Introduction to SMD Welding
Surface Mount Device (SMD) welding, also known as Surface Mount Technology (SMT), is a method of attaching electronic components directly onto the surface of a Printed Circuit Board (PCB). This technology has revolutionized the electronics manufacturing industry by enabling the production of smaller, lighter, and more efficient electronic devices. In this article, we will explore the various aspects of SMD welding, including its advantages, the equipment used, and the process involved.
Advantages of SMD Welding
SMD welding offers several advantages over traditional through-hole technology:
- Miniaturization: SMD components are much smaller than their through-hole counterparts, allowing for more compact and lightweight electronic devices.
- Increased component density: With SMD welding, more components can be placed on a single PCB, resulting in higher functionality and complexity.
- Improved performance: SMD components have shorter lead lengths, reducing parasitic capacitance and inductance, which leads to better high-frequency performance.
- Cost-effectiveness: The automated nature of SMD welding results in faster production times and lower labor costs.
SMD Welding Equipment
To successfully perform SMD welding, several pieces of equipment are essential:
Pick and Place Machine
A pick and place machine is an automated system that accurately places SMD components onto the PCB. These machines use vacuum nozzles or grippers to pick up components from feeders and place them on the pre-programmed locations on the PCB.
Machine Type | Placement Speed (components per hour) | Accuracy (μm) |
---|---|---|
High-speed | 50,000 – 200,000 | ±50 |
Mid-range | 10,000 – 50,000 | ±25 |
Precision | 1,000 – 10,000 | ±10 |
Reflow Oven
A reflow oven is used to melt the solder paste and form a permanent connection between the SMD components and the PCB. The oven follows a specific temperature profile, which typically includes four stages: preheat, soak, reflow, and cooling.
Reflow Stage | Temperature Range (°C) | Time (seconds) |
---|---|---|
Preheat | 150 – 180 | 60 – 120 |
Soak | 180 – 200 | 60 – 120 |
Reflow | 220 – 250 | 30 – 60 |
Cooling | < 100 | 60 – 120 |
Solder Paste Printer
A solder paste printer applies solder paste onto the PCB pads prior to component placement. The printer uses a stencil with apertures that match the PCB pad layout, ensuring precise solder paste deposition.
Inspection Systems
Inspection systems are used to verify the quality of the SMD welding process. These systems include:
- Automated Optical Inspection (AOI): Uses cameras and image processing software to detect component placement and soldering defects.
- X-ray Inspection: Utilizes X-rays to examine solder joints hidden under components, such as Ball Grid Arrays (BGAs).
SMD Welding Process
The SMD welding process involves several steps:
PCB Preparation
Before starting the SMD welding process, the PCB must be cleaned and inspected for any defects. Solder paste is then applied onto the PCB pads using a solder paste printer.
Component Placement
The pick and place machine accurately places the SMD components onto the PCB, aligning them with the solder paste deposits.
Reflow Soldering
The populated PCB is then passed through a reflow oven, which melts the solder paste and creates a permanent bond between the components and the PCB pads.
Inspection and Testing
After the reflow soldering process, the PCB undergoes inspection using AOI or X-ray systems to identify any defects. Functional testing is also performed to ensure the proper operation of the assembled device.
