Understanding Surface Finish and its Importance in PCB Manufacturing
When designing and manufacturing printed circuit boards (PCBs), one crucial aspect to consider is the surface finish. The surface finish is the coating applied to the exposed copper on the PCB, which serves multiple purposes, such as protecting the copper from oxidation, enhancing solderability, and improving the overall reliability of the board. Selecting the appropriate surface finish is essential for ensuring the proper functioning and longevity of your electronic devices.
In this comprehensive article, we will explore the various surface finish options available, their properties, and the factors to consider when choosing the right surface finish for your PCB project.
The Role of Surface Finish in PCB Performance
Surface finish plays a vital role in the performance and reliability of PCBs. Here are some key reasons why surface finish is important:
-
Protection against oxidation: Exposed copper on the PCB can quickly oxidize when exposed to air, leading to a decrease in solderability and conductivity. Surface finishes act as a barrier, preventing oxidation and maintaining the integrity of the copper traces.
-
Enhanced solderability: A good surface finish improves the solderability of the PCB, ensuring strong and reliable solder joints between components and the board. This is particularly important for Surface Mount Technology (SMT) components, which require precise and uniform solder connections.
-
Improved reliability: The right surface finish can enhance the overall reliability of the PCB by protecting against environmental factors such as moisture, corrosion, and wear. This is especially crucial for PCBs operating in harsh environments or applications with stringent reliability requirements.
-
Compatibility with different components: Surface finishes can affect the compatibility of the PCB with various components, such as connectors, switches, and sensors. Choosing a surface finish that is compatible with the components used in your design ensures proper functionality and longevity.
-
Aesthetics: In some cases, the surface finish can also contribute to the aesthetic appeal of the PCB. Certain finishes, such as immersion silver or immersion gold, can provide a professional and visually pleasing appearance to the board.
Common Surface Finish Options
There are several surface finish options available for PCBs, each with its own set of advantages and disadvantages. Let’s explore some of the most common surface finishes:
1. Hot Air Solder Leveling (HASL)
HASL is one of the most widely used surface finishes in the PCB industry. In this process, the PCB is immersed in a molten solder bath, and then hot air is used to level the solder on the surface of the board. The resulting finish is a thin, uniform layer of solder that provides excellent solderability and protection against oxidation.
Advantages:
– Cost-effective
– Good solderability
– Suitable for through-hole components
– Widely available and well-established process
Disadvantages:
– Inconsistent surface flatness due to the manual leveling process
– Not suitable for fine-pitch SMT components
– May cause thermal shock to the PCB during the hot air leveling process
2. Organic Solderability Preservative (OSP)
OSP is a chemical coating applied to the exposed copper on the PCB. It acts as a temporary protective layer, preventing oxidation and maintaining solderability until the PCB is ready for assembly.
Advantages:
– Cost-effective
– Flat and uniform surface
– Suitable for fine-pitch SMT components
– Environmentally friendly (no lead or other heavy metals)
Disadvantages:
– Limited shelf life (typically 6-12 months)
– Requires careful handling and storage to maintain solderability
– May not be suitable for multiple reflow cycles or rework
3. Immersion Silver (IAg)
Immersion silver is a chemical process that deposits a thin layer of silver onto the exposed copper surfaces of the PCB. The silver layer provides excellent solderability and protection against oxidation.
Advantages:
– Flat and uniform surface
– Good solderability
– Suitable for fine-pitch SMT components
– Long shelf life (up to 12 months)
– Environmentally friendly (no lead)
Disadvantages:
– Higher cost compared to OSP and HASL
– May tarnish over time, especially in high-sulfur environments
– Not suitable for some connectors and switches due to the risk of silver migration
4. Immersion Tin (ISn)
Immersion tin is another chemical process that deposits a thin layer of tin onto the exposed copper surfaces of the PCB. It provides good solderability and protection against oxidation.
Advantages:
– Flat and uniform surface
– Good solderability
– Suitable for fine-pitch SMT components
– Environmentally friendly (no lead)
– Relatively low cost compared to other immersion finishes
Disadvantages:
– Limited shelf life (typically 6-12 months)
– May develop Tin Whiskers over time, which can cause short circuits
– Not suitable for high-temperature applications
5. Electroless Nickel Immersion Gold (ENIG)
ENIG is a two-step process that first deposits a layer of nickel onto the copper surface, followed by a thin layer of gold. The nickel layer provides a barrier against copper migration, while the gold layer ensures excellent solderability and protection against oxidation.
Advantages:
– Flat and uniform surface
– Excellent solderability
– Suitable for fine-pitch SMT components
– Long shelf life (up to 12 months)
– Good resistance to corrosion and wear
Disadvantages:
– Higher cost compared to other surface finishes
– Requires strict process control to avoid defects such as black pad syndrome
– Gold layer may dissolve into the solder joint during assembly, potentially affecting joint strength
Factors to Consider When Choosing a Surface Finish
When selecting a surface finish for your PCB, there are several factors to consider to ensure the best performance and reliability for your application:
-
Application requirements: Consider the specific requirements of your application, such as operating environment, temperature range, and expected lifespan. Some surface finishes may be more suitable for harsh environments or high-reliability applications than others.
-
Component compatibility: Ensure that the chosen surface finish is compatible with the components used in your design. Some components may have specific requirements or restrictions regarding the surface finish.
-
Manufacturing process: Take into account the manufacturing process and the capabilities of your PCB fabricator. Some surface finishes may require specialized equipment or expertise, which can affect availability and lead time.
-
Cost: Consider the cost implications of different surface finishes. While some finishes may have a higher upfront cost, they may provide better long-term reliability and performance, ultimately saving costs in the long run.
-
Shelf life: If your PCBs will be stored for an extended period before assembly, choose a surface finish with a longer shelf life to maintain solderability and prevent oxidation.
