What is IPC-6012?
IPC-6012 is a standard that defines the qualification and performance specifications for rigid printed boards. It covers various aspects of PCB Production, including:
- Material requirements
- Dimensional tolerances
- Hole size and placement
- Conductor width and spacing
- Solder mask and marking
- Electrical testing
The standard is divided into three performance classes (1, 2, and 3) based on the intended end-use of the PCB. Class 1 is for general electronic products, Class 2 is for dedicated service electronic products, and Class 3 is for high-reliability electronic products.
Performance Class | End-Use | Example Applications |
---|---|---|
Class 1 | General Electronic Products | Consumer electronics, toys, computer peripherals |
Class 2 | Dedicated Service Electronic Products | Industrial controls, automotive, medical devices |
Class 3 | High-Reliability Electronic Products | Aerospace, military, life-support systems |
Adhering to IPC-6012 ensures that PCBs meet the necessary quality and reliability standards for their intended application.
What is IPC-A-600?
IPC-A-600 is a visual acceptability standard for PCBs. It provides a comprehensive set of visual criteria for inspecting and accepting printed circuit boards. The standard covers various aspects of PCB Quality, including:
- Conductor definition and edges
- Solder mask and coating
- Marking and legend
- Laminate defects
- Plating and surface finish
- Solder joints and connections
IPC-A-600 defines three acceptance levels (Target, Acceptable, and Nonconforming) for each criterion, providing a clear guideline for quality control inspectors.
Acceptance Level | Description |
---|---|
Target | The ideal condition, with no defects or imperfections |
Acceptable | Allows for minor defects that do not affect PCB functionality |
Nonconforming | Defects that exceed the acceptable limits and may impact PCB performance |
By following IPC-A-600, PCB Manufacturers can ensure consistent quality and minimize the risk of defective boards entering the supply chain.
The Importance of IPC-6012 and IPC-A-600 in PCB Production
Quality and Reliability
IPC-6012 and IPC-A-600 play a crucial role in ensuring the quality and reliability of PCBs. By adhering to these standards, manufacturers can:
- Reduce the risk of defects and failures
- Improve the consistency and uniformity of PCBs
- Meet the specific requirements of different applications and industries
Consistent quality and reliability are essential for PCBs, as they are critical components in a wide range of electronic devices. Failures or malfunctions can lead to costly repairs, product recalls, and even safety hazards.
Supply Chain Efficiency
Adopting IPC-6012 and IPC-A-600 can also streamline the PCB Supply Chain by:
- Providing a common language and set of expectations for PCB manufacturers, suppliers, and customers
- Reducing the need for custom specifications and negotiations
- Facilitating seamless integration of PCBs into end products
When all parties in the supply chain follow the same standards, it becomes easier to source components, ensure compatibility, and minimize delays and disruptions.
Cost Savings
Implementing IPC-6012 and IPC-A-600 can lead to significant cost savings for PCB manufacturers and their customers. By reducing defects, rework, and scrap, companies can:
- Lower production costs
- Improve yields and efficiency
- Minimize warranty claims and returns
Additionally, by following industry-standard practices, manufacturers can optimize their processes, reduce waste, and increase overall profitability.
Competitive Advantage
PCB manufacturers that consistently adhere to IPC-6012 and IPC-A-600 can differentiate themselves in the market and gain a competitive advantage. Customers are more likely to choose suppliers that:
- Demonstrate a commitment to quality and reliability
- Offer products that meet industry standards
- Provide transparent and consistent documentation
By investing in IPC compliance, PCB manufacturers can attract and retain customers, expand their market share, and build a strong reputation in the industry.
