What is an SMT Stencil?
An SMT stencil, also known as a solder paste stencil, is a thin sheet of metal or other material with precisely cut openings that correspond to the pads on a printed circuit board (PCB). The stencil is used to apply solder paste onto the PCB pads before placing the surface mount components. The openings in the stencil ensure that the correct amount of solder paste is deposited on each pad, leading to a consistent and reliable solder joint after reflow.
Types of SMT Stencils
There are several types of SMT stencils available, each with its own unique characteristics and applications:
-
Laser-Cut Stencils: These stencils are created using a high-precision laser cutting process, resulting in clean and accurate openings. Laser-cut stencils are ideal for fine-pitch components and high-density PCB designs.
-
Electroformed Stencils: Electroformed stencils are made by electroplating nickel onto a photoresist-coated master. They offer excellent dimensional accuracy and are suitable for applications requiring very fine features and tight tolerances.
-
Chemical-etched Stencils: Chemical-etched stencils are produced by chemically etching the stencil material, typically stainless steel. They are less expensive than laser-cut or electroformed stencils but may have lower dimensional accuracy and edge quality.
-
Additive Stencils: Additive stencils, also known as nano-coated or E-FAB stencils, are created by selectively depositing a nano-coating onto a laser-cut or electroformed stencil. This process enables the creation of ultra-fine features and improved paste release characteristics.
Importance of SMT Stencils in PCB assembly
SMT stencils play a critical role in the PCB assembly process, and their importance cannot be overstated. Here are some key reasons why SMT stencils are essential:
Precise Solder Paste Deposition
One of the primary functions of an SMT stencil is to ensure that the correct amount of solder paste is deposited on each pad of the PCB. The stencil’s openings are designed to match the size and shape of the pads, allowing for a controlled and consistent application of solder paste. This precision is crucial for achieving reliable solder joints and preventing defects such as bridging, insufficient solder, or excessive solder.
Consistent Solder Joint Quality
By depositing the right amount of solder paste on each pad, SMT stencils contribute to the formation of consistent and high-quality solder joints. This consistency is essential for ensuring the reliability and longevity of the assembled PCB. Poor solder joint quality can lead to issues such as open circuits, short circuits, or intermittent connections, which can cause device failures and customer dissatisfaction.
Improved Manufacturing Efficiency
SMT stencils help streamline the PCB assembly process by enabling the rapid and accurate application of solder paste to multiple PCBs simultaneously. This efficiency is particularly important in high-volume production environments where speed and throughput are critical. By using SMT stencils, manufacturers can reduce cycle times, minimize human error, and increase overall productivity.
Cost Reduction
Investing in high-quality SMT stencils can lead to significant cost savings in the long run. By ensuring precise solder paste deposition and consistent solder joint quality, SMT stencils help reduce the occurrence of defects and rework, which can be costly and time-consuming. Additionally, the improved manufacturing efficiency achieved through the use of SMT stencils can result in lower production costs and increased profitability.
Factors to Consider When Choosing an SMT Stencil
When selecting an SMT stencil for your PCB assembly process, there are several key factors to consider:
Stencil Thickness
The thickness of the SMT stencil is a critical parameter that affects the amount of solder paste deposited on the PCB pads. The stencil thickness should be chosen based on the specific requirements of the PCB design, such as the component pitch, pad size, and solder paste type. Typical stencil thicknesses range from 0.100 mm to 0.150 mm (4 to 6 mils), but thinner or thicker stencils may be used depending on the application.
Aperture Size and Shape
The size and shape of the stencil apertures (openings) should match the size and shape of the PCB pads to ensure optimal solder paste deposition. The aperture design must take into account factors such as the component pitch, pad geometry, and solder paste rheology. Properly designed apertures will promote good paste release and minimize the occurrence of defects such as insufficient or excessive solder.
Stencil Material
SMT stencils can be made from various materials, including stainless steel, nickel, and polyester. Stainless steel is the most common material due to its durability, stability, and compatibility with a wide range of solder pastes. Nickel stencils, such as electroformed stencils, are often used for applications requiring very fine features and tight tolerances. Polyester stencils are less durable but offer advantages such as lower cost and the ability to conform to uneven surfaces.
