Introduction to PCB Development
Printed Circuit Boards (PCBs) have revolutionized the electronics industry since their inception in the early 20th century. PCBs are the backbone of modern electronic devices, providing a platform for the interconnection and assembly of electronic components. The development of PCBs has been a continuous process, driven by the ever-increasing demand for smaller, faster, and more complex electronic devices.
Early History of PCBs
The concept of PCBs can be traced back to the early 1900s when the first patent for a printed wire was filed by Albert Hanson, a German inventor. However, it wasn’t until the 1940s that the first practical PCBs were developed. During World War II, the U.S. military needed a reliable and compact way to connect electronic components in their radar systems. This led to the development of the first double-sided PCBs, which were made by printing conductive ink onto a substrate.
The Rise of PCBs in the Electronics Industry
After the war, PCBs quickly found their way into the consumer electronics industry. The 1950s saw the introduction of the first commercially available PCBs, which were used in televisions and radios. The 1960s brought the development of multilayer PCBs, which allowed for even greater component density and complexity.
PCB Manufacturing Process
PCB Design
The PCB manufacturing process begins with the design phase. PCB designers use specialized software to create a schematic diagram of the circuit, which shows the interconnections between the various components. The schematic is then used to create a layout of the PCB, which determines the placement of the components and the routing of the traces.
PCB Fabrication
Once the design is complete, the PCB is ready for fabrication. The fabrication process involves several steps, including:
- Printing the circuit pattern onto a copper-clad substrate using a photoresist and etching process.
- Drilling holes for through-hole components and vias.
- Applying a solder mask to protect the copper traces and prevent short circuits.
- Applying a silkscreen to add component labels and other markings.
PCB Assembly
After fabrication, the PCB is ready for assembly. The assembly process involves placing the components onto the board and soldering them in place. This can be done manually or using automated pick-and-place machines. Once the components are in place, the board is inspected for defects and tested to ensure proper functionality.
Advancements in PCB Technology
Surface Mount Technology (SMT)
One of the most significant advancements in PCB technology has been the development of Surface Mount Technology (SMT). SMT allows for the placement of components directly onto the surface of the PCB, rather than through holes. This has several advantages, including:
- Smaller component sizes
- Higher component density
- Faster assembly times
- Lower manufacturing costs
High-Density Interconnect (HDI) PCBs
Another major advancement in PCB technology has been the development of High-Density Interconnect (HDI) PCBs. HDI PCBs are characterized by their fine pitch traces and small via sizes, which allow for even greater component density and complexity. HDI PCBs are commonly used in smartphones, tablets, and other high-performance electronic devices.
Flexible PCBs
Flexible PCBs are another important development in PCB technology. As the name suggests, flexible PCBs are designed to be bendable and conformable, allowing them to fit into tight spaces and curved surfaces. Flexible PCBs are commonly used in wearable electronics, medical devices, and aerospace applications.
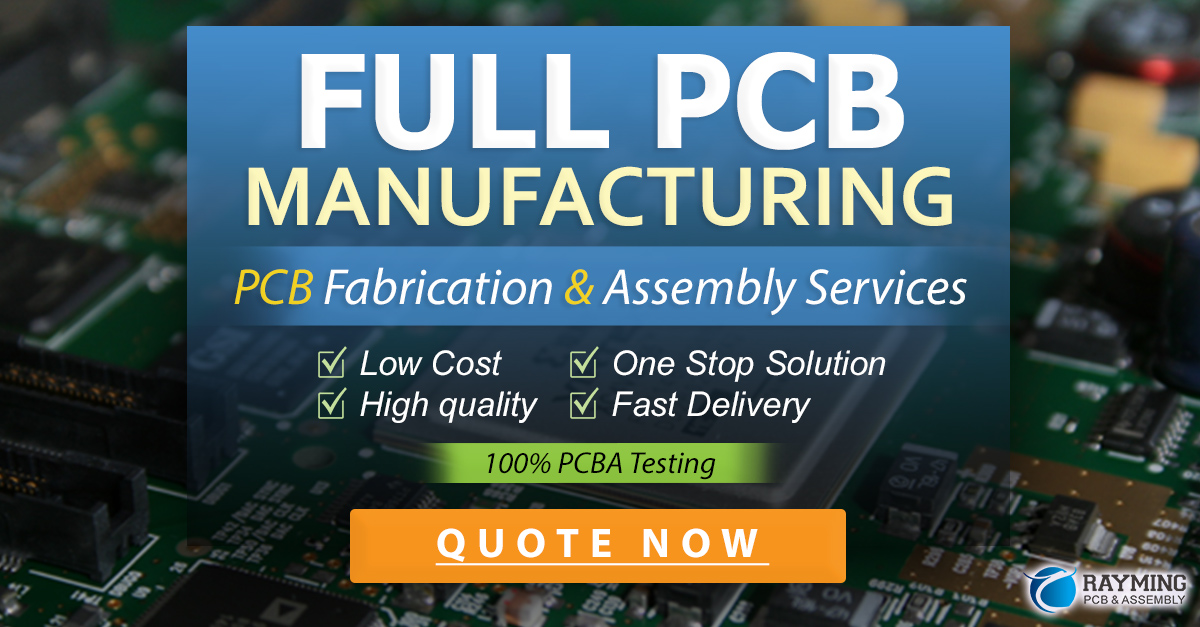
PCB Materials
The choice of materials used in PCB fabrication can have a significant impact on the performance and reliability of the finished product. Some of the most common PCB materials include:
FR-4
FR-4 is a glass-reinforced epoxy laminate that is widely used in PCB fabrication. It has good mechanical and electrical properties, as well as excellent thermal stability. FR-4 is the most common material used for rigid PCBs.
