Introduction to MCPCB and its significance in the LED industry
Metal Core Printed Circuit Boards (MCPCBs) have revolutionized the LED industry by providing an efficient and reliable solution for heat dissipation in high-power LED applications. As LED technology continues to advance, the demand for effective thermal management solutions has become increasingly critical. MCPCBs have emerged as a key component in ensuring the long-term performance and reliability of LED lighting systems.
In this comprehensive article, we will delve into the role of MCPCB in the LED industry, exploring its unique features, benefits, and applications. We will also discuss the manufacturing process, design considerations, and future trends in MCPCB technology.
What is MCPCB?
MCPCB, or Metal Core PCB, is a specialized type of printed circuit board that features a metal substrate, typically aluminum, as its core material. This metal core provides excellent thermal conductivity, allowing for efficient heat dissipation from the mounted electronic components, such as high-power LEDs.
The structure of an MCPCB consists of three main layers:
-
Dielectric layer: A thin, electrically insulating layer that is applied directly onto the metal core. This layer prevents electrical short-circuits between the metal core and the copper circuit layer.
-
Copper circuit layer: A layer of copper foil that is laminated onto the dielectric layer. This layer is etched to create the desired circuit pattern for electrical connections.
-
Protective layer: A solder mask layer that is applied over the copper circuit layer to protect the circuitry from oxidation and provide electrical insulation.
Comparison between MCPCB and traditional PCB
Feature | MCPCB | Traditional PCB |
---|---|---|
Thermal conductivity | High (2-8 W/mK) | Low (0.3-0.5 W/mK) |
Heat dissipation | Efficient | Poor |
Dielectric layer | Thin (50-100 μm) | Thick (1.5-3 mm) |
Weight | Heavier | Lighter |
Cost | Higher | Lower |
Application | High-power LEDs, power electronics | General electronics |
Benefits of using MCPCB in LED applications
Improved thermal management
The primary benefit of using MCPCB in LED applications is its superior thermal management capabilities. The metal core of the MCPCB acts as a heat sink, efficiently conducting heat away from the LED components and dissipating it into the surrounding environment. This effective heat dissipation helps to maintain the LED’s optimal operating temperature, which is crucial for several reasons:
-
Longevity: High operating temperatures can significantly reduce the lifespan of LEDs. By keeping the temperature within the recommended range, MCPCBs help to extend the service life of LED lighting systems.
-
Performance: LEDs are sensitive to temperature fluctuations, and their light output and color consistency can be affected by excessive heat. MCPCBs ensure stable performance by maintaining a consistent operating temperature.
-
Reliability: Thermal stress can cause damage to the LED package and its interconnects, leading to premature failure. MCPCBs minimize thermal stress, enhancing the overall reliability of the LED system.
Enhanced electrical performance
In addition to thermal management, MCPCBs also offer improved electrical performance compared to traditional PCBs. The thin dielectric layer in MCPCBs allows for better electrical insulation and reduced capacitance between the copper circuit layer and the metal core. This results in faster signal propagation, lower signal losses, and reduced electromagnetic interference (EMI).
Design flexibility
MCPCBs provide designers with greater flexibility in terms of circuit layout and component placement. The metal core can be shaped and machined to accommodate various LED packaging types and sizes, allowing for more compact and efficient designs. Additionally, the copper circuit layer can be customized to meet specific electrical requirements, such as current carrying capacity and voltage drop.
Cost-effectiveness
Although MCPCBs have a higher initial cost compared to traditional PCBs, they offer long-term cost savings in LED applications. The improved thermal management and reliability of MCPCBs reduce the need for additional heat sinking components and minimize maintenance and replacement costs over the lifetime of the LED lighting system.
