Introduction to Solder Mask Bridges
A solder mask bridge is a thin layer of solder mask material that spans across two or more adjacent pads or traces on a printed circuit board (PCB). The purpose of the solder mask bridge is to prevent solder from flowing between the pads during the soldering process, which could cause short circuits or other issues. However, solder mask bridges can sometimes break off, leading to various problems in the PCB manufacturing process and the final product’s functionality.
In this article, we will explore the reasons behind solder mask bridge breaking off, the consequences of this issue, and potential solutions to prevent or mitigate the problem.
What is a Solder Mask?
Before diving into the specifics of solder mask bridges, let’s first understand what a solder mask is and its role in PCB manufacturing.
A solder mask, also known as a solder resist or solder stop, is a thin layer of polymer material applied to the surface of a PCB. The primary functions of a solder mask are:
- To protect the copper traces and pads from oxidation and corrosion
- To prevent solder from bridging between adjacent pads or traces during the soldering process
- To provide electrical insulation between conductive areas
- To improve the PCB’s aesthetics and readability by providing a contrasting background color
Solder masks are typically applied using screen printing or photoimaging techniques, and they come in various colors, with green being the most common.
The Role of Solder Mask Bridges
Solder mask bridges are an essential feature in PCB design and manufacturing. They are created by leaving a small gap in the solder mask between adjacent pads or traces. This gap allows the solder mask material to form a bridge, which prevents solder from flowing between the pads during the soldering process.
Solder mask bridges are particularly important in fine-pitch components, such as ball grid arrays (BGAs) or quad-flat no-leads (QFNs), where the distance between pads is minimal. Without proper solder mask bridges, the risk of solder bridging and short circuits increases significantly.
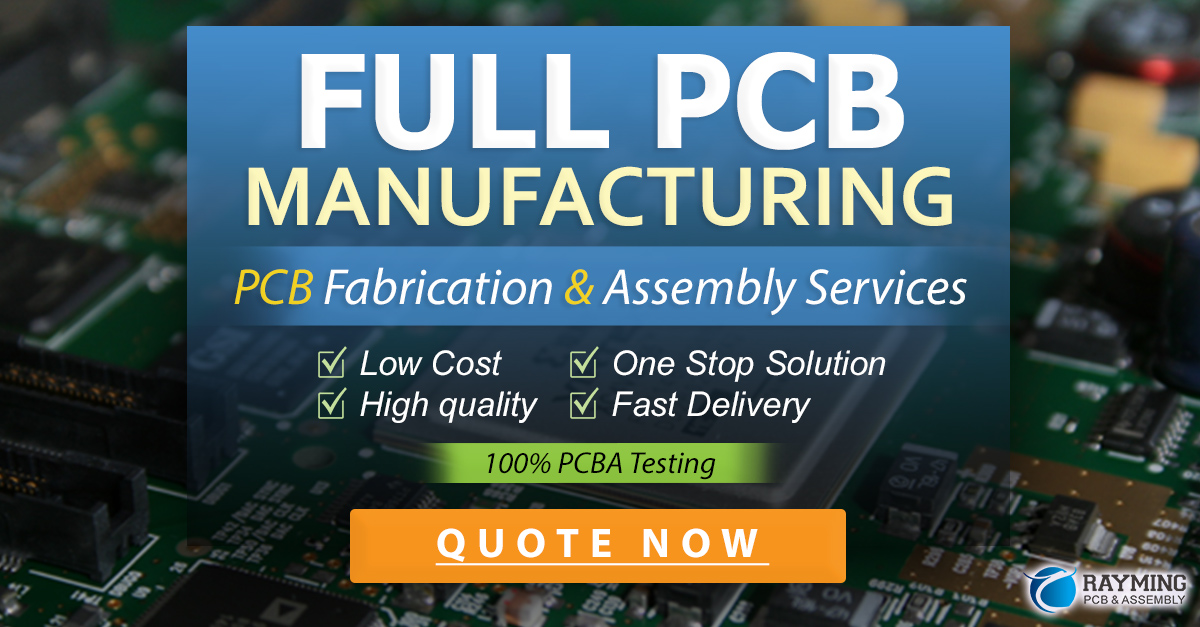
Causes of Solder Mask Bridge Breaking Off
There are several reasons why solder mask bridges may break off during the PCB manufacturing process or in the final product. Some of the most common causes include:
1. Improper Solder Mask Design
One of the primary reasons for solder mask bridge breakage is improper design. If the solder mask bridge is too thin or too narrow, it may not have sufficient strength to withstand the stresses encountered during the manufacturing process or in the final application.
The following table provides general guidelines for solder mask bridge dimensions:
Solder Mask Bridge Parameter | Recommended Value |
---|---|
Minimum width | 0.1 mm (4 mil) |
Minimum thickness | 0.025 mm (1 mil) |
Minimum spacing between pads | 0.15 mm (6 mil) |
Designers should adhere to these guidelines and consider the specific requirements of their PCB when creating solder mask bridges.
