Introduction
Printed Circuit Boards (PCBs) are essential components in modern electronic devices, forming the backbone of everything from smartphones to industrial equipment. However, the cost of manufacturing and assembling PCBs can significantly impact the overall expense of a project. In this comprehensive guide, we will explore seven effective strategies to help reduce PCB costs without compromising quality or functionality.
Tip 1: Optimize PCB Design for Manufacturing (DFM)
Understanding DFM
Design for Manufacturing (DFM) is a crucial approach that involves designing PCBs with the manufacturing process in mind. By adhering to DFM guidelines, you can minimize the risk of manufacturing issues, reduce production time, and ultimately save on PCB costs.
Key DFM Considerations
- Component Placement: Ensure adequate spacing between components to facilitate easy assembly and minimize the risk of bridging or short circuits.
- Trace Width and Spacing: Maintain appropriate trace widths and spacing to prevent signal integrity issues and improve manufacturability.
- Via Size and Placement: Optimize via sizes and placement to enhance reliability and reduce drilling costs.
- Solder Mask and Silkscreen: Use clear and legible solder mask and silkscreen markings to aid in assembly and troubleshooting.
By incorporating DFM principles into your PCB design process, you can streamline manufacturing, reduce the likelihood of costly rework, and achieve significant cost savings.
Tip 2: Choose the Right PCB Material
PCB Substrate Materials
The choice of PCB substrate material plays a vital role in determining the overall cost of your PCB. Common PCB materials include:
1. FR-4: A popular and cost-effective choice for most PCB applications.
2. High-Frequency Materials: Specialized materials like Rogers or Isola for high-frequency or RF applications, which tend to be more expensive.
3. Flexible PCBs: Polymide or polyester-based materials for flexible PCB designs, which can be costlier than rigid PCBs.
Cost-Saving Strategies
- Evaluate Material Requirements: Carefully assess your PCB’s performance and environmental requirements to select the most cost-effective material that meets your needs.
- Opt for Standard Materials: Whenever possible, choose standard PCB materials like FR-4 to benefit from lower costs and better availability.
- Consider Hybrid Designs: In some cases, using a combination of standard and specialized materials in a hybrid design can help balance cost and performance.
By selecting the most suitable and cost-effective PCB material for your project, you can significantly reduce overall PCB costs without compromising functionality.
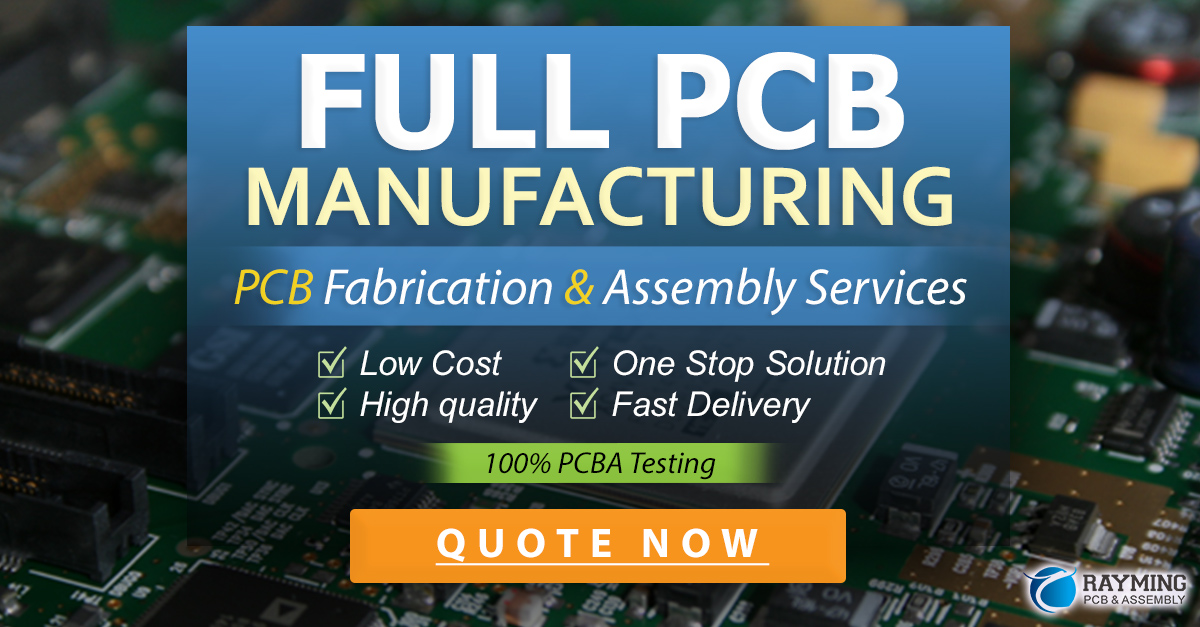
Tip 3: Minimize PCB Layer Count
Impact of Layer Count on Cost
The number of layers in a PCB directly affects its manufacturing cost. Each additional layer requires more material, processing time, and complexity, resulting in higher expenses. Therefore, minimizing the layer count is a key strategy for reducing PCB costs.