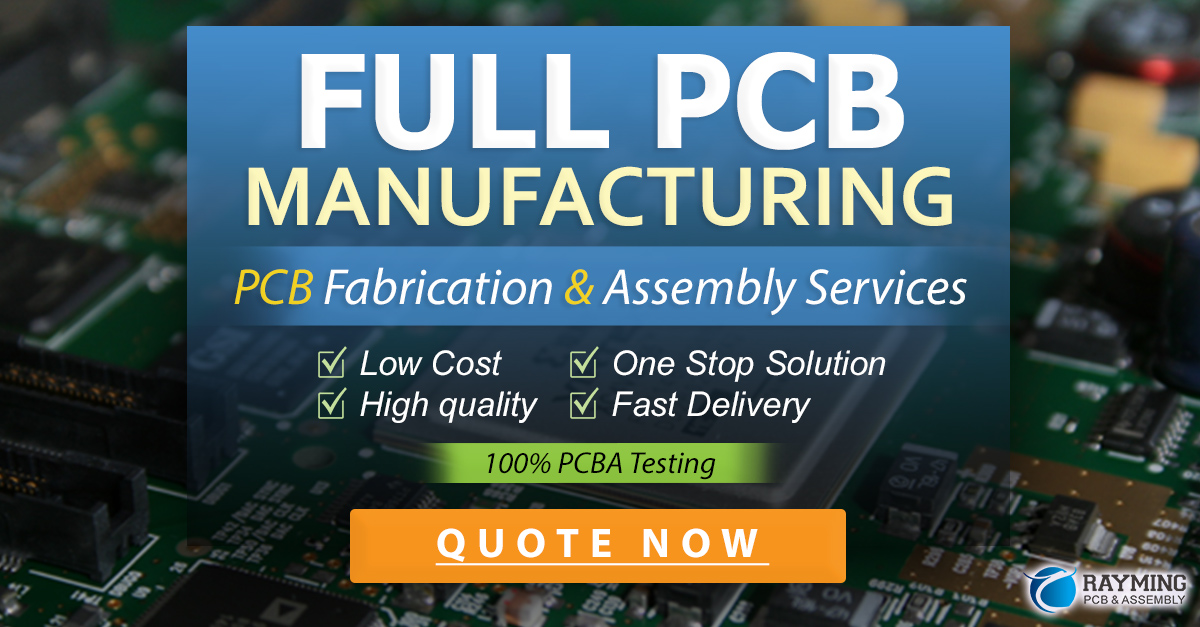
Manufacturing process of MCPCB
The manufacturing process of MCPCB involves several key steps:
-
Substrate preparation: The aluminum substrate is cleaned and pretreated to ensure proper adhesion of the dielectric layer.
-
Dielectric layer application: The dielectric layer, typically a polymer-based material, is applied onto the aluminum substrate using techniques such as screen printing, curtain coating, or lamination.
-
Copper foil lamination: A copper foil is laminated onto the dielectric layer using heat and pressure.
-
Circuit patterning: The desired circuit pattern is transferred onto the copper layer using photolithography and etching processes.
-
Protective layer application: A solder mask layer is applied over the copper circuit layer to provide protection and insulation.
-
Surface finish: The exposed copper areas are coated with a surface finish, such as HASL (Hot Air Solder Leveling), ENIG (Electroless Nickel Immersion Gold), or OSP (Organic Solderability Preservative), to enhance solderability and prevent oxidation.
-
Singulation: The panel is cut into individual MCPCB Boards using routing or punching techniques.
Applications of MCPCB in the LED industry
MCPCBs find extensive applications in various LED lighting systems, including:
-
Street lighting: High-power LED street lights require efficient heat dissipation to ensure long-term performance and reliability. MCPCBs provide the necessary thermal management solution for these applications.
-
Automotive lighting: LED headlights, taillights, and interior lighting in vehicles demand compact, reliable, and thermally efficient designs. MCPCBs enable the development of high-performance automotive LED lighting systems.
-
Architectural lighting: LED lighting is widely used in architectural applications, such as building facades, landscaping, and indoor accent lighting. MCPCBs help to maintain the desired light output and color consistency in these applications.
-
Horticulture lighting: LED grow lights for indoor farming and horticulture require specific wavelengths and high light intensity. MCPCBs ensure optimal thermal management for these high-power LED systems, promoting plant growth and health.
-
Industrial lighting: LED lighting is replacing traditional lighting solutions in industrial settings due to its energy efficiency, durability, and low maintenance requirements. MCPCBs play a crucial role in ensuring the reliability and performance of industrial LED lighting systems.
