What is Gold Plating?
Gold plating is an electroplating process that involves depositing a thin layer of gold onto the surface of a PCB. The gold layer is typically applied over a nickel underlayer, which serves as a barrier between the copper substrate and the gold layer. The nickel layer prevents the diffusion of copper into the gold layer, which can cause the gold to become brittle and lose its desired properties.
Advantages of Gold Plating PCBs
Gold plating offers several advantages for PCBs, including:
- Excellent electrical conductivity
- High corrosion resistance
- Improved durability and wear resistance
- Enhanced solderability
- Compatibility with wire bonding and other advanced packaging techniques
These properties make gold-plated PCBs ideal for applications that require high reliability, long-term stability, and superior electrical performance.
The Gold Plating Process
The gold plating process for PCBs typically involves the following steps:
1. Surface Preparation
Before gold plating, the PCB surface must be thoroughly cleaned and prepared to ensure proper adhesion of the gold layer. This process includes:
- Degreasing: Removing oils, greases, and other contaminants from the PCB surface using solvents or alkaline cleaners.
- Microetching: Slightly roughening the copper surface to improve adhesion of the subsequent layers.
- Acid dipping: Removing any oxides or tarnish from the copper surface using a mild acid solution.
2. Nickel Plating
After surface preparation, a thin layer of nickel is electroplated onto the copper surface. The nickel layer serves as a barrier layer, preventing the diffusion of copper into the gold layer. The nickel layer also improves the overall durability and wear resistance of the PCB.
The nickel plating process involves:
- Activating the PCB surface using a mildly acidic solution to ensure uniform plating.
- Immersing the PCB in a nickel electroplating bath containing nickel salts and additives.
- Applying an electric current to deposit the nickel layer onto the PCB surface.
- Rinsing the PCB with deionized water to remove any residual plating solution.
3. Gold Plating
Once the nickel layer is applied, the PCB is ready for gold plating. The gold plating process is similar to nickel plating and involves:
- Immersing the PCB in a gold electroplating bath containing gold salts and additives.
- Applying an electric current to deposit the gold layer onto the nickel surface.
- Controlling the plating parameters (current density, temperature, and time) to achieve the desired gold thickness and uniformity.
- Rinsing the PCB with deionized water to remove any residual plating solution.
4. Post-Plating Treatment
After gold plating, the PCB may undergo additional treatments to enhance its properties or to prepare it for subsequent processes. These treatments may include:
- Heat treatment: Annealing the PCB to improve the adhesion between the layers and to relieve any internal stresses.
- Surface finish protection: Applying a clear protective coating to prevent oxidation and contamination of the gold surface.
- Electrical testing: Verifying the electrical continuity and resistance of the gold-plated circuits.
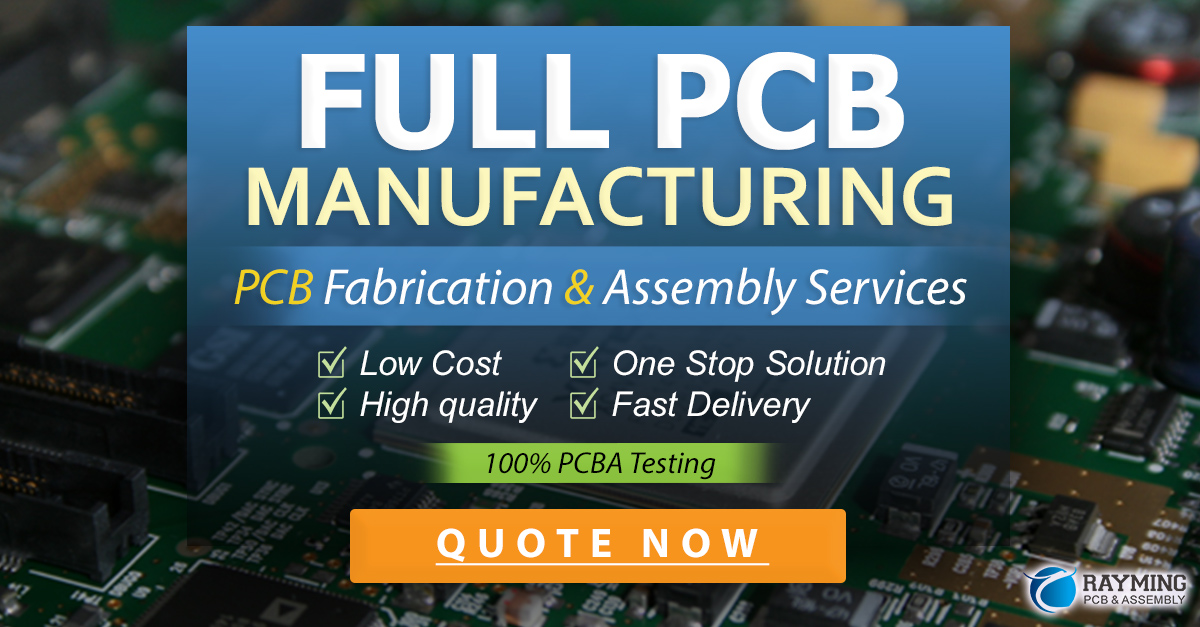
Factors Affecting Gold Plating Quality
Several factors can influence the quality of the gold plating on PCBs, including:
1. Gold Purity and Thickness
The purity and thickness of the gold layer are critical factors in determining the performance and durability of gold-plated PCBs. Higher gold purity (99.9% or above) and thicker gold layers (typically 1-5 µm) offer better corrosion resistance, electrical conductivity, and wear resistance.
