What is Wave Soldering?
Wave soldering is a process in which the underside of a PCB is exposed to a wave of molten solder. The components are first inserted into the PCB through holes, and the board is then passed over a molten solder bath. The solder adheres to the exposed metal surfaces, creating electrical connections between the components and the PCB.
The Wave Soldering Process
- Fluxing: The PCB is first coated with a layer of flux, which helps to remove oxidation and improve solder wettability.
- Preheating: The board is then preheated to activate the flux and prevent thermal shock when it comes into contact with the molten solder.
- Solder Wave: The PCB is passed over a wave of molten solder, which is typically a tin-lead alloy. The solder adheres to the exposed metal surfaces, creating electrical connections.
- Cooling: After the soldering process, the PCB is cooled to allow the solder joints to solidify.
Advantages of Wave Soldering
- Suitable for high-volume production
- Can handle through-hole components
- Provides strong mechanical bonds
- Relatively low cost compared to other soldering methods
Disadvantages of Wave Soldering
- Not suitable for surface mount components (SMDs)
- Limited control over solder joint quality
- Potential for bridging and solder balls
- High thermal stress on components
What is Reflow Soldering?
Reflow soldering is a process in which solder paste is applied to the PCB pads, components are placed on top, and the entire assembly is heated in a reflow oven. The solder paste melts and forms electrical connections between the components and the PCB.
The Reflow Soldering Process
- Solder Paste Application: Solder paste, a mixture of tiny solder spheres and flux, is applied to the PCB pads using a stencil or syringe.
- Component Placement: Surface mount components are placed on top of the solder paste using a pick-and-place machine or by hand.
- Reflow: The PCB is passed through a reflow oven, which heats the board according to a specific temperature profile. The solder paste melts and forms electrical connections between the components and the PCB.
- Cooling: After the reflow process, the PCB is cooled to allow the solder joints to solidify.
Advantages of Reflow Soldering
- Suitable for surface mount components (SMDs)
- High level of automation and precision
- Consistent solder joint quality
- Low thermal stress on components
- Enables high-density PCB designs
Disadvantages of Reflow Soldering
- Not suitable for through-hole components
- Higher initial equipment costs compared to wave soldering
- Requires precise control of the reflow temperature profile
- Solder paste has a limited shelf life and requires refrigeration
Comparing Wave Soldering and Reflow Soldering
Factor | Wave Soldering | Reflow Soldering |
---|---|---|
Component Types | Through-hole | Surface mount |
Solder Application | Molten solder wave | Solder paste |
Process Control | Limited | High |
Solder Joint Quality | Variable | Consistent |
Thermal Stress on Components | High | Low |
PCB Density | Low to medium | High |
Production Volume | High | Medium to high |
Equipment Cost | Low to medium | High |
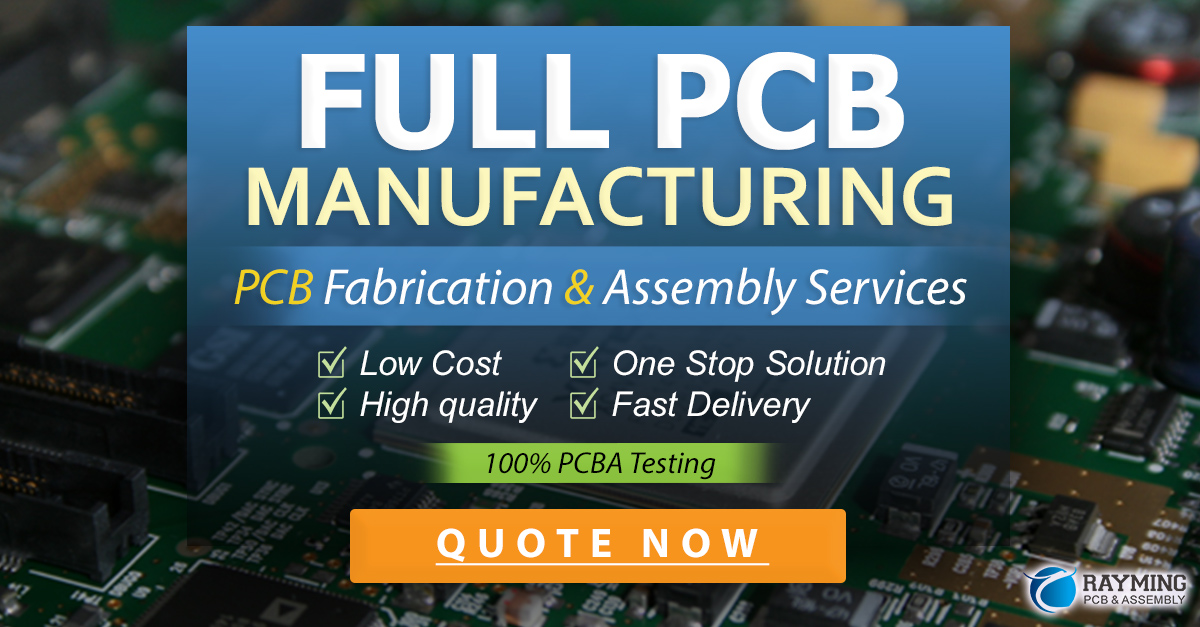
Choosing the Right Soldering Method
When deciding between wave soldering and reflow soldering, consider the following factors:
