Introduction to Solder Paste Basics
Solder paste is a critical component in surface mount technology (SMT) that enables the attachment of surface mount components to printed circuit boards (PCBs). It is a mixture of tiny solder particles suspended in a flux medium, which helps to clean and protect the metal surfaces during the soldering process. Understanding the basics of solder paste is essential for achieving high-quality and reliable solder joints in SMT assembly.
What is Solder Paste?
Solder paste is a gray, paste-like material that consists of tiny solder alloy particles (typically tin, lead, and silver) suspended in a thick flux medium. The solder particles are usually spherical in shape and range in size from 25 to 45 microns. The flux medium is a complex mixture of chemicals that serves several important functions:
- Cleaning the metal surfaces of oxides and contaminants
- Protecting the metal surfaces from oxidation during the soldering process
- Promoting the wetting and spreading of the molten solder on the metal surfaces
- Helping to hold the components in place before soldering
Types of Solder Paste
There are two main types of solder paste used in SMT assembly:
- Lead-based solder paste
- Contains a tin-lead alloy (typically Sn63Pb37)
- Has a lower melting point (183°C) compared to lead-free solder
- Easier to work with and less prone to defects
-
Restricted in many countries due to environmental and health concerns
-
Lead-free solder paste
- Contains a tin-silver-copper alloy (typically SAC305: Sn96.5Ag3.0Cu0.5)
- Has a higher melting point (217-220°C) compared to lead-based solder
- More difficult to work with and prone to defects
- Required for RoHS (Restriction of Hazardous Substances) compliance
Solder Paste Composition
The composition of solder paste is critical to its performance in SMT assembly. The main components are:
- Solder alloy particles
- Make up 85-90% of the solder paste by weight
- Determine the melting point, wetting behavior, and mechanical properties of the solder joint
-
Common alloys include Sn63Pb37, SAC305, and Sn96.5Ag3.5
-
Flux medium
- Makes up 10-15% of the solder paste by weight
- Contains activators, solvents, rheological modifiers, and other additives
- Determines the printing, slumping, and tack properties of the solder paste
- Classified into four types based on the activator: rosin (RO), resin (RE), organic (OR), and inorganic (IN)
Solder Paste Properties
The key properties of solder paste that affect its performance in SMT assembly are:
- Viscosity
- Determines the flow behavior and printability of the solder paste
- Affected by the particle size, shape, and distribution, as well as the flux composition
-
Typically ranges from 100,000 to 1,000,000 centipoise (cP)
-
Thixotropy
- Describes the shear-thinning behavior of the solder paste
- Allows the solder paste to flow easily under shear stress (during printing) but maintain its shape after deposition
-
Prevents slumping and bridging of the solder paste
-
Tack
- Refers to the ability of the solder paste to hold components in place before soldering
- Depends on the flux composition and the surface area of the solder particles
-
Decreases over time as the solder paste dries out
-
Slump
- Describes the tendency of the solder paste to spread or flow after deposition
- Affected by the particle size, shape, and distribution, as well as the flux composition
-
Can cause bridging or short circuits if excessive
-
Stencil life
- Refers to the amount of time the solder paste can be left on the stencil before it dries out or loses its printability
- Depends on the flux composition, the printing environment, and the stencil design
- Typically ranges from 4 to 8 hours
Solder Paste Storage and Handling
Proper storage and handling of solder paste are critical to maintaining its quality and performance. Some key guidelines include:
- Store solder paste in a refrigerator at 0-10°C (32-50°F) to prevent drying and oxidation
- Allow solder paste to reach room temperature (20-25°C) before use to ensure proper viscosity and printability
- Stir or mix solder paste thoroughly before use to ensure homogeneity and prevent separation of the solder particles and flux
- Use solder paste within its shelf life (typically 6-12 months) to avoid degradation of its properties
- Avoid contamination of solder paste with dust, dirt, or other materials that can affect its performance
Solder Paste Printing Process
The solder paste printing process is the first and most critical step in SMT assembly. It involves the following steps:
- Stencil design
- Create a stencil with apertures that match the size and shape of the solder pads on the PCB
-
Choose the appropriate stencil thickness (typically 100-150 microns) based on the component pitch and solder paste volume requirements
-
Stencil alignment
- Align the stencil with the PCB using fiducial marks or vision systems
-
Ensure proper contact between the stencil and PCB to prevent paste smearing or bridging
-
Solder paste deposition
- Apply solder paste to the stencil using a squeegee or blade
- Use a consistent pressure and speed to ensure uniform deposition of the solder paste
-
Inspect the printed solder paste for defects such as bridging, insufficient volume, or poor shape definition
-
Stencil cleaning
- Clean the stencil periodically to remove excess solder paste and prevent clogging of the apertures
- Use a compatible solvent and cleaning method (manual or automatic) based on the solder paste and stencil type
Solder Paste Inspection Methods
