Introduction
Printed Circuit Board (PCB) assembly is a crucial process in the manufacturing of electronic devices. It involves the placement and soldering of various components onto a PCB to create a functional circuit. The success of a PCB Assembly project depends on several factors, including the design of the PCB, the selection of components, and the assembly process itself. In this article, we will discuss the steps involved in a successful PCB assembly process for efficient PCB Prototyping and production.
The Importance of PCB Assembly
PCB assembly is an essential process in the manufacturing of electronic devices. It is the process of placing and soldering various components onto a PCB to create a functional circuit. The quality of the PCB assembly directly affects the performance and reliability of the final product. A poorly assembled PCB can lead to malfunctions, short circuits, and even complete failure of the device. Therefore, it is crucial to ensure that the PCB assembly process is carried out with the utmost care and precision.
Benefits of PCB Assembly
-
Increased Reliability: A well-assembled PCB ensures that the electronic device functions as intended, without any malfunctions or failures.
-
Improved Performance: Proper PCB assembly ensures that the components are placed and soldered correctly, resulting in optimal performance of the device.
-
Cost-Effective: PCB assembly allows for the mass production of electronic devices, which reduces the overall cost of manufacturing.
-
Faster Time-to-Market: An efficient PCB assembly process enables faster prototyping and production, allowing companies to bring their products to market quickly.
Steps to a Successful PCB Assembly
Step 1: PCB Design and Layout
The first step in the PCB assembly process is the design and layout of the PCB. This involves creating a schematic diagram of the circuit and then translating it into a physical layout. The layout determines the placement of components, traces, and vias on the PCB. It is essential to ensure that the layout is optimized for manufacturability, reliability, and functionality.
Tips for PCB Design and Layout
-
Use a PCB design software: There are several PCB design software available in the market, such as Altium Designer, Eagle, and KiCad. These software provide a user-friendly interface and powerful tools for creating PCB layouts.
-
Follow design rules: Each PCB manufacturer has its own set of design rules that must be followed to ensure manufacturability. These rules include minimum trace width, minimum spacing between components, and drill hole sizes.
-
Consider component placement: The placement of components on the PCB is crucial for optimal performance and reliability. It is essential to consider factors such as signal integrity, thermal management, and mechanical stress when placing components.
-
Use a grid system: Using a grid system helps in aligning components and traces, making the layout more organized and easier to read.
Step 2: Component Selection
The next step in the PCB assembly process is the selection of components. It is essential to choose components that are compatible with the PCB design and meet the requirements of the final product. The selection of components also depends on factors such as cost, availability, and lead time.
Tips for Component Selection
-
Use reputable suppliers: It is essential to use reputable suppliers who provide high-quality components with reliable delivery times.
-
Consider lead times: Some components may have longer lead times than others, which can affect the overall production schedule. It is essential to consider lead times when selecting components.
-
Use standardized components: Using standardized components reduces the risk of obsolescence and makes it easier to find replacements in the future.
-
Consider cost: The cost of components can significantly affect the overall cost of the final product. It is essential to find a balance between cost and quality when selecting components.
Step 3: PCB Fabrication
Once the PCB design and component selection are complete, the next step is PCB fabrication. This involves the manufacturing of the physical PCB based on the design files. PCB fabrication typically involves the following processes:
- Printing the circuit pattern on a copper-clad laminate
- Etching away the unwanted copper to create the circuit traces
- Drilling holes for through-hole components and vias
- Applying a solder mask and silkscreen for protection and labeling
Tips for PCB Fabrication
-
Choose a reputable PCB manufacturer: It is essential to choose a reputable PCB manufacturer with a proven track record of producing high-quality PCBs.
-
Provide clear and accurate design files: The design files provided to the PCB manufacturer must be clear and accurate to ensure that the PCB is manufactured to the correct specifications.
-
Specify the required materials and finishes: The choice of materials and finishes can affect the performance and reliability of the PCB. It is essential to specify the required materials and finishes to the PCB manufacturer.
-
Consider lead times: PCB fabrication can have varying lead times depending on the complexity of the design and the workload of the manufacturer. It is essential to consider lead times when planning the production schedule.