Strategies for Reducing Layer Count
- Efficient Component Placement: Optimize component placement to minimize the need for additional layers and reduce overall PCB size.
- Strategic Via Usage: Use vias judiciously to route signals between layers, avoiding unnecessary layer changes.
- Multilayer Alternatives: Consider alternative technologies like High-Density Interconnect (HDI) or blind and buried vias to achieve higher density without increasing layer count.
Layer Count | Relative Cost |
---|---|
1 | 1.0 |
2 | 1.5 |
4 | 2.0 |
6 | 2.5 |
8 | 3.0 |
Table 1: Relative cost comparison based on PCB layer count
By carefully evaluating your design requirements and optimizing layer usage, you can significantly reduce PCB Manufacturing Costs while still meeting your project’s needs.
Tip 4: Opt for Standard PCB Sizes and Shapes
Benefits of Standard PCB Sizes and Shapes
Using standard PCB sizes and shapes can lead to significant cost savings in PCB manufacturing. Standard sizes allow for better utilization of raw materials, reduced setup times, and streamlined production processes. Common standard PCB sizes include:
PCB Size | Dimensions (mm) |
---|---|
Small | 25 x 25 |
Medium | 50 x 50 |
Large | 100 x 100 |
Extra Large | 150 x 150 |
Table 2: Common standard PCB sizes
Cost-Saving Strategies
- Choose Standard Sizes: Whenever possible, design your PCB to fit within standard size ranges to take advantage of cost efficiencies.
- Avoid Irregular Shapes: Stick to rectangular or square PCB shapes to minimize the need for custom tooling and reduce manufacturing complexity.
- Panelize for Volume Production: If your project requires a large quantity of smaller PCBs, consider panelizing them to fit standard panel sizes, reducing overall manufacturing costs.
By leveraging standard PCB sizes and shapes, you can optimize material usage, simplify manufacturing processes, and achieve significant cost savings in PCB production.
Tip 5: Reduce Component Count and Complexity
Impact of Component Count on Cost
The number and complexity of components on a PCB directly influence its manufacturing and assembly costs. Each additional component requires more materials, assembly time, and increases the risk of defects. By reducing component count and complexity, you can minimize costs and improve overall PCB reliability.
Strategies for Reducing Component Count
- Integrate Functions: Look for opportunities to combine multiple functions into a single component, such as using a microcontroller with built-in peripherals instead of separate ICs.
- Optimize Circuit Design: Carefully review your schematic and eliminate any unnecessary components or redundant functionality.
- Use Standardized Components: Opt for standard, readily available components instead of custom or specialized parts to benefit from lower costs and better availability.
- Consider Modular Design: Break down complex designs into smaller, modular sub-circuits that can be easily assembled and tested separately, reducing overall complexity.
By streamlining your component selection and optimizing your circuit design, you can significantly reduce PCB Assembly Costs and improve manufacturing efficiency.
Tip 6: Leverage Economies of Scale
Benefits of Volume Production
One of the most effective ways to reduce PCB costs is to leverage economies of scale through volume production. As the quantity of PCBs increases, the fixed costs associated with setup, tooling, and other non-recurring expenses are spread across a larger number of units, resulting in a lower cost per PCB.
