What is PCB Prototyping?
PCB prototyping is the process of creating a physical representation of a circuit design for testing and validation purposes. It involves the fabrication of one or more copies of a PCB based on a digital design files, such as a schematic and PCB layout. PCB Prototypes allow engineers and makers to test their designs in real-world conditions, identify any issues or areas for improvement, and make necessary changes before committing to a full production run.
Benefits of PCB Prototyping
- Early detection of design flaws
- Opportunity for design optimization
- Reduced development time and costs
- Improved product quality and reliability
- Faster time-to-market
PCB Prototyping Processes
There are several methods for creating PCB prototypes, each with its own advantages and limitations. The choice of process depends on factors such as the complexity of the design, the required turnaround time, and the available budget.
1. Traditional PCB Fabrication
Traditional PCB fabrication involves the use of subtractive processes, such as etching and drilling, to create the conductive traces and holes on a copper-clad substrate. This method is suitable for producing high-quality prototypes with fine features and multiple layers. However, traditional PCB fabrication often requires longer lead times and higher costs compared to other prototyping methods.
2. Quick Turn PCB Fabrication
Quick turn PCB fabrication is a streamlined version of the traditional process, designed to reduce turnaround times and costs. This is achieved through the use of automated manufacturing equipment, standardized materials and processes, and optimized production workflows. Quick turn PCB fabrication is ideal for projects with tight deadlines and budget constraints, as well as for designs that require multiple iterations.
Advantages of Quick Turn PCB Fabrication
- Faster turnaround times (as low as 24 hours)
- Lower costs compared to traditional fabrication
- Suitable for simple to moderately complex designs
- Ideal for rapid prototyping and iteration
3. PCB Milling
PCB milling is a subtractive process that uses a computer-controlled milling machine to remove unwanted copper from a substrate, leaving behind the desired conductive traces. This method is suitable for creating simple to moderately complex PCB prototypes in-house, as it requires minimal setup and can be performed using readily available materials and equipment.
Advantages of PCB Milling
- Quick turnaround times (usually within a few hours)
- Low setup costs and minimal equipment requirements
- Ideal for simple to moderately complex designs
- Suitable for in-house prototyping and small-scale production
4. PCB Printing
PCB printing is an additive process that involves the deposition of conductive ink or paste onto a substrate to create the desired circuit patterns. This method is relatively new and is still evolving, but it shows promise for rapid prototyping and low-cost production of simple PCB designs.
Advantages of PCB Printing
- Very fast turnaround times (often within minutes)
- Low material costs and minimal waste
- Suitable for simple designs and low-volume production
- Potential for integration with other additive manufacturing processes
Considerations for PCB Prototyping
When embarking on a PCB prototyping project, there are several key factors to consider to ensure the best possible outcome:
-
Design complexity: The complexity of your PCB design will influence the choice of prototyping process, as well as the time and cost involved. Simple designs can often be prototyped using in-house methods like PCB milling, while more complex designs may require the use of quick turn or traditional PCB fabrication services.
-
Material selection: The choice of substrate material and copper weight will impact the performance and durability of your PCB prototype. Common substrate materials include FR-4, Rogers, and polyimide, each with its own unique properties and suitability for different applications.
-
Component availability: Ensure that all necessary components for your design are readily available and compatible with your chosen prototyping process. This includes considering factors such as package size, pitch, and temperature sensitivity.
-
Turnaround time: Consider the urgency of your project and choose a prototyping process that can meet your timeline requirements. Quick turn PCB fabrication and in-house methods like PCB milling often offer the fastest turnaround times.
-
Budget: Determine your project budget and select a prototyping process that fits within your financial constraints. Keep in mind that lower costs may sometimes come at the expense of quality or turnaround time.
