What is FR4 PCB?
FR4 PCB stands for Flame Retardant 4 Printed Circuit Board. It is the most widely used base material for PCBs due to its excellent mechanical, electrical, and thermal properties. FR4 is a composite material composed of woven fiberglass cloth with an epoxy resin binder that is flame resistant.
Key Characteristics of FR4 PCB
- High mechanical strength and dimensional stability
- Excellent electrical insulation properties
- Good resistance to heat and moisture
- Flame retardant
- Cost-effective
Advantages of Using FR4 PCB
1. Durability and Reliability
FR4 PCBs are known for their durability and long-term reliability. The high-quality materials used in their construction make them resistant to wear and tear, impact damage, and environmental factors such as heat, humidity, and chemicals. This makes FR4 PCBs suitable for a wide range of applications, from consumer electronics to industrial equipment.
2. Excellent Electrical Properties
One of the key advantages of FR4 PCBs is their excellent electrical insulation properties. The glass reinforced epoxy laminate provides high dielectric strength and low dielectric constant, which minimizes signal loss and ensures reliable performance even at high frequencies.
The typical electrical properties of FR4 PCB are:
Property | Value |
---|---|
Dielectric Constant (1 MHz) | 4.7 |
Dielectric Strength | >50 kV/mm |
Volume Resistivity | 10^14 ohm-cm |
Surface Resistivity | 10^12 ohm |
Loss Tangent (1 MHz) | 0.02 |
3. Thermal Stability
FR4 PCBs have good thermal stability, with a glass transition temperature (Tg) of around 130°C to 140°C. This allows them to withstand the heat generated by electronic components during operation without deforming or losing their mechanical properties. The thermal conductivity of FR4 is also relatively low, which helps to dissipate heat and prevent hot spots on the PCB.
4. Cost-Effectiveness
Compared to other PCB materials like polyimide or ceramic, FR4 offers a cost-effective solution for most applications. The raw materials used in FR4 production are readily available, and the manufacturing process is well-established and efficient. This makes FR4 PCBs an affordable choice for both prototyping and mass production.
Applications of FR4 PCB
FR4 PCBs are used in a wide variety of electronic applications across different industries:
1. Consumer Electronics
- Smartphones and tablets
- Laptops and desktop computers
- TVs and home appliances
- Gaming consoles and peripherals
2. Automotive Electronics
- Engine control units (ECUs)
- Infotainment systems
- Driver assistance systems
- Electric vehicle charging systems
3. Industrial Electronics
- Process control systems
- Automation and robotics
- Power electronics
- Instrumentation and measurement equipment
4. Medical Devices
- Diagnostic and monitoring equipment
- Implantable devices
- Surgical instruments
- Medical imaging systems
5. Aerospace and Defense
- Avionics systems
- Radar and communication equipment
- Satellite components
- Military-grade electronics
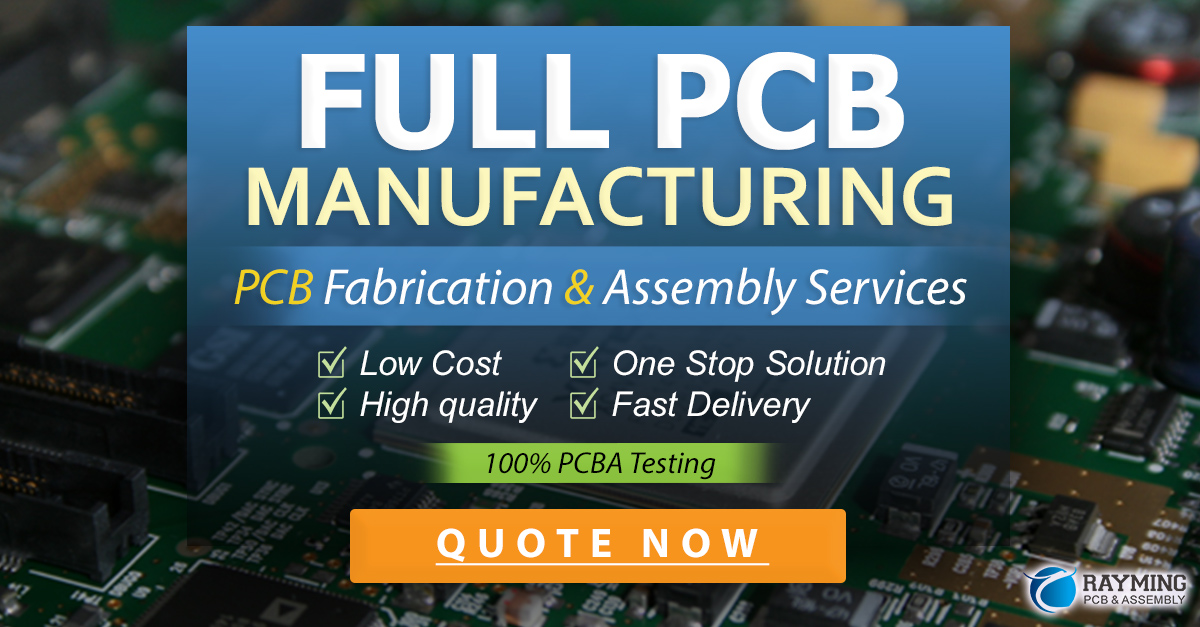
Manufacturing Process of FR4 PCB
The manufacturing process of FR4 PCBs involves several steps:
-
Design and Artwork Creation: The PCB design is created using CAD software, and the artwork files are generated for each layer of the board.
-
Material Selection and Cutting: The FR4 Laminate sheets are selected based on the required thickness and copper weight. The sheets are then cut to the desired size using a CNC machine or laser cutter.
