What are PCB Surface Finishes?
PCB surface finishes are coatings applied to the exposed copper traces and pads on a printed circuit board. The main purposes of PCB surface finishes are:
– Protecting the copper from oxidation and corrosion
– Enhancing the solderability of components
– Improving wear resistance
– Providing a smooth, level surface for component placement
There are various types of PCB surface finishes available, each with their own advantages and drawbacks. Two of the most popular options today are Electroless Nickel Immersion Gold (ENIG) and Electroless Nickel Electroless Palladium Immersion Gold (ENEPIG).
What is ENIG?
ENIG stands for Electroless Nickel Immersion Gold. It is a chemical process that deposits a thin layer of nickel (typically 3-6 µm) followed by a thin layer of gold (0.05-0.15 µm) onto the copper pads and traces.
The process involves these key steps:
- The bare PCB is cleaned to remove any contaminants.
- An electroless nickel plating bath is used to deposit the nickel layer onto the copper. The nickel acts as a barrier, protecting the copper from diffusing into the gold layer.
- The board is rinsed.
- An immersion gold plating bath is used to deposit a thin layer of gold onto the nickel. The gold provides excellent solderability and protects the nickel from oxidation.
Advantages of ENIG
- Good solderability
- Coplanarity for fine-pitch devices
- Gold wire bonding compatible
- Corrosion resistant
- Long shelf life
- Suitable for both lead and lead-free soldering
- Lower cost than ENEPIG
Disadvantages of ENIG
- Not suitable for aluminum wire bonding
- Black pad defect can occur
- Limited life of the immersion gold bath
- Some issues with solder joint reliability under extreme conditions
What is ENEPIG?
ENEPIG stands for Electroless Nickel Electroless Palladium Immersion Gold. It is an extension of the ENIG process that adds an electroless palladium layer (0.05-0.3 µm) between the nickel and gold.
The process involves:
- Cleaning the bare PCB
- Electroless nickel plating
- Electroless palladium plating
- Immersion gold plating
The additional palladium layer acts as a barrier between the nickel and gold, which provides some key benefits.
Advantages of ENEPIG
- Excellent solderability
- Aluminum and gold wire bonding compatible
- Eliminates black pad issue seen with ENIG
- Longer shelf life than ENIG
- Better solder joint reliability under extreme conditions
- Suitable for fine-pitch devices
- Lower gold thickness required compared to ENIG
Disadvantages of ENEPIG
- Higher cost than ENIG due to palladium
- More complex process with tighter tolerances
- Palladium layer can be porous if not processed correctly
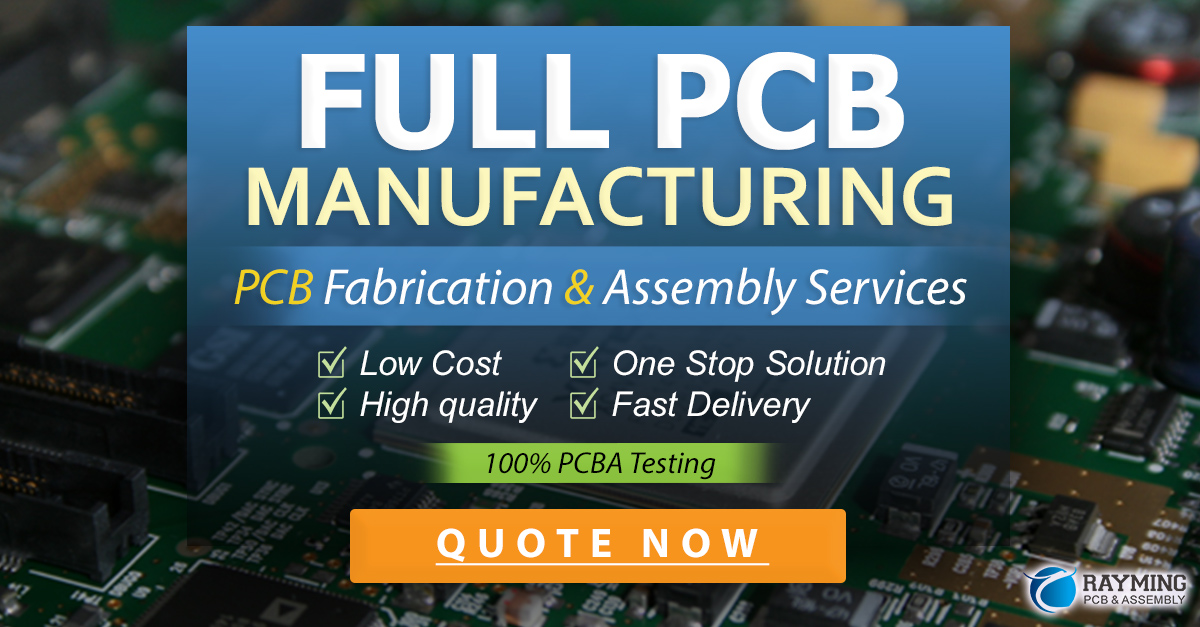
ENIG vs ENEPIG Comparison
Here is a table comparing the key characteristics of ENIG and ENEPIG:
Property | ENIG | ENEPIG |
---|---|---|
Solderability | Good | Excellent |
Wire Bonding | Gold only | Gold & Aluminum |
Shelf Life | 6-12 months | 12+ months |
Black Pad Issue | Possible | Eliminated |
Nickel Thickness | 3-6 µm | 3-6 µm |
Palladium Thickness | N/A | 0.05-0.3 µm |
Gold Thickness | 0.05-0.15 µm | 0.05-0.10 µm |
Suitable for Fine Pitch | Yes | Yes |
Copper Wire Bonding | No | Yes |
Cost | $$ | $$$ |
