Introduction to Multilayer PCB Additive Manufacturing
Multilayer PCBs (Printed Circuit Boards) are essential components in modern electronics, enabling the creation of compact, high-performance devices. Traditional manufacturing methods for multilayer PCBs involve subtractive processes, such as etching and drilling, which can be time-consuming, wasteful, and limited in terms of design flexibility. However, the emergence of additive manufacturing technologies has opened up new possibilities for revolutionizing multilayer PCB production.
Additive manufacturing, also known as 3D printing, is a process that builds objects layer by layer using digital design files. This approach offers several advantages over traditional manufacturing methods, including faster prototyping, reduced material waste, and the ability to create complex geometries. In the context of multilayer PCBs, additive manufacturing has the potential to streamline production, reduce costs, and enable innovative designs.
Benefits of Additive Manufacturing for Multilayer PCBs
- Rapid Prototyping: Additive manufacturing allows for the quick creation of prototype PCBs, enabling designers to test and refine their designs iteratively.
- Design Flexibility: 3D printing technologies can produce complex geometries and unique features that are difficult or impossible to achieve with traditional manufacturing methods.
- Reduced Waste: Additive manufacturing only uses the material necessary to build the PCB, minimizing waste compared to subtractive processes.
- Cost Efficiency: By reducing material waste and streamlining the production process, additive manufacturing can lead to cost savings in multilayer PCB production.
Additive Manufacturing Technologies for Multilayer PCBs
Several additive manufacturing technologies have been adapted for multilayer PCB production, each with its own advantages and limitations.
Inkjet Printing
Inkjet printing is a popular method for additive manufacturing of PCBs. This process involves depositing conductive ink onto a substrate using a high-precision inkjet printer. The ink is then cured or sintered to create conductive traces. Inkjet printing is suitable for creating fine features and can be used with a variety of substrate materials.
Advantages of Inkjet Printing for Multilayer PCBs
- High resolution and precision
- Compatibility with various substrate materials
- Ability to create fine features and complex geometries
Limitations of Inkjet Printing for Multilayer PCBs
- Relatively slow printing speed compared to other methods
- Limited materials available for conductive inks
- Potential for nozzle clogging and print head maintenance issues
Aerosol Jet Printing
Aerosol jet printing is another additive manufacturing technique suitable for multilayer PCB production. This method uses a focused aerosol beam to deposit conductive materials onto a substrate. The aerosol is generated by atomizing a conductive ink or material suspension, which is then carried to the substrate by a carrier gas. Aerosol jet printing offers high resolution and the ability to print on non-planar surfaces.
Advantages of Aerosol Jet Printing for Multilayer PCBs
- High resolution and precision
- Ability to print on non-planar surfaces
- Wide range of compatible materials, including conductive inks, polymers, and nanoparticle suspensions
Limitations of Aerosol Jet Printing for Multilayer PCBs
- Relatively slow printing speed compared to other methods
- Higher equipment costs compared to inkjet printing
- Potential for nozzle clogging and material compatibility issues
Selective Laser Sintering (SLS)
Selective laser sintering is an additive manufacturing process that uses a laser to sinter powdered materials, fusing them together to create a solid object. In the context of multilayer PCBs, SLS can be used to create conductive traces by sintering conductive powders, such as copper or silver, onto a substrate. SLS offers high precision and the ability to create complex 3D structures.
Advantages of Selective Laser Sintering for Multilayer PCBs
- High precision and resolution
- Ability to create complex 3D structures
- Wide range of compatible materials, including conductive powders and polymers
Limitations of Selective Laser Sintering for Multilayer PCBs
- Relatively slow printing speed compared to other methods
- Higher equipment costs compared to inkjet and aerosol jet printing
- Potential for thermal distortion and residual stresses in the printed parts
Materials for Additive Manufacturing of Multilayer PCBs
The success of additive manufacturing for multilayer PCBs depends on the availability of suitable materials that can provide the necessary electrical and mechanical properties. Several types of materials have been developed for this purpose, including:
-
Conductive Inks: These are specialized inks containing conductive particles, such as silver or copper nanoparticles, suspended in a liquid medium. Conductive inks are used in inkjet and aerosol jet printing processes.
-
Conductive Polymers: These are polymers that have been modified to exhibit electrical conductivity. Conductive polymers can be used as filaments or powders in additive manufacturing processes, such as fused deposition modeling (FDM) or selective laser sintering (SLS).
-
Conductive Nanoparticle Suspensions: These are suspensions of conductive nanoparticles, such as silver or copper, in a liquid medium. Nanoparticle suspensions can be used in inkjet and aerosol jet printing processes, offering high conductivity and the ability to create fine features.
-
Conductive Powders: These are powdered materials, such as copper or silver, that can be sintered using selective laser sintering (SLS) to create conductive traces and structures.
