What are Vias?
Vias are small holes drilled in a printed circuit board (PCB) that allow electrical connections to be made between different layers of the board. They are an essential component in multilayer PCB design, enabling complex circuits to be routed in a compact space.
Vias come in several types, each with its own characteristics and applications:
Via Type | Description | Typical Size |
---|---|---|
Through Hole | Goes completely through the PCB, may be used for component leads | 0.5-1.0 mm |
Blind | Connects an outer layer to an inner layer, but does not go through the entire board | 0.1-0.5 mm |
Buried | Connects inner layers, does not reach either surface of the PCB | 0.1-0.5 mm |
Micro | Very small through hole via used for high density designs | 0.05-0.1 mm |
The choice of via type depends on factors such as the complexity of the circuit, the available board space, the required electrical performance, and manufacturing cost constraints. Designing the via structure is a key part of the PCB layout process.
Why is Via Analysis Important?
As PCBs have become more complex and miniaturized, with higher layer counts and finer pitches, the impact of vias on circuit performance has increased. Vias can introduce signal integrity issues, add capacitance and inductance, and limit the routing density.
Some of the key reasons to perform via analysis include:
Signal Integrity
At high frequencies, vias can cause reflections, crosstalk, and other signal degradation effects. The via barrel acts as a small stub antenna, while the pad capacitance creates a discontinuity. Careful design of the via geometry and placement is necessary to minimize these issues.
Impedance Control
Maintaining a consistent characteristic impedance is critical for high-speed signals. Vias introduce a local impedance change that can cause reflections if not properly matched. The via structure must be optimized to provide a smooth impedance transition.
Thermal Management
Vias play an important role in conducting heat away from power-hungry components. Thermal vias are often added under devices such as FPGAs, processors, and motor drivers to transfer heat to the inner layers or a heatsink. The size, number, and placement of thermal vias must be analyzed to ensure adequate cooling.
Manufacturing Constraints
The via design must take into account the capabilities of the PCB fabrication process. Smaller vias are more difficult and expensive to manufacture reliably. The aspect ratio (depth to diameter) of the vias is limited by the plating process. Vias that are too close together may create yield problems.
Via Analysis Techniques
A range of techniques can be used to analyze and optimize the via structure in a PCB design:
3D Electromagnetic Simulation
Full-wave 3D EM simulators such as Ansys HFSS or CST Studio can be used to model the detailed geometry of the vias and predict their electrical behavior. This allows parameters such as the via inductance, capacitance, and impedance to be extracted, and signal integrity effects to be investigated. However, 3D EM simulation is computationally intensive and requires significant setup time.
Analytical Formulas
For simpler via structures, closed-form equations can provide a quick way to estimate key parameters. For example, the via inductance can be approximated as:
L = 5.08 h [ln(4h/d) + 1]
where L is the inductance in nH, h is the via length in mm, and d is the via diameter in mm.
Similarly, the via-to-plane capacitance can be estimated using:
C = 1.41 εr d l / ln(D/d)
where C is the capacitance in pF, εr is the dielectric constant of the PCB material, d is the via diameter in mm, l is the via length through the plane in mm, and D is the antipad diameter in mm.
These formulas can be used for rapid “what if” analysis during the design process, but may not capture all the relevant effects in complex structures.
EDA Via Tools
Most PCB layout software includes built-in tools for via analysis and design. These may allow the via stackup, drill sizes, and antipads to be defined parametrically, and provide features such as automatic via stitching and via-in-pad creation. More advanced tools can perform rule-based design checks and extract models for simulation.
For example, Cadence Allegro has a Via Structure Generator that allows custom via spans and topologies to be defined graphically. It checks the via design against manufacturing constraints and generates a detailed 3D solid model. This model can be used for impedance extraction and exported to EM simulators.