As you can see, ENEPIG offers several advantages over ENIG, most notably the compatibility with aluminum wire bonding, elimination of black pad, and improved solder joint reliability. However, this comes at a higher cost due to the additional palladium layer.
When to Use ENIG
ENIG is a great choice for many PCB applications, especially when cost is a key factor. It is well suited for boards that require:
- Good solderability
- Gold wire bonding only
- Corrosion resistance
- Lead or lead-free soldering
- Fine-pitch SMT devices
Some typical applications that use ENIG include:
- Consumer electronics
- Automotive electronics
- Industrial controls
- Medical devices
- Telecom equipment
When to Use ENEPIG
ENEPIG is the preferred choice when the highest level of reliability and flexibility is required. It is ideal for PCBs that need:
- Excellent solderability
- Aluminum and gold wire bonding
- Copper wire bonding
- Extended shelf life
- Elimination of black pad risk
- Ultra fine-pitch SMT devices
- High reliability under extreme conditions
Typical applications that benefit from ENEPIG include:
- High-end servers and data centers
- Aerospace and defense electronics
- Medical implantable devices
- Automotive safety systems
- 5G infrastructure
FAQ
1. Is ENEPIG always better than ENIG?
Not necessarily. While ENEPIG does offer several advantages, ENIG is still a great choice for many applications. ENIG is more cost-effective and is suitable for PCBs that don’t require aluminum wire bonding or the highest level of reliability.
2. Can ENIG be used for aluminum wire bonding?
No, ENIG is not compatible with aluminum wire bonding. The gold surface is too soft and will not form a reliable bond with the aluminum wire. If aluminum wire bonding is required, ENEPIG should be used instead.
3. What causes black pad in ENIG?
Black pad is a defect that can occur with the ENIG process where the nickel layer separates from the copper pad, resulting in a non-solderable black spot. It is caused by excessive phosphorus in the electroless nickel bath, which can make the nickel brittle and prone to separation.
4. How does ENEPIG prevent black pad?
The additional palladium layer in ENEPIG acts as a barrier between the nickel and gold, which prevents the corrosive immersion gold bath from attacking the nickel. This eliminates the risk of black pad defects.
5. Is the higher cost of ENEPIG justified?
It depends on the specific application and requirements. For high-reliability products that demand the best solderability, wire bonding flexibility, and long shelf life, the added cost of ENEPIG can easily be justified. However, for more cost-sensitive consumer products, ENIG is often the better choice.
Conclusion
Selecting the right PCB surface finish is critical to the performance, reliability, and cost of the end product. ENIG and ENEPIG are two of the most popular choices, each with their own strengths and weaknesses.
ENIG offers a good balance of solderability, gold wire bonding compatibility, and cost-effectiveness for a wide range of applications. ENEPIG builds upon the capabilities of ENIG, adding an extra palladium layer that improves reliability, eliminates black pad risk, and allows for aluminum wire bonding.
By understanding the differences between these two finishes, engineers can make an informed decision that optimizes the performance and value of their PCB designs.
Leave a Reply