The choice of material depends on the specific additive manufacturing process, the desired electrical and mechanical properties, and the compatibility with the substrate and other materials used in the multilayer PCB.
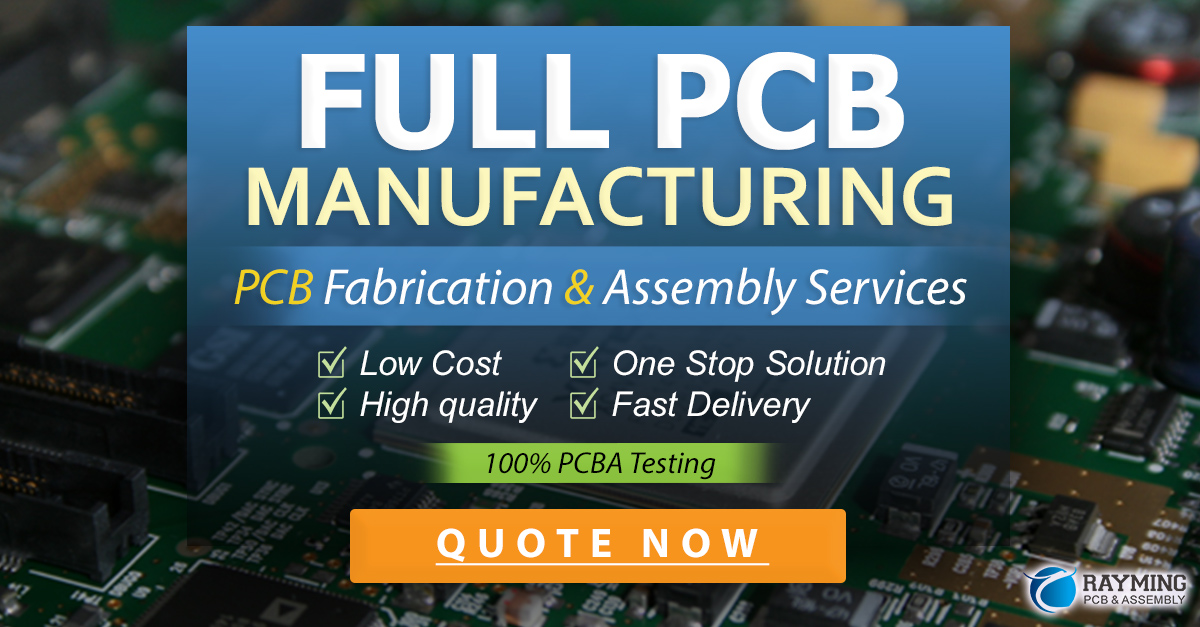
Design Considerations for Additive Manufacturing of Multilayer PCBs
Designing multilayer PCBs for additive manufacturing requires a different approach compared to traditional subtractive manufacturing methods. Designers must consider the specific capabilities and limitations of the chosen additive manufacturing process and materials. Some key design considerations include:
-
Feature Size: Additive manufacturing processes have different resolutions and minimum feature sizes. Designers must ensure that the PCB layout is compatible with the capabilities of the selected manufacturing process.
-
Material Properties: The electrical and mechanical properties of the materials used in additive manufacturing may differ from those of traditional PCB materials. Designers must consider these properties when selecting materials and designing the PCB layout.
-
Substrate Compatibility: The substrate material used in additive manufacturing must be compatible with the selected printing process and materials. Designers must consider factors such as surface energy, roughness, and thermal stability when choosing a substrate.
-
Warpage and Shrinkage: Additive manufacturing processes may introduce thermal stresses and material shrinkage, which can cause warpage in the printed PCB. Designers must consider these factors and incorporate appropriate compensation techniques, such as adding support structures or adjusting the design geometry.
-
Post-Processing: Some additive manufacturing processes may require post-processing steps, such as sintering, curing, or surface treatment, to achieve the desired electrical and mechanical properties. Designers must consider these additional steps when planning the manufacturing process and assessing the overall production time and cost.
Applications of Additive Manufacturing in Multilayer PCB Production
Additive manufacturing has the potential to revolutionize multilayer PCB production across various industries and applications. Some key areas where additive manufacturing can make a significant impact include:
-
Rapid Prototyping: Additive manufacturing enables the quick creation of prototype PCBs, allowing designers to test and refine their designs iteratively. This can significantly reduce the time and cost associated with product development and validation.
-
Customization and Low-Volume Production: Additive manufacturing is well-suited for producing customized or low-volume PCBs, as it eliminates the need for expensive tooling and setup costs associated with traditional manufacturing methods.
-
High-Density Interconnects (HDI): Additive manufacturing processes, such as inkjet printing and aerosol jet printing, can create fine features and high-density interconnects, enabling the production of compact, high-performance PCBs for advanced applications.
-
Flexible and Stretchable Electronics: Additive manufacturing can be used to create PCBs on flexible and stretchable substrates, enabling the development of wearable electronics, medical devices, and other innovative applications.
