What is Surface Mount PCB assembly (SMPCBA)?
Surface Mount PCB Assembly is a method of assembling electronic components onto a printed circuit board (PCB) using surface mount technology (SMT). Unlike through-hole technology, where components are inserted into holes drilled in the PCB, surface mount components are placed directly onto the surface of the board.
SMPCBA has become the preferred method for assembling electronic devices due to its numerous advantages, including:
- Smaller component sizes
- Higher component density
- Improved performance
- Reduced manufacturing costs
- Faster assembly process
The Surface Mount PCB Assembly Process
The surface mount PCB assembly process involves several steps, each of which is critical to ensuring the quality and reliability of the final product. The main steps in the SMPCBA process are:
1. Solder Paste Application
The first step in the SMPCBA process is the application of solder paste onto the PCB. Solder paste is a mixture of tiny solder particles suspended in a flux medium. It is applied to the PCB using a stencil or screen printing process, ensuring that the correct amount of solder is deposited on the pads where the components will be placed.
2. Component Placement
Once the solder paste has been applied, the surface mount components are placed onto the PCB using a pick-and-place machine. These machines use computer-controlled robotic arms to accurately place components onto the board at high speeds. The components are held in place by the tackiness of the solder paste.
3. Reflow Soldering
After the components have been placed, the PCB undergoes a reflow soldering process. The board is passed through a reflow oven, which heats the solder paste to its melting point. As the solder melts, it forms a strong electrical and mechanical bond between the components and the PCB. The reflow profile, which defines the temperature and duration of the heating process, is carefully controlled to ensure optimal results.
4. Inspection and Testing
Following the reflow soldering process, the assembled PCB undergoes inspection and testing to ensure that all components are properly placed and functioning as intended. Automated optical inspection (AOI) systems are often used to check for missing or misaligned components, while electrical testing is performed to verify the functionality of the assembled board.
Choosing a Surface Mount PCB Assembly Company
When selecting a surface mount PCB assembly company, there are several key factors to consider to ensure that you receive high-quality, reliable products. These factors include:
1. Experience and Expertise
Look for a company with extensive experience in surface mount PCB assembly and a proven track record of delivering quality products. The company should have a team of skilled technicians and engineers who are well-versed in the latest SMPCBA technologies and techniques.
2. Equipment and Facilities
The SMPCBA company should have state-of-the-art equipment and facilities to ensure the highest level of precision and reliability in the assembly process. This includes advanced pick-and-place machines, reflow ovens, and inspection systems.
3. Quality Control and Certifications
Choose a company that adheres to strict quality control standards and holds relevant certifications, such as ISO 9001 and IPC-A-610. These certifications demonstrate the company’s commitment to quality and adherence to industry best practices.
4. Customer Support and Communication
Effective communication and responsive customer support are essential when working with a surface mount PCB assembly company. Look for a company that is easy to communicate with, provides regular updates on your project’s progress, and is willing to address any concerns or questions you may have.
5. Cost and Lead Time
While cost is an important consideration, it should not be the sole deciding factor when choosing an SMPCBA company. Balancing cost with quality, reliability, and lead time is crucial. Look for a company that offers competitive pricing without compromising on the quality of the final product.
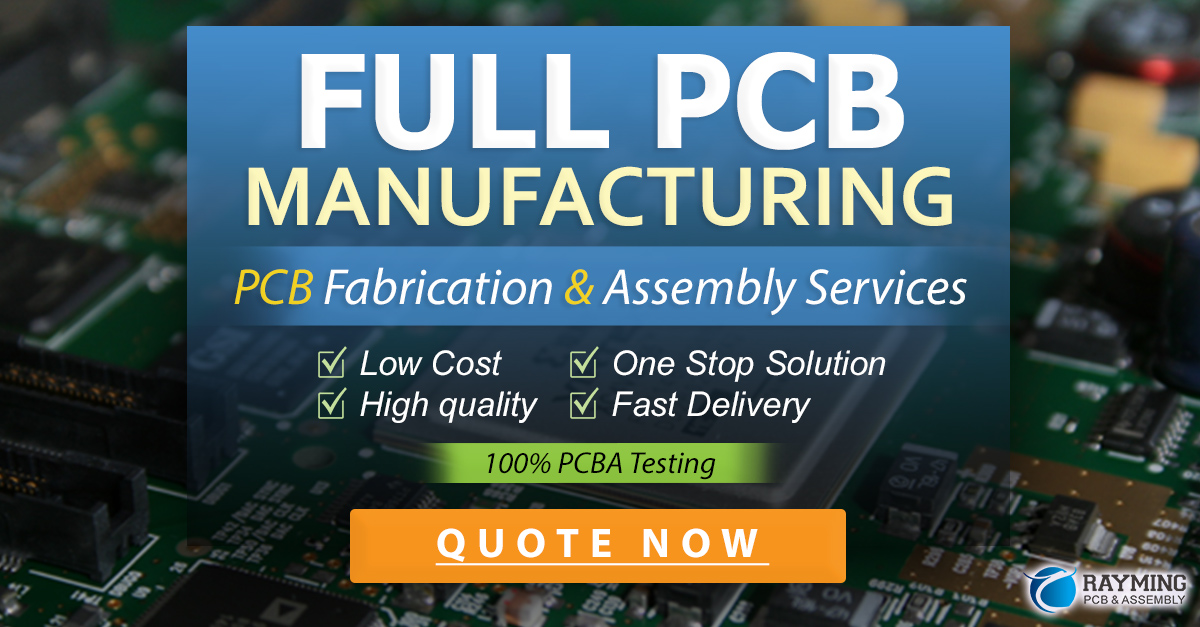
Advantages of Surface Mount PCB Assembly
Surface mount PCB assembly offers numerous advantages over through-hole assembly, making it the preferred choice for many electronic devices. Some of the key advantages of SMPCBA include:
1. Smaller Component Sizes
Surface mount components are significantly smaller than their through-hole counterparts, allowing for more compact designs and higher component density on the PCB. This is particularly important in today’s increasingly miniaturized electronic devices, such as smartphones, wearables, and IoT devices.