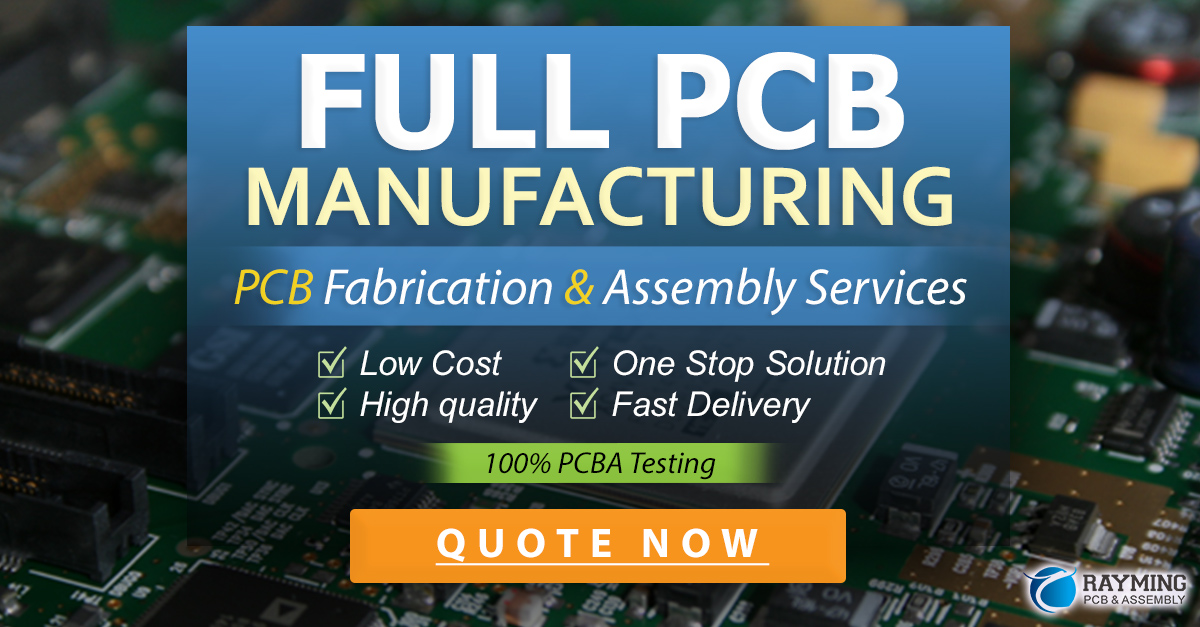
PCB Prototype Testing and Validation
Once your PCB prototypes have been fabricated, it is essential to thoroughly test and validate their functionality and performance. This process helps identify any design flaws or areas for improvement, allowing for necessary changes to be made before proceeding to full production.
1. Visual Inspection
Begin by visually inspecting your PCB prototypes for any obvious defects or inconsistencies, such as:
- Incomplete or broken traces
- Shorts or bridging between traces
- Incorrect component placement or orientation
- Damaged or missing components
2. Continuity and Resistance Testing
Use a multimeter to test the continuity and resistance of the various traces and connections on your PCB prototype. This helps identify any open circuits or unintended short circuits that could impact the functionality of your design.
3. Power-On Testing
Apply power to your PCB prototype and verify that it functions as intended. Use oscilloscopes, logic analyzers, and other test equipment to monitor the behavior of your circuit and identify any anomalies or unexpected results.
4. Environmental Testing
Subject your PCB prototypes to various environmental conditions, such as temperature extremes, humidity, and vibration, to assess their durability and reliability. This is particularly important for designs intended for use in harsh or demanding environments.
5. Iterative Refinement
Based on the results of your testing and validation, make any necessary changes or improvements to your PCB design. This may involve adjusting component values, modifying trace routing, or even redesigning certain aspects of your circuit. Repeat the prototyping and testing process until you are satisfied with the performance and reliability of your design.
Frequently Asked Questions (FAQ)
-
What is the difference between quick turn and traditional PCB fabrication?
Quick turn PCB fabrication is a streamlined version of the traditional process, designed to reduce turnaround times and costs through the use of automated manufacturing equipment and optimized production workflows. Traditional PCB fabrication often requires longer lead times and higher costs but is suitable for producing high-quality prototypes with fine features and multiple layers. -
Can I create PCB prototypes in-house?
Yes, PCB milling is a subtractive process that allows for the creation of simple to moderately complex PCB prototypes in-house using a computer-controlled milling machine. This method requires minimal setup and can be performed using readily available materials and equipment. -
What factors should I consider when choosing a PCB prototyping process?
When selecting a PCB prototyping process, consider factors such as design complexity, material selection, component availability, turnaround time, and budget. These factors will influence the suitability of different prototyping methods for your specific project. -
How important is testing and validation in the PCB prototyping process?
Testing and validation are critical steps in the PCB prototyping process, as they help identify design flaws, ensure functionality, and assess the durability and reliability of your PCB prototypes. Thorough testing and iterative refinement help ensure the success of your final product. -
What are the benefits of PCB prototyping?
PCB prototyping offers several benefits, including early detection of design flaws, opportunity for design optimization, reduced development time and costs, improved product quality and reliability, and faster time-to-market.
PCB Prototyping Process | Advantages | Limitations |
---|---|---|
Traditional PCB Fabrication | High-quality prototypes with fine features and multiple layers | Longer lead times and higher costs |
Quick Turn PCB Fabrication | Faster turnaround times, lower costs, suitable for simple to moderately complex designs | May not be suitable for highly complex designs |
PCB Milling | Quick turnaround times, low setup costs, ideal for simple to moderately complex designs | Limited to relatively simple designs, may require in-house equipment |
PCB Printing | Very fast turnaround times, low material costs, suitable for simple designs | Limited to simple designs, technology still evolving |
In conclusion, quick turn and fast PCB prototyping are essential tools for engineers and makers in today’s rapidly evolving electronics industry. By understanding the various prototyping processes, considering key factors, and thoroughly testing and validating designs, engineers and makers can create reliable, high-quality PCB prototypes that form the foundation for successful final products. As technology continues to advance, the importance of efficient and effective PCB prototyping will only continue to grow, making it a crucial skill for anyone involved in electronics design and development.
Leave a Reply