Introduction to Circuit Assembly
Circuit assembly is the process of connecting electronic components together to create a functional electronic circuit. It involves soldering components onto a printed circuit board (PCB) according to a specific design. The quality of the circuit assembly process is crucial for ensuring the reliability and performance of the final product.
In this comprehensive guide, we will cover the basics of circuit assembly, including the tools and materials required, the step-by-step process, and best practices for achieving high-quality results.
Key Components of Circuit Assembly
Before diving into the assembly process, it’s essential to understand the key components involved:
- Printed Circuit Board (PCB): The foundation of the circuit, providing a substrate for mounting and connecting components.
- Electronic Components: Including resistors, capacitors, diodes, transistors, and integrated circuits (ICs).
- Solder: A metal alloy used to create electrical and mechanical connections between components and the PCB.
- Flux: A chemical agent that helps to remove oxides and improve the flow of solder.
Tools and Materials Required for Circuit Assembly
To perform circuit assembly effectively, you’ll need the following tools and materials:
- Soldering Iron: A tool that heats up to melt solder and create connections between components and the PCB.
- Solder Wire: A thin wire made of a solder alloy, typically a combination of tin and lead or lead-free alternatives.
- Flux: Available in liquid or paste form, flux is applied to the PCB and components to improve solderability.
- Tweezers: Used for handling small components and precise placement on the PCB.
- Wire Cutters: Used for trimming component leads and cutting wires to the desired length.
- Magnifying Glass or Microscope: Helps with inspecting the quality of solder joints and identifying any defects.
- Isopropyl Alcohol and Lint-Free Wipes: Used for cleaning the PCB and components before and after soldering.
Choosing the Right Soldering Iron
Selecting the appropriate soldering iron is crucial for achieving quality solder joints. Consider the following factors when choosing a soldering iron:
- Wattage: A soldering iron with a wattage between 20-50 watts is suitable for most circuit assembly tasks.
- Temperature Control: Look for a soldering iron with adjustable temperature control to accommodate different types of solder and components.
- Tip Size and Shape: Choose a tip size and shape that matches the size of the components and the precision required for the job.
Step-by-Step Circuit Assembly Process
Follow these steps to assemble a circuit successfully:
- Preparation:
- Clean the PCB with isopropyl alcohol and lint-free wipes to remove any dirt or grease.
- Gather all the necessary components and tools.
-
Review the circuit schematic and assembly instructions.
-
Component Placement:
- Start with the lowest profile components, such as resistors and capacitors.
- Place the components according to the schematic, ensuring the correct orientation.
-
Bend the component leads to secure them in place.
-
Soldering:
- Apply a small amount of flux to the component leads and PCB pads.
- Heat the soldering iron to the appropriate temperature (typically between 300-400°C).
- Touch the solder wire to the tip of the iron and the component lead simultaneously, allowing the solder to melt and flow onto the joint.
- Remove the solder wire and the iron, and let the joint cool down naturally.
-
Repeat the process for all the components.
-
Inspection and Cleaning:
- Visually inspect each solder joint for quality, looking for a smooth, shiny, and concave appearance.
- Check for any bridging (unintended connections) between adjacent pads or traces.
-
Clean the PCB with isopropyl alcohol to remove any flux residue.
-
Testing and Troubleshooting:
- Power up the circuit and perform functionality tests to ensure it works as intended.
- If any issues are detected, use a multimeter or oscilloscope to troubleshoot and identify the problem.
- Rework any faulty solder joints or replace defective components as necessary.
Step | Description | Tools Required |
---|---|---|
1 | Preparation | Isopropyl alcohol, lint-free wipes |
2 | Component Placement | Tweezers |
3 | Soldering | Soldering iron, solder wire, flux |
4 | Inspection and Cleaning | Magnifying glass, isopropyl alcohol |
5 | Testing and Troubleshooting | Multimeter, oscilloscope |
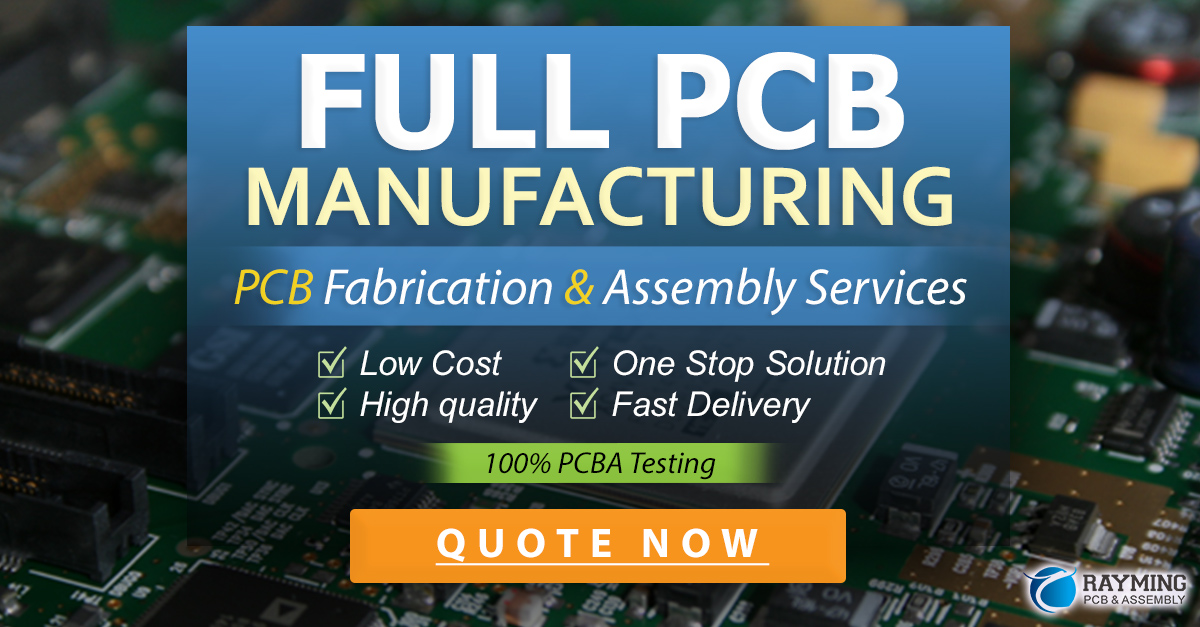
Best Practices for Quality Circuit Assembly
To ensure the highest quality of your circuit assembly, follow these best practices:
- Use high-quality components from reputable suppliers to minimize the risk of defects and failures.
