Introduction to Anti-reflective soldermask
In the world of printed circuit boards (PCBs), the soldermask plays a crucial role in protecting the copper traces from oxidation and preventing solder bridges during the assembly process. While green is the most common color for soldermasks, there are instances where a black soldermask is preferred, particularly when light reflection is not desired. This is where the anti-reflective soldermask comes into play.
What is a soldermask?
A soldermask, also known as a solder resist or solder mask, is a thin layer of polymer applied to the surface of a PCB. Its primary purpose is to protect the copper traces from oxidation and prevent solder from bridging between adjacent pads during the soldering process. The soldermask also provides electrical insulation and helps to improve the durability of the PCB.
The role of color in soldermasks
Soldermasks come in various colors, with green being the most common. The choice of color is often a matter of preference or based on the specific requirements of the application. Some common soldermask colors include:
- Green
- Red
- Blue
- Yellow
- Black
Each color has its own characteristics and benefits. For example, red soldermasks are often used in high-voltage applications due to their increased visibility, while Blue Soldermasks are sometimes chosen for aesthetic reasons.
The importance of reducing light reflection
In certain applications, light reflection from the PCB surface can be problematic. This is particularly true in optical systems, where stray light can interfere with the desired signal or cause unwanted glare. In such cases, using a black soldermask can help to minimize light reflection and improve the overall performance of the system.
Applications where light reflection is undesirable
There are several applications where light reflection from the PCB surface can be detrimental:
-
Optical sensors: In devices that rely on optical sensors, such as cameras or scanners, stray light reflecting from the PCB can interfere with the sensor’s ability to accurately detect the desired signal.
-
Displays: In display applications, light reflection from the PCB can cause glare or reduce the contrast ratio, leading to a suboptimal viewing experience.
-
Infrared systems: In applications that use infrared light, such as remote controls or night vision devices, reflections from the PCB can interfere with the proper functioning of the system.
-
Automotive electronics: In automotive applications, light reflection from the PCB can cause distractions or interfere with the driver’s vision, particularly in low-light conditions.
The benefits of using a black soldermask
A black soldermask offers several advantages when it comes to reducing light reflection:
-
Low reflectivity: Black has the lowest reflectivity of any color, meaning that it absorbs most of the incident light. This makes it an ideal choice for applications where light reflection needs to be minimized.
-
Improved contrast: In display applications, a black soldermask can help to improve the contrast ratio by reducing the amount of stray light that reaches the viewer’s eyes.
-
Enhanced aesthetics: In some cases, a black soldermask can give the PCB a more professional and sleek appearance, which can be desirable for certain products.
-
Compatibility with other components: Black soldermasks are compatible with a wide range of components and materials, making them a versatile choice for various applications.
Choosing the right anti-reflective soldermask
When selecting an anti-reflective soldermask for your PCB, there are several factors to consider:
Material properties
The soldermask material should have the following properties:
- Low reflectivity in the desired wavelength range
- Good adhesion to the PCB surface
- High resistance to chemicals and solvents
- Excellent electrical insulation
- Compatibility with the desired manufacturing process
Some common anti-reflective soldermask materials include:
Material | Reflectivity (%) | Adhesion | Chemical Resistance | Insulation |
---|---|---|---|---|
Epoxy-based | < 5 | Good | High | Excellent |
Acrylic-based | < 3 | Excellent | Moderate | Good |
Polyurethane-based | < 4 | Very Good | High | Excellent |
Silicone-based | < 2 | Good | Very High | Excellent |
Application method
The soldermask can be applied to the PCB using various methods, such as:
- Screen printing
- Spray coating
- Curtain coating
- Electrophoretic deposition
The choice of application method will depend on factors such as the size and complexity of the PCB, the desired thickness of the soldermask, and the available equipment.
Curing process
After application, the soldermask must be cured to achieve its final properties. The curing process typically involves exposing the soldermask to UV light and/or heat. The specific curing requirements will depend on the soldermask material and the application method used.
Compatibility with other PCB materials
When selecting an anti-reflective soldermask, it is essential to ensure that it is compatible with the other materials used in the PCB, such as the substrate, copper traces, and components. Incompatible materials can lead to delamination, poor adhesion, or other issues that can compromise the reliability of the PCB.