2. Manufacturing Process Issues
Various issues during the PCB manufacturing process can lead to solder mask bridge breakage:
- Overetching: If the copper etching process is not well-controlled, it can result in overetching, which weakens the solder mask bridge and makes it more susceptible to breakage.
- Improper curing: Solder masks require proper curing to achieve optimal mechanical and chemical properties. Insufficient or excessive curing can lead to brittle or weak solder mask bridges.
- Misalignment: Misalignment between the solder mask and the copper layer can cause the solder mask bridge to be positioned incorrectly, making it more prone to damage.
- Contamination: Contaminants, such as dust or oil, on the PCB surface during solder mask application can weaken the adhesion between the solder mask and the substrate, increasing the risk of bridge breakage.
3. Environmental Factors
Environmental factors can also contribute to solder mask bridge breaking off, especially in the final application:
- Thermal stress: Exposure to high temperatures or rapid temperature changes can cause the solder mask bridge to expand or contract, leading to mechanical stress and potential breakage.
- Mechanical stress: Physical forces, such as bending, twisting, or impacts, can cause the solder mask bridge to break off, particularly if it is already weakened due to design or manufacturing issues.
- Chemical exposure: Certain chemicals, such as solvents or cleaning agents, can degrade the solder mask material, making the bridges more susceptible to breakage.
Consequences of Solder Mask Bridge Breaking Off
When a solder mask bridge breaks off, it can lead to several problems in the PCB and the final product:
-
Solder bridging: Without the solder mask bridge in place, solder can flow between adjacent pads or traces during the soldering process, causing short circuits and compromising the PCB’s functionality.
-
Decreased reliability: Broken solder mask bridges can expose the underlying copper to the environment, making it more susceptible to oxidation, corrosion, and mechanical damage. This can reduce the overall reliability of the PCB.
-
Aesthetic issues: Broken solder mask bridges can affect the visual appearance of the PCB, which may be a concern for some applications or customers.
-
Rework and repair costs: If solder mask bridge breakage is detected during the manufacturing process, it may require rework or repair, increasing production time and costs. If the issue is discovered in the final product, it can lead to costly field failures and returns.
Solutions to Prevent Solder Mask Bridge Breaking Off
To minimize the risk of solder mask bridge breaking off, consider the following solutions:
-
Proper design: Ensure that solder mask bridges are designed with appropriate dimensions and spacing, taking into account the specific requirements of the PCB and the manufacturing process.
-
Process optimization: Work closely with the PCB manufacturer to optimize the manufacturing process, including etching, solder mask application, and curing, to minimize the risk of bridge breakage.
-
Quality control: Implement strict quality control measures, such as visual inspection and electrical testing, to identify and address any solder mask bridge issues early in the manufacturing process.
-
Material selection: Choose high-quality solder mask materials that offer good mechanical and chemical properties, and are compatible with the PCB substrate and the manufacturing process.
-
Environmental testing: Perform environmental testing, such as thermal cycling and mechanical stress tests, to ensure that the solder mask bridges can withstand the expected operating conditions of the final product.
Frequently Asked Questions (FAQ)
-
What is the purpose of a solder mask bridge?
A solder mask bridge prevents solder from flowing between adjacent pads or traces during the soldering process, minimizing the risk of short circuits and other issues. -
What are the most common causes of solder mask bridge breaking off?
The most common causes include improper solder mask design, manufacturing process issues (such as overetching or improper curing), and environmental factors (such as thermal or mechanical stress). -
What are the consequences of solder mask bridge breaking off?
Broken solder mask bridges can lead to solder bridging, decreased PCB reliability, aesthetic issues, and increased rework and repair costs. -
How can I prevent solder mask bridge breaking off?
To prevent solder mask bridge breakage, ensure proper design, optimize the manufacturing process, implement strict quality control measures, select high-quality materials, and perform environmental testing. -
What are the recommended dimensions for solder mask bridges?
The minimum recommended width for a solder mask bridge is 0.1 mm (4 mil), the minimum thickness is 0.025 mm (1 mil), and the minimum spacing between pads is 0.15 mm (6 mil). However, designers should consider the specific requirements of their PCB when creating solder mask bridges.
Conclusion
Solder mask bridges play a crucial role in ensuring the proper functionality and reliability of printed circuit boards. However, when these bridges break off, it can lead to various problems, such as solder bridging, decreased reliability, and increased costs.
By understanding the causes of solder mask bridge breakage, including improper design, manufacturing process issues, and environmental factors, PCB designers and manufacturers can take steps to minimize the risk of this issue occurring.
Implementing proper design practices, optimizing the manufacturing process, selecting high-quality materials, and performing thorough testing can help prevent solder mask bridge breaking off and ensure the long-term success of the PCB and the final product.
Leave a Reply