Stencil Coating
Some SMT stencils are coated with a special material to improve their performance and durability. Common coatings include nano-coatings, which enhance paste release and reduce the occurrence of clogging, and nickel-teflon coatings, which provide a non-stick surface and extend the stencil’s lifespan. The choice of coating will depend on the specific requirements of the application and the solder paste being used.
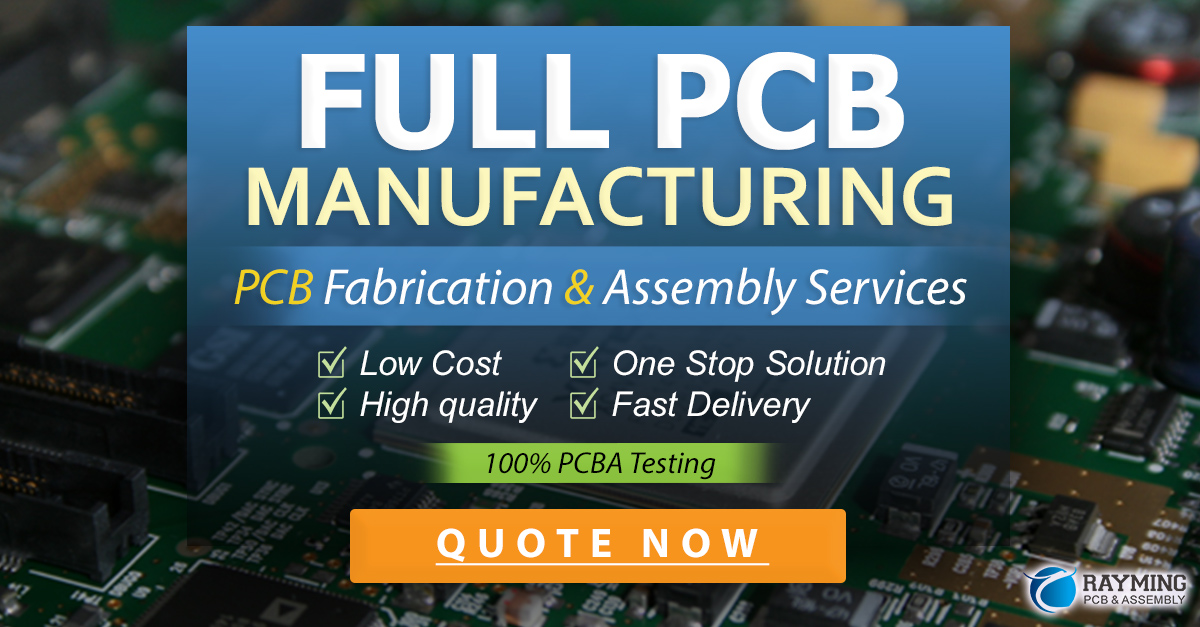
SMT Stencil Maintenance and Handling
To ensure optimal performance and longevity, SMT stencils must be properly maintained and handled. Here are some best practices for stencil maintenance and handling:
Cleaning
Regular cleaning of the SMT stencil is essential to remove solder paste residue and prevent clogging of the apertures. Stencils should be cleaned using a compatible solvent and a soft brush or lint-free cloth. The cleaning process should be performed after every print cycle or as recommended by the stencil manufacturer. Proper cleaning helps maintain print quality and extends the stencil’s lifespan.
Storage
When not in use, SMT stencils should be stored in a clean, dry environment to prevent damage and contamination. Stencils should be stored flat or hung vertically to avoid warping or deformation. It is also important to store stencils away from sources of heat, moisture, or chemical exposure, as these factors can degrade the stencil material or coating.
Handling
SMT stencils should be handled with care to avoid damage or contamination. When handling stencils, operators should wear clean, lint-free gloves to prevent the transfer of oils, dirt, or other contaminants to the stencil surface. Stencils should be grasped by the edges or using a dedicated stencil handle to minimize the risk of damage or warping.
Inspection
Regular inspection of the SMT stencil is important to identify any signs of wear, damage, or contamination. Operators should visually inspect the stencil for defects such as bent or broken apertures, scratches, or excessive solder paste buildup. Any issues should be addressed promptly to maintain print quality and prevent further damage to the stencil or PCB.
