What are PCB Tolerances?
PCB tolerances refer to the acceptable variations in the dimensions, spacing, and other physical characteristics of a printed circuit board. These tolerances are essential to ensure that the PCB functions as intended and fits properly within its designated enclosure or assembly. Adhering to strict tolerances helps to minimize the risk of manufacturing defects, assembly issues, and potential performance problems.
Types of PCB Tolerances
There are several types of PCB tolerances that manufacturers must consider, including:
- Dimensional Tolerances
- Board size and thickness
- Hole size and position
- Edge clearance
-
Slot and cutout dimensions
-
Feature Tolerances
- Trace width and spacing
- Pad size and shape
- Solder mask opening
-
Silkscreen registration
-
Electrical Tolerances
- Impedance control
- Dielectric constant
- Copper thickness
- Resistivity
IPC Guidelines and Standards for PCB Tolerances
The IPC (Association Connecting Electronics Industries) is a global trade association that develops and publishes standards for the electronic manufacturing industry. These standards provide guidelines for the design, fabrication, assembly, and testing of electronic products, including PCBs.
The most relevant IPC standards for PCB tolerances include:
- IPC-6012: Qualification and Performance Specification for Rigid Printed Boards
- IPC-6013: Qualification and Performance Specification for Flexible Printed Boards
- IPC-2221: Generic Standard on Printed Board Design
- IPC-2222: Sectional Design Standard for Rigid Organic Printed Boards
- IPC-2223: Sectional Design Standard for Flexible Printed Boards
These standards outline the recommended tolerances for various aspects of PCB manufacturing, helping manufacturers to produce high-quality, reliable products consistently.
San Francisco Circuits’ Updated PCB Tolerances
San Francisco Circuits has updated its PCB tolerances to align with the latest IPC guidelines and standards. Some of the key updates include:
Dimensional Tolerances
Dimension | Tolerance |
---|---|
Board Size | ± 0.25 mm (0.010″) |
Board Thickness | ± 10% |
Hole Size (Plated) | ± 0.075 mm (0.003″) |
Hole Size (Non-Plated) | ± 0.125 mm (0.005″) |
Hole Position | ± 0.25 mm (0.010″) |
Edge Clearance | ± 0.25 mm (0.010″) |
Slot and Cutout Dimensions | ± 0.25 mm (0.010″) |
Feature Tolerances
Feature | Tolerance |
---|---|
Trace Width and Spacing | ± 20% (minimum 0.075 mm or 0.003″) |
Pad Size and Shape | ± 20% (minimum 0.075 mm or 0.003″) |
Solder Mask Opening | ± 0.075 mm (0.003″) |
Silkscreen Registration | ± 0.25 mm (0.010″) |
Electrical Tolerances
Electrical Property | Tolerance |
---|---|
Impedance Control | ± 10% |
Dielectric Constant | ± 0.1 |
Copper Thickness | ± 10% |
Resistivity | ± 10% |
By adhering to these updated tolerances, San Francisco Circuits ensures that their customers receive PCBs that meet the highest industry standards for quality and reliability.
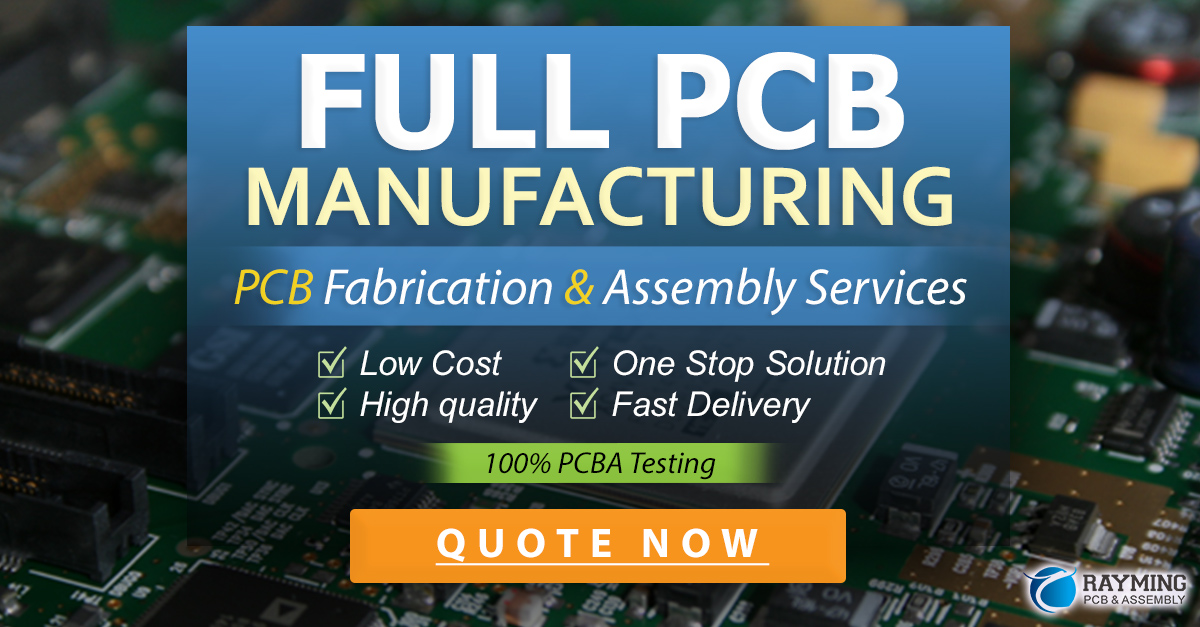
Benefits of Strict PCB Tolerances
Maintaining strict PCB tolerances offers several benefits for both manufacturers and customers, including:
-
Improved Reliability: PCBs that are manufactured within the specified tolerances are more likely to function as intended and have a lower risk of failure due to manufacturing defects or assembly issues.
