Introduction to PCB Design Optimization
Printed Circuit Board (PCB) design is a complex process that involves multiple steps, from schematic capture to final fabrication. To achieve the best possible results, it is essential to optimize the PCB design flow and ensure that the design is done right the first time. In this article, we will discuss the optimum PCB design flow and the techniques that can be used to achieve a high-quality, reliable, and cost-effective PCB design.
Why is PCB Optimization Important?
PCB optimization is crucial for several reasons:
- Cost reduction: An optimized PCB design reduces the overall cost of the project by minimizing the number of iterations and avoiding costly mistakes.
- Improved reliability: A well-optimized PCB design ensures that the final product is reliable and functions as intended.
- Faster time-to-market: By getting the design right the first time, the development cycle is shortened, allowing for faster time-to-market.
The PCB Design Flow
The PCB design flow consists of several stages, each of which plays a critical role in the overall success of the project. Let’s take a closer look at each stage:
1. Schematic Capture
The first step in the PCB design flow is schematic capture. This involves creating a graphical representation of the electronic circuit using a schematic capture tool. The schematic should be clear, well-organized, and easy to understand.
Tips for Optimizing Schematic Capture:
- Use a consistent naming convention for components and nets
- Group related components together
- Use hierarchical design techniques to simplify complex circuits
- Perform a thorough review of the schematic to catch any errors early on
2. Component Selection and Placement
Once the schematic is complete, the next step is to select the appropriate components and place them on the PCB layout. This stage is critical because the placement of components can significantly impact the overall performance and manufacturability of the PCB.
Tips for Optimizing Component Selection and Placement:
- Choose components that meet the required specifications and are readily available
- Place components in a logical and organized manner, taking into account signal integrity and thermal considerations
- Use surface mount components whenever possible to reduce the size of the PCB
- Consider the manufacturing process when placing components, ensuring adequate spacing and clearance
3. PCB Routing
PCB routing involves creating the conductive traces that connect the components on the PCB. This is a critical stage in the PCB design flow, as the quality of the routing can significantly impact the performance and reliability of the final product.
Tips for Optimizing PCB Routing:
- Use appropriate trace widths and spacing to ensure signal integrity and manufacturability
- Minimize the use of vias, as they can add complexity and cost to the manufacturing process
- Use ground planes and power planes to reduce noise and improve signal quality
- Perform a design rule check (DRC) to ensure that the routing meets the required specifications
4. Simulation and Verification
Before sending the PCB design for fabrication, it is essential to perform simulations and verifications to ensure that the design meets the required performance and reliability standards.
Tips for Optimizing Simulation and Verification:
- Use signal integrity simulations to ensure that the PCB can handle the required signal speeds and frequencies
- Perform thermal simulations to ensure that the PCB can dissipate heat effectively
- Use electromagnetic compatibility (EMC) simulations to ensure that the PCB meets the required EMC standards
- Perform a final design review to catch any remaining issues before fabrication
5. Fabrication and Assembly
The final stage in the PCB design flow is fabrication and assembly. This involves sending the PCB design files to a manufacturer for fabrication and then assembling the components onto the PCB.
Tips for Optimizing Fabrication and Assembly:
- Choose a reputable manufacturer with experience in producing high-quality PCBs
- Provide clear and detailed manufacturing files, including Gerber Files, drill files, and assembly drawings
- Communicate regularly with the manufacturer to ensure that the PCB is being produced to the required specifications
- Perform thorough testing and inspection of the assembLED PCBs to ensure that they meet the required quality standards
PCB Optimization Techniques
In addition to following the optimum PCB design flow, there are several techniques that can be used to optimize the PCB design and ensure the best possible results. Let’s take a look at some of these techniques:
1. Design for Manufacturability (DFM)
Design for Manufacturability (DFM) is a technique that involves designing the PCB with the manufacturing process in mind. By considering the limitations and capabilities of the manufacturing process early on in the design phase, it is possible to avoid costly mistakes and ensure that the PCB can be manufactured efficiently and cost-effectively.
Tips for Implementing DFM:
- Use standard component sizes and packages whenever possible
- Ensure adequate spacing and clearance between components and traces
- Avoid using non-standard or custom components unless absolutely necessary
- Consider the capabilities and limitations of the manufacturing process when designing the PCB
2. High-Speed Design Techniques
High-Speed PCB design involves designing the PCB to handle high-frequency signals and minimize signal integrity issues. This requires careful consideration of factors such as trace length, impedance matching, and crosstalk.
Tips for High-Speed PCB Design:
- Use controlled impedance traces to ensure proper impedance matching
- Minimize the use of vias and stubs to reduce signal reflections
- Use differential signaling whenever possible to reduce noise and crosstalk
- Perform signal integrity simulations to ensure that the PCB can handle the required signal speeds and frequencies
3. Thermal Management
Thermal management is the process of designing the PCB to dissipate heat effectively and prevent overheating of components. This is particularly important for high-power PCBs or PCBs with high component density.
Tips for Thermal Management:
- Use thermal vias to conduct heat away from components
- Use copper pours and ground planes to distribute heat evenly across the PCB
- Consider the use of heatsinks or fans for high-power components
- Perform thermal simulations to ensure that the PCB can dissipate heat effectively
4. EMC Considerations
Electromagnetic Compatibility (EMC) is the ability of electronic devices to operate without causing or being affected by electromagnetic interference. PCBs must be designed with EMC considerations in mind to ensure that they meet the required EMC standards.