Applications of SMT Stencils
SMT stencils are used in a wide range of industries and applications, wherever surface mount technology is employed. Some common applications include:
Consumer Electronics
SMT stencils are extensively used in the production of consumer electronics, such as smartphones, tablets, laptops, and wearables. These devices often require high-density PCB assemblies with fine-pitch components, making the use of SMT stencils essential for achieving the necessary precision and consistency in solder paste deposition.
Automotive Electronics
The automotive industry relies heavily on SMT stencils for the assembly of various electronic components, such as engine control units, infotainment systems, and sensor modules. The harsh operating conditions in automotive environments demand high-quality solder joints and reliable performance, which can be achieved through the use of well-designed SMT stencils.
Medical Devices
Medical devices, such as implantable electronics, diagnostic equipment, and patient monitoring systems, require the highest levels of reliability and performance. SMT stencils play a critical role in ensuring the quality and consistency of solder joints in these devices, helping to minimize the risk of device failure and ensure patient safety.
Aerospace and Defense
SMT stencils are used in the assembly of electronic components for aerospace and defense applications, such as avionics, communication systems, and radar modules. These applications often require specialized stencil designs and materials to meet the stringent reliability and environmental requirements of the industry.
Industrial Electronics
Industrial electronics, such as process control systems, automation equipment, and power electronics, rely on SMT stencils for the precise and consistent application of solder paste. The use of SMT stencils helps ensure the reliability and longevity of these systems in demanding industrial environments.
Frequently Asked Questions (FAQ)
-
Q: What is the difference between laser-cut and electroformed SMT stencils?
A: Laser-cut stencils are created using a high-precision laser cutting process, resulting in clean and accurate openings. Electroformed stencils are made by electroplating nickel onto a photoresist-coated master and offer excellent dimensional accuracy. Laser-cut stencils are more common and suitable for most applications, while electroformed stencils are used for very fine features and tight tolerances. -
Q: How often should I clean my SMT stencil?
A: SMT stencils should be cleaned after every print cycle or as recommended by the stencil manufacturer. Regular cleaning helps remove solder paste residue, prevents clogging of the apertures, and maintains print quality. -
Q: Can I use the same SMT stencil for different solder paste types?
A: It is generally recommended to use a dedicated stencil for each solder paste type to avoid cross-contamination and ensure optimal performance. Different solder pastes may have different rheological properties and require specific stencil designs and coatings for best results. -
Q: How long does an SMT stencil typically last?
A: The lifespan of an SMT stencil depends on various factors, such as the stencil material, coating, usage frequency, and maintenance practices. With proper care and maintenance, a high-quality stencil can last for several thousand print cycles. However, it is important to regularly inspect the stencil for signs of wear or damage and replace it as needed to maintain print quality. -
Q: Can I reuse an SMT stencil after a long period of storage?
A: Before reusing an SMT stencil that has been in storage for an extended period, it is important to thoroughly clean and inspect the stencil. Check for any signs of damage, warping, or contamination, and ensure that the apertures are clear and free of debris. If the stencil is in good condition, it can be reused, but it is always best to test the stencil on a non-critical PCB to verify its performance before using it in production.
Conclusion
In conclusion, SMT stencils are an indispensable tool in the world of surface mount technology, enabling the precise and consistent application of solder paste to PCB pads. By ensuring the quality and reliability of solder joints, SMT stencils contribute to the overall success of PCB assembly processes across various industries, from consumer electronics to aerospace and defense.
When selecting an SMT stencil, it is important to consider factors such as stencil thickness, aperture size and shape, stencil material, and coating to ensure optimal performance for your specific application. Proper maintenance and handling of SMT stencils, including regular cleaning, storage, and inspection, are also crucial for maintaining print quality and extending the stencil’s lifespan.
As the electronics industry continues to evolve, with ever-increasing demands for miniaturization, high-density assemblies, and reliable performance, the role of SMT stencils in enabling these advancements cannot be overstated. By understanding the importance of SMT stencils and implementing best practices in their selection, use, and maintenance, manufacturers can ensure the highest levels of quality, efficiency, and profitability in their PCB assembly processes.
Leave a Reply