What is Solder wicking?
Solder wicking, also known as capillary action, is the tendency of molten solder to travel up the leads of connectors or component pins due to the surface tension of the liquid solder and the small spaces between the leads. When the solder is heated to its melting point, it becomes a liquid with a high surface tension. This surface tension causes the molten solder to be drawn into small gaps and spaces, such as those found between the strands of a stranded wire or the leads of a connector.
Factors Affecting Solder Wicking
Several factors can influence the occurrence and extent of solder wicking:
-
Temperature: Higher soldering temperatures can increase the likelihood of solder wicking, as the molten solder becomes less viscous and more prone to capillary action.
-
Soldering time: Prolonged exposure to heat can cause more solder to be drawn up the leads, exacerbating the wicking effect.
-
Lead spacing: Closely spaced leads or pins create smaller gaps, which can promote solder wicking due to increased capillary action.
-
Solder composition: Different solder alloys have varying surface tensions and flow characteristics, which can affect their tendency to wick.
-
Surface cleanliness: Contamination or oxidation on the leads or pins can hinder the flow of solder and contribute to wicking.
Effects of Solder Wicking
Solder wicking can have several negative effects on the soldering process and the resulting electrical connections:
-
Short circuits: When solder wicks up the leads of adjacent pins or connectors, it can create unintended electrical connections, leading to short circuits and device malfunction.
-
Poor connections: Excessive solder wicking can result in a lack of solder at the intended joint, weakening the electrical and mechanical connection.
-
Difficulty in component removal: Solder that has wicked up the leads of a component can make it challenging to remove the component without damaging the board or the component itself.
-
Aesthetic issues: Solder wicking can create an unsightly appearance, with solder extending beyond the intended joint area.
Techniques to Prevent Solder Wicking
To minimize the occurrence of solder wicking and its associated problems, several techniques can be employed:
1. Temperature Control
Maintaining the appropriate soldering temperature is crucial in preventing excessive solder wicking. The ideal temperature range for most soldering applications is between 300°C and 350°C (572°F to 662°F). Temperatures higher than this can cause the solder to become too fluid, increasing the likelihood of wicking.
Solder Alloy | Melting Point Range |
---|---|
Lead-based (Sn63/Pb37) | 183°C – 190°C |
Lead-free (Sn96.5/Ag3.0/Cu0.5) | 217°C – 220°C |
2. Soldering Time Reduction
Minimizing the time the soldering iron is in contact with the joint can help reduce solder wicking. Prolonged exposure to heat allows more time for the molten solder to be drawn up the leads. To achieve a good solder joint while minimizing wicking, follow these steps:
- Preheat the joint area using the soldering iron tip.
- Apply the solder to the joint quickly and efficiently.
- Remove the soldering iron as soon as a good joint is formed.
3. Lead Spacing and Design Considerations
When designing circuit boards or selecting components, consider the spacing between leads or pins. Wider lead spacing can help reduce the likelihood of solder wicking by decreasing the capillary action between adjacent leads. If possible, choose components with adequate lead spacing or design the board layout to accommodate wider spacing.
4. Solder Selection
The choice of solder alloy can impact the occurrence of solder wicking. Lead-free solders, such as Sn96.5/Ag3.0/Cu0.5 (SAC305), have higher surface tensions compared to lead-based solders, making them more prone to wicking. When possible, select a solder alloy with a lower surface tension to minimize wicking. However, it is essential to consider other factors such as compatibility with the components and adherence to environmental regulations when choosing a solder alloy.
5. Surface Preparation and Cleanliness
Ensuring the cleanliness of the leads and pins before soldering can help reduce solder wicking. Contamination, oxidation, or residues on the surface can hinder the flow of solder and contribute to wicking. To prepare the surfaces for soldering:
- Clean the leads and pins with isopropyl alcohol or a suitable solvent to remove any dirt or oils.
- Use a fine abrasive, such as a fiberglass brush or solder tip cleaner, to remove any oxidation or stubborn residues.
- Apply a small amount of flux to the joint area to promote solder flow and prevent re-oxidation during soldering.