Solder paste inspection (SPI) is an important quality control step in SMT assembly that helps to identify and correct printing defects before component placement and reflow. There are two main types of SPI methods:
- 2D SPI
- Uses a camera to capture a top-down image of the printed solder paste
- Measures the area, shape, and position of the solder paste deposits
- Can detect defects such as bridging, insufficient volume, or misalignment
-
Limited in its ability to measure the height or volume of the solder paste
-
3D SPI
- Uses a laser or structured light to capture a 3D profile of the printed solder paste
- Measures the height, volume, and shape of the solder paste deposits
- Can detect defects such as insufficient volume, poor shape definition, or voids
- Provides more accurate and comprehensive data compared to 2D SPI
Solder Paste Reflow Profile
The solder paste reflow profile is a critical factor in achieving high-quality solder joints in SMT assembly. It describes the temperature and time profile that the solder paste undergoes during the reflow process. A typical reflow profile consists of four stages:
- Preheat
- Gradually raises the temperature of the PCB and components to activate the flux and remove volatiles
- Typically ranges from 150-180°C for lead-based solder and 180-200°C for lead-free solder
-
Ramp rate should be controlled to prevent thermal shock or component damage
-
Soak
- Maintains the temperature of the PCB and components to allow the flux to fully activate and the solder particles to coalesce
- Typically ranges from 60-90 seconds for lead-based solder and 90-120 seconds for lead-free solder
-
Temperature should be kept below the melting point of the solder to prevent premature melting
-
Reflow
- Raises the temperature of the PCB and components above the melting point of the solder to allow the solder to wet and spread on the metal surfaces
- Peak temperature should be 20-30°C above the melting point of the solder (typically 210-230°C for lead-based solder and 235-250°C for lead-free solder)
-
Time above liquidus (TAL) should be 60-90 seconds for lead-based solder and 60-120 seconds for lead-free solder
-
Cooling
- Gradually lowers the temperature of the PCB and components to solidify the solder joints
- Ramp rate should be controlled to prevent thermal shock or component damage
- Final temperature should be below 50°C to allow safe handling of the PCB
Common Solder Paste Defects
Despite careful control of the solder paste printing and reflow processes, defects can still occur in SMT assembly. Some common solder paste defects include:
- Insufficient solder
- Caused by low solder paste volume, poor wetting, or solder mask damage
-
Can result in weak or open solder joints
-
Bridging
- Caused by excessive solder paste volume, poor stencil design, or component misalignment
-
Can result in short circuits or poor reliability
-
Solder balls
- Caused by contamination, poor flux activation, or incorrect reflow profile
-
Can cause short circuits or interfere with other components
-
Tombstoning
- Caused by uneven heating, component misalignment, or incorrect pad design
-
Can result in one end of the component lifting off the PCB
-
Head-in-pillow
- Caused by poor wetting, oxide formation, or incorrect reflow profile
- Can result in weak or open solder joints
Troubleshooting Solder Paste Issues
When solder paste defects occur, it is important to identify the root cause and take corrective action to prevent further issues. Some troubleshooting steps include:
- Check the solder paste
- Ensure that the solder paste is within its shelf life and has been stored and handled properly
-
Verify that the solder paste composition and properties are suitable for the application
-
Check the stencil
- Ensure that the stencil is clean, undamaged, and properly aligned with the PCB
-
Verify that the stencil apertures are the correct size and shape for the solder pads
-
Check the printing process
- Ensure that the squeegee pressure, speed, and angle are consistent and appropriate for the solder paste and stencil
-
Verify that the PCB and stencil are properly supported and gasketed to prevent paste smearing or bridging
-
Check the reflow profile
- Ensure that the reflow profile is optimized for the solder paste and PCB design
-
Verify that the peak temperature, time above liquidus, and ramp rates are within the recommended ranges
-
Check the components
- Ensure that the components are clean, undamaged, and properly oriented on the PCB
- Verify that the component leads are properly aligned with the solder pads and not bent or twisted
Frequently Asked Questions (FAQ)
1. What is the shelf life of solder paste?
The shelf life of solder paste depends on the specific formulation and storage conditions, but is typically 6-12 months when stored at 0-10°C (32-50°F) in an unopened container. Once opened, the shelf life is reduced to 1-3 months depending on the frequency of use and exposure to air and moisture.
2. Can solder paste be reused?
Solder paste should not be reused once it has been printed onto a stencil or PCB. The solder particles and flux can become contaminated or degraded during the printing process, which can affect the quality and reliability of the solder joints. Excess solder paste should be discarded according to local regulations.
3. What is the difference between no-clean and water-soluble solder paste?
No-clean solder paste contains a flux that leaves a minimal, non-conductive residue after reflow that does not require cleaning. This type of solder paste is commonly used in applications where cleaning is difficult or impractical.