- Follow the manufacturer’s recommendations for soldering temperature and duration to avoid damaging components or creating poor solder joints.
- Keep the soldering iron tip clean and well-tinned to ensure optimal heat transfer and prevent oxidation.
- Apply the appropriate amount of solder – enough to create a strong joint, but not so much that it creates bridging or excessive fillets.
- Work in a well-ventilated area and use a fume extractor to minimize exposure to solder fumes, which can be harmful to health.
- Practice proper electrostatic discharge (ESD) prevention techniques, such as wearing an ESD wrist strap and working on an ESD-safe mat, to protect sensitive components from static damage.
- Double-check component placement and orientation before soldering to avoid costly rework.
- Perform thorough visual inspections and functionality tests to catch any defects early in the process.
- Keep your workspace clean and organized to prevent contamination and improve efficiency.
- Continuously improve your skills and knowledge through training, workshops, and staying up-to-date with industry best practices.
Common Pitfalls to Avoid in Circuit Assembly
Be aware of these common pitfalls to ensure a smooth and successful circuit assembly process:
- Using the wrong solder type or flux for the application, which can lead to poor joint quality or component damage.
- Applying excessive heat or prolonged soldering times, causing component damage or Lifted Pads.
- Insufficient or excessive solder application, resulting in weak joints or bridging.
- Neglecting to clean the PCB and components before and after soldering, leading to contamination and reduced reliability.
- Rushing through the assembly process, increasing the likelihood of errors and defects.
Advanced Circuit Assembly Techniques
Once you’ve mastered the basics of circuit assembly, you may want to explore more advanced techniques:
- Surface Mount Technology (SMT): A method of assembling circuits using smaller components that are soldered directly onto the surface of the PCB, enabling higher component density and improved performance.
- Reflow Soldering: A process that involves applying solder paste to the PCB pads, placing components, and then heating the entire assembly in a reflow oven to melt the solder and create connections.
- Wave Soldering: An automated process that involves passing the PCB over a molten solder wave, which selectively solders through-hole components to the board.
- Rework and Repair: Techniques for removing and replacing faulty components, as well as repairing damaged PCBs.
- Automated Optical Inspection (AOI): Using machine vision systems to automatically inspect solder joints and component placement for defects.
Frequently Asked Questions (FAQ)
- What is the difference between lead-based and lead-free solder?
-
Lead-based solder contains a combination of tin and lead, typically in a 60/40 or 63/37 ratio. Lead-free solder, on the other hand, is made from a combination of tin, silver, and copper. Lead-free solder is becoming more popular due to environmental and health concerns associated with lead exposure.
-
How do I choose the right solder wire diameter?
-
The choice of solder wire diameter depends on the size of the components and the precision required for the job. For most through-hole components, a solder wire diameter of 0.8-1.0mm is suitable. For smaller or SMT components, a thinner solder wire (0.5-0.6mm) may be more appropriate.
-
What is the proper way to clean a soldering iron tip?
-
To clean a soldering iron tip, use a brass or stainless steel sponge dampened with distilled water. Wipe the tip gently on the sponge to remove any excess solder or debris. Alternatively, you can use a tip cleaner or tinner, which is a container filled with a special cleaning compound.
-
How can I prevent static damage to sensitive components during assembly?
-
To prevent electrostatic discharge (ESD) damage, take the following precautions:
- Wear an ESD wrist strap connected to a grounded point.
- Work on an ESD-safe mat or surface.
- Use ESD-safe storage containers for components.
- Avoid touching component leads or pins directly.
-
What should I do if I encounter a defective component during assembly?
- If you suspect a component is defective, first double-check its placement and orientation. If the issue persists, remove the component using desoldering techniques and replace it with a known good component. It’s essential to investigate the root cause of the defect to prevent recurrence in future assemblies.
Conclusion
Mastering the art of circuit assembly requires patience, practice, and attention to detail. By following the steps outlined in this guide and adhering to best practices, you can create high-quality, reliable electronic circuits. Remember to prioritize safety, invest in quality tools and materials, and continuously improve your skills. With dedication and experience, you’ll be well on your way to becoming a proficient circuit assembly technician.
Leave a Reply