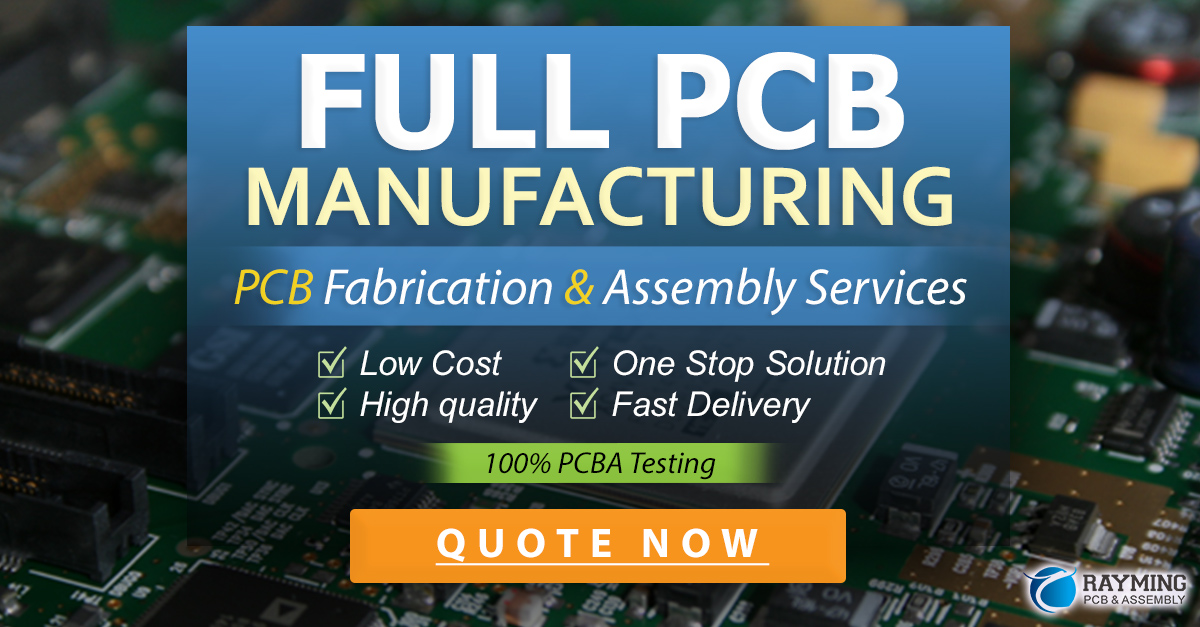
Via Optimization Strategies
Based on the results of via analysis, various techniques can be used to optimize the via design for better electrical and thermal performance:
Via Shielding
Adding ground vias around signal vias can help to reduce crosstalk and contain the electromagnetic fields. The spacing and number of shield vias must be carefully chosen to balance the shielding effectiveness against the routing density impact. Typically, two to four ground vias are placed in a symmetrical pattern around each signal via.
Differential Pair Vias
High-speed differential pairs should maintain a constant spacing through vias to avoid mode conversion. The vias should be symmetrical and as short as possible. If the via length is significant relative to the signal rise time, a larger antipad may be needed to compensate for the via-to-via capacitance. In some cases, a differential impedance-controlled via structure may be required.
Via Stubs
The unused portion of a through hole via below the signal layer acts as a stub that can cause reflections. To mitigate this effect, the via stubs can be backdrilled to remove the excess copper. Alternatively, blind or buried vias can be used to avoid creating stubs in the first place. For high-frequency signals, the via stub length should be kept much shorter than a quarter wavelength at the maximum frequency of interest.
Thermal Via Optimization
The thermal resistance of a via array can be minimized by increasing the number and size of the vias, and by placing them as close to the heat source as possible. However, this must be balanced against the impact on routing density and signal integrity. Thermal simulation can be used to find the optimal via placement and design for a given power dissipation and temperature rise target.
FAQ
Q: What is the difference between a blind via and a buried via?
A: A blind via connects an outer layer of the PCB to an inner layer, but does not go through the entire board. A buried via only connects inner layers and does not reach either surface of the PCB.
Q: How do vias affect signal integrity?
A: Vias can cause signal integrity issues such as reflections, crosstalk, and impedance discontinuities. The via barrel acts as a small stub antenna, while the pad capacitance creates a discontinuity. Careful design of the via geometry and placement is necessary to minimize these effects.
Q: What is via shielding and why is it used?
A: Via shielding involves placing ground vias around a signal via to reduce crosstalk and contain the electromagnetic fields. Typically, two to four ground vias are placed symmetrically around each signal via. The spacing and number of shield vias must be chosen to balance the shielding effectiveness against the impact on routing density.
Q: How can via stubs be mitigated?
A: Via stubs are the unused portion of a through hole via below the signal layer, which can cause reflections. To mitigate this effect, the via stubs can be backdrilled to remove the excess copper. Alternatively, blind or buried vias can be used to avoid creating stubs. For high-frequency signals, the via stub length should be kept much shorter than a quarter wavelength at the maximum frequency of interest.
Q: What is the role of vias in thermal management?
A: Vias play an important role in conducting heat away from power-hungry components on a PCB. Thermal vias are often added under devices such as FPGAs, processors, and motor drivers to transfer heat to the inner layers or a heatsink. The size, number, and placement of thermal vias must be optimized to ensure adequate cooling while minimizing the impact on routing density and signal integrity.
Conclusion
Via analysis is a critical aspect of modern PCB design, with significant impacts on signal integrity, impedance control, thermal management, and manufacturability. A range of techniques can be used to analyze via performance, including 3D EM simulation, analytical formulas, and EDA tools.
Based on the analysis results, the via structure can be optimized using strategies such as shielding, differential pair routing, stub mitigation, and thermal placement. By carefully designing and analyzing the vias, PCB designers can ensure robust and reliable operation of complex, high-speed systems.
Leave a Reply