Key Components of a Professional Soldering Station
A complete professional bench-top soldering station typically includes the following main components:
- Soldering iron
- Soldering stand
- Power supply and temperature control unit
- Accessories (tips, sponges, fume extractor, etc.)
Let’s look at each of these in more detail.
Soldering Iron
The soldering iron is the most important part of the soldering station. Professional-grade Soldering Irons offer:
- High wattage (40-100W) for fast heat-up and recovery
- Precise temperature control and stability
- Lightweight, ergonomic handpieces for comfort during extended use
- Wide range of available tip shapes and sizes for different tasks
- ESD-safe designs to protect sensitive components
Some popular professional soldering iron brands include:
Brand | Model Examples |
---|---|
Weller | WE1010NA, WX2021, WXDP120 |
Hakko | FX-951, FX-888D, FM-203 |
JBC | CD-2BHE, CD-B, NANOTWEEZERS |
Metcal | MX-5200, MX-500 |
Pace | ADS200, WJS100 |
Soldering Stand
A good soldering stand keeps your iron safely stored, ready to use, and helps maintain the tip’s temperature when not in use. Key features include:
- Sturdy, weighted base for stability
- Adjustable cradle to securely hold irons of different sizes
- Integrated sponge or brass-wire tip cleaner
- Heat-resistant materials
Power Supply and Temperature Control Unit
The power supply provides the necessary electrical power to heat the soldering iron, while the temperature control unit allows precise adjustment and maintains a stable temperature. Important features include:
- Adjustable temperature range (200-450°C or 400-850°F)
- Digital temperature display for accuracy
- Fast heat-up and recovery times
- Low-voltage output for safety
- ESD-safe design
- Multiple iron support for versatility
Brand | Power Supply Examples |
---|---|
Weller | WE PS, WX PS |
Hakko | FH-200, FH-800, FP-1001 |
JBC | SFME-A, JTMPS |
Pace | ST-25, ST-75 |
Accessories
Various accessories enhance the functionality and convenience of the soldering station, including:
- Soldering tips in different shapes and sizes
- Brass or conventional sponges for tip cleaning
- Brass wool for tip cleaning and re-tinning
- Fume extractors for removing harmful fumes
- Tip thermometers for calibration
- Hot air pencils for SMD work
- Tweezers for handling small components
Choosing the Right Soldering Station
When selecting a professional bench-top soldering station for prototype work, consider the following factors:
- Soldering tasks and applications
- Budget and cost-performance balance
- Brand reputation and customer support
- Compatibility with existing tools and accessories
- Ease of use and maintenance
- Safety and ESD protection features
- Upgradeability and expansion options
Evaluate your specific needs and priorities to find the best fit for your prototyping requirements.
Setting Up and Using Your Soldering Station
Once you have chosen your soldering station, proper setup and use will ensure optimal performance and longevity. Key steps include:
- Read the manufacturer’s instructions and safety guidelines thoroughly.
- Choose an appropriate workspace with good ventilation, lighting, and ESD protection.
- Assemble and connect all components according to the instructions.
- Select the appropriate tip for your task and install it securely.
- Set the desired temperature and wait for the iron to heat up fully.
- Tin the tip with a small amount of solder to promote heat transfer and prevent oxidation.
- Always use the stand when the iron is not in use to protect the tip and work surface.
- Clean the tip regularly with a damp sponge or brass wool to remove excess solder and oxidation.
- Adjust the temperature as needed for different tasks and materials.
- Turn off and unplug the unit when not in use, allowing it to cool completely before storage.
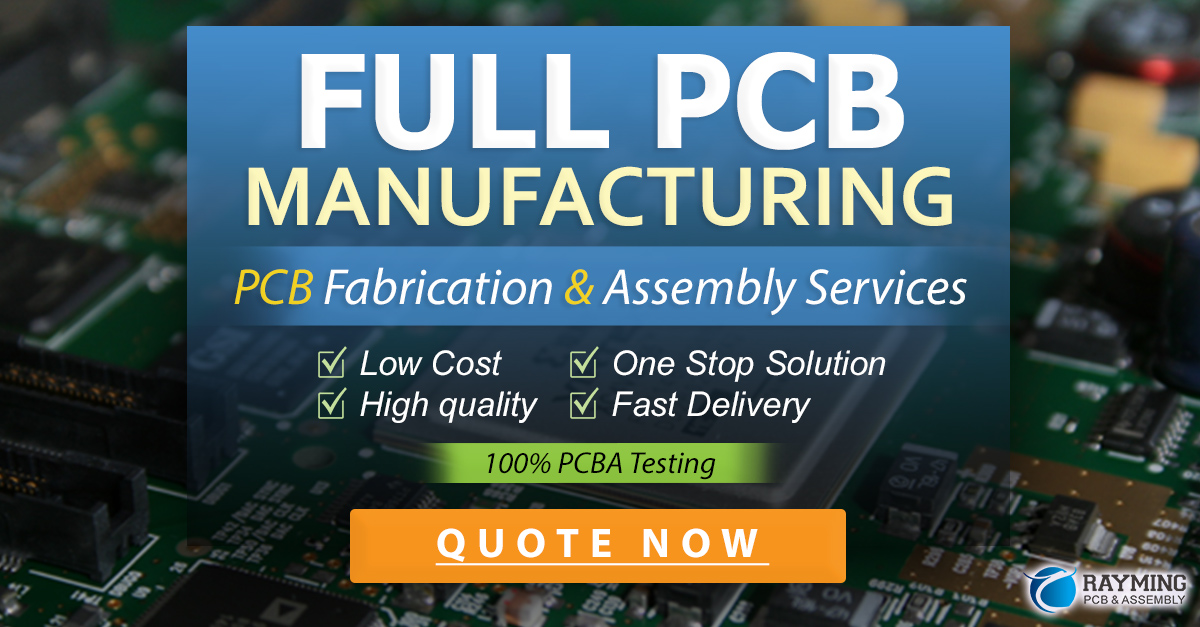
Soldering Techniques for Prototype Work
Effective Prototype Soldering requires mastering a few key techniques:
Tinning Wires and Leads
Before soldering, tin the component leads and wires by applying a small amount of solder. This promotes better heat transfer and faster, more reliable connections.