Design considerations for MCPCB in LED applications
When designing MCPCBs for LED applications, several key factors must be considered:
-
Thermal management: The thermal design of the MCPCB should be optimized to ensure efficient heat dissipation from the LED components. This involves selecting the appropriate dielectric material, copper thickness, and metal core thickness based on the specific application requirements.
-
Electrical design: The copper circuit layer should be designed to meet the electrical requirements of the LED system, such as current carrying capacity, voltage drop, and power distribution. Proper trace width and spacing should be maintained to minimize electrical losses and ensure reliable performance.
-
LED packaging compatibility: The MCPCB design should be compatible with the specific LED packaging type and size used in the application. The layout and component placement should be optimized to maximize thermal transfer and minimize thermal stress on the LED components.
-
Mechanical considerations: The MCPCB should be designed to withstand the mechanical stresses encountered during assembly, installation, and operation. Proper mounting hole placement and board thickness should be considered to ensure structural integrity and reliability.
-
Manufacturing feasibility: The MCPCB design should be manufacturable using standard PCB fabrication processes. Design for manufacturability (DFM) guidelines should be followed to ensure high yields and cost-effectiveness.
Future trends in MCPCB technology
As the LED industry continues to evolve, MCPCB technology is expected to advance to meet the growing demands for higher performance, efficiency, and reliability. Some of the future trends in MCPCB technology include:
-
Advanced dielectric materials: The development of new dielectric materials with higher thermal conductivity and better electrical insulation properties will enable the design of thinner and more efficient MCPCBs.
-
Embedded components: The integration of passive components, such as resistors and capacitors, directly into the MCPCB substrate will reduce the number of external components required, leading to more compact and reliable LED lighting systems.
-
3D printing technology: The adoption of 3D printing techniques for MCPCB fabrication will enable greater design freedom, faster prototyping, and cost-effective production of customized LED lighting solutions.
-
Smart LED lighting: The integration of IoT (Internet of Things) technologies and sensors into LED lighting systems will require advanced MCPCB designs that can accommodate additional electronic components and connectivity features.
-
Sustainability and eco-friendliness: The development of environmentally friendly materials and manufacturing processes for MCPCBs will become increasingly important as the industry focuses on sustainability and reducing its ecological footprint.
Conclusion
MCPCB technology has played a vital role in the growth and advancement of the LED industry. Its superior thermal management capabilities, improved electrical performance, design flexibility, and cost-effectiveness have made it an essential component in high-power LED applications.
As the demand for energy-efficient and reliable LED lighting solutions continues to rise, the importance of MCPCB in the industry will only continue to grow. By understanding the key features, benefits, and design considerations of MCPCB, LED lighting manufacturers and designers can leverage this technology to develop innovative, high-performance, and sustainable LED lighting systems for a wide range of applications.
Frequently Asked Questions (FAQ)
-
What is the difference between MCPCB and traditional PCB?
MCPCB features a metal core substrate, typically aluminum, which provides superior thermal conductivity compared to traditional PCBs. This allows for efficient heat dissipation from the mounted electronic components, making MCPCB ideal for high-power LED applications. -
Can MCPCB be used for applications other than LED lighting?
While MCPCB is primarily used in LED lighting applications, it can also be used in other high-power electronic applications that require efficient thermal management, such as power converters, motor drives, and automotive electronics. -
What are the key factors to consider when designing MCPCB for LED applications?
When designing MCPCB for LED applications, the key factors to consider include thermal management, electrical design, LED packaging compatibility, mechanical considerations, and manufacturing feasibility. Proper optimization of these factors ensures optimal performance, reliability, and cost-effectiveness of the LED lighting system. -
How does MCPCB technology contribute to the sustainability of LED lighting?
MCPCB technology contributes to the sustainability of LED lighting by enabling the development of energy-efficient, long-lasting, and reliable LED lighting systems. By ensuring optimal thermal management and performance, MCPCB helps to reduce energy consumption and minimize the environmental impact of LED lighting over its lifetime. -
What are the future trends in MCPCB technology for the LED industry?
The future trends in MCPCB technology for the LED industry include the development of advanced dielectric materials, embedded components, 3D printing technology, smart LED lighting integration, and a focus on sustainability and eco-friendliness. These advancements will enable the creation of more efficient, compact, and innovative LED lighting solutions.
Leave a Reply