What are PCBs and Why are They Essential in Robotics?
A printed circuit board, or PCB, is a flat board made of insulating material, such as fiberglass or plastic, with conductive pathways etched or printed onto its surface. These conductive pathways, known as traces, connect various electronic components, such as resistors, capacitors, integrated circuits (ICs), and microcontrollers, to form a complete electronic circuit.
PCBs are essential in robotics for several reasons:
-
Miniaturization: PCBs allow for the compact and efficient packaging of electronic components, enabling robots to be smaller, lighter, and more agile.
-
Reliability: The robust construction and precise layout of PCBs ensure reliable and consistent performance, even in challenging environments.
-
Customization: PCBs can be custom-designed to meet the specific requirements of a robot, optimizing functionality, power consumption, and form factor.
-
Scalability: PCBs facilitate the mass production of robotic systems, enabling the creation of large numbers of identical robots with consistent performance.
Key Considerations in PCB Design for Robots
Designing PCBs for robotic applications involves several key considerations to ensure optimal performance, reliability, and functionality. These include:
1. Component Selection
Choosing the right components is crucial for the success of a robotic PCB. Factors to consider when selecting components include:
- Power requirements
- Operating temperature range
- Physical size and weight
- Compatibility with other components
- Cost and availability
2. Layout and Routing
The layout and routing of traces on a PCB can significantly impact its performance and reliability. Key considerations include:
- Minimizing trace length to reduce signal loss and interference
- Providing adequate spacing between traces to prevent crosstalk
- Using appropriate trace widths to handle the required current
- Implementing proper grounding and shielding techniques
- Placing components strategically to optimize signal integrity and heat dissipation
3. Electromagnetic Compatibility (EMC)
Robots often operate in environments with various electromagnetic sources, making EMC a critical consideration in PCB design. Techniques to mitigate electromagnetic interference (EMI) include:
- Using ground planes and shielding to reduce EMI
- Implementing proper filtering and decoupling techniques
- Choosing components with low EMI characteristics
- Following best practices for PCB layout and routing
4. Mechanical Considerations
The mechanical design of a robotic PCB must account for the physical stresses and environmental conditions it will encounter. Key considerations include:
- Choosing appropriate PCB materials and thicknesses for mechanical strength
- Incorporating mounting holes and supports for secure attachment
- Designing for vibration and shock resistance
- Providing adequate clearance for moving parts and cable routings
- Considering thermal management and heat dissipation requirements
Manufacturing Processes for RobotIC PCBs
The manufacturing process for robotic PCBs involves several steps, each of which contributes to the quality and reliability of the final product.
1. PCB Fabrication
PCB fabrication begins with the creation of a copper-clad laminate, which is then patterned using a photolithographic process. The unwanted copper is etched away, leaving the desired conductive traces. Additional layers are then laminated together to form a multi-layer PCB.
2. Component Placement
Once the PCB is fabricated, electronic components are placed onto the board using automated pick-and-place machines. These machines use computer vision and precision positioning systems to accurately place components at high speeds.
3. Soldering
After component placement, the PCB undergoes a soldering process to electrically and mechanically connect the components to the board. This can be done using various methods, such as Wave Soldering, reflow soldering, or selective soldering, depending on the specific requirements of the board.
4. Testing and Inspection
To ensure the quality and reliability of the manufactured PCB, various testing and inspection processes are employed. These include:
- Automated optical inspection (AOI) to detect component placement and soldering defects
- In-circuit testing (ICT) to verify the functionality of individual components and circuits
- Functional testing to validate the overall performance of the assembLED PCB
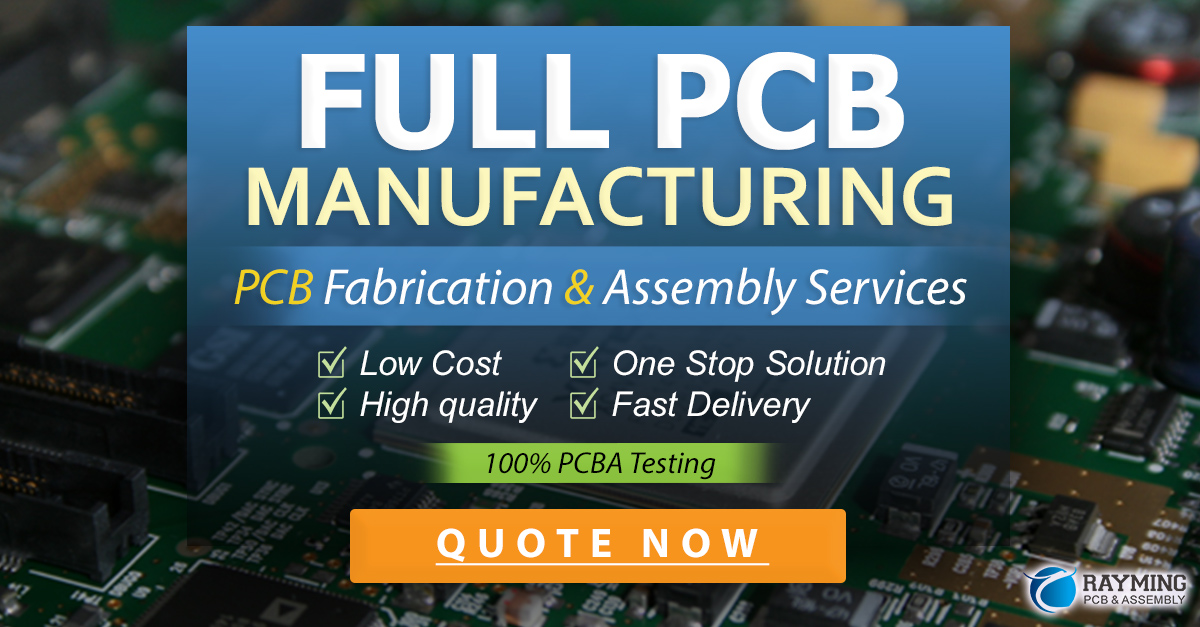
Advancements in PCB Technology for Robotics