-
Rework and repair: Consider the ease of rework and repair for the selected surface finish. Some finishes may be more forgiving during rework processes, while others may require special handling or techniques.
-
Environmental considerations: If environmental sustainability is a priority for your project, consider surface finishes that are lead-free and comply with RoHS (Restriction of Hazardous Substances) regulations.
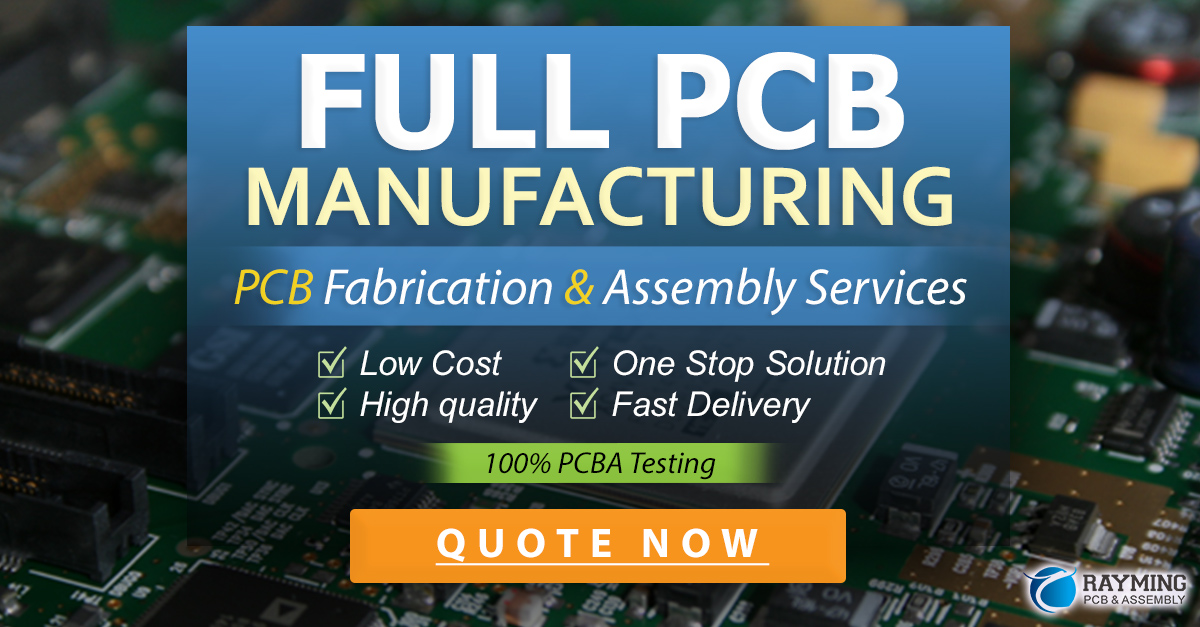
Comparison of Surface Finishes
To help you make an informed decision, here’s a comparison table of the common surface finishes discussed earlier:
Surface Finish | Solderability | Shelf Life | Fine-Pitch SMT | Cost | Environmental |
---|---|---|---|---|---|
HASL | Good | Long | Not suitable | Low | Contains lead |
OSP | Good | Limited | Suitable | Low | Lead-free |
Immersion Silver | Excellent | Long | Suitable | Medium | Lead-free |
Immersion Tin | Good | Limited | Suitable | Medium | Lead-free |
ENIG | Excellent | Long | Suitable | High | Lead-free |
Frequently Asked Questions (FAQ)
-
Q: What is the most cost-effective surface finish for my PCB?
A: The most cost-effective surface finish depends on your specific requirements. HASL and OSP are generally the lowest-cost options, but they may not be suitable for all applications. Consider the long-term reliability and performance needs of your project when making a decision. -
Q: Can I mix different surface finishes on the same PCB?
A: While it is possible to use different surface finishes on the same PCB, it is generally not recommended. Mixing surface finishes can lead to compatibility issues and may complicate the assembly process. It’s best to choose a single surface finish that meets all your requirements. -
Q: How do I choose between immersion silver and ENIG?
A: Both immersion silver and ENIG offer excellent solderability and are suitable for fine-pitch SMT components. ENIG provides better corrosion and wear resistance, making it a good choice for harsh environments. However, ENIG is more expensive than immersion silver. Consider your application requirements and budget when deciding between the two. -
Q: What is the shelf life of OSP, and how can I extend it?
A: The shelf life of OSP is typically limited to 6-12 months. To extend the shelf life, store your PCBs in a controlled environment with low humidity and stable temperature. Avoid exposure to air and contaminants by sealing the PCBs in moisture-barrier bags with desiccants. -
Q: Can I use HASL for fine-pitch SMT components?
A: HASL is not recommended for fine-pitch SMT components due to its inconsistent surface flatness. The manual leveling process can result in uneven surfaces, making it difficult to achieve reliable solder joints for small components. For fine-pitch SMT, consider surface finishes like OSP, immersion silver, or ENIG.
Conclusion
Selecting the right surface finish for your PCB is a critical decision that can significantly impact the performance, reliability, and longevity of your electronic devices. By understanding the various surface finish options available and considering factors such as application requirements, component compatibility, manufacturing process, cost, shelf life, and environmental considerations, you can make an informed choice that best suits your project needs.
Remember, there is no one-size-fits-all solution when it comes to surface finishes. Each option has its own strengths and weaknesses, and the best choice will depend on your specific requirements. Don’t hesitate to consult with your PCB fabricator or an experienced engineer to discuss your options and get expert advice tailored to your project.
By carefully evaluating your surface finish options and making an informed decision, you can ensure that your PCBs perform optimally and reliably, ultimately contributing to the success of your electronic products.
Leave a Reply