Introduction to BGA Rework
Ball Grid Array (BGA) is an advanced semiconductor packaging technology that uses a grid of solder balls to connect the integrated circuit (IC) to the printed circuit board (PCB). BGA packages offer numerous advantages over traditional through-hole and surface-mount packages, including:
- Higher pin density
- Smaller footprint
- Better thermal and electrical performance
- Increased reliability
However, BGAs also present challenges when it comes to rework and repair. The high pin count and small pitch of BGA packages make them difficult to remove and replace without damaging the PCB or neighboring components. This is where specialized BGA rework equipment and expertise come into play.
What is BGA Rework?
BGA rework refers to the process of removing and replacing BGA components on a PCB. This may be necessary due to:
- Manufacturing defects
- Component failure
- Design changes
- Upgrades or modifications
The BGA rework process typically involves the following steps:
- Pre-heating the PCB to a specific temperature profile
- Removing the old BGA component using hot air or infrared heating
- Cleaning the PCB pads and applying new solder paste
- Placing the new BGA component using precise alignment tools
- Reflowing the solder joints using controlled heating
- Inspecting the solder joints for proper wetting and alignment
- Testing the PCB for functionality
Rocket EMS Invests in Large BGA Rework
Rocket EMS, a leading provider of electronics manufacturing services, has recently added large BGA rework capability to its arsenal. This investment allows Rocket EMS to handle BGAs with pin counts up to 2,500 and pitch sizes down to 0.3mm.
Why Large BGA Rework Matters
As electronic devices become more complex and miniaturized, the use of large BGAs is becoming increasingly common. Large BGAs offer several benefits, such as:
- Increased functionality in a smaller package
- Improved signal integrity and power delivery
- Reduced PCB layer count and cost
However, large BGAs also pose unique rework challenges due to their high pin count and fine pitch. Without proper equipment and expertise, large BGA rework can result in:
- Solder bridging or opens
- Component misalignment or tilting
- PCB pad lifting or damage
- Thermal stress on neighboring components
By investing in large BGA rework capability, Rocket EMS can help its customers overcome these challenges and achieve high-quality, reliable results.
Rocket EMS’s Large BGA Rework Equipment
To perform large BGA rework, Rocket EMS has acquired state-of-the-art equipment from leading manufacturers. This includes:
-
BGA rework station: A fully automated system with advanced features such as split vision alignment, multi-zone heating, and real-time temperature monitoring. This ensures precise component placement and controlled heating for optimal solder joint quality.
-
Solder paste printer: A high-precision printer that can apply solder paste to fine-pitch BGA pads with minimal variation. This ensures consistent solder volume and prevents defects such as bridging or insufficient solder.
-
Reflow oven: A nitrogen-based reflow oven with multiple heating zones and precise temperature control. This allows for customized reflow profiles that match the specific requirements of large BGAs and minimize thermal stress on the PCB.
-
X-ray inspection system: A high-resolution X-ray system that can detect hidden solder joint defects such as voids, cracks, or head-in-pillow. This provides valuable feedback for process optimization and quality control.
Rocket EMS’s Large BGA Rework Process
Rocket EMS follows a rigorous process for large BGA rework to ensure consistent quality and reliability. The process includes the following key steps:
-
PCB preparation: The PCB is cleaned and baked to remove moisture and contaminants. Any damaged pads or traces are repaired using micro-soldering techniques.
-
BGA removal: The old BGA component is removed using a combination of hot air and vacuum suction. The PCB is preheated to a specific temperature profile to minimize thermal shock and pad lifting.
-
Site redressing: The PCB pads are cleaned using a soldering iron and solder wick. New solder paste is applied using a stencil printer or dispensing system.
-
BGA placement: The new BGA component is aligned to the PCB using the split vision system of the rework station. The component is held in place with a vacuum pick-up tool.
-
Reflow soldering: The PCB is heated using the reflow oven to melt the solder paste and form a metallurgical bond between the BGA balls and PCB pads. The reflow profile is carefully controlled to achieve optimal solder joint quality and minimize thermal stress.
-
Inspection and testing: The reworked PCB is inspected using X-ray imaging to verify solder joint integrity and detect any hidden defects. Functional testing is performed to ensure that the PCB meets performance specifications.
Benefits of Large BGA Rework at Rocket EMS
By utilizing Rocket EMS’s large BGA rework service, customers can enjoy several benefits, such as:
-
Cost savings: Reworking large BGAs in-house can be expensive and time-consuming. Outsourcing to Rocket EMS allows customers to avoid capital equipment costs and focus on their core competencies.