2. Improved Performance
SMPCBA enables shorter signal paths between components, reducing parasitic capacitance and inductance. This results in improved electrical performance, particularly at high frequencies, making surface mount technology ideal for high-speed digital circuits and RF applications.
3. Reduced Manufacturing Costs
The automated nature of the surface mount PCB assembly process, combined with the smaller component sizes, leads to reduced manufacturing costs compared to through-hole assembly. SMPCBA allows for faster assembly times, lower material costs, and reduced labor requirements, making it a cost-effective choice for high-volume production.
4. Enhanced Reliability
Surface mount components have a stronger mechanical bond to the PCB compared to through-hole components, thanks to the larger contact area between the component leads and the solder pads. This improved mechanical stability, along with the reduced number of drill holes in the PCB, enhances the overall reliability of the assembled board.
5. Faster Assembly Process
The automated pick-and-place machines used in SMPCBA can place components onto the PCB at extremely high speeds, often exceeding 100,000 components per hour. This, combined with the parallel processing capabilities of reflow soldering, enables much faster assembly times compared to manual through-hole assembly.
Surface Mount PCB Assembly vs. Through-Hole Assembly
While surface mount PCB assembly has become the dominant technology in the electronics industry, through-hole assembly still has its place in certain applications. The following table compares the key aspects of SMPCBA and through-hole assembly:
Aspect | Surface Mount PCB Assembly | Through-Hole Assembly |
---|---|---|
Component Sizes | Smaller, more compact | Larger, less compact |
Component Density | Higher | Lower |
Performance | Improved, particularly at high frequencies | Suitable for low-frequency applications |
Manufacturing Costs | Lower, especially for high-volume production | Higher, due to manual labor and longer assembly times |
Reliability | Enhanced mechanical stability and fewer drill holes | Suitable for applications requiring strong mechanical connections |
Assembly Speed | Faster, thanks to automation | Slower, due to manual placement and soldering |
Frequently Asked Questions (FAQ)
1. What is the difference between surface mount and through-hole components?
Surface mount components are designed to be placed directly onto the surface of a PCB, while through-hole components have leads that are inserted into holes drilled in the board. Surface mount components are generally smaller and enable higher component density, while through-hole components offer stronger mechanical connections.
2. Can surface mount and through-hole components be used on the same PCB?
Yes, it is possible to use both surface mount and through-hole components on the same PCB. This is known as a mixed-technology or hybrid assembly. However, it is essential to consider the impact on the assembly process and ensure that the design is optimized for manufacturability.
3. What is the role of solder paste in surface mount PCB assembly?
Solder paste is a critical material in the SMPCBA process. It is a mixture of tiny solder particles suspended in a flux medium, which is applied to the PCB pads before component placement. The solder paste holds the components in place during the reflow soldering process and forms the electrical and mechanical connection between the components and the board.
4. How does the reflow soldering process work in SMPCBA?
During the reflow soldering process, the PCB with the placed components is passed through a reflow oven. The oven heats the board according to a carefully controlled temperature profile, causing the solder paste to melt and form a strong bond between the components and the PCB pads. The temperature profile is designed to ensure optimal solder joint formation and minimize thermal stress on the components.
5. What certifications should I look for when choosing a surface mount PCB assembly company?
When selecting an SMPCBA company, look for certifications such as ISO 9001, which demonstrates the company’s commitment to quality management systems, and IPC-A-610, which is the industry standard for electronic assemblies. Other relevant certifications may include IPC-J-STD-001 (requirements for soldered electrical and electronic assemblies) and IPC-7711/7721 (rework, modification, and repair of electronic assemblies).
Conclusion
Surface mount PCB assembly has revolutionized the electronics industry, enabling the production of smaller, faster, and more reliable electronic devices. By understanding the SMPCBA process, its advantages, and the key factors to consider when choosing a surface mount PCB assembly company, you can ensure that your electronic products are manufactured to the highest standards of quality and performance.
As technology continues to advance and the demand for more complex and compact electronic devices grows, the importance of surface mount PCB assembly will only continue to increase. By partnering with a reputable and experienced SMPCBA company, you can stay ahead of the curve and bring your innovative electronic products to market quickly and efficiently.
Leave a Reply