-
Drilling: Holes are drilled into the laminate sheets to accommodate through-hole components and vias.
-
Copper Deposition: A thin layer of copper is deposited onto the laminate sheets using an electroless plating process.
-
Patterning: The copper layer is patterned using photolithography and etching techniques to create the desired circuit traces and pads.
-
Lamination: Multiple layers of patterned FR4 sheets are stacked and laminated together under high pressure and temperature to form a multi-layer PCB.
-
Solder Mask Application: A solder mask layer is applied onto the PCB surface to protect the copper traces from oxidation and prevent solder bridging during assembly.
-
Surface Finishing: The exposed copper pads are coated with a surface finish, such as HASL, ENIG, or OSP, to improve solderability and protect against corrosion.
-
Silkscreen Printing: The component labels, logos, and other markings are printed onto the PCB surface using silkscreen printing.
-
Electrical Testing: The finished PCB is subjected to electrical testing to ensure proper functionality and connectivity.
Future Trends in FR4 PCB Technology
As electronic devices continue to evolve and become more complex, the demands on PCB technology also increase. Here are some of the future trends in FR4 PCB technology:
1. High-Speed and High-Frequency Applications
With the growing demand for faster data transmission and higher bandwidth, FR4 PCBs are being optimized for high-speed and high-frequency applications. This involves the use of low-loss materials, controlled impedance designs, and advanced manufacturing techniques to minimize signal distortion and crosstalk.
2. Miniaturization and High-Density Interconnects
The trend towards miniaturization of electronic devices requires PCBs with higher component density and finer pitch sizes. FR4 PCBs are being designed with smaller vias, thinner traces, and tighter tolerances to accommodate these requirements. The use of micro-vias and blind/buried vias is also becoming more common to increase interconnect density.
3. Environmentally Friendly Materials
There is a growing focus on the use of environmentally friendly materials in PCB manufacturing. Halogen-free FR4 laminates are being developed to reduce the use of harmful chemicals and improve the recyclability of PCBs. Lead-free solder alloys and surface finishes are also being adopted to comply with RoHS regulations.
4. Thermal Management Solutions
As electronic components become more powerful and generate more heat, thermal management becomes a critical issue for PCBs. FR4 PCBs are being designed with thermal vias, heat spreaders, and metal-core substrates to improve heat dissipation and prevent overheating. The use of thermally conductive materials and advanced cooling techniques is also being explored.
5. Flexible and Rigid-Flex PCBs
Flexible and Rigid-Flex PCBs are gaining popularity for applications that require bending, folding, or twisting of the PCB. FR4 is being used as the rigid substrate in these designs, while polyimide or other flexible materials are used for the flexible sections. This allows for more compact and lightweight designs with improved reliability and durability.
Frequently Asked Questions (FAQ)
1. What is the difference between FR4 and other PCB materials?
FR4 is a glass-reinforced epoxy laminate that offers a good balance of mechanical, electrical, and thermal properties at a reasonable cost. Other PCB materials like polyimide, PTFE, or ceramic may offer better performance in specific areas but are generally more expensive and harder to manufacture.
2. Can FR4 PCBs be used for high-temperature applications?
Standard FR4 PCBs have a glass transition temperature (Tg) of around 130°C to 140°C, which limits their use in high-temperature environments. However, high-Tg FR4 laminates with Tg values of 170°C or higher are available for applications that require higher temperature resistance.
3. How does the thickness of FR4 PCB affect its performance?
The thickness of an FR4 PCB can affect its mechanical strength, rigidity, and thermal dissipation properties. Thicker boards are generally more robust and can handle higher power levels, while thinner boards are more flexible and suitable for space-constrained designs. The choice of thickness depends on the specific application requirements.
4. What surface finishes are commonly used on FR4 PCBs?
The most common surface finishes for FR4 PCBs are:
– HASL (Hot Air Solder Leveling)
– ENIG (Electroless Nickel Immersion Gold)
– OSP (Organic Solderability Preservative)
– Immersion Silver
– Immersion Tin
Each surface finish has its own advantages and limitations in terms of cost, solderability, shelf life, and compatibility with different assembly processes.
5. How long do FR4 PCBs typically last?
The lifespan of an FR4 PCB depends on various factors such as the operating environment, power levels, and assembly quality. In general, a well-designed and manufactured FR4 PCB can last for several years or even decades in normal use conditions. However, exposure to extreme temperatures, humidity, vibration, or chemical agents can degrade the performance and reliability of the PCB over time.
Conclusion
FR4 PCB has been the workhorse of the electronics industry for decades, and it continues to evolve to meet the ever-increasing demands of modern applications. Its unique combination of mechanical strength, electrical insulation, thermal stability, and cost-effectiveness makes it the material of choice for a wide range of products, from consumer gadgets to mission-critical systems.
As we look towards the future, FR4 PCB technology is poised to play a crucial role in enabling the next generation of electronic devices. With ongoing advancements in materials science, manufacturing processes, and design techniques, FR4 PCBs are becoming more capable, reliable, and sustainable than ever before.
Whether you are a PCB designer, manufacturer, or end-user, staying up-to-date with the latest trends and best practices in FR4 PCB technology is essential for success in today’s fast-paced and competitive market. By leveraging the full potential of FR4 PCBs, you can create innovative products that push the boundaries of performance, functionality, and efficiency.
As we move into 2024 and beyond, the future of FR4 PCB looks brighter than ever. With its proven track record and ongoing evolution, FR4 PCB is set to remain the backbone of the electronics industry for years to come.
Leave a Reply