What is PCB Cutting?
PCB cutting is the process of separating a large PCB panel into individual PCBs or smaller panels. This process is necessary because PCBs are typically manufactured in large panels to maximize production efficiency and reduce costs. Once the PCBs are fabricated, they need to be cut into their final sizes and shapes before they can be used in electronic devices.
Why is PCB Cutting Important?
PCB cutting is important for several reasons:
-
Functionality: Properly cut PCBs ensure that the electronic components can be correctly mounted and soldered, resulting in a functional device.
-
Aesthetics: Clean and precise cuts contribute to the overall appearance of the final product.
-
Cost-effectiveness: Accurate PCB cutting minimizes material waste and reduces production costs.
-
Time-saving: Efficient PCB cutting methods can significantly reduce the time required for the manufacturing process.
Methods for PCB Cutting
There are several methods for cutting PCBs, each with its own advantages and disadvantages. The choice of the cutting method depends on factors such as the PCB material, thickness, desired cut quality, and production volume. Let’s explore some of the most common PCB cutting methods:
1. Manual Cutting
Manual cutting is the most basic method for cutting PCBs. It involves using hand tools like scissors, knives, or saws to cut the PCB along the desired lines. This method is suitable for low-volume production, prototyping, or when the cut quality is not a critical factor.
Advantages:
– Low cost
– No specialized equipment required
– Suitable for small-scale production or prototyping
Disadvantages:
– Time-consuming
– Inconsistent cut quality
– Risk of damaging the PCB
– Not suitable for high-volume production
2. Shearing
Shearing is a mechanical cutting method that uses a shear machine to cut PCBs. The machine consists of a fixed blade and a moving blade that apply a shearing force to the PCB, causing it to split along the cutting line. This method is suitable for cutting straight lines on PCBs with a thickness of up to 3 mm.
Advantages:
– Fast and efficient
– Suitable for high-volume production
– Relatively low cost compared to other mechanical cutting methods
Disadvantages:
– Limited to straight cuts
– Not suitable for cutting intricate shapes or designs
– May cause deformation or burrs on the cut edges
3. Punching
Punching is another mechanical cutting method that uses a punch and die set to cut PCBs. The punch is a sharp tool that is forced through the PCB and into a die, creating a clean cut. This method is suitable for cutting simple shapes like circles, squares, or rectangles on PCBs with a thickness of up to 3 mm.
Advantages:
– Fast and efficient
– Suitable for high-volume production
– Produces clean and precise cuts
– Can cut simple shapes
Disadvantages:
– Limited to simple shapes
– Requires specialized equipment
– May cause deformation or burrs on the cut edges
4. Routing
Routing is a computer-controlled cutting method that uses a rotating cutting tool called a router bit to cut PCBs. The router bit is guided along a programmed path, cutting through the PCB material. This method is suitable for cutting complex shapes, contours, and cutouts on PCBs with a thickness of up to 6 mm.
Advantages:
– High precision and accuracy
– Can cut complex shapes and designs
– Suitable for high-volume production
– Minimal deformation or burrs on the cut edges
Disadvantages:
– Requires specialized equipment
– Higher cost compared to other cutting methods
– May cause vibration or chipping during the cutting process
5. Laser Cutting
Laser cutting is a non-contact cutting method that uses a high-powered laser beam to cut PCBs. The laser beam vaporizes the PCB material along the programmed path, creating a clean and precise cut. This method is suitable for cutting intricate shapes, fine details, and small features on PCBs with a thickness of up to 2 mm.
Advantages:
– High precision and accuracy
– Can cut intricate shapes and fine details
– No mechanical stress on the PCB
– Minimal deformation or burrs on the cut edges
Disadvantages:
– Requires specialized equipment
– Higher cost compared to other cutting methods
– Limited to thin PCBs
– May cause thermal stress or discoloration on the cut edges
6. V-Scoring
V-scoring is a specialized cutting method that uses a V-shaped cutting tool to create a groove along the desired cutting line on the PCB. The groove weakens the PCB material, allowing it to be easily broken along the score line. This method is suitable for separating large PCB panels into smaller panels or individual PCBs.
Advantages:
– Fast and efficient
– Suitable for high-volume production
– Minimal material waste
– Enables easy separation of PCBs
Disadvantages:
– Limited to straight lines
– May cause breakage or deformation if not handled carefully
– Requires specialized equipment
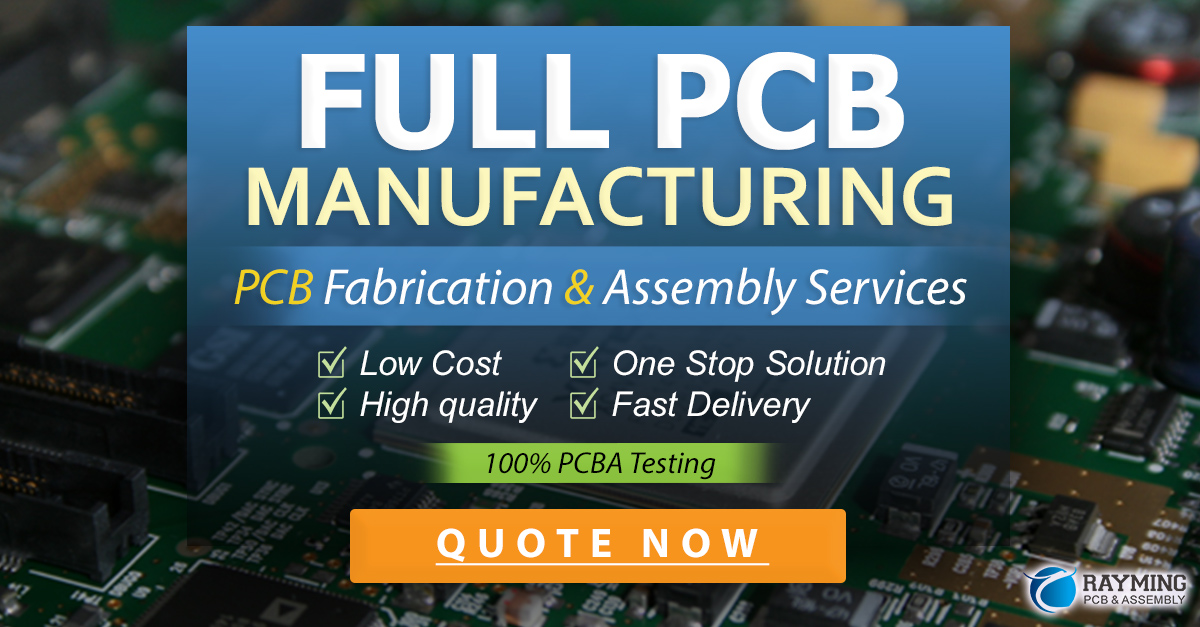
Choosing the Best PCB Cutting Method
When choosing the best PCB cutting method for your project, consider the following factors:
-
PCB material and thickness: Different cutting methods are suitable for different PCB materials and thicknesses. Ensure that the chosen method is compatible with your PCB specifications.