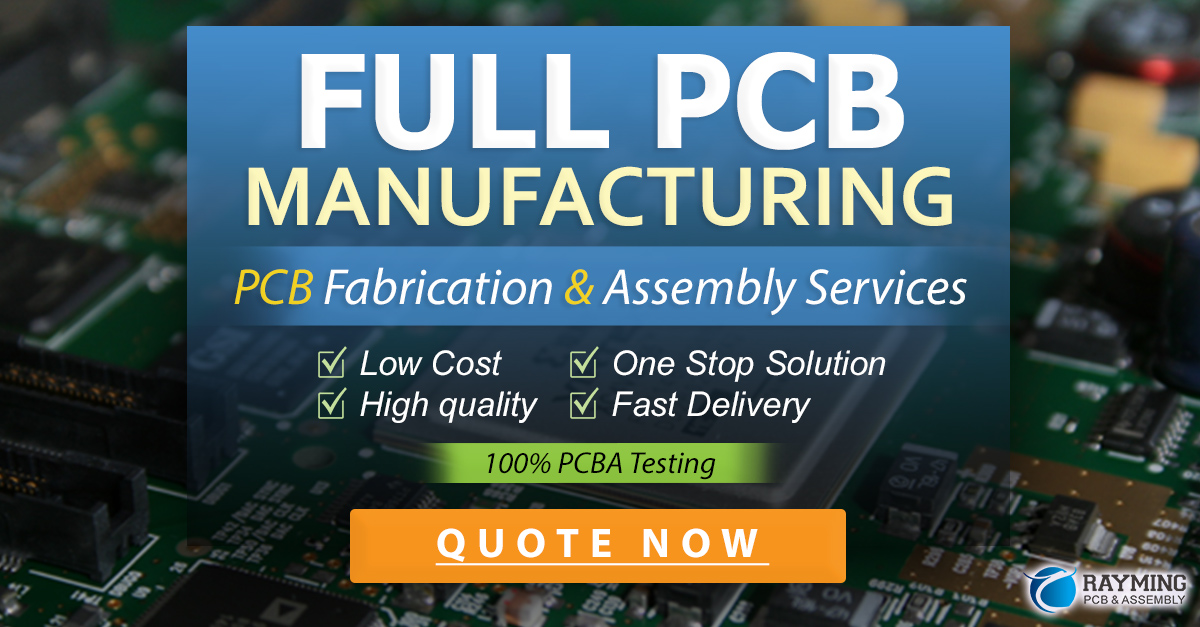
Dealing with Solder Wicking
Despite taking preventive measures, solder wicking may still occur in some instances. In such cases, the following techniques can be used to address the issue:
1. Desoldering and Rework
If solder wicking has caused short circuits or poor connections, the affected joints may need to be desoldered and reworked. Desoldering can be performed using a desoldering pump, solder wick, or a specialized desoldering station. Once the excess solder is removed, the joint can be resoldered using the appropriate techniques to minimize wicking.
2. Solder Wick Removal
Solder wick, also known as desoldering braid, can be used to remove excess solder from wicked leads. To use solder wick:
- Place the solder wick over the affected area.
- Apply the soldering iron tip to the wick, allowing it to heat up and absorb the excess solder.
- Move the wick along the wicked leads to remove the solder gradually.
- Trim off the used portion of the wick and repeat the process if necessary.
3. Mechanical Removal
In some cases, excess solder can be removed mechanically using tweezers, pliers, or a knife. However, this method should be used with caution to avoid damaging the leads or the circuit board. It is essential to ensure that the solder has cooled and solidified before attempting mechanical removal.
Frequently Asked Questions (FAQ)
-
What is solder wicking, and why does it occur?
Solder wicking, also known as capillary action, is the tendency of molten solder to travel up the leads of connectors or component pins due to the surface tension of the liquid solder and the small spaces between the leads. It occurs when the solder is heated to its melting point, and the surface tension causes the molten solder to be drawn into small gaps and spaces. -
What are the negative effects of solder wicking?
Solder wicking can cause several problems, including short circuits, poor connections, difficulty in removing components, and aesthetic issues. Short circuits can occur when solder wicks up the leads of adjacent pins or connectors, creating unintended electrical connections. Poor connections can result from excessive solder wicking, leaving insufficient solder at the intended joint. Solder wicking can also make it challenging to remove components without damaging the board or the component itself. -
How can I prevent solder wicking?
To prevent or minimize solder wicking, you can employ several techniques, such as temperature control, soldering time reduction, lead spacing and design considerations, solder selection, and surface preparation and cleanliness. Maintaining the appropriate soldering temperature, minimizing soldering time, ensuring adequate lead spacing, choosing a suitable solder alloy, and cleaning the surfaces before soldering can all help reduce the occurrence of solder wicking. -
What should I do if solder wicking has already occurred?
If solder wicking has caused issues like short circuits or poor connections, you may need to desolder and rework the affected joints. Desoldering can be done using a desoldering pump, solder wick, or a specialized desoldering station. Solder wick can also be used to remove excess solder from wicked leads by heating the wick with a soldering iron and allowing it to absorb the solder. In some cases, mechanical removal using tweezers, pliers, or a knife may be possible, but caution should be exercised to avoid damaging the leads or the circuit board. -
Can the choice of solder alloy affect the likelihood of solder wicking?
Yes, the choice of solder alloy can impact the occurrence of solder wicking. Lead-free solders, such as Sn96.5/Ag3.0/Cu0.5 (SAC305), have higher surface tensions compared to lead-based solders, making them more prone to wicking. When possible, selecting a solder alloy with a lower surface tension can help minimize wicking. However, it is essential to consider other factors such as compatibility with the components and adherence to environmental regulations when choosing a solder alloy.
Conclusion
Solder wicking is a common issue in the soldering process, where molten solder travels up the leads of connectors or component pins due to capillary action. It can cause problems such as short circuits, poor connections, and difficulty in removing components. By understanding the causes and effects of solder wicking, and employing various techniques to prevent or minimize its occurrence, you can improve the quality and reliability of your soldered joints.
Temperature control, soldering time reduction, lead spacing considerations, solder selection, and surface cleanliness are all essential factors in preventing solder wicking. If wicking does occur, desoldering and rework, solder wick removal, or mechanical removal can be used to address the issue.
By following best practices and being mindful of the potential for solder wicking, you can ensure that your soldered connections are strong, reliable, and free from the problems associated with this phenomenon. As with any soldering task, practice, patience, and attention to detail are key to achieving the best results.
Leave a Reply