Introduction to Rayming-reflow-pilot
Rayming-reflow-pilot is a cutting-edge technology designed to optimize the reflow soldering process in Electronic Manufacturing. This innovative system utilizes advanced sensors, sophisticated algorithms, and precise control mechanisms to ensure optimal temperature profiles, minimize thermal stress, and improve the overall quality of solder joints. By integrating Rayming-reflow-pilot into the production line, manufacturers can significantly enhance process efficiency, reduce defects, and achieve higher levels of reliability in their electronic products.
How Rayming-reflow-pilot works
The Rayming-reflow-pilot system consists of several key components that work together to optimize the reflow soldering process:
Sensor network
A network of high-precision sensors is strategically placed throughout the reflow oven to monitor temperature, humidity, and other critical parameters in real-time. These sensors provide accurate and continuous feedback to the control system, enabling it to make dynamic adjustments to maintain the desired temperature profile.
Advanced algorithms
Rayming-reflow-pilot employs sophisticated algorithms that analyze sensor data and make intelligent decisions to optimize the reflow process. These algorithms take into account various factors, such as component characteristics, board layout, and material properties, to calculate the optimal temperature profile for each specific product.
Precise control mechanisms
Based on the sensor data and algorithmic calculations, Rayming-reflow-pilot precisely controls the heating elements, cooling fans, and conveyor speed within the reflow oven. This ensures that the temperature profile closely follows the ideal curve, minimizing thermal stress on components and preventing common defects such as tombstoning, bridging, and voiding.
Data logging and analysis
Rayming-reflow-pilot continuously logs process data, including temperature readings, control actions, and system status. This data can be analyzed to identify trends, detect anomalies, and optimize the reflow process over time. Manufacturers can use this information to improve their process, reduce variability, and achieve higher levels of quality and reliability.
Benefits of Rayming-reflow-pilot
Implementing Rayming-reflow-pilot in electronic manufacturing offers numerous benefits:
-
Improved process control: With real-time monitoring and precise control, Rayming-reflow-pilot ensures that the reflow process remains within the desired parameters, reducing the risk of defects and improving overall quality.
-
Increased efficiency: By optimizing the temperature profile for each product, Rayming-reflow-pilot minimizes the time required for the reflow process, increasing throughput and reducing energy consumption.
-
Reduced defects: The advanced algorithms and precise control mechanisms of Rayming-reflow-pilot help to minimize common reflow defects, such as tombstoning, bridging, and voiding, resulting in higher yields and lower rework costs.
-
Enhanced reliability: By ensuring optimal temperature profiles and minimizing thermal stress, Rayming-reflow-pilot contributes to the long-term reliability of electronic products, reducing field failures and improving customer satisfaction.
-
Data-driven optimization: The data logging and analysis capabilities of Rayming-reflow-pilot enable manufacturers to make data-driven decisions, continuously improving their processes and adapting to changing product requirements.
