Introduction to Solder Paste Volume for QFP Packages
Solder paste volume is a critical factor in the successful assembly of Quad Flat Package (QFP) components onto printed circuit boards (PCBs). Applying the correct amount of solder paste is essential for achieving reliable solder joints and ensuring the overall quality of the assembled product. In this article, we will explore the importance of solder paste volume for QFP packages and provide guidelines for determining the optimal Solder Volume.
What is Solder Paste?
Solder paste is a mixture of tiny solder particles suspended in a flux medium. It is used in surface mount technology (SMT) to form electrical and mechanical connections between electronic components and PCBs. The solder particles in the paste melt during the reflow soldering process, creating a reliable solder joint.
Composition of Solder Paste
Solder paste typically consists of the following components:
- Solder alloy particles (e.g., tin-lead, lead-free)
- Flux medium (e.g., rosin-based, water-soluble, no-clean)
- Additives (e.g., rheological modifiers, surfactants)
The solder alloy particles make up the bulk of the solder paste, while the flux medium helps to remove oxides, improve wetting, and protect the solder joint during the reflow process.
Importance of Solder Paste Volume for QFP Packages
Ensuring Reliable Solder Joints
Applying the correct volume of solder paste is crucial for creating reliable solder joints between QFP leads and PCB pads. Insufficient solder paste can result in open circuits or weak solder joints, while excessive solder paste can lead to bridging or solder balls.
Preventing Defects
Proper solder paste volume helps to prevent common assembly defects, such as:
- Solder bridges: Excessive solder paste can cause adjacent leads to be connected by solder.
- Solder balls: Excessive solder paste can result in the formation of small solder spheres that can cause short circuits.
- Insufficient solder joints: Inadequate solder paste can lead to weak or open solder joints.
Optimizing Manufacturing Yield
By maintaining the correct solder paste volume, manufacturers can improve the overall yield of their assembly process. Consistent solder paste application reduces the occurrence of defects, minimizing rework and scrap, and ultimately lowering production costs.
Factors Affecting Solder Paste Volume for QFP Packages
Stencil Design
The stencil used in the solder paste printing process plays a significant role in determining the solder paste volume. Factors to consider when designing a stencil for QFP packages include:
- Aperture size: The size of the stencil openings should match the size of the PCB pads, taking into account the lead pitch and package dimensions.
- Stencil thickness: Thicker stencils deposit more solder paste, while thinner stencils deposit less. The optimal stencil thickness depends on the package size and lead pitch.
- Aperture shape: The shape of the stencil openings can affect the solder paste volume and the resulting solder joint shape. Common aperture shapes include rectangles, circles, and home plates.
Solder Paste Properties
The properties of the solder paste itself can influence the deposited volume. Key factors include:
- Particle size distribution: The size and distribution of the solder particles in the paste affect its printing characteristics and the resulting solder volume.
- Viscosity: The viscosity of the solder paste determines its flow behavior and the amount of paste that can be deposited through the stencil apertures.
- Flux type: Different flux types (e.g., rosin-based, water-soluble, no-clean) can affect the solder paste’s printing and reflow performance.
Printing Process Parameters
The settings used during the solder paste printing process can impact the deposited solder volume. Important parameters include:
- Print speed: The speed at which the squeegee moves across the stencil can affect the amount of solder paste deposited.
- Squeegee pressure: The pressure applied by the squeegee during printing influences the solder paste volume and the print quality.
- Separation speed: The speed at which the PCB is separated from the stencil after printing can affect the solder paste volume and the occurrence of defects like solder bridges.
