What are Castellated Solder Pads?
Castellated solder pads, also known as castellated holes or castellations, are a type of surface mount technology (SMT) used in printed circuit board (PCB) design. These pads are essentially a series of half-holes or semi-circular cutouts along the edge of a PCB, resembling the battlements of a castle, hence the name “castellated.”
Castellated Pads serve as an alternative to traditional through-hole mounting or edge connectors, providing a simple and efficient way to connect multiple PCBs or modules together. They allow for perpendicular board-to-board connections, creating a more compact and space-saving design compared to other methods.
Advantages of Castellated Solder Pads
- Space-saving: Castellated pads enable vertical stacking of PCBs, reducing the overall footprint of the device.
- Simplified assembly: The semi-circular cutouts allow for easy alignment and soldering of the boards, streamlining the assembly process.
- Reduced cost: Castellated pads eliminate the need for additional connectors or headers, reducing the overall cost of the device.
- Improved signal integrity: The direct board-to-board connection provided by castellated pads minimizes signal loss and interference compared to other connection methods.
How to Design Castellated Solder Pads
Designing castellated solder pads requires careful consideration of several factors to ensure proper functionality and reliability. Here are some key points to keep in mind:
Pad Size and Spacing
The size and spacing of the castellated pads should be determined based on the specific requirements of the project, such as the PCB thickness, soldering method, and the desired mechanical strength of the connection.
Pad Size | Spacing | PCB Thickness | Application |
---|---|---|---|
0.5 mm | 1.0 mm | 0.8 mm | Compact, lightweight devices |
0.8 mm | 1.6 mm | 1.6 mm | General-purpose applications |
1.0 mm | 2.0 mm | 2.4 mm | High-reliability, industrial applications |
Drill Hole Size and Shape
The drill holes for castellated pads are typically oval-shaped, with the semi-circular portion exposed at the edge of the PCB. The hole size should be selected based on the pad size and the desired solder fill.
Pad Size | Drill Hole Size | Solder Fill |
---|---|---|
0.5 mm | 0.3 mm | 50-75% |
0.8 mm | 0.5 mm | 50-75% |
1.0 mm | 0.7 mm | 50-75% |
Solder Mask and Paste
Applying solder mask and solder paste to the castellated pads is essential for ensuring a reliable and robust connection. The solder mask should be designed to expose the entire semi-circular portion of the pad, while the solder paste should be applied in sufficient quantity to fill the hole and form a strong bond.
Castellated Solder Pad Manufacturing Process
The manufacturing process for castellated solder pads involves several steps, including:
- PCB fabrication: The PCB is manufactured according to the design specifications, with the castellated holes drilled and plated.
- Solder mask application: The solder mask is applied to the PCB, exposing the castellated pads.
- Solder paste printing: Solder paste is applied to the castellated pads using a stencil or syringe.
- Component placement: The PCBs or modules are aligned and placed onto the castellated pads.
- Reflow soldering: The assembly is heated in a reflow oven, melting the solder paste and forming a strong bond between the pads.
