What is Solder?
Solder is a fusible metal alloy with a melting point below 450°C (840°F). It is used to join two or more metal surfaces together by melting and flowing into the joint, creating a strong, electrically conductive bond upon cooling. The most common types of solder are lead-based and lead-free alloys, which are composed of varying proportions of metals such as tin, lead, silver, copper, and bismuth.
The Importance of Solder Classification
Classifying solder is essential for several reasons:
- Ensuring the right solder is used for a specific application
- Maintaining the quality and reliability of the soldered joint
- Complying with environmental and health regulations
- Optimizing the soldering process and equipment
By understanding the different types of solder and their properties, engineers, technicians, and hobbyists can make informed decisions when selecting the appropriate solder for their projects.
Solder Classification Based on Composition
Solder can be classified based on its composition, which determines its melting point, wetting ability, mechanical strength, and other properties. The two main categories of solder based on composition are lead-based and lead-free solders.
Lead-Based Solders
Lead-based solders have been widely used for decades due to their excellent wetting properties, low melting points, and good mechanical strength. The most common lead-based solder is the tin-lead (Sn-Pb) alloy, which typically contains 60% tin and 40% lead (60/40) or 63% tin and 37% lead (63/37).
Advantages of Lead-Based Solders
- Low melting point (183°C for 63/37)
- Excellent wetting properties
- Good mechanical strength
- Easy to work with
Disadvantages of Lead-Based Solders
- Toxicity of lead
- Environmental concerns
- Restricted use due to regulations (e.g., RoHS, WEEE)
Lead-Free Solders
Due to the toxicity of lead and environmental concerns, lead-free solders have gained popularity in recent years. These solders are composed of various combinations of metals, such as tin, silver, copper, bismuth, and indium.
Common Lead-Free Solder Alloys
-
Tin-Silver-Copper (SAC): SAC305 (96.5% Sn, 3% Ag, 0.5% Cu) is a widely used lead-free solder alloy. It has a melting point of 217-220°C and offers good mechanical strength and reliability.
-
Tin-Copper (Sn-Cu): Alloys such as Sn99.3Cu0.7 and Sn100C are cost-effective alternatives to SAC solders. They have melting points around 227°C and provide adequate wetting and mechanical properties.
-
Tin-Bismuth (Sn-Bi): Low-melting-point alloys like Sn42Bi58 (138°C) and Sn57Bi43 (139°C) are used for temperature-sensitive applications or step soldering processes.
-
Tin-Silver (Sn-Ag): Alloys such as Sn96.5Ag3.5 have melting points around 221°C and offer good wetting and mechanical properties, but are more expensive than SAC solders.
Advantages of Lead-Free Solders
- Non-toxic and environmentally friendly
- Compliance with regulations (RoHS, WEEE)
- Higher melting points can provide better thermal stability
Disadvantages of Lead-Free Solders
- Higher melting points require higher soldering temperatures