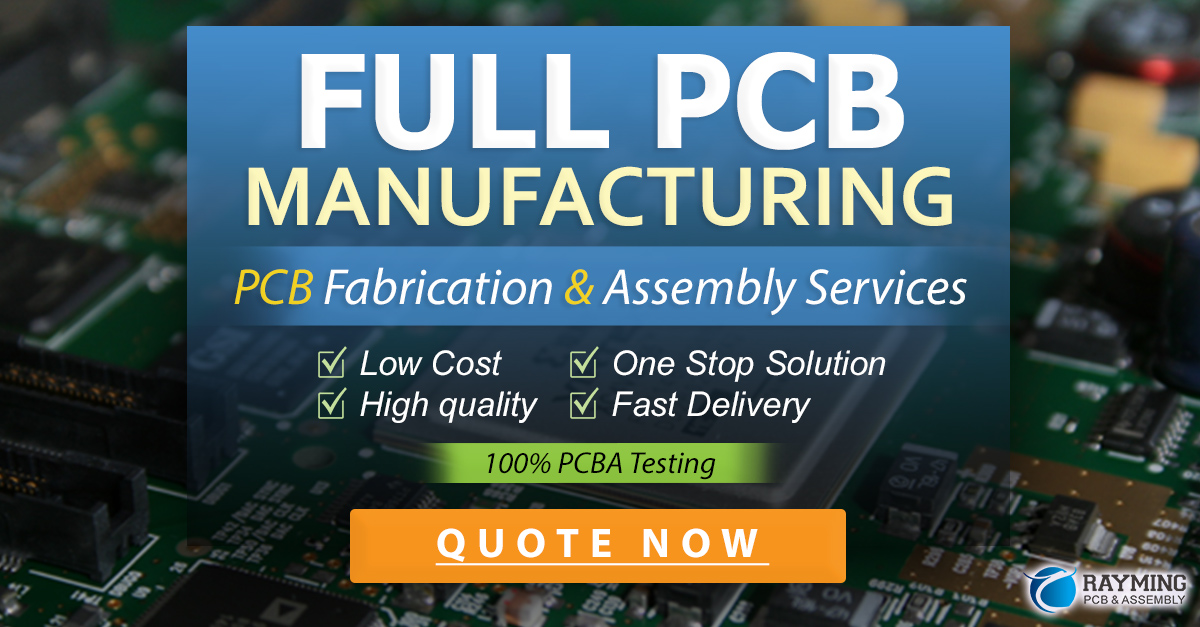
Calculating Solder Paste Volume for QFP Packages
To determine the appropriate solder paste volume for a QFP package, consider the following factors:
- Lead pitch: The distance between the centers of adjacent leads on the QFP package.
- Lead width: The width of the individual leads on the QFP package.
- PCB pad size: The dimensions of the copper pads on the PCB designed to accommodate the QFP leads.
- Stencil thickness: The thickness of the stencil used for solder paste printing.
The solder paste volume can be calculated using the following formula:
Solder Paste Volume = Stencil Thickness × PCB Pad Area
For example, consider a QFP package with a lead pitch of 0.5 mm, a lead width of 0.2 mm, and PCB pads measuring 0.3 mm × 0.6 mm. Using a stencil thickness of 0.1 mm, the solder paste volume for each pad would be:
Solder Paste Volume = 0.1 mm × (0.3 mm × 0.6 mm) = 0.018 mm³
It is essential to note that this is a simplified calculation, and factors such as the aperture shape and solder paste properties may influence the actual deposited volume.
Guidelines for Optimal Solder Paste Volume
To achieve the best results when applying solder paste for QFP packages, follow these guidelines:
-
Use a stencil thickness that is appropriate for the lead pitch and package size. A general rule of thumb is to use a stencil thickness that is 50-60% of the lead pitch.
-
Design stencil apertures that match the size and shape of the PCB pads, taking into account the lead pitch and package dimensions.
-
Select a solder paste with properties (e.g., particle size distribution, viscosity) that are suitable for the specific application and printing process.
-
Optimize the printing process parameters, such as print speed, squeegee pressure, and separation speed, to achieve consistent solder paste deposits.
-
Regularly inspect the printed solder paste deposits using visual inspection or automated solder paste inspection (SPI) systems to ensure consistency and identify any defects.
-
Monitor the reflow soldering process to ensure that the solder paste is properly melted and that the resulting solder joints are of acceptable quality.
Common Challenges and Solutions
Solder Bridging
Solder bridging occurs when excessive solder paste causes adjacent leads to be connected by solder. To prevent solder bridging:
- Reduce the stencil thickness or aperture size to decrease the solder paste volume.
- Increase the lead pitch or reduce the lead width to provide more space between adjacent leads.
- Optimize the printing process parameters to achieve consistent solder paste deposits.