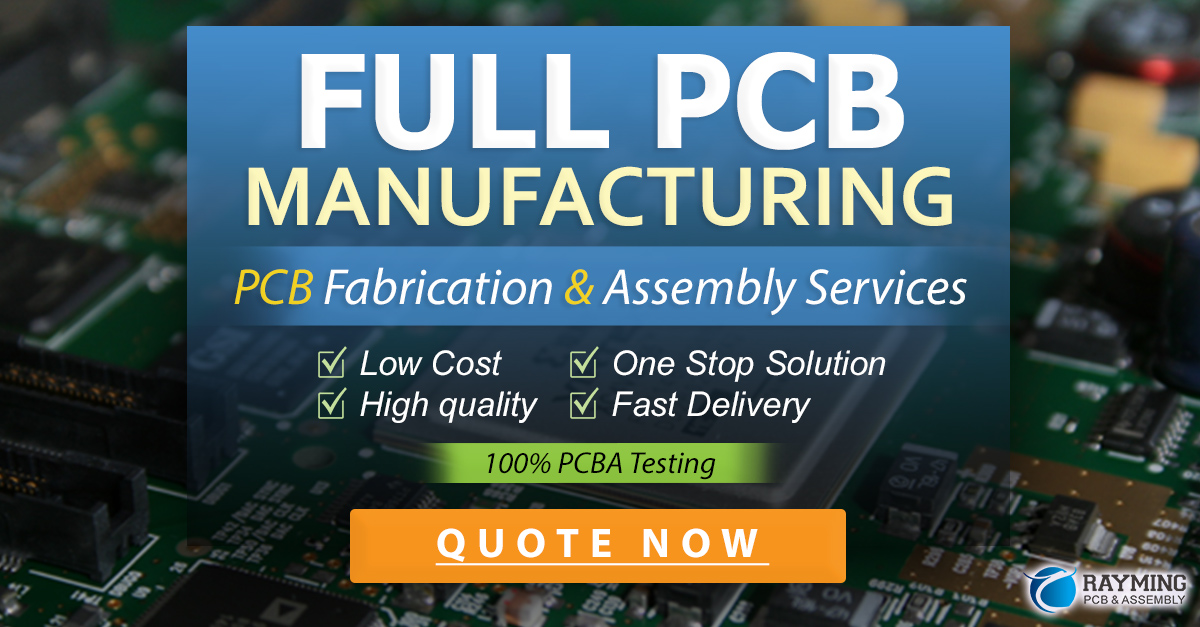
Applications of Castellated Solder Pads
Castellated solder pads find applications in various industries and projects where space-saving, modular design, and reliable board-to-board connections are required. Some common applications include:
- Internet of Things (IoT) devices
- Wearable electronics
- Robotics and automation
- Aerospace and defense systems
- Medical devices
- Automotive electronics
- Consumer electronics
Best Practices for Using Castellated Solder Pads
To ensure optimal performance and reliability when using castellated solder pads, consider the following best practices:
- Follow the recommended pad size and spacing guidelines for your specific application and PCB thickness.
- Ensure proper alignment of the boards during assembly to avoid misalignment and poor connections.
- Use the appropriate amount of solder paste to achieve the desired fill level and bond strength.
- Implement proper reflow soldering techniques, including temperature profile and cooling rate, to minimize thermal stress and warpage.
- Conduct thorough testing and inspection of the assembled devices to identify any potential issues or defects.
Frequently Asked Questions (FAQ)
- Q: Can castellated solder pads be used with through-hole components?
A: No, castellated solder pads are designed specifically for surface mount components and cannot accommodate through-hole components. - Q: What is the minimum PCB thickness required for using castellated solder pads?
A: The minimum PCB thickness depends on the specific pad size and spacing used, but generally, a thickness of 0.8 mm or greater is recommended for reliable connections. - Q: Can castellated solder pads be reworked or repaired?
A: Yes, castellated solder pads can be reworked or repaired using standard SMT rework techniques, such as hot air or soldering iron. However, care must be taken to avoid damaging the pads or the PCB. - Q: Are there any limitations to the number of times a castellated connection can be mated and unmated?
A: The number of mating cycles depends on various factors, such as the pad size, solder material, and environmental conditions. Generally, castellated connections can withstand several mating cycles, but it is essential to consider the specific requirements of the application. - Q: Can castellated solder pads be used in high-vibration or shock environments?
A: Castellated solder pads can be used in high-vibration or shock environments, provided that proper design considerations are made, such as using larger pad sizes, increasing solder fill, and implementing additional mechanical support or strain relief.
Conclusion
Castellated solder pads offer a compact, cost-effective, and reliable solution for board-to-board connections in various electronic devices and systems. By understanding the design principles, manufacturing process, and best practices associated with castellated pads, engineers and designers can create more efficient and robust electronic assemblies that meet the demanding requirements of modern applications.
As the electronics industry continues to evolve, castellated solder pads will likely remain an essential tool in the designer’s arsenal, enabling the development of innovative, space-saving, and high-performance devices across a wide range of industries and applications.
Leave a Reply