Cost-Saving Strategies
- Plan for Volume Production: If your project allows, plan for higher production volumes to take advantage of cost efficiencies.
- Negotiate with Suppliers: Work closely with your PCB manufacturer and component suppliers to secure volume discounts and better pricing for larger orders.
- Optimize Inventory Management: Implement effective inventory management strategies to minimize the risk of obsolescence and reduce carrying costs.
Production Volume | Relative Cost per PCB |
---|---|
100 | 1.0 |
500 | 0.8 |
1,000 | 0.6 |
5,000 | 0.4 |
10,000 | 0.3 |
Table 3: Relative cost per PCB based on production volume
By carefully planning your production volumes and collaborating with your supply chain partners, you can significantly reduce PCB costs through economies of scale.
Tip 7: Work Closely with Your PCB Manufacturer
Benefits of Collaboration
Establishing a strong partnership with your PCB manufacturer is crucial for achieving cost savings and ensuring the success of your project. By collaborating closely with your manufacturer, you can tap into their expertise, receive valuable feedback, and optimize your design for cost-effective manufacturing.
Strategies for Effective Collaboration
- Early Involvement: Engage your PCB manufacturer early in the design process to benefit from their insights and recommendations.
- DFM Feedback: Share your design files with your manufacturer and request a DFM review to identify potential issues and cost-saving opportunities.
- Regular Communication: Maintain open and regular communication with your manufacturer to stay informed about project progress, address any concerns, and explore cost-saving strategies.
- Leverage Manufacturer Capabilities: Understand your manufacturer’s capabilities and leverage their expertise in areas such as material selection, assembly techniques, and testing methodologies.
By fostering a strong collaborative relationship with your PCB manufacturer, you can optimize your design for cost-effective production, minimize the risk of costly errors, and achieve significant cost savings throughout the manufacturing process.
Frequently Asked Questions (FAQ)
-
What is the most effective way to reduce PCB costs?
The most effective way to reduce PCB costs is to optimize your design for manufacturing (DFM) and work closely with your PCB manufacturer to identify cost-saving opportunities throughout the production process. -
How does PCB layer count affect manufacturing costs?
PCB layer count has a direct impact on manufacturing costs. Each additional layer increases the complexity of the PCB, requiring more materials, processing time, and specialized equipment. By minimizing the layer count and optimizing your design, you can significantly reduce PCB manufacturing costs. -
Can using standard PCB sizes and shapes really save money?
Yes, using standard PCB sizes and shapes can lead to significant cost savings. Standard sizes allow for better utilization of raw materials, reduced setup times, and streamlined manufacturing processes. By designing your PCB to fit within standard size ranges, you can take advantage of these cost efficiencies. -
How does component selection impact PCB Assembly Costs?
The choice of components on your PCB directly affects assembly costs. Using standardized, readily available components instead of custom or specialized parts can help reduce costs and improve availability. Additionally, reducing the overall component count and complexity can minimize assembly time and the risk of defects, leading to cost savings. -
Is it always better to opt for higher production volumes to save costs?
In many cases, higher production volumes can lead to significant cost savings due to economies of scale. However, it’s essential to carefully assess your project requirements and market demand to determine the optimal production volume. Overproduction can lead to excess inventory and carrying costs, so it’s crucial to strike a balance between cost savings and actual demand.
Conclusion
Reducing PCB costs is a critical aspect of any electronics project, as it directly impacts the overall budget and profitability. By implementing the seven tips discussed in this article, you can effectively optimize your PCB design, manufacturing, and assembly processes to achieve significant cost savings.
Remember to prioritize Design for Manufacturing (DFM) principles, select the most suitable PCB materials, minimize layer count and component complexity, leverage standard sizes and shapes, and collaborate closely with your PCB manufacturer. By adopting these strategies and continuously seeking opportunities for improvement, you can drive down PCB costs without compromising quality or functionality.
As you embark on your next PCB project, keep these cost-saving tips in mind and work closely with your team and supply chain partners to identify and implement the most effective solutions. With a focus on cost optimization and a commitment to excellence, you can successfully navigate the challenges of PCB manufacturing and assembly while achieving your project goals within budget.
Leave a Reply