This is because copper is a dense material, and the additional thickness adds to the board’s mass. The weight increase should be considered when designing for weight-sensitive applications.
-
Are there any limitations in terms of the minimum feature size in thick copper PCBs?
- Yes, the minimum feature size (e.g., trace width and spacing) in thick copper PCBs is generally larger compared to standard PCBs. This is due to the limitations in etching and plating processes when dealing with thicker copper layers. It is important to consult with the PCB manufacturer and adhere to their design guidelines to ensure manufacturability and reliability.
Conclusion
Thick copper PCBs offer numerous advantages over standard PCBs, particularly in applications that require high current carrying capacity, enhanced heat dissipation, and improved mechanical strength. By increasing the copper thickness, these PCBs can handle higher power levels, dissipate heat more effectively, and withstand harsh environmental conditions.
However, designing and manufacturing thick copper PCBs also presents challenges and considerations that differ from standard PCBs. Trace width and spacing, via design, thermal management, and manufacturing processes need to be carefully optimized to ensure optimal performance and reliability.
When considering thick copper PCBs for a particular application, it is essential to weigh the benefits against the increased cost and design complexities. Close collaboration with PCB manufacturers and adherence to their design guidelines are crucial for successful implementation.
As technology advances and the demand for high-power electronics continues to grow, thick copper PCBs will likely play an increasingly important role in enabling the development of robust and efficient systems across various industries.
Leave a Reply