2. Nickel Layer Characteristics
The properties of the nickel underlayer also play a significant role in the overall performance of gold-plated PCBs. The nickel layer should be:
- Sufficiently thick (2-5 µm) to provide an effective barrier against copper diffusion.
- Uniform in thickness and composition to ensure consistent properties across the PCB surface.
- Free from defects, such as pinholes, cracks, or nodules, which can compromise the integrity of the gold layer.
3. Plating Parameters
The electroplating parameters, such as current density, temperature, and plating time, must be carefully controlled to achieve the desired gold thickness, uniformity, and adhesion. Improper plating conditions can lead to issues such as:
- Uneven gold distribution
- Poor adhesion between the layers
- Excessive internal stresses, which can cause cracking or delamination
- Incorporation of impurities or defects in the gold layer
4. Surface Preparation
Proper surface preparation is essential for ensuring good adhesion between the copper substrate, nickel underlayer, and gold layer. Inadequate cleaning, microetching, or acid dipping can result in poor plating quality and reduced durability of the gold-plated PCB.
Common Applications of Gold-Plated PCBs
Gold-plated PCBs are used in a wide range of applications that require high reliability, excellent electrical performance, and durability. Some common applications include:
- Aerospace and military electronics
- Medical devices and implantable electronics
- High-frequency and RF applications
- Automotive electronics
- Industrial sensors and control systems
- High-end consumer electronics, such as smartphones and laptops
In these applications, gold-plated PCBs provide the necessary electrical and mechanical properties to ensure long-term reliability and performance under demanding conditions.
Alternatives to Gold Plating
While gold plating is a popular choice for high-performance PCBs, there are alternatives that may be suitable for certain applications. These include:
-
Immersion silver: A thin layer of silver is chemically deposited onto the copper surface, providing good electrical conductivity and solderability.
-
Organic solderability preservatives (OSP): A thin, organic coating is applied to the copper surface to protect it from oxidation and to enhance solderability.
-
Electroless nickel immersion gold (ENIG): A thin layer of gold is chemically deposited onto an electroless nickel underlayer, offering similar benefits to electroplated gold but with a more uniform thickness distribution.
Each of these alternatives has its own advantages and limitations, and the choice of surface finish depends on the specific requirements of the application, cost considerations, and manufacturing capabilities.
Frequently Asked Questions (FAQ)
- What is the typical thickness of the gold layer in gold-plated PCBs?
The typical thickness of the gold layer in gold-plated PCBs ranges from 1 to 5 µm (micrometers). The exact thickness depends on the specific application requirements, such as electrical conductivity, wear resistance, and cost considerations.
- Can gold plating be applied selectively to specific areas of a PCB?
Yes, gold plating can be applied selectively to specific areas of a PCB using a process called selective plating. This involves using masking techniques to protect the areas that do not require gold plating, while exposing the desired areas to the electroplating process.
- How does the purity of the gold affect the performance of gold-plated PCBs?
The purity of the gold used in plating PCBs affects its electrical conductivity, corrosion resistance, and durability. Higher purity gold (99.9% or above) offers better performance in these aspects compared to lower purity gold. However, higher purity gold also comes with a higher cost.
- What is the purpose of the nickel underlayer in gold-plated PCBs?
The nickel underlayer serves as a barrier between the copper substrate and the gold layer. It prevents the diffusion of copper into the gold layer, which can cause the gold to become brittle and lose its desired properties. The nickel layer also enhances the overall durability and wear resistance of the PCB.
- How can the quality of gold plating on PCBs be tested?
The quality of gold plating on PCBs can be tested using various methods, including:
- Visual inspection: Checking for surface defects, such as pinholes, cracks, or discoloration.
- Thickness measurement: Using X-ray fluorescence (XRF) or cross-sectioning techniques to measure the thickness of the gold and nickel layers.
- Adhesion testing: Performing tape tests or peel tests to assess the adhesion between the layers.
- Electrical testing: Measuring the electrical continuity and resistance of the gold-plated circuits.
- Environmental testing: Exposing the PCB to various environmental conditions (e.g., temperature, humidity, or corrosive atmospheres) to evaluate its long-term stability and performance.
Conclusion
Gold plating is a widely used surface finishing process for PCBs, offering excellent electrical conductivity, corrosion resistance, and durability. The common gold plating process involves surface preparation, nickel plating, gold plating, and post-plating treatments. The quality of the gold plating depends on several factors, including gold purity and thickness, nickel layer characteristics, plating parameters, and surface preparation.
Gold-plated PCBs are essential in various industries, such as aerospace, military, medical, and high-end consumer electronics, where high reliability and performance are critical. While alternatives to gold plating exist, such as immersion silver, OSP, and ENIG, gold plating remains the preferred choice for applications that demand the highest level of electrical and mechanical properties.
As technology advances and electronic devices become more sophisticated, the demand for high-quality gold-plated PCBs is expected to grow. By understanding the common gold plating process and the factors that influence its quality, manufacturers can optimize their plating operations to meet the evolving needs of the electronics industry.
Leave a Reply