Water-soluble solder paste contains a flux that leaves a conductive residue after reflow that must be cleaned with water or a mild solvent. This type of solder paste is used in applications where high cleanliness and reliability are required, such as military or aerospace electronics.
4. How do you determine the appropriate solder paste volume for a given component?
The appropriate solder paste volume for a given component depends on several factors, including the size and shape of the component leads, the size and shape of the solder pads, and the desired solder joint profile. As a general rule, the solder paste volume should be 50-75% of the total volume of the solder pad and component lead.
There are several methods for calculating the solder paste volume, including:
- Using a solder paste volume calculator or software
- Using a stencil thickness and aperture size formula (e.g., area ratio or transfer efficiency)
- Measuring the actual solder paste volume using 3D SPI or cross-sectioning
5. What are some best practices for handling and storing solder paste?
Some best practices for handling and storing solder paste include:
- Store solder paste in a refrigerator at 0-10°C (32-50°F) in an unopened container
- Allow solder paste to reach room temperature (20-25°C) for at least 2 hours before use
- Stir or mix solder paste thoroughly before use to ensure homogeneity and prevent separation of the solder particles and flux
- Use solder paste within its shelf life and discard any expired or contaminated solder paste
- Avoid exposing solder paste to excessive heat, humidity, or light, which can degrade its properties
- Use clean, lint-free gloves or tools when handling solder paste to prevent contamination
- Clean and maintain solder paste printing equipment regularly to ensure consistent and accurate deposition
Conclusion
Solder paste is a critical material in surface mount technology that enables the attachment of surface mount components to printed circuit boards. Understanding the basics of solder paste, including its composition, properties, and printing and reflow processes, is essential for achieving high-quality and reliable solder joints in SMT assembly.
By following best practices for handling, storing, and using solder paste, and by implementing effective quality control measures such as solder paste inspection and reflow profiling, manufacturers can minimize defects and ensure the long-term performance of their electronic assemblies.
As technology continues to advance and electronic devices become smaller and more complex, the importance of solder paste in SMT will only continue to grow. By staying up-to-date with the latest developments and techniques in solder paste technology, manufacturers can remain competitive and meet the ever-increasing demands of the electronics industry.
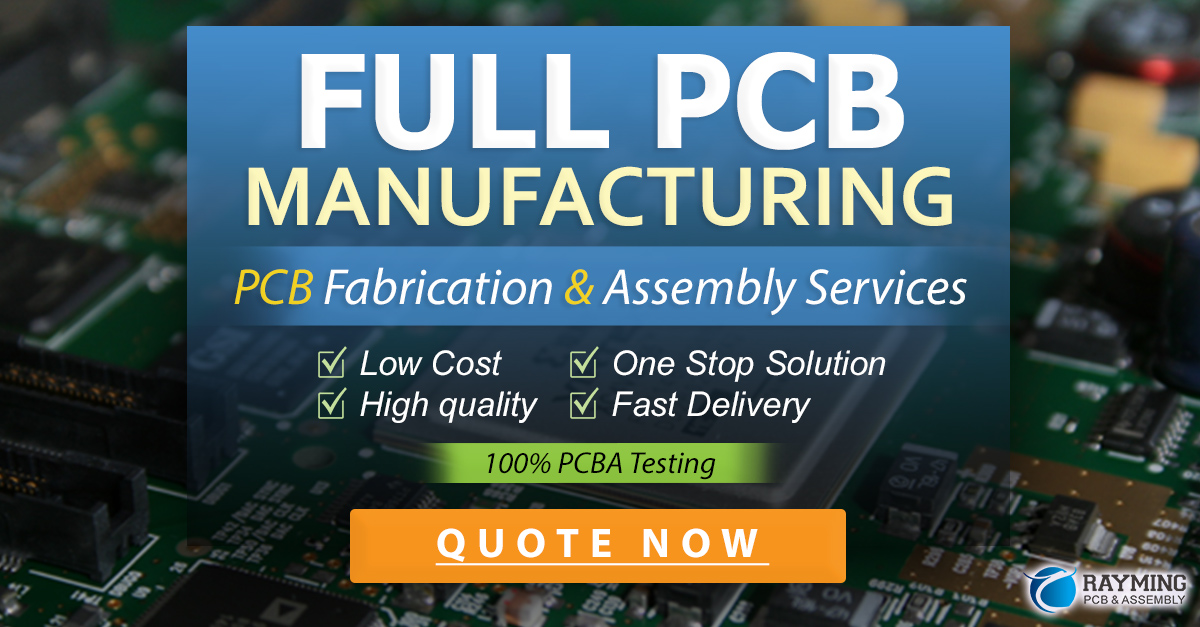
Leave a Reply