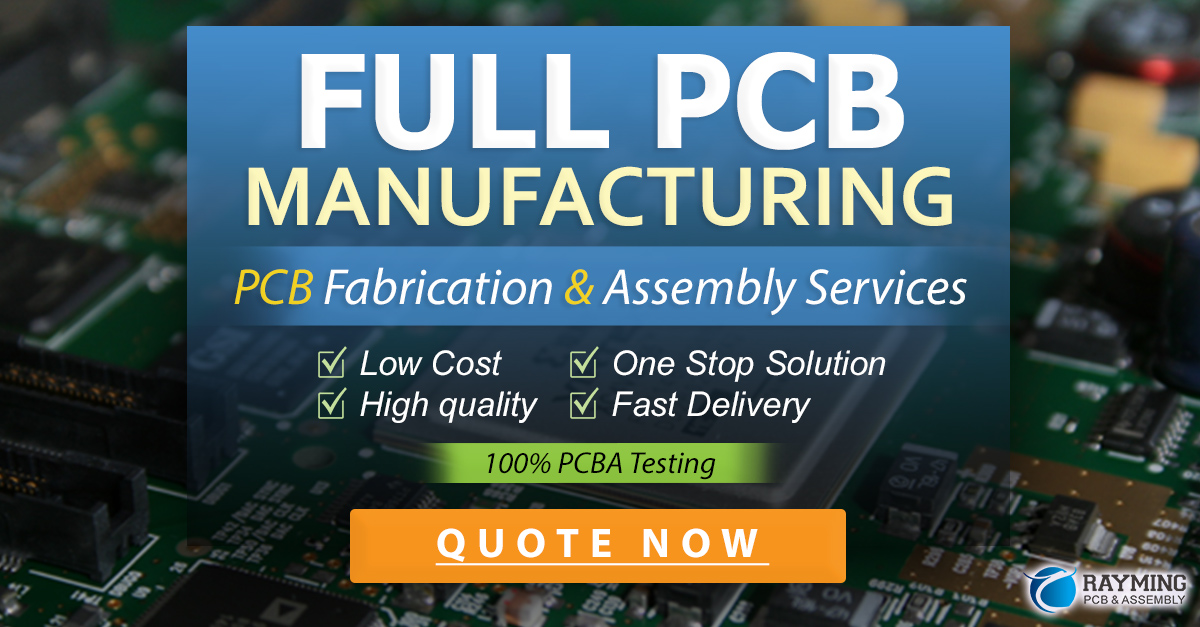
Designing PCBs with anti-reflective soldermasks
When designing a PCB that will use an anti-reflective soldermask, there are several considerations to keep in mind:
Pad and trace spacing
The soldermask will cover the areas between the pads and traces, so it is important to ensure that there is sufficient spacing to allow for proper coverage. The minimum spacing will depend on the soldermask material and the application method used.
Soldermask openings
Openings in the soldermask are necessary to allow for soldering of components and connectors. When designing these openings, it is important to consider the size and shape of the pads and the type of components being used. The openings should be large enough to allow for proper soldering but not so large that they compromise the protection provided by the soldermask.
Fiducial markers
Fiducial markers are used to help align the PCB during the assembly process. When using an anti-reflective soldermask, it is important to ensure that the fiducial markers are still visible and detectable by the assembly equipment. This may require using a different color or material for the fiducial markers.
Silkscreen considerations
The silkscreen is used to add text and graphics to the PCB surface. When using an anti-reflective soldermask, it is important to ensure that the silkscreen is still legible and does not interfere with the soldermask’s performance. This may require using a different color or material for the silkscreen or adjusting the design to ensure adequate contrast.
Manufacturing PCBs with anti-reflective soldermasks
The manufacturing process for PCBs with anti-reflective soldermasks is similar to that of standard PCBs, with a few additional steps:
Surface preparation
Before applying the soldermask, the PCB surface must be cleaned and prepared to ensure good adhesion. This typically involves a combination of chemical cleaning and mechanical abrasion to remove any contaminants or oxidation.
Soldermask application
The soldermask is then applied to the PCB surface using the chosen application method. The thickness of the soldermask layer will depend on the specific material and application requirements but is typically in the range of 10-50 microns.
Curing
After application, the soldermask is cured using UV light and/or heat. The curing process helps to crosslink the polymers in the soldermask, giving it its final properties.
Inspection
Once the soldermask is cured, the PCB is inspected to ensure that the coverage is complete and that there are no defects or voids. Any issues must be addressed before the PCB can move on to the next stage of manufacturing.
Assembly
The final step is to assemble the components onto the PCB. The anti-reflective soldermask should not interfere with the assembly process, but it is important to ensure that the soldermask openings are properly aligned with the pads and that the components are seated correctly.
FAQ
-
Q: What is the main benefit of using a black soldermask?
A: The main benefit of using a black soldermask is its ability to reduce light reflection from the PCB surface, which can be important in applications where stray light can interfere with the desired signal or cause unwanted glare. -
Q: Are black soldermasks more expensive than other colors?
A: Black soldermasks may be slightly more expensive than standard green soldermasks due to the additional pigments and processing required. However, the cost difference is usually not significant and is often outweighed by the performance benefits in applications where light reflection is a concern. -
Q: Can a black soldermask be used with any PCB substrate material?
A: Black soldermasks are compatible with most common PCB substrate materials, including FR-4, polyimide, and aluminum. However, it is important to ensure that the soldermask material is specifically formulated for the chosen substrate to ensure good adhesion and compatibility. -
Q: How does the thickness of the soldermask affect its anti-reflective properties?
A: The thickness of the soldermask does not have a significant impact on its anti-reflective properties, as the reflectivity is primarily determined by the pigments and surface texture of the material. However, a thicker soldermask layer can provide better protection against oxidation and mechanical damage. -
Q: Are there any special considerations when soldering components on a PCB with a black soldermask?
A: The soldering process for PCBs with black soldermasks is generally the same as for other soldermask colors. However, it is important to ensure that the soldermask openings are properly aligned with the pads and that the solder mask material is compatible with the chosen soldering method (e.g., wave soldering, reflow soldering) to ensure reliable solder joints.
Conclusion
Anti-reflective soldermasks, particularly those in black, offer a valuable solution for applications where light reflection from the PCB surface can be problematic. By reducing stray light and improving contrast, black soldermasks can enhance the performance of optical systems, displays, and other sensitive electronics.
When selecting an anti-reflective soldermask, it is important to consider factors such as the material properties, application method, curing process, and compatibility with other PCB materials. By carefully designing and manufacturing PCBs with anti-reflective soldermasks, engineers and manufacturers can create products that meet the demanding requirements of today’s advanced electronic systems.
As technology continues to evolve, the use of anti-reflective soldermasks is likely to become increasingly important in a wide range of applications. By understanding the benefits and considerations associated with these materials, PCB designers and manufacturers can stay ahead of the curve and deliver high-performance products that meet the needs of their customers.
Leave a Reply