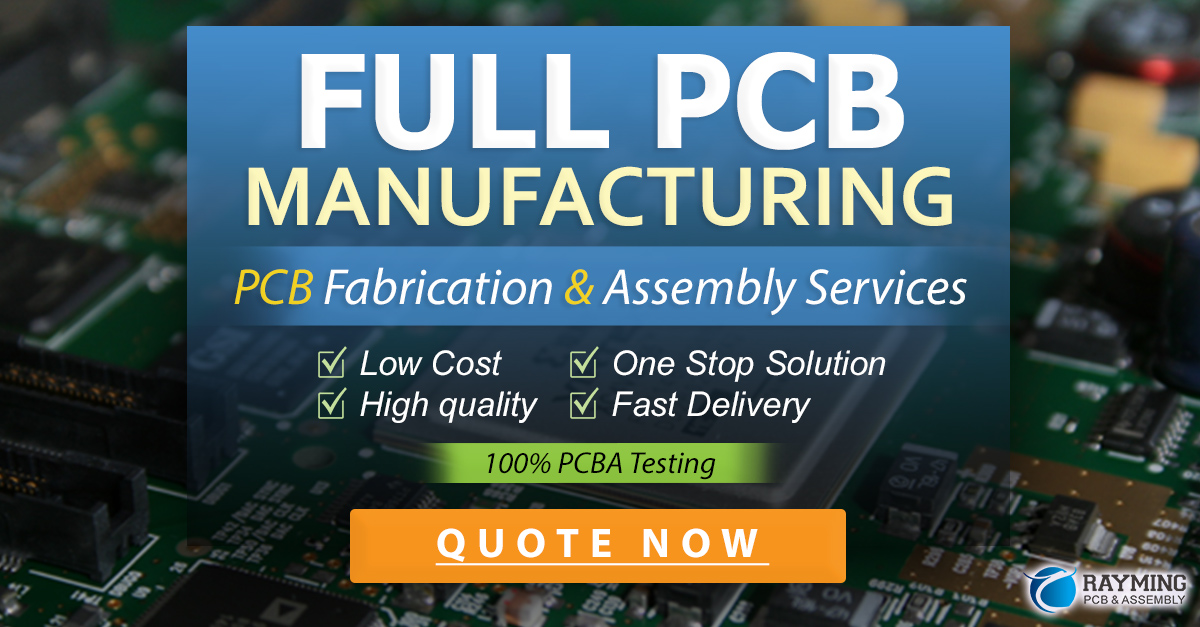
Implementing IPC-6012 and IPC-A-600 in PCB Production
To successfully implement IPC-6012 and IPC-A-600 in PCB production, manufacturers should follow these steps:
- Train employees on the standards and their requirements
- Develop and document processes that align with the standards
- Invest in the necessary equipment and resources for compliance
- Conduct regular audits and inspections to ensure ongoing adherence
- Continuously improve processes based on feedback and industry updates
Implementing these standards requires a commitment from all levels of the organization, from top management to production floor employees. It may also involve collaborating with suppliers, customers, and industry partners to ensure a consistent and integrated approach.
Conclusion
IPC-6012 and IPC-A-600 are essential standards for PCB production, ensuring the quality, reliability, and consistency of these critical components. By adhering to these standards, PCB manufacturers can improve their processes, reduce costs, and gain a competitive advantage in the market. As the electronics industry continues to evolve, the importance of IPC Standards will only continue to grow, making them a crucial investment for any PCB manufacturer looking to succeed in the long term.
Frequently Asked Questions (FAQ)
-
What is the difference between IPC-6012 and IPC-A-600?
IPC-6012 defines the qualification and performance specifications for rigid printed boards, while IPC-A-600 provides visual acceptability criteria for inspecting and accepting PCBs. -
Are IPC-6012 and IPC-A-600 mandatory for PCB manufacturers?
While not legally mandatory, these standards are widely adopted and often required by customers in the electronics industry. Adhering to these standards is considered a best practice and can provide a competitive advantage. -
How often should PCB manufacturers conduct audits and inspections to ensure compliance with IPC-6012 and IPC-A-600?
The frequency of audits and inspections may vary depending on the manufacturer’s quality management system and customer requirements. However, it is generally recommended to conduct regular checks, such as daily or weekly inspections, and more comprehensive audits on a monthly or quarterly basis. -
Can PCB manufacturers be certified to IPC-6012 and IPC-A-600?
Yes, PCB manufacturers can be certified to these standards through IPC’s Validation Services program. This involves an on-site audit by IPC experts to verify compliance with the standards and provide a certificate of conformance. -
How can PCB manufacturers stay up-to-date with changes and updates to IPC-6012 and IPC-A-600?
IPC regularly publishes updates and revisions to its standards. PCB manufacturers can stay informed by becoming IPC members, attending industry events and training sessions, and subscribing to IPC publications and newsletters. It is also important to maintain open communication with suppliers, customers, and industry partners to stay current with the latest requirements and best practices.
Leave a Reply