Step 4: PCB Assembly
After PCB fabrication, the next step is PCB assembly. This involves the placement and soldering of components onto the PCB. PCB assembly can be done manually or using automated equipment, depending on the complexity of the design and the volume of production.
Manual PCB Assembly
Manual PCB assembly involves the placement and soldering of components onto the PCB by hand. This method is suitable for low-volume production or prototypes. Manual PCB assembly requires skilled technicians who can handle small components and perform precise soldering.
Automated PCB Assembly
Automated PCB assembly involves the use of machines to place and solder components onto the PCB. This method is suitable for high-volume production and complex designs. Automated PCB assembly offers several advantages, including:
- Increased speed and efficiency
- Improved accuracy and consistency
- Reduced labor costs
- Ability to handle smaller components
Tips for PCB Assembly
-
Use a pick-and-place machine: A pick-and-place machine automates the placement of components onto the PCB, improving speed and accuracy.
-
Use solder paste: Solder paste is a mixture of solder particles and flux that is applied to the PCB before component placement. It helps to hold the components in place and ensures a good solder joint.
-
Use a reflow oven: A reflow oven is used to melt the solder paste and create a permanent solder joint between the components and the PCB.
-
Perform visual inspection: After PCB assembly, it is essential to perform a visual inspection to ensure that all components are placed correctly and that there are no visible defects.
Step 5: PCB Testing
The final step in the PCB assembly process is PCB testing. This involves testing the assembled PCB to ensure that it functions as intended and meets the required specifications. PCB testing can be done at various stages of the assembly process, including:
-
In-circuit testing: This involves testing the PCB while it is still in the assembly process to identify any defects or issues.
-
Functional testing: This involves testing the assembled PCB to ensure that it performs the intended functions correctly.
-
Boundary scan testing: This involves testing the interconnections between components on the PCB to identify any open or short circuits.
-
Environmental testing: This involves testing the PCB under various environmental conditions, such as temperature, humidity, and vibration, to ensure that it can withstand the intended operating conditions.
Tips for PCB Testing
-
Use automated testing equipment: Automated testing equipment, such as in-circuit testers and flying probe testers, can quickly and accurately test the PCB for defects and issues.
-
Develop a comprehensive test plan: It is essential to develop a comprehensive test plan that covers all aspects of the PCB’s functionality and performance.
-
Use statistical process control: Statistical process control (SPC) can be used to monitor the PCB assembly process and identify any trends or issues that may affect quality.
-
Perform root cause analysis: If any issues are identified during PCB testing, it is essential to perform a root cause analysis to identify the underlying cause and implement corrective actions.
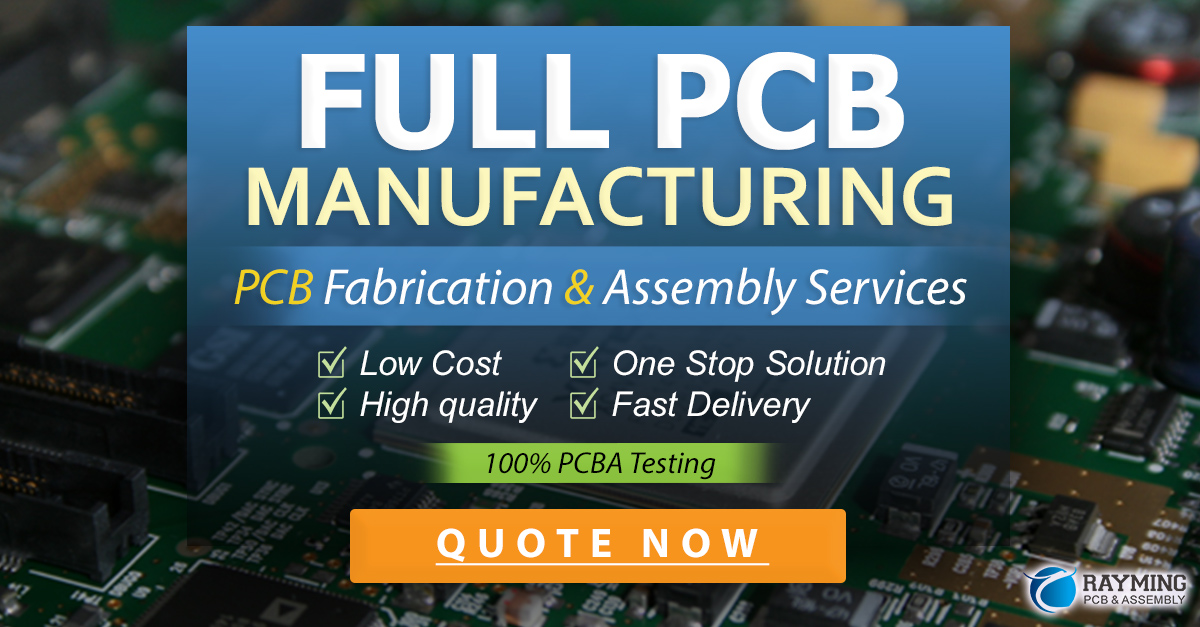
Common PCB Assembly Defects and How to Avoid Them
Despite the best efforts of PCB designers and manufacturers, defects can still occur during the PCB assembly process. Some common PCB assembly defects include:
-