-
3D Integrated Circuits: Additive manufacturing technologies, such as selective laser sintering (SLS), can create complex 3D structures, enabling the integration of electronic components and interconnects in three-dimensional space. This can lead to the development of highly compact and efficient electronic devices.
Challenges and Future Outlook
Despite the numerous benefits and applications of additive manufacturing in multilayer PCB production, several challenges need to be addressed for widespread adoption:
-
Material Development: There is a need for continued development of high-performance, reliable, and cost-effective materials for additive manufacturing of PCBs, including conductive inks, polymers, and powders.
-
Process Optimization: Additive manufacturing processes for multilayer PCBs must be optimized to improve printing speed, resolution, and reliability. This requires advancements in equipment design, process control, and quality assurance techniques.
-
Standardization: The development of industry standards and guidelines for additive manufacturing of PCBs is essential to ensure consistency, reliability, and compatibility across different manufacturers and applications.
-
Skill Development: As additive manufacturing technologies for PCBs evolve, there is a need for skilled professionals who can design, operate, and maintain these systems. Educational institutions and industry organizations must collaborate to develop training programs and curricula to address this skill gap.
Despite these challenges, the future outlook for additive manufacturing in multilayer PCB production is promising. As technology continues to advance and more companies adopt these innovative manufacturing methods, we can expect to see significant improvements in PCB performance, customization, and sustainability. Additive manufacturing has the potential to transform the electronics industry, enabling the creation of novel devices and applications that were previously unimaginable.
Frequently Asked Questions (FAQ)
-
What is additive manufacturing, and how does it differ from traditional PCB manufacturing methods?
Additive manufacturing, also known as 3D printing, is a process that builds objects layer by layer using digital design files. In contrast, traditional PCB manufacturing methods, such as etching and drilling, involve subtractive processes that remove material from a substrate. Additive manufacturing offers several advantages, including faster prototyping, reduced material waste, and the ability to create complex geometries. -
What are the main additive manufacturing technologies used for multilayer PCB production?
The main additive manufacturing technologies used for multilayer PCB production include inkjet printing, aerosol jet printing, and selective laser sintering (SLS). Each method has its own advantages and limitations, such as resolution, material compatibility, and printing speed. -
What materials are used in additive manufacturing of multilayer PCBs?
Materials used in additive manufacturing of multilayer PCBs include conductive inks, conductive polymers, conductive nanoparticle suspensions, and conductive powders. The choice of material depends on the specific additive manufacturing process, the desired electrical and mechanical properties, and the compatibility with the substrate and other materials used in the PCB. -
What are the key design considerations for additive manufacturing of multilayer PCBs?
Key design considerations for additive manufacturing of multilayer PCBs include feature size, material properties, substrate compatibility, warpage and shrinkage, and post-processing requirements. Designers must consider the specific capabilities and limitations of the chosen additive manufacturing process and materials when creating PCB layouts. -
What are the potential applications of additive manufacturing in multilayer PCB production?
Additive manufacturing has numerous potential applications in multilayer PCB production, including rapid prototyping, customization and low-volume production, high-density interconnects (HDI), flexible and stretchable electronics, and 3D integrated circuits. As technology advances, we can expect to see even more innovative applications emerge, transforming the electronics industry and enabling the creation of novel devices and solutions.
Additive Manufacturing Technology | Advantages | Limitations |
---|---|---|
Inkjet Printing | – High resolution and precision – Compatibility with various substrate materials – Ability to create fine features and complex geometries |
– Relatively slow printing speed compared to other methods – Limited materials available for conductive inks – Potential for nozzle clogging and print head maintenance issues |
Aerosol Jet Printing | – High resolution and precision – Ability to print on non-planar surfaces – Wide range of compatible materials, including conductive inks, polymers, and nanoparticle suspensions |
– Relatively slow printing speed compared to other methods – Higher equipment costs compared to inkjet printing – Potential for nozzle clogging and material compatibility issues |
Selective Laser Sintering (SLS) | – High precision and resolution – Ability to create complex 3D structures – Wide range of compatible materials, including conductive powders and polymers |
– Relatively slow printing speed compared to other methods – Higher equipment costs compared to inkjet and aerosol jet printing – Potential for thermal distortion and residual stresses in the printed parts |
In conclusion, additive manufacturing has the potential to revolutionize multilayer PCB production by offering faster prototyping, reduced material waste, and the ability to create complex geometries. As technology continues to advance and more companies adopt these innovative manufacturing methods, we can expect to see significant improvements in PCB performance, customization, and sustainability. However, challenges such as material development, process optimization, standardization, and skill development must be addressed for widespread adoption. Despite these challenges, the future outlook for additive manufacturing in multilayer PCB production is promising, and it has the potential to transform the electronics industry, enabling the creation of novel devices and applications that were previously unimaginable.
Leave a Reply