-
Desired cut quality: Consider the required cut quality, such as precision, accuracy, and minimal deformation or burrs on the cut edges.
-
Production volume: Select a cutting method that can efficiently handle your production volume, whether it’s low-volume prototyping or high-volume manufacturing.
-
Cost: Evaluate the cost of the cutting method, including equipment, materials, and labor costs, and choose the one that fits your budget.
-
Shape complexity: If your PCB design includes complex shapes, contours, or fine details, choose a cutting method that can accommodate these requirements, such as routing or laser cutting.
Tips for Successful PCB Cutting
To ensure successful PCB cutting, follow these tips:
-
Use the appropriate cutting tools: Choose cutting tools that are compatible with your PCB material and thickness, and ensure that they are sharp and well-maintained.
-
Secure the PCB: Firmly secure the PCB during the cutting process to prevent movement or vibration, which can affect the cut quality.
-
Follow the cutting lines: Carefully follow the cutting lines or programmed paths to ensure accurate and precise cuts.
-
Protect the PCB: Use protective measures, such as covering the PCB surface or using vacuum cleaners, to prevent dust or debris from contaminating the PCB during the cutting process.
-
Inspect the cut edges: After cutting, inspect the cut edges for any deformation, burrs, or damage, and make necessary adjustments to the cutting process if needed.
Frequently Asked Questions (FAQ)
- What is the most precise PCB cutting method?
-
Laser cutting and routing are the most precise PCB cutting methods, capable of cutting intricate shapes and fine details with high accuracy.
-
Can I cut PCBs with a regular scissor?
-
While it is possible to cut thin PCBs with a regular scissor, it is not recommended as it may result in poor cut quality and damage to the PCB. It is better to use specialized cutting tools designed for PCBs.
-
How thick of a PCB can be cut using the shearing method?
-
The shearing method is suitable for cutting PCBs with a thickness of up to 3 mm.
-
Is laser cutting suitable for all PCB materials?
-
Laser cutting is suitable for most PCB materials, but some materials may require special considerations. For example, PCBs with metallic substrates or heat-sensitive components may not be suitable for laser cutting.
-
What is the most cost-effective PCB cutting method for high-volume production?
- Shearing and punching are generally the most cost-effective PCB cutting methods for high-volume production, as they are fast, efficient, and require relatively low investment in equipment.
Conclusion
Choosing the best way to cut PCB board is crucial for ensuring the functionality, aesthetics, and cost-effectiveness of your electronic devices. By understanding the various PCB cutting methods, their advantages and disadvantages, and considering factors such as PCB material, thickness, desired cut quality, and production volume, you can select the most suitable cutting method for your project.
Remember to follow the tips for successful PCB cutting, such as using appropriate cutting tools, securing the PCB, following the cutting lines, protecting the PCB, and inspecting the cut edges. By doing so, you can achieve high-quality PCB cuts that meet your requirements and contribute to the overall success of your electronic projects.
PCB Cutting Method | Advantages | Disadvantages |
---|---|---|
Manual Cutting | – Low cost – No specialized equipment required – Suitable for small-scale production or prototyping |
– Time-consuming – Inconsistent cut quality – Risk of damaging the PCB – Not suitable for high-volume production |
Shearing | – Fast and efficient – Suitable for high-volume production – Relatively low cost compared to other mechanical cutting methods |
– Limited to straight cuts – Not suitable for cutting intricate shapes or designs – May cause deformation or burrs on the cut edges |
Punching | – Fast and efficient – Suitable for high-volume production – Produces clean and precise cuts – Can cut simple shapes |
– Limited to simple shapes – Requires specialized equipment – May cause deformation or burrs on the cut edges |
Routing | – High precision and accuracy – Can cut complex shapes and designs – Suitable for high-volume production – Minimal deformation or burrs on the cut edges |
– Requires specialized equipment – Higher cost compared to other cutting methods – May cause vibration or chipping during the cutting process |
Laser Cutting | – High precision and accuracy – Can cut intricate shapes and fine details – No mechanical stress on the PCB – Minimal deformation or burrs on the cut edges |
– Requires specialized equipment – Higher cost compared to other cutting methods – Limited to thin PCBs – May cause thermal stress or discoloration on the cut edges |
V-Scoring | – Fast and efficient – Suitable for high-volume production – Minimal material waste – Enables easy separation of PCBs |
– Limited to straight lines – May cause breakage or deformation if not handled carefully – Requires specialized equipment |
Leave a Reply