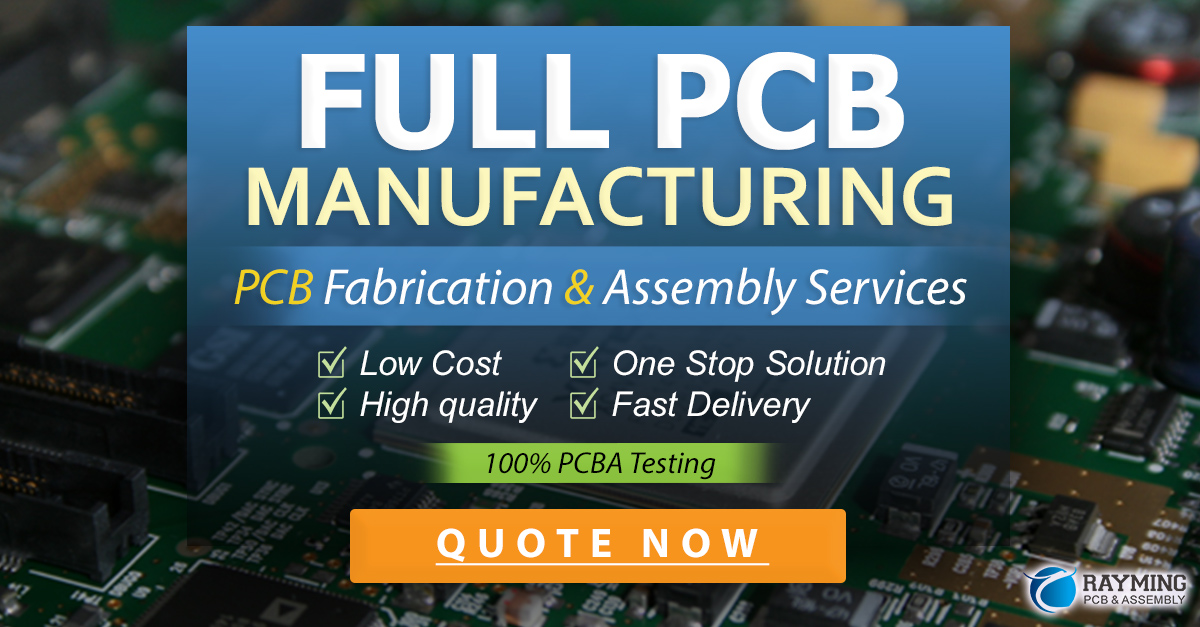
Common SMD Welding Defects and Solutions
Despite the automated nature of SMD welding, defects can still occur. Some common defects include:
-
Tombstoning: This occurs when one end of a component lifts off the PCB during reflow soldering. To prevent tombstoning, ensure proper solder paste deposition and component placement.
-
Bridging: Solder bridges form when excess solder connects adjacent pads. Adjust solder paste volume and stencil design to minimize bridging.
-
Insufficient Solder: Insufficient solder joints can result in poor electrical connections. Increase solder paste volume or adjust reflow profile to ensure adequate solder joint formation.
-
Component Shifting: Components may shift during reflow soldering due to improper placement or inadequate solder paste volume. Optimize pick and place machine settings and solder paste deposition to minimize component shifting.
Frequently Asked Questions (FAQ)
-
Q: What is the difference between SMD and through-hole technology?
A: SMD components are mounted directly onto the surface of the PCB, while through-hole components have leads that are inserted into holes drilled in the PCB and soldered on the opposite side. -
Q: Can SMD components be soldered manually?
A: Yes, SMD components can be soldered manually using a soldering iron and tweezers. However, this method is time-consuming and requires a steady hand and good eyesight. -
Q: What is the purpose of solder paste in SMD welding?
A: Solder paste is a mixture of tiny solder particles and flux. It is used to temporarily hold the SMD components in place on the PCB pads and to form a permanent solder joint during the reflow soldering process. -
Q: How does the reflow oven temperature profile affect the SMD welding process?
A: The reflow oven temperature profile must be carefully controlled to ensure proper solder joint formation. An incorrect temperature profile can lead to defects such as insufficient solder, tombstoning, or component damage. -
Q: What are the challenges in inspecting SMD solder joints?
A: SMD solder joints are often hidden under the components, making visual inspection difficult. Automated Optical Inspection (AOI) and X-ray inspection systems are used to detect defects in SMD solder joints that are not visible to the naked eye.
Conclusion
SMD welding has become an indispensable technology in the electronics manufacturing industry, enabling the production of smaller, faster, and more reliable electronic devices. By understanding the equipment, process, and common defects associated with SMD welding, manufacturers can optimize their production lines and ensure the highest quality end products. As electronic devices continue to advance, SMD welding will play a crucial role in driving innovation and meeting the ever-increasing demands of consumers.
Leave a Reply