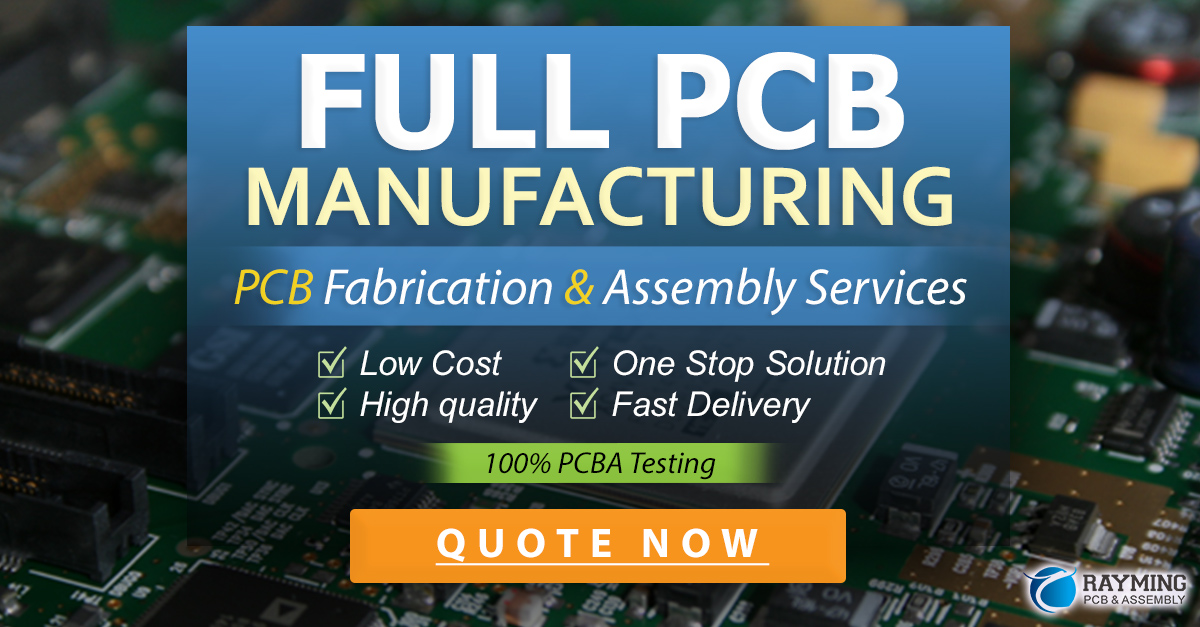
Applications of Rayming-reflow-pilot
Rayming-reflow-pilot is suitable for a wide range of electronic manufacturing applications, including:
- Consumer electronics
- Automotive electronics
- Medical devices
- Aerospace and defense systems
- Industrial control systems
- Telecommunications equipment
The versatility and adaptability of Rayming-reflow-pilot make it an ideal solution for manufacturers seeking to optimize their reflow soldering processes and achieve higher levels of quality and reliability.
Case studies
Several manufacturers have successfully implemented Rayming-reflow-pilot in their production lines, achieving significant improvements in process control, efficiency, and product quality. Here are two notable case studies:
Case study 1: Consumer electronics manufacturer
A leading consumer electronics manufacturer integrated Rayming-reflow-pilot into their production line for a new line of smartphones. By optimizing the reflow process, they achieved:
- 15% reduction in reflow cycle time
- 20% reduction in defect rate
- 10% increase in overall production efficiency
Case study 2: Automotive electronics supplier
An automotive electronics supplier implemented Rayming-reflow-pilot to improve the reliability of their safety-critical components. With the new system, they achieved:
- 25% reduction in thermal stress on components
- 30% reduction in solder joint defects
- 15% improvement in product reliability
These case studies demonstrate the tangible benefits that Rayming-reflow-pilot can bring to electronic manufacturing operations, regardless of the specific industry or product type.
Implementation process
Implementing Rayming-reflow-pilot in an electronic manufacturing facility involves several key steps:
-
Assessment: A team of experts from Rayming conducts a thorough assessment of the existing reflow soldering process, identifying areas for improvement and gathering data on product requirements and process parameters.
-
System design: Based on the assessment findings, the Rayming team designs a customized Rayming-reflow-pilot system, taking into account the specific needs and constraints of the manufacturing facility.
-
Installation: The Rayming-reflow-pilot system is installed in the reflow oven, including the sensor network, control mechanisms, and data logging equipment. The installation process is carefully planned to minimize downtime and ensure a smooth transition.
-
Training: Rayming provides comprehensive training to the manufacturing staff, covering the operation, maintenance, and troubleshooting of the Rayming-reflow-pilot system. This ensures that the team is fully equipped to leverage the benefits of the new technology.
-
Commissioning and optimization: After installation and training, the Rayming team works closely with the manufacturer to commission the system and optimize the reflow process. This involves fine-tuning the algorithms, validating the temperature profiles, and ensuring that the system is performing as expected.
-
Ongoing support: Rayming offers ongoing support and maintenance services to ensure that the Rayming-reflow-pilot system continues to operate at peak performance. This includes regular software updates, remote monitoring, and on-site support as needed.
By following this structured implementation process, manufacturers can seamlessly integrate Rayming-reflow-pilot into their operations and start realizing the benefits of improved process control, efficiency, and product quality.
