What is RoHS and Why is it Important?
RoHS is a directive that restricts the use of certain hazardous substances in electrical and electronic equipment. The primary goal of RoHS is to protect human health and the environment by reducing the use of lead and other harmful substances in electronics.
RoHS compliance is crucial for electronics manufacturers because:
- It is a legal requirement in many countries
- It demonstrates a commitment to environmental responsibility
- It ensures safer products for consumers
- It facilitates access to global markets
Challenges of Lead-Free PCB Assembly
Transitioning to lead-free PCB assembly presents several challenges:
Higher Melting Point of Lead-Free Solder
Lead-free solder alloys have higher melting points than traditional tin-lead solder. This requires higher processing temperatures, which can cause thermal stress on components and PCBs.
Tin Whiskers
Lead-free solder is more prone to the formation of tin whiskers, which are thin, conductive filaments that can grow from tin-plated surfaces. Tin whiskers can cause short circuits and reliability issues.
Compatibility Issues
Some components and PCB materials may not be compatible with lead-free assembly processes, requiring careful selection and testing.
Top RoHS (Lead-Free) PCB Assembly Companies
Several companies specialize in lead-free PCB assembly, offering expertise and advanced manufacturing capabilities to meet RoHS requirements.
1. Jabil Circuit
Jabil Circuit is a global manufacturing services company that provides lead-free PCB assembly services. They have extensive experience in RoHS compliance and offer a range of services, including design for manufacturability (DFM) analysis, component selection, and reliability testing.
2. Foxconn
Foxconn is a Taiwanese electronics manufacturing company that offers lead-free PCB assembly services. They have a global presence and are known for their high-volume manufacturing capabilities. Foxconn has invested in advanced lead-free assembly technologies and processes to ensure RoHS compliance.
3. Flex
Flex (formerly Flextronics) is a multinational electronics manufacturing company that provides lead-free PCB assembly services. They have a global network of manufacturing facilities and offer a full range of services, from design and engineering to manufacturing and testing. Flex has expertise in lead-free assembly and can handle both high-mix, low-volume and high-volume production.
4. Celestica
Celestica is a Canadian electronics manufacturing services company that specializes in lead-free PCB assembly. They have a global footprint and offer a range of services, including design, engineering, manufacturing, and supply chain management. Celestica has invested in advanced lead-free assembly equipment and processes to ensure RoHS compliance.
5. Sanmina
Sanmina is a global electronics manufacturing services company that provides lead-free PCB assembly services. They have a network of manufacturing facilities worldwide and offer a full range of services, from design and engineering to manufacturing and logistics. Sanmina has expertise in lead-free assembly and can handle both prototyping and high-volume production.
Company | Headquarters | Global Presence | Services |
---|---|---|---|
Jabil Circuit | USA | Worldwide | DFM analysis, component selection, reliability testing |
Foxconn | Taiwan | Worldwide | High-volume manufacturing, advanced lead-free technologies |
Flex | Singapore | Worldwide | Design, engineering, manufacturing, testing |
Celestica | Canada | Worldwide | Design, engineering, manufacturing, supply chain management |
Sanmina | USA | Worldwide | Design, engineering, manufacturing, logistics |
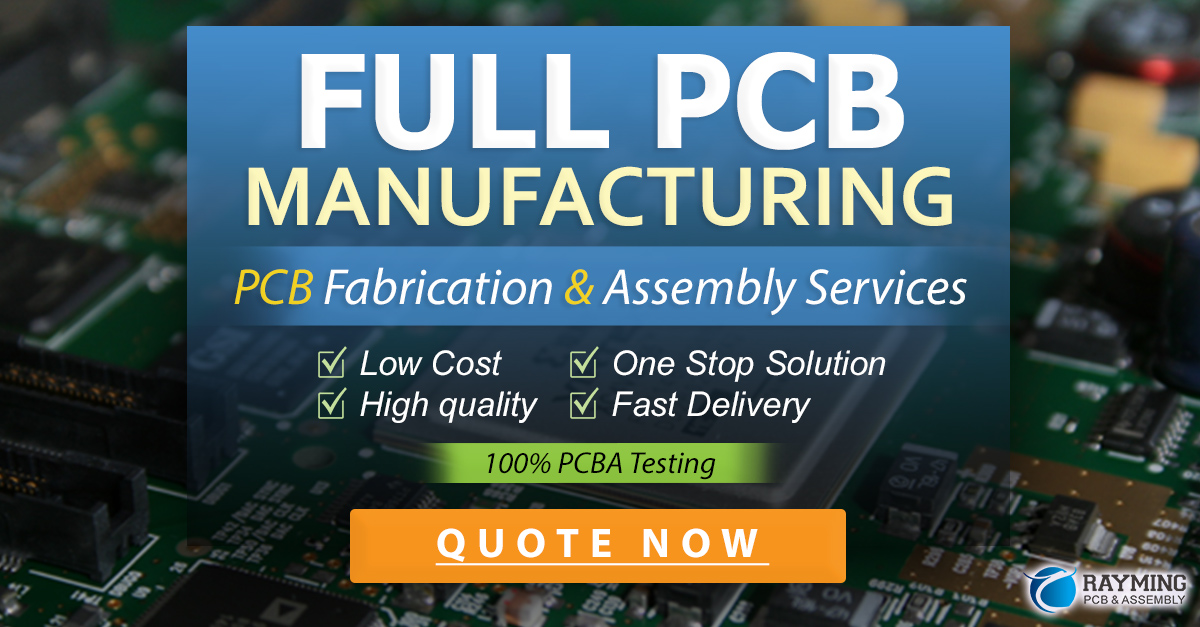
Choosing a Lead-Free PCB Assembly Partner
When selecting a lead-free PCB assembly partner, consider the following factors:
- RoHS compliance expertise and track record
- Manufacturing capabilities and capacity