Applying the Right Amount of Solder
Use just enough solder to create a strong, conductive joint. Excessive solder can cause short circuits or impede heat transfer, while too little may result in weak or unreliable connections.
Maintaining Proper Tip Temperature
Different tasks and materials require specific temperature ranges for optimal results. Consult guides or manufacturer recommendations to determine the appropriate settings.
Material | Temperature Range |
---|---|
Leaded Solder | 300-380°C (572-716°F) |
lead-free solder | 360-420°C (680-788°F) |
Delicate Components | 270-350°C (518-662°F) |
Heavy Gauge Wires | 380-450°C (716-842°F) |
Using Flux
Flux helps remove oxidation, improves solder flow, and promotes stronger joints. Apply a small amount of rosin-core solder or a separate flux before soldering.
Keeping Tips Clean and Tinned
Regular cleaning and re-tinning of soldering tips maintain optimal heat transfer and prevent oxidation. Use a damp sponge or brass wool between joints and re-tin if needed.
Maintenance and Troubleshooting
Proper maintenance extends the life of your soldering equipment and ensures consistent performance:
- Inspect and clean tips regularly, replacing worn or damaged ones as needed.
- Keep the station and work area clean and organized to prevent damage or accidents.
- Periodically check cords and connections for wear or damage.
- Calibrate the temperature control unit if readings seem inaccurate.
- Replace sponges, brass wool, or other consumables as they become contaminated or degraded.
Common issues and troubleshooting tips:
Problem | Possible Causes | Solutions |
---|---|---|
No power | Loose connections, damaged cord | Check connections, replace cord |
Inaccurate temperature | Calibration drift, faulty sensor | Recalibrate, replace sensor |
Poor solder joints | Incorrect temp, dirty tip, flux | Adjust temp, clean tip, use flux |
Tip not heating | Loose connection, faulty element | Tighten connection, replace iron |
If problems persist, consult the manufacturer’s support resources or contact a professional for assistance.
Frequently Asked Questions (FAQ)
- What is the difference between lead-free and leaded solder?
Lead-free solder is an alloy that does not contain lead, typically consisting of tin, copper, and silver. It has a higher melting point and requires slightly different techniques compared to traditional leaded solder. Lead-free solder is becoming more common due to environmental and health concerns.
- How often should I replace my soldering tip?
Soldering tip life depends on factors such as usage frequency, maintenance, and the type of solder used. With proper care and cleaning, a high-quality tip can last for several months to a year. Replace tips when they become worn, pitted, or no longer hold a tinned surface well.
- Can I use the same soldering station for both through-hole and SMD work?
Yes, most professional soldering stations can handle both through-hole and surface-mount soldering tasks. However, SMD work often requires additional tools like tweezers, hot air pencils, or specialized tips. Some stations offer additional features or attachments specifically for SMD soldering.
- What safety precautions should I take when using a soldering station?
Always follow the manufacturer’s safety guidelines and use proper equipment. Work in a well-ventilated area to avoid inhaling fumes, and use a fume extractor if available. Wear safety glasses to protect your eyes from solder splatter. Handle hot components and tips with caution, and never touch them directly. Keep flammable materials away from the work area.
- How do I choose the right tip size and shape for my soldering tasks?
Tip selection depends on the size and type of components you’ll be soldering. Generally, choose a tip that is slightly larger than the pad or lead you’re soldering to maximize heat transfer. Conical or pencil tips are versatile for most tasks, while chisel tips are useful for larger components or wires. Consult tip selection charts or guides provided by the manufacturer.
Conclusion
Investing in professional bench-top prototype soldering equipment is crucial for creating high-quality, reliable electronic prototypes. By understanding the key components, features, and techniques involved in soldering, you can make informed decisions when selecting and using your soldering station. Remember to prioritize safety, maintain your equipment regularly, and practice proper techniques to achieve the best results in your prototype soldering projects.
Leave a Reply