Tips for EMC Considerations:
- Use appropriate shielding and grounding techniques to reduce electromagnetic interference
- Minimize the use of high-frequency components and signals
- Use filters and suppression components to reduce noise and interference
- Perform EMC simulations to ensure that the PCB meets the required EMC standards
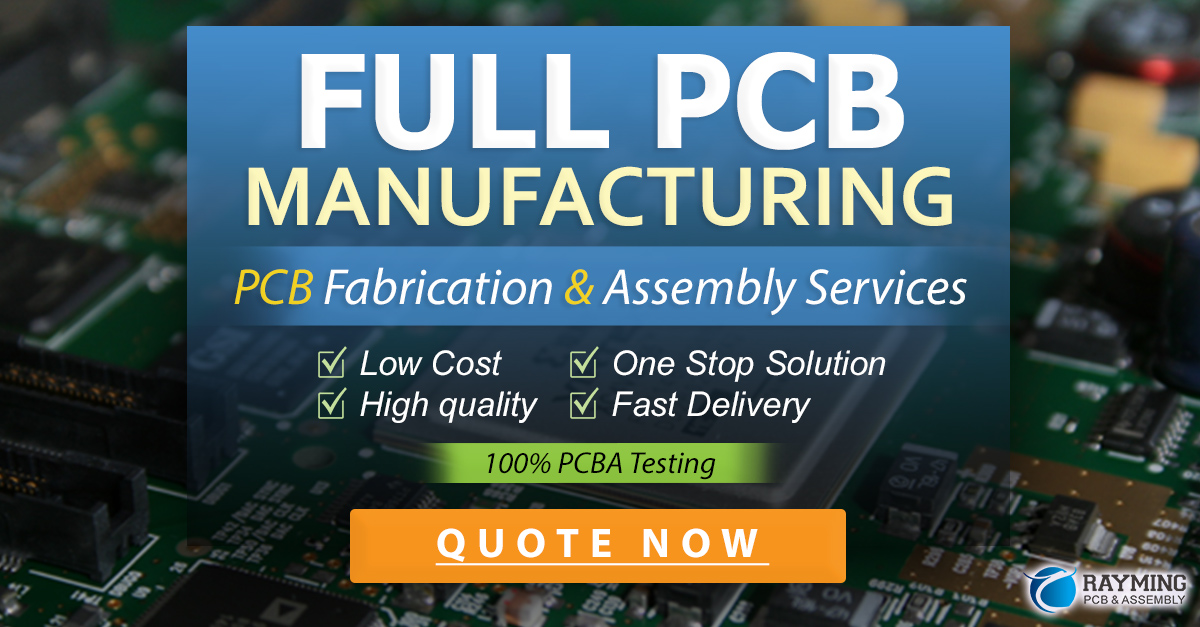
Frequently Asked Questions (FAQ)
- What is the most important stage in the PCB design flow?
-
All stages in the PCB design flow are important, but component selection and placement, PCB routing, and simulation and verification are particularly critical stages that can significantly impact the overall performance and reliability of the PCB.
-
What are the benefits of using surface mount components in PCB design?
-
Surface mount components are smaller and can be placed more densely on the PCB, reducing the overall size of the PCB. They also have shorter lead lengths, which can improve signal integrity and reduce noise.
-
What is the purpose of performing simulations and verifications in PCB design?
-
Simulations and verifications are used to ensure that the PCB design meets the required performance and reliability standards before fabrication. They can help catch issues early on and prevent costly mistakes.
-
What is design for manufacturability (DFM) and why is it important in PCB design?
-
Design for manufacturability (DFM) is a technique that involves designing the PCB with the manufacturing process in mind. It is important because it can help avoid costly mistakes and ensure that the PCB can be manufactured efficiently and cost-effectively.
-
What are some common techniques used for thermal management in PCB design?
- Common techniques for thermal management in PCB design include using thermal vias to conduct heat away from components, using copper pours and ground planes to distribute heat evenly across the PCB, and using heatsinks or fans for high-power components. Thermal simulations can also be used to ensure that the PCB can dissipate heat effectively.
Conclusion
PCB design optimization is a critical process that involves following the optimum PCB design flow and using various techniques to ensure the best possible results. By considering factors such as component selection and placement, PCB routing, simulation and verification, design for manufacturability, high-speed design, thermal management, and EMC considerations, it is possible to achieve a high-quality, reliable, and cost-effective PCB design.
Stage | Description | Key Considerations |
---|---|---|
Schematic Capture | Creating a graphical representation of the electronic circuit | – Consistent naming convention – Grouping related components – Hierarchical design techniques |
Component Selection and Placement | Selecting appropriate components and placing them on the PCB layout | – Meeting required specifications – Logical and organized placement – Surface mount components – Manufacturing process considerations |
PCB Routing | Creating conductive traces that connect components on the PCB | – Appropriate trace widths and spacing – Minimizing vias – Ground and power planes – Design rule check (DRC) |
Simulation and Verification | Ensuring the design meets required performance and reliability standards | – Signal integrity simulations – Thermal simulations – EMC simulations – Final design review |
Fabrication and Assembly | Sending the PCB design files to a manufacturer for fabrication and assembly | – Choosing a reputable manufacturer – Providing clear and detailed manufacturing files – Regular communication with the manufacturer – Thorough testing and inspection |
By following the optimum PCB design flow and implementing the various optimization techniques discussed in this article, designers can achieve a high-quality, reliable, and cost-effective PCB design that meets the required performance and reliability standards.
Leave a Reply