-
Quality assurance: Rocket EMS’s advanced equipment and expertise ensure high-quality solder joints and minimal risk of PCB damage. This translates to improved reliability and reduced field failures.
-
Quick turnaround: Rocket EMS’s streamlined process and dedicated rework team enable fast turnaround times for large BGA rework projects. This helps customers meet tight deadlines and minimize downtime.
-
Flexibility: Rocket EMS can accommodate a wide range of large BGA packages and PCB designs. This allows customers to choose the best component for their application without worrying about rework limitations.
Conclusion
Large BGA rework is a critical capability for electronics manufacturers that want to stay competitive in today’s market. By investing in advanced equipment and expertise, Rocket EMS has positioned itself as a leader in this area.
Whether you need to rework a few prototypes or a large production run, Rocket EMS has the tools and know-how to get the job done right. With its commitment to quality, efficiency, and customer satisfaction, Rocket EMS is the ideal partner for your large BGA rework needs.
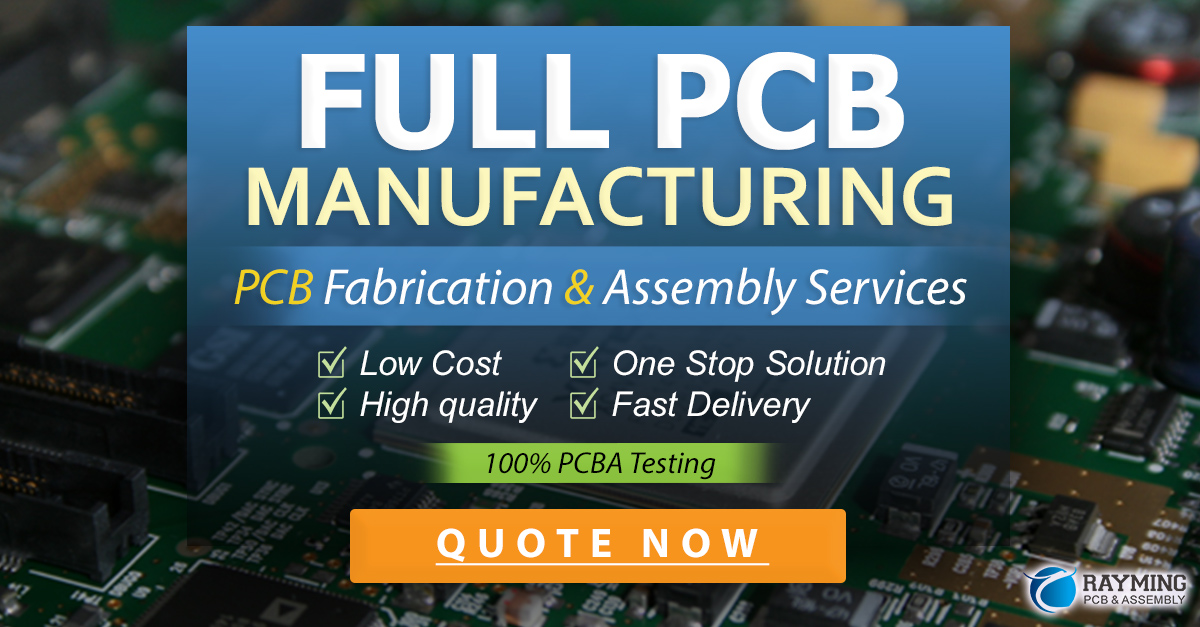
FAQ
What is the maximum BGA pin count that Rocket EMS can rework?
Rocket EMS can rework BGAs with up to 2,500 pins.
What is the minimum BGA pitch that Rocket EMS can handle?
Rocket EMS can handle BGAs with pitch sizes down to 0.3mm.
How long does a typical large BGA rework project take?
The turnaround time for a large BGA rework project depends on factors such as the number of PCBs, the complexity of the design, and the availability of replacement components. However, Rocket EMS strives to complete most projects within 3-5 business days.
Can Rocket EMS rework other types of components besides BGAs?
Yes, Rocket EMS has the capability to rework a wide range of surface-mount and through-hole components, including QFPs, LGAs, SOICs, and more.
What industries does Rocket EMS serve with its large BGA rework service?
Rocket EMS serves customers in a variety of industries, including aerospace, defense, medical, automotive, consumer electronics, and more. Its large BGA rework service is suitable for any application that requires high-reliability solder joints and precise component placement.
Leave a Reply