- May have poorer wetting properties compared to lead-based solders
- Some alloys can be more expensive (e.g., high-silver SAC alloys)
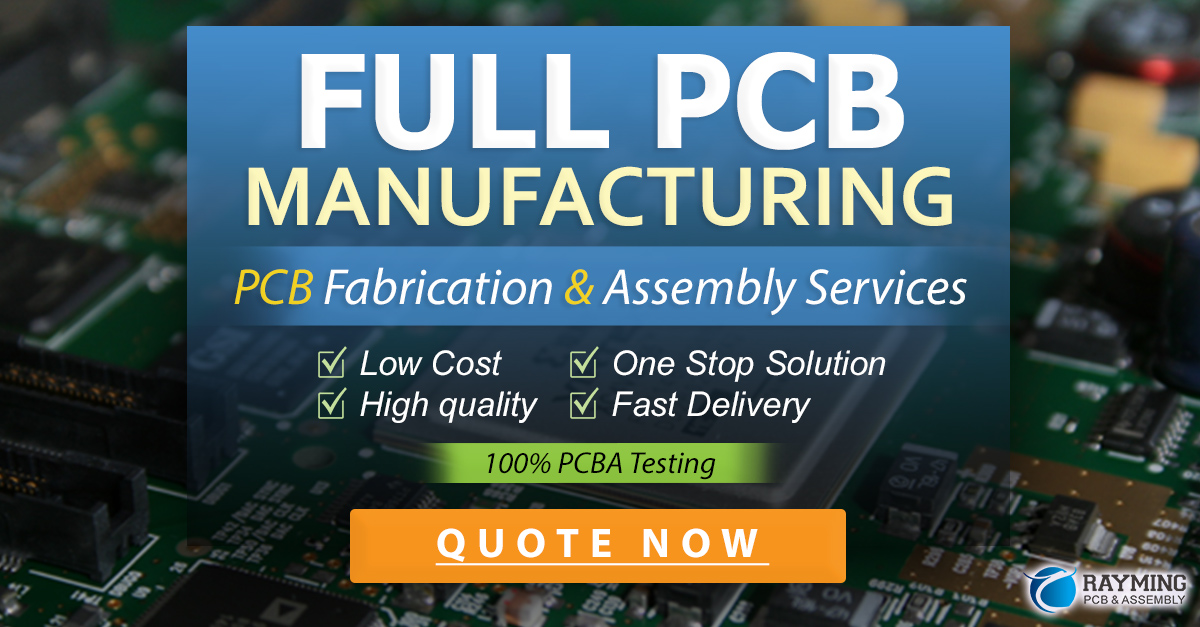
Solder Classification Based on Form
Solder is available in various forms to accommodate different soldering techniques and applications. The most common forms of solder are wire, bar, paste, and preforms.
Solder Wire
Solder wire is the most widely used form of solder, consisting of a wire-shaped alloy with a flux core. The flux helps to remove oxides and improve wetting during the soldering process. Solder wire is available in different diameters, alloy compositions, and flux types (e.g., rosin, no-clean, water-soluble).
Advantages of Solder Wire
- Convenient and easy to use
- Suitable for hand soldering and rework
- Flux core promotes good wetting and joint quality
Disadvantages of Solder Wire
- Not suitable for automated soldering processes
- Limited control over the amount of solder applied
Solder Bar
Solder bars are solid pieces of solder alloy, typically used in wave soldering machines or for creating custom solder alloys. They are available in various alloy compositions and sizes.
Advantages of Solder Bar
- Suitable for automated wave soldering processes
- Can be used to create custom solder alloys
- Economical for large-scale soldering operations
Disadvantages of Solder Bar
- Requires additional equipment (e.g., wave soldering machine)
- Not suitable for hand soldering or rework
Solder Paste
Solder paste is a mixture of fine solder particles suspended in a flux medium. It is commonly used in surface mount technology (SMT) for reflow soldering processes. Solder paste is applied to the PCB using stencil printing or dispensing methods.
Advantages of Solder Paste
- Enables precise control over the amount of solder applied
- Suitable for automated SMT assembly processes
- Provides good wetting and joint quality
Disadvantages of Solder Paste
- Requires specialized equipment for application and reflow
- Limited shelf life and storage requirements
- Not suitable for hand soldering or rework
Solder Preforms
Solder preforms are pre-shaped pieces of solder alloy, available in various geometries such as rings, discs, and washers. They are used for specific applications where precise amounts of solder are required, such as die-attach or hermetic sealing.
Advantages of Solder Preforms
- Precise control over the amount of solder applied
- Consistent and repeatable solder joint quality
- Suitable for automated assembly processes
Disadvantages of Solder Preforms
- Higher cost compared to other solder forms
- Limited flexibility in terms of alloy composition and geometry
- Not suitable for general-purpose soldering applications
Solder Classification Based on Flux Type
Flux is a chemical compound that helps to remove oxides, prevent reoxidation, and improve the wetting properties of the solder during the soldering process. Solder can be classified based on the type of flux used, which can be either incorporated within the solder (e.g., flux-cored wire) or applied separately.
