Introduction to LED PCB
Light-emitting diode (LED) printed circuit boards (PCBs) have revolutionized the lighting industry, offering energy-efficient, long-lasting, and versatile solutions for a wide range of applications. LED PCBs are specially designed to support and power LED components, ensuring optimal performance and reliability. In this comprehensive guide, we will dive into the world of LED PCBs, exploring their benefits, design considerations, manufacturing processes, and various applications.
What is an LED PCB?
An LED PCB is a printed circuit board specifically designed to accommodate and power LED components. These PCBs provide the necessary electrical connections and heat dissipation properties required for LED functionality. LED PCBs come in various shapes, sizes, and configurations, depending on the specific application and LED type used.
Types of LED PCBs
There are several types of LED PCBs, each with its own unique characteristics and benefits:
-
Rigid LED PCBs: These are the most common type of LED PCBs, featuring a solid, inflexible substrate material, such as FR-4. Rigid LED PCBs offer excellent stability and durability, making them suitable for a wide range of applications.
-
Flexible LED PCBs: Flexible LED PCBs use a pliable substrate material, such as polyimide, allowing them to bend and conform to various shapes. These PCBs are ideal for applications requiring a more dynamic or space-constrained design.
-
Metal Core LED PCBs: Metal Core PCBs (MCPCBs) feature a metal substrate, typically aluminum, which provides superior heat dissipation properties. MCPCBs are commonly used in high-power LED applications where thermal management is critical.
-
Aluminum PCBs: Similar to MCPCBs, aluminum PCBs offer excellent thermal conductivity, helping to dissipate heat generated by LED components. These PCBs are often used in applications requiring a balance between cost and thermal performance.
PCB Type | Substrate Material | Key Benefits |
---|---|---|
Rigid LED PCB | FR-4 | Stability, durability |
Flexible LED PCB | Polyimide | Flexibility, space-saving |
Metal Core LED PCB | Aluminum | Superior heat dissipation |
Aluminum PCB | Aluminum | Cost-effective thermal management |
Benefits of LED PCBs
LED PCBs offer numerous advantages over traditional lighting solutions:
-
Energy Efficiency: LEDs are highly energy-efficient, consuming significantly less power than incandescent or fluorescent lighting. This translates to lower energy costs and a reduced environmental impact.
-
Long Lifespan: LED PCBs have a much longer lifespan compared to traditional lighting solutions, often lasting up to 50,000 hours or more. This minimizes maintenance and replacement costs.
-
Versatility: LED PCBs can be designed in various shapes, sizes, and colors, making them adaptable to a wide range of applications and aesthetic requirements.
-
Improved Heat Dissipation: Specialized LED PCBs, such as MCPCBs and aluminum PCBs, provide excellent thermal management, ensuring optimal LED performance and longevity.
-
Environmentally Friendly: LEDs contain no hazardous materials, such as mercury, making them a more eco-friendly choice compared to traditional lighting options.
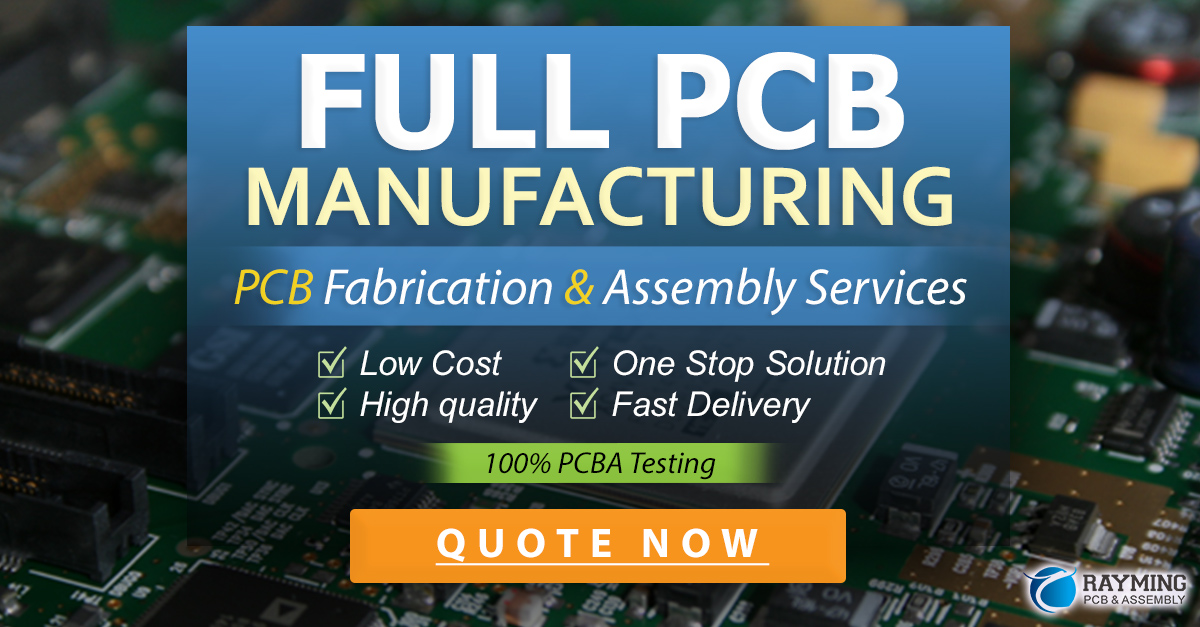
LED PCB Design Considerations
Designing an LED PCB requires careful consideration of several factors to ensure optimal performance, reliability, and longevity.