Solder bridges: This occurs when solder inadvertently connects two or more components or traces that should not be connected.
-
Cold solder joints: This occurs when the solder joint is not heated sufficiently, resulting in a weak or unreliable connection.
-
Component misalignment: This occurs when components are not placed correctly on the PCB, resulting in poor connections or short circuits.
-
Tombstoning: This occurs when a component lifts off the PCB during the soldering process, resulting in an open circuit.
To avoid these defects, it is essential to follow best practices for PCB design, component selection, and PCB assembly. Some tips to avoid common PCB assembly defects include:
-
Use a solder mask: A solder mask helps to prevent solder bridges by covering the areas of the PCB that should not be soldered.
-
Use a temperature profile: A temperature profile ensures that the solder joint is heated to the correct temperature for the correct amount of time, preventing cold solder joints.
-
Use a vision system: A vision system can detect component misalignment and other defects during the assembly process, allowing for corrective action to be taken.
-
Use a reflow profile: A reflow profile ensures that the solder paste is heated and cooled at the correct rates to prevent tombstoning and other defects.
FAQ
-
What is PCB assembly?
PCB assembly is the process of placing and soldering components onto a printed circuit board (PCB) to create a functional electronic device. -
What are the steps involved in PCB assembly?
The steps involved in PCB assembly include PCB design and layout, component selection, PCB fabrication, PCB assembly, and PCB testing. -
What are some common PCB assembly defects?
Some common PCB assembly defects include solder bridges, cold solder joints, component misalignment, and tombstoning. -
How can I avoid PCB assembly defects?
To avoid PCB assembly defects, it is essential to follow best practices for PCB design, component selection, and PCB assembly, such as using a solder mask, temperature profile, vision system, and reflow profile. -
What is the difference between manual and automated PCB assembly?
Manual PCB assembly involves the placement and soldering of components onto the PCB by hand, while automated PCB assembly involves the use of machines to place and solder components onto the PCB. Automated PCB assembly is suitable for high-volume production and complex designs, while manual PCB assembly is suitable for low-volume production or prototypes.
Conclusion
PCB assembly is a critical process in the manufacturing of electronic devices. The success of a PCB assembly project depends on several factors, including the design of the PCB, the selection of components, and the assembly process itself. By following best practices for PCB design, component selection, and PCB assembly, manufacturers can ensure that their PCBs are reliable, functional, and cost-effective.
Some key considerations for successful PCB assembly include:
- Using reputable suppliers for high-quality components
- Following design rules and considering manufacturability during PCB layout
- Choosing a reputable PCB manufacturer with a proven track record
- Using automated equipment for high-volume production and complex designs
- Performing comprehensive testing to ensure functionality and reliability
By following these steps and best practices, manufacturers can streamline their PCB assembly process, reduce defects and issues, and ultimately create high-quality electronic devices that meet the needs of their customers.
Leave a Reply