-
Better Compatibility: Adhering to industry-standard tolerances ensures that PCBs are compatible with a wide range of components and assemblies, reducing the risk of fit or performance issues.
-
Increased Consistency: By following consistent tolerance guidelines, manufacturers can produce PCBs with uniform quality and characteristics, making it easier for customers to integrate them into their products.
-
Cost Savings: Strict tolerances help to minimize the need for rework, repairs, or replacements due to manufacturing defects or assembly problems, ultimately saving time and money for both manufacturers and customers.
Challenges in Maintaining PCB Tolerances
While maintaining strict PCB tolerances is essential for producing high-quality products, manufacturers may face several challenges, such as:
-
Equipment Limitations: Some manufacturing equipment may have inherent limitations in terms of precision and accuracy, making it difficult to consistently achieve the desired tolerances.
-
Material Variations: Inconsistencies in the raw materials used for PCB manufacturing, such as copper foils or substrates, can affect the ability to maintain tight tolerances.
-
Process Control: Ensuring that all manufacturing processes, from etching to plating, are tightly controlled and monitored is crucial for maintaining tolerances but can be challenging in practice.
-
Cost Considerations: Achieving tighter tolerances often requires more advanced equipment, higher-quality materials, and additional process controls, which can increase manufacturing costs.
Despite these challenges, San Francisco Circuits is committed to maintaining the highest standards for PCB tolerances, ensuring that their customers receive the best possible products.
FAQ
-
Q: Why are PCB tolerances important?
A: PCB tolerances are important because they ensure that the PCB functions as intended, fits properly within its designated enclosure or assembly, and minimizes the risk of manufacturing defects, assembly issues, and potential performance problems. -
Q: What are the most relevant IPC standards for PCB tolerances?
A: The most relevant IPC standards for PCB tolerances include IPC-6012, IPC-6013, IPC-2221, IPC-2222, and IPC-2223. These standards outline the recommended tolerances for various aspects of PCB manufacturing. -
Q: How do strict PCB tolerances benefit manufacturers and customers?
A: Strict PCB tolerances benefit manufacturers and customers by improving reliability, ensuring better compatibility, increasing consistency, and ultimately saving time and money by minimizing the need for rework, repairs, or replacements due to manufacturing defects or assembly problems. -
Q: What are some of the challenges in maintaining PCB tolerances?
A: Some of the challenges in maintaining PCB tolerances include equipment limitations, material variations, process control, and cost considerations. Achieving tighter tolerances often requires more advanced equipment, higher-quality materials, and additional process controls, which can increase manufacturing costs. -
Q: How does San Francisco Circuits ensure that their PCBs meet the highest industry standards for quality and reliability?
A: San Francisco Circuits ensures that their PCBs meet the highest industry standards for quality and reliability by adhering to the updated tolerances based on the latest IPC guidelines and standards. They are committed to maintaining the highest standards for PCB tolerances despite the challenges involved in the manufacturing process.
Conclusion
San Francisco Circuits’ release of updated PCB tolerances in accordance with IPC guidelines and standards demonstrates their commitment to providing customers with the highest quality PCBs. By adhering to strict tolerances, they ensure that their products are reliable, compatible, and consistent, ultimately benefiting both the manufacturer and the customer. While maintaining tight tolerances can present challenges, San Francisco Circuits remains dedicated to upholding the highest industry standards and delivering superior PCB manufacturing services.
Leave a Reply