Thermal Management
Proper thermal management is crucial in LED PCB design. LED components generate heat during operation, which can negatively impact their performance and lifespan if not effectively dissipated. Some key thermal management strategies include:
-
Using metal core or aluminum PCBs: These PCB types offer excellent thermal conductivity, helping to efficiently transfer heat away from the LED components.
-
Incorporating thermal vias: Thermal vias are small, conductive holes drilled through the PCB, allowing heat to be transferred from the LED components to the other side of the board or to a heat sink.
-
Designing adequate copper pour: Increasing the amount of copper on the PCB can help distribute heat more evenly across the board, improving overall thermal performance.
Power Distribution
Efficient power distribution is essential for ensuring consistent LED performance and minimizing voltage drop across the PCB. Some considerations for power distribution include:
-
Using appropriate trace widths: Wider traces can help minimize resistance and voltage drop, ensuring that LEDs receive adequate power.
-
Implementing proper power plane design: A well-designed power plane can provide a low-impedance path for current, minimizing voltage drop and ensuring consistent power distribution.
-
Incorporating current-limiting resistors: Current-limiting resistors help regulate the current flowing through the LEDs, preventing overcurrent conditions that could damage the components.
LED Selection and Placement
Choosing the right LED components and placing them strategically on the PCB is crucial for achieving the desired lighting performance and ensuring long-term reliability.
-
Select appropriate LED components: Consider factors such as color, brightness, viewing angle, and power requirements when selecting LED components for your design.
-
Optimize LED placement: Place LEDs in a way that maximizes light output and minimizes shadowing or interference from other components.
-
Consider LED binning: LEDs can vary slightly in color and brightness, even within the same batch. Binning helps ensure consistency by grouping LEDs with similar characteristics together.
LED PCB Manufacturing Process
The manufacturing process for LED PCBs involves several key steps:
-
PCB Design and Layout: The LED PCB design is created using computer-aided design (CAD) software, taking into account all the necessary design considerations.
-
PCB Fabrication: The PCB design is used to create the physical board, which involves processes such as copper etching, drilling, and applying solder mask and silkscreen.
-
SMT Assembly: Surface-mount technology (SMT) is used to place and solder the LED components onto the PCB. This process is typically automated using pick-and-place machines and reflow soldering.
-
Testing and Quality Control: The assembled LED PCBs undergo rigorous testing to ensure proper functionality, light output, and color consistency. Quality control measures are implemented to identify and address any issues.
Applications of LED PCBs
LED PCBs find applications in a wide range of industries and products, including:
-
Automotive Lighting: LED PCBs are used in headlights, taillights, interior lighting, and instrument panel illumination.
-
General Lighting: LED PCBs are used in residential, commercial, and industrial lighting fixtures, offering energy-efficient and long-lasting illumination.
-
Backlighting: LED PCBs are used for backlighting LCD displays in televisions, computer monitors, and mobile devices.
-
Signage and Advertising: LED PCBs are used in digital signage, billboards, and other advertising displays, providing vibrant and eye-catching visuals.
-
Medical Devices: LED PCBs are used in various medical applications, such as endoscopy, dental lighting, and surgical lighting.
Frequently Asked Questions (FAQ)
-
What is the difference between an LED PCB and a regular PCB?
An LED PCB is specifically designed to support and power LED components, while a regular PCB is a more general-purpose board that can be used for various electronic components and circuits. -
Can I use a regular PCB for LED applications?
While it is possible to use a regular PCB for LED applications, it may not provide the optimal thermal management and power distribution properties required for LED performance and longevity. It is recommended to use specialized LED PCBs for best results. -
What is the lifespan of an LED PCB?
The lifespan of an LED PCB depends on factors such as the quality of components, design, and operating conditions. However, LED PCBs generally have a much longer lifespan compared to traditional lighting solutions, often lasting up to 50,000 hours or more. -
How do I choose the right LED components for my PCB design?
When selecting LED components, consider factors such as color, brightness, viewing angle, power requirements, and compatibility with your PCB design. It is also important to choose reputable suppliers and ensure that the LEDs meet the necessary quality and performance standards. -
What are the key considerations for LED PCB thermal management?
The key considerations for LED PCB thermal management include using metal core or aluminum PCBs for better heat dissipation, incorporating thermal vias to transfer heat away from the LED components, and designing adequate copper pour to evenly distribute heat across the board.
Conclusion
LED PCBs have transformed the lighting industry, offering numerous benefits over traditional lighting solutions. By understanding the various types of LED PCBs, design considerations, manufacturing processes, and applications, engineers and designers can create efficient, reliable, and visually appealing LED-based products. As the demand for energy-efficient and long-lasting lighting continues to grow, the importance of well-designed and manufactured LED PCBs will only continue to increase.
Leave a Reply