- Component Types: If your PCB primarily uses through-hole components, wave soldering is the best choice. For surface mount components, reflow soldering is the preferred method.
- PCB Density: Reflow soldering enables higher-density PCB designs due to the smaller size of surface mount components and the precision of the solder paste application process.
- Production Volume: Wave soldering is better suited for high-volume production, while reflow soldering can handle medium to high volumes.
- Budget: Wave soldering generally has lower equipment costs compared to reflow soldering, which requires specialized ovens and pick-and-place machines.
FAQ
1. Can wave soldering and reflow soldering be used together on the same PCB?
Yes, it is possible to use both wave soldering and reflow soldering on the same PCB in a process called mixed assembly. In this case, surface mount components are first reflow soldered, followed by the wave soldering of through-hole components.
2. What is selective soldering, and how does it differ from wave soldering?
Selective soldering is a process in which solder is applied to specific areas of a PCB using a specialized nozzle. This method is often used for boards that have a mix of through-hole and surface mount components, or when certain components are heat-sensitive and cannot be exposed to the high temperatures of a molten solder wave.
3. What is the purpose of flux in the soldering process?
Flux is a chemical agent that is used to remove oxidation from metal surfaces and improve solder wettability. It helps to ensure that the solder adheres properly to the components and PCB pads, creating reliable electrical connections.
4. How does the reflow temperature profile affect the solder joint quality?
The reflow temperature profile is crucial for achieving consistent and reliable solder joints. It must be carefully controlled to ensure that the solder paste melts and flows properly without causing damage to the components or the PCB. An incorrect temperature profile can lead to solder joint defects such as cold joints, tombstoning, or delamination.
5. What are some common defects that can occur in wave soldering and reflow soldering?
Some common defects in wave soldering include bridging (solder connecting adjacent pins), solder balls, and insufficient solder fillets. In reflow soldering, common defects include tombstoning (components standing on end), solder beading, and poor wetting. These defects can be minimized by properly controlling the soldering process parameters and ensuring that the PCB design follows best practices for manufacturability.
Conclusion
Wave soldering and reflow soldering are two essential methods for assembling printed circuit boards, each with its own advantages and disadvantages. Wave soldering is best suited for through-hole components and high-volume production, while reflow soldering is ideal for surface mount components and high-density PCB designs. When choosing between the two methods, consider factors such as component types, PCB density, production volume, and budget. By understanding the differences between wave soldering and reflow soldering, you can make an informed decision and ensure the success of your PCB assembly process.
Leave a Reply