Insufficient Solder Joints
Insufficient solder joints can occur when inadequate solder paste is deposited on the PCB pads. To address this issue:
- Increase the stencil thickness or aperture size to deposit more solder paste.
- Ensure that the stencil apertures are properly aligned with the PCB pads.
- Verify that the solder paste has the appropriate properties (e.g., viscosity, particle size distribution) for the application.
Solder Balls
Solder balls are small spheres of solder that can form when excessive solder paste is deposited or when the reflow process is not properly controlled. To minimize the occurrence of solder balls:
- Reduce the solder paste volume by adjusting the stencil thickness or aperture size.
- Optimize the reflow profile to ensure that the solder paste is fully melted and that the flux is properly activated.
- Use a solder paste with a compatible flux type and appropriate rheological properties.
Best Practices for Solder Paste Application
To ensure the best results when applying solder paste for QFP packages, consider the following best practices:
-
Use a high-quality solder paste that is suitable for the specific application and compatible with the printing process.
-
Implement a robust stencil design that takes into account the lead pitch, package dimensions, and PCB pad size.
-
Regularly maintain and clean the stencil to prevent clogging of the apertures and ensure consistent solder paste deposits.
-
Optimize the printing process parameters, such as print speed, squeegee pressure, and separation speed, to achieve consistent solder paste deposits.
-
Implement a quality control system that includes visual inspection, automated solder paste inspection (SPI), and post-reflow inspection to identify and address any defects.
-
Provide adequate training for operators involved in the solder paste printing process to ensure consistency and adherence to best practices.
Conclusion
Solder paste volume is a critical factor in the successful assembly of QFP packages onto PCBs. Applying the correct amount of solder paste is essential for creating reliable solder joints, preventing defects, and optimizing manufacturing yield. By understanding the factors that influence solder paste volume, such as stencil design, solder paste properties, and printing process parameters, manufacturers can implement best practices to ensure consistent and high-quality solder paste application.
Regular inspection, process optimization, and adherence to best practices can help to minimize common challenges such as solder bridging, insufficient solder joints, and solder balls. By carefully controlling the solder paste volume and implementing a robust quality control system, manufacturers can achieve reliable and cost-effective assembly of QFP packages.
FAQs
-
What is the recommended stencil thickness for QFP packages?
A general rule of thumb is to use a stencil thickness that is 50-60% of the lead pitch. For example, for a QFP package with a lead pitch of 0.5 mm, a stencil thickness of 0.25-0.30 mm would be appropriate. -
How can I prevent solder bridging when applying solder paste for QFP packages?
To prevent solder bridging, reduce the stencil thickness or aperture size to decrease the solder paste volume, increase the lead pitch or reduce the lead width to provide more space between adjacent leads, and optimize the printing process parameters to achieve consistent solder paste deposits. -
What should I do if I encounter insufficient solder joints?
If you encounter insufficient solder joints, increase the stencil thickness or aperture size to deposit more solder paste, ensure that the stencil apertures are properly aligned with the PCB pads, and verify that the solder paste has the appropriate properties (e.g., viscosity, particle size distribution) for the application. -
How can I minimize the occurrence of solder balls?
To minimize the occurrence of solder balls, reduce the solder paste volume by adjusting the stencil thickness or aperture size, optimize the reflow profile to ensure that the solder paste is fully melted and that the flux is properly activated, and use a solder paste with a compatible flux type and appropriate rheological properties. -
What are some best practices for applying solder paste for QFP packages?
Best practices for applying solder paste for QFP packages include using a high-quality solder paste that is suitable for the specific application, implementing a robust stencil design, regularly maintaining and cleaning the stencil, optimizing the printing process parameters, implementing a quality control system, and providing adequate training for operators involved in the solder paste printing process.
Factor | Influence on Solder Paste Volume |
---|---|
Stencil thickness | Thicker stencils deposit more solder paste, while thinner stencils deposit less |
Aperture size | Larger apertures deposit more solder paste, while smaller apertures deposit less |
Solder paste viscosity | Higher viscosity pastes deposit more solder paste, while lower viscosity pastes deposit less |
Print speed | Slower print speeds deposit more solder paste, while faster print speeds deposit less |
Squeegee pressure | Higher squeegee pressure deposits more solder paste, while lower pressure deposits less |
Leave a Reply