As the field of robotics continues to evolve, so too does the technology behind the PCBs that power these machines. Some of the latest advancements in PCB technology for robotic applications include:
1. Flexible and Stretchable PCBs
Flexible and stretchable PCBs are gaining popularity in robotics due to their ability to conform to complex shapes and withstand repeated bending and stretching. These PCBs are made using flexible substrates, such as polyimide or thermoplastic polyurethane (TPU), and can be designed with stretchable interconnects to accommodate large deformations.
2. High-Density Interconnect (HDI) PCBs
HDI PCBs feature finer trace widths, smaller via sizes, and higher component densities compared to traditional PCBs. This allows for the creation of more compact and powerful robotic control systems, enabling the development of smaller and more sophisticated robots.
3. Embedded Components
Embedding components, such as resistors, capacitors, and ICs, directly into the PCB substrate can significantly reduce the size and weight of robotic PCBs. This technique also improves reliability by reducing the number of solder joints and interconnections.
4. 3D Printed Electronics
The integration of 3D printing technology with PCB manufacturing is opening up new possibilities for robotic PCBs. 3D printed electronics allow for the creation of complex, three-dimensional PCB structures with embedded components and interconnects, enabling the development of highly customized and space-efficient robotic control systems.
FAQ
1. What is the difference between a single-layer and multi-layer PCB in robotics?
Single-Layer PCBs have conductive traces on only one side of the board, while multi-layer PCBs have traces on multiple layers, separated by insulating layers. Multi-layer PCBs offer several advantages for robotic applications, including increased component density, improved signal integrity, and better EMI performance.
2. How do I choose the right components for my robotic PCB?
When selecting components for a robotic PCB, consider factors such as power requirements, operating temperature range, physical size and weight, compatibility with other components, and cost and availability. It’s also important to choose components with low EMI characteristics and adequate performance specifications for your specific application.
3. What are some common PCB design mistakes to avoid in robotics?
Common PCB design mistakes in robotics include improper component placement, inadequate trace spacing and width, poor grounding and shielding techniques, and failure to consider mechanical and environmental factors. To avoid these mistakes, follow best practices for PCB layout and routing, implement proper EMC techniques, and consider the specific requirements of your robotic application.
4. How can I ensure the reliability of my robotic PCB?
To ensure the reliability of your robotic PCB, use high-quality components, follow best practices for PCB design and manufacturing, and perform thorough testing and inspection processes. Additionally, consider incorporating redundancy and fault-tolerant design techniques to improve the overall reliability of your robotic system.
5. What are the benefits of using flexible or stretchable PCBs in robotics?
Flexible and stretchable PCBs offer several benefits for robotic applications, including the ability to conform to complex shapes, withstand repeated bending and stretching, and enable the creation of more compact and lightweight robotic systems. These PCBs also provide improved reliability and durability compared to traditional rigid PCBs in applications that require significant mechanical flexibility.
Conclusion
PCBs are the unsung heroes of the robotic world, providing the essential interconnects and circuitry that bring these incredible machines to life. By understanding the key considerations in PCB design, manufacturing processes, and the latest advancements in PCB technology, robotics engineers and enthusiasts can create more capable, reliable, and innovative robotic systems.
As the field of robotics continues to evolve, so too will the PCBs that power these machines. From flexible and stretchable substrates to high-density interconnects and 3D printed electronics, the future of robotic PCBs is filled with exciting possibilities. By staying at the forefront of these advancements, we can unlock new frontiers in robotic performance and functionality, paving the way for a world where robots play an increasingly vital role in our lives.
Leave a Reply