Future developments
As technology continues to advance, Rayming is committed to continuously improving the Rayming-reflow-pilot system to meet the evolving needs of the electronic manufacturing industry. Some of the planned future developments include:
-
Enhanced AI capabilities: Integration of advanced artificial intelligence and machine learning algorithms to further optimize the reflow process and enable predictive maintenance.
-
Expanded sensor capabilities: Development of new sensor technologies to monitor additional process parameters, such as flux activity and solder paste viscosity, providing even more comprehensive control over the reflow process.
-
Integration with other manufacturing systems: Seamless integration with other manufacturing execution systems (MES), enterprise resource planning (ERP) systems, and quality management systems (QMS) to enable end-to-end process optimization and data-driven decision making.
-
Cloud-based analytics: Development of cloud-based analytics platforms to enable remote monitoring, benchmarking, and collaboration across multiple manufacturing sites and supply chain partners.
By continuously innovating and expanding the capabilities of Rayming-reflow-pilot, Rayming aims to empower electronic manufacturers to stay ahead of the curve and achieve new levels of process excellence and product quality.
Frequently Asked Questions (FAQ)
-
Q: What types of reflow ovens are compatible with Rayming-reflow-pilot?
A: Rayming-reflow-pilot is designed to be compatible with a wide range of reflow ovens, including both convection and vapor phase systems. The system can be customized to fit the specific requirements of each oven and manufacturing process. -
Q: How long does it take to implement Rayming-reflow-pilot in a manufacturing facility?
A: The implementation time for Rayming-reflow-pilot varies depending on the complexity of the manufacturing process and the size of the facility. Typically, the entire process, from assessment to commissioning, can take between 4 to 8 weeks. However, Rayming works closely with manufacturers to minimize disruption and ensure a smooth transition. -
Q: What level of training is required for operators to use Rayming-reflow-pilot effectively?
A: Rayming provides comprehensive training for all operators and maintenance staff involved in the reflow soldering process. The training covers the operation, maintenance, and troubleshooting of the Rayming-reflow-pilot system, ensuring that the team is fully equipped to leverage the benefits of the technology. Typically, the training takes 1 to 2 days, depending on the size of the team and their existing knowledge of reflow soldering processes. -
Q: How does Rayming-reflow-pilot handle different product types and configurations?
A: Rayming-reflow-pilot is designed to be highly adaptable to different product types and configurations. The system’s advanced algorithms and sensing capabilities enable it to optimize the reflow process for each specific product, taking into account factors such as component density, board thickness, and material properties. This ensures that the system can handle a wide range of products without compromising on quality or efficiency. -
Q: What kind of support and maintenance services does Rayming offer for the Rayming-reflow-pilot system?
A: Rayming offers comprehensive support and maintenance services to ensure that the Rayming-reflow-pilot system continues to operate at peak performance. This includes regular software updates, remote monitoring, and on-site support as needed. Rayming’s team of experts is available to provide technical assistance, troubleshoot issues, and help manufacturers optimize their reflow processes over time. Additionally, Rayming offers customized maintenance contracts to meet the specific needs of each manufacturing facility.
Conclusion
Rayming-reflow-pilot represents a significant advancement in reflow soldering technology, enabling electronic manufacturers to achieve new levels of process control, efficiency, and product quality. By integrating advanced sensors, algorithms, and control mechanisms, Rayming-reflow-pilot optimizes the reflow process, minimizes defects, and enhances the reliability of electronic products.
As the electronic manufacturing industry continues to evolve, with increasing demands for miniaturization, higher performance, and greater reliability, Rayming-reflow-pilot provides a powerful tool for manufacturers to stay ahead of the curve. By partnering with Rayming and implementing this innovative technology, manufacturers can unlock new opportunities for growth, differentiation, and success in the highly competitive electronics market.
With its proven track record of success, comprehensive implementation process, and commitment to continuous innovation, Rayming-reflow-pilot is poised to revolutionize the electronic manufacturing landscape. As more and more manufacturers adopt this technology, we can expect to see significant improvements in the quality, reliability, and performance of electronic products across a wide range of industries, from consumer electronics to automotive, aerospace, and beyond.
Leave a Reply