Polyimide
Polyimide is a high-performance polymer that is commonly used in flexible PCBs. It has excellent thermal and chemical resistance, as well as good mechanical properties. Polyimide is often used in applications that require high reliability and long-term stability.
PTFE
PTFE (polytetrafluoroethylene) is a fluoropolymer that is known for its low dielectric constant and low loss tangent. It is commonly used in high-frequency applications, such as radar and wireless communication systems.
PCB Testing and Inspection
To ensure the quality and reliability of PCBs, manufacturers employ a variety of testing and inspection techniques. Some of the most common methods include:
Automated Optical Inspection (AOI)
AOI uses computer vision technology to inspect PCBs for defects such as missing components, incorrect component placement, and solder defects. AOI systems can inspect PCBs at high speeds and with a high degree of accuracy.
X-Ray Inspection
X-ray inspection is used to detect defects that are not visible to the naked eye, such as voids in solder joints and internal cracks in components. X-ray systems can produce high-resolution images of the internal structure of a PCB.
In-Circuit Testing (ICT)
ICT is a technique used to test the functionality of individual components on a PCB. ICT systems use a bed-of-nails fixture to make electrical contact with the component leads and test for shorts, opens, and other faults.
PCB Design Software
PCB design software has come a long way since the early days of PCB development. Today, there are a variety of powerful tools available for PCB design, including:
Software | Description |
---|---|
Altium Designer | A comprehensive PCB design tool with advanced features such as 3D modeling and simulation. |
Eagle | A popular PCB design tool that is known for its ease of use and extensive library of components. |
KiCad | A free, open-source PCB design tool that is widely used in the open-source hardware community. |
OrCAD | A suite of PCB design tools that includes schematic capture, layout, and simulation capabilities. |
Future of PCB Development
As the demand for smaller, faster, and more complex electronic devices continues to grow, PCB technology will need to keep pace. Some of the trends and challenges facing PCB development in the coming years include:
Miniaturization
The trend towards miniaturization will continue to drive the development of smaller and more compact PCBs. This will require the use of advanced materials and manufacturing techniques, such as 3D printing and embedding of components.
High-Speed Design
As data rates continue to increase, PCBs will need to be designed to handle high-speed signals without introducing signal integrity issues. This will require the use of advanced simulation tools and design techniques, such as controlled impedance routing and differential signaling.
Sustainability
The electronics industry is facing increasing pressure to reduce its environmental impact. This will require the development of more sustainable PCB materials and manufacturing processes, as well as the design of products that are easier to recycle and reuse.
Conclusion
PCBs have come a long way since their early days, and they continue to play a critical role in the electronics industry. The development of new materials, manufacturing processes, and design tools will be essential to meeting the challenges of the future. As PCB technology continues to evolve, we can expect to see even more advanced and capable electronic devices in the years to come.
Frequently Asked Questions (FAQ)
1. What is a PCB?
A PCB (Printed Circuit Board) is a flat board made of insulating material with conductive tracks on one or both sides, used to connect electronic components together.
2. What are the different types of PCBs?
There are several types of PCBs, including:
– Single-sided PCBs: Have conductive tracks on one side only.
– Double-sided PCBs: Have conductive tracks on both sides, connected by through-hole plating.
– Multi-layer PCBs: Have multiple layers of conductive tracks separated by insulating layers.
– Flexible PCBs: Made of flexible materials that can bend and conform to different shapes.
– Rigid-Flex PCBs: Combine rigid and flexible sections for added flexibility and durability.
3. What materials are used to make PCBs?
PCBs are typically made of a combination of materials, including:
– Substrate: The base material, usually made of FR-4 (a glass-reinforced epoxy laminate).
– Copper: Used for the conductive tracks and pads.
– Solder mask: A protective layer that covers the copper tracks, leaving only the pads exposed.
– Silkscreen: Used for adding text and graphics to the PCB surface.
4. What is the difference between through-hole and surface-mount components?
Through-hole components have leads that are inserted into holes drilled in the PCB and soldered in place on the opposite side. Surface-mount components are mounted directly onto pads on the PCB surface and soldered in place.
5. What are the advantages of using PCBs?
PCBs offer several advantages over other methods of connecting electronic components, including:
– Compact size: PCBs allow for high component density and small form factors.
– Reliability: PCBs provide a stable and durable platform for electronic components.
– Consistency: PCBs are manufactured using automated processes, ensuring consistent quality and performance.
– Cost-effective: PCBs are relatively inexpensive to manufacture in large quantities.
– Flexibility: PCBs can be designed to meet a wide range of requirements and applications.
Leave a Reply