- Quality control and testing processes
- Design and engineering support
- Supply chain management and logistics
- Cost and lead times
- Communication and customer support
Working with an experienced lead-free PCB assembly company can help ensure RoHS compliance, product quality, and reliability.
Best Practices for Lead-Free PCB Design
To optimize your PCB design for lead-free assembly, follow these best practices:
- Choose RoHS-compliant components and materials
- Consider the thermal requirements of lead-free solder
- Design for manufacturability (DFM) to minimize assembly challenges
- Use appropriate surface finishes and coatings
- Conduct thorough testing and validation
By designing your PCBs with lead-free assembly in mind, you can streamline the manufacturing process and ensure the best possible results.
The Future of Lead-Free PCB Assembly
As environmental regulations continue to evolve, lead-free PCB assembly will remain a critical aspect of electronics manufacturing. Advances in lead-free solder alloys, assembly processes, and testing methods will help address the challenges associated with lead-free assembly.
Emerging technologies, such as low-temperature solder (LTS) and conductive adhesives, may offer new solutions for lead-free assembly. Additionally, the increasing adoption of eco-friendly materials and processes will drive innovation in the lead-free PCB assembly industry.
Frequently Asked Questions (FAQ)
1. What is RoHS, and why is it important for PCB assembly?
RoHS (Restriction of Hazardous Substances) is a directive that restricts the use of certain hazardous substances, including lead, in electrical and electronic equipment. RoHS compliance is important for PCB assembly because it helps protect human health and the environment, demonstrates environmental responsibility, and facilitates access to global markets.
2. What are the main challenges of lead-free PCB assembly?
The main challenges of lead-free PCB assembly include higher melting points of lead-free solder alloys, which require higher processing temperatures; the formation of tin whiskers, which can cause short circuits and reliability issues; and compatibility issues with certain components and PCB materials.
3. How do I choose a lead-free PCB assembly partner?
When choosing a lead-free PCB assembly partner, consider factors such as their RoHS compliance expertise and track record, manufacturing capabilities and capacity, quality control and testing processes, design and engineering support, supply chain management and logistics, cost and lead times, and communication and customer support.
4. What are some best practices for designing PCBs for lead-free assembly?
Best practices for designing PCBs for lead-free assembly include choosing RoHS-compliant components and materials, considering the thermal requirements of lead-free solder, designing for manufacturability (DFM) to minimize assembly challenges, using appropriate surface finishes and coatings, and conducting thorough testing and validation.
5. What does the future hold for lead-free PCB assembly?
The future of lead-free PCB assembly will be shaped by evolving environmental regulations, advances in lead-free solder alloys and assembly processes, and the adoption of eco-friendly materials and technologies. Emerging solutions, such as low-temperature solder (LTS) and conductive adhesives, may help address the challenges associated with lead-free assembly and drive innovation in the industry.
In conclusion, lead-free PCB assembly is a critical aspect of modern electronics manufacturing, driven by the need for RoHS compliance and environmental responsibility. By partnering with experienced lead-free PCB assembly companies and following best practices for PCB design, electronics manufacturers can ensure the quality, reliability, and compliance of their products in an increasingly regulated global market.
Leave a Reply