Rosin Flux
Rosin flux is a natural or synthetic resin-based flux that is commonly used in electronics soldering. It is available in various activity levels, such as mildly activated (RMA), fully activated (RA), and water-soluble (WS) formulations.
Advantages of Rosin Flux
- Provides good wetting and oxide removal
- Leaves a protective residue that can be left on the PCB
- Available in no-clean formulations that minimize post-soldering cleaning
Disadvantages of Rosin Flux
- Rosin residue can be difficult to remove if cleaning is required
- Some activated formulations may cause corrosion if not properly cleaned
Water-Soluble Flux
Water-soluble flux is a type of flux that can be easily removed using water or aqueous cleaning solutions after soldering. It is commonly used in applications where post-soldering cleaning is required, such as high-reliability electronics or medical devices.
Advantages of Water-Soluble Flux
- Easy to remove using water or aqueous cleaning solutions
- Provides good wetting and oxide removal
- Suitable for applications requiring post-soldering cleaning
Disadvantages of Water-Soluble Flux
- Requires post-soldering cleaning, which can add to processing time and costs
- May cause corrosion if not completely removed
No-Clean Flux
No-clean flux is a type of flux that leaves minimal, non-corrosive residue after soldering, eliminating the need for post-soldering cleaning. It is widely used in electronics assembly for cost-effective and efficient production.
Advantages of No-Clean Flux
- Eliminates the need for post-soldering cleaning
- Reduces processing time and costs
- Leaves a minimal, non-corrosive residue
Disadvantages of No-Clean Flux
- May not provide as much oxide removal as activated fluxes
- Some no-clean flux residues may interfere with electrical testing or coating processes
Solder Selection Considerations
When selecting the appropriate solder for a specific application, several factors should be considered:
-
Soldering temperature: Choose a solder with a melting point suitable for the components and substrate materials being soldered.
-
Mechanical properties: Consider the required strength, ductility, and fatigue resistance of the solder joint.
-
Electrical conductivity: Ensure the solder provides adequate electrical conductivity for the application.
-
Environmental and health regulations: Select a solder that complies with relevant regulations, such as RoHS and WEEE.
-
Soldering process: Choose a solder form and flux type that is compatible with the intended soldering process (e.g., hand soldering, wave soldering, reflow soldering).
-
Cost: Consider the cost of the solder alloy and its impact on the overall production costs.
Frequently Asked Questions (FAQ)
-
Q: What is the most common lead-based solder alloy?
A: The most common lead-based solder alloy is tin-lead (Sn-Pb), typically in the proportions of 60% tin and 40% lead (60/40) or 63% tin and 37% lead (63/37). -
Q: Why are lead-free solders becoming more popular?
A: Lead-free solders are becoming more popular due to the toxicity of lead and environmental concerns. Regulations such as RoHS and WEEE have restricted the use of lead in electronics, driving the adoption of lead-free alternatives. -
Q: What is the role of flux in soldering?
A: Flux helps to remove oxides from the metal surfaces, prevent reoxidation during soldering, and improve the wetting properties of the solder. This ensures a strong, reliable solder joint. -
Q: Can lead-free solders directly replace lead-based solders in all applications?
A: Lead-free solders cannot always directly replace lead-based solders due to differences in melting points, wetting properties, and mechanical characteristics. The soldering process and equipment may need to be adjusted to accommodate lead-free solders. -
Q: How do I choose the right solder for my application?
A: When selecting a solder, consider factors such as the soldering temperature, required mechanical and electrical properties, environmental regulations, soldering process, and cost. Consult with solder manufacturers or experienced professionals for guidance on choosing the most suitable solder for your specific application.
Conclusion
Solder classification is essential for understanding the properties and applications of different solder types. By considering factors such as composition, form, and flux type, engineers, technicians, and hobbyists can select the most appropriate solder for their specific needs. As environmental regulations and technological advancements continue to shape the soldering industry, staying informed about solder classifications and their implications will be crucial for ensuring the quality, reliability, and sustainability of soldered joints in various applications.
Leave a Reply