What are PCB Layers?
PCB layers refer to the number of conductive copper layers that are stacked and laminated together to form a complete PCB. The number of layers in a PCB can vary depending on the complexity and requirements of the electronic circuit. The most common PCB layers are:
- Single-layer PCB
- Double-layer PCB
- Multi-layer PCB
Each layer serves a specific purpose in the overall functionality of the PCB, and the production process differs accordingly.
Single-Layer PCB Production Process
Single-layer PCBs, also known as single-sided PCBs, have conductive copper traces on only one side of the board. The production process for single-layer PCBs involves the following steps:
1. Substrate Preparation
The substrate, typically made of FR-4 (Flame Retardant 4) material, is cleaned and prepared for the subsequent processes. The substrate is cut to the desired size and shape using precise cutting machines.
2. Copper Cladding
A thin layer of copper foil is laminated onto the substrate using heat and pressure. The copper foil is usually pre-coated with a photoresist material, which is sensitive to light.
3. Photoresist Application
If the copper foil is not pre-coated with photoresist, a layer of photoresist is applied evenly onto the copper surface. The photoresist can be applied using various methods, such as spin coating or dry film lamination.
4. Exposure and Development
The PCB artwork, which contains the desired circuit pattern, is placed on top of the photoresist-coated copper layer. The artwork is then exposed to UV light, which hardens the photoresist in the exposed areas. The unexposed areas of the photoresist are then removed using a chemical developer solution, revealing the copper layer beneath.
5. Etching
The exposed copper areas are etched away using a chemical etching process, typically involving ferric chloride or ammonium persulfate. The remaining photoresist acts as a protective barrier, preventing the etching of the desired circuit pattern.
6. Photoresist Removal
After etching, the remaining photoresist is removed using a chemical stripper, leaving behind the copper traces that form the circuit pattern.
7. Drilling
Holes are drilled in the PCB to accommodate through-hole components and provide electrical connections between layers (if applicable). The drilling process is carried out using computer-controlled drill machines.
8. Surface Finishing
To protect the exposed copper traces from oxidation and enhance solderability, a surface finish is applied. Common surface finishes include:
- Hot Air Solder Leveling (HASL)
- Electroless Nickel Immersion Gold (ENIG)
- Immersion Silver
- Immersion Tin
- Organic Solderability Preservative (OSP)
9. Solder Mask Application
A solder mask, typically green in color, is applied over the PCB surface, leaving only the exposed pads and areas where components will be soldered. The solder mask provides insulation and protection to the copper traces.
10. Silkscreen Printing
The final step involves printing the component labels, logos, and other markings onto the PCB surface using silkscreen printing. This aids in the assembly process and provides clear identification of components.
Double-Layer PCB Production Process
Double-layer PCBs, also known as double-sided PCBs, have conductive copper traces on both sides of the board. The production process for double-layer PCBs is similar to that of single-layer PCBs, with a few additional steps:
1. Substrate Preparation
The substrate is prepared in the same manner as for single-layer PCBs, ensuring cleanliness and proper sizing.
2. Copper Cladding
Copper foil is laminated onto both sides of the substrate using heat and pressure.
3. Photoresist Application
Photoresist is applied to both sides of the copper-clad substrate, either through pre-coated copper foil or manual application.
4. Double-Sided Exposure and Development
The PCB artwork for both sides is aligned and exposed simultaneously using a double-sided exposure machine. The photoresist is then developed, revealing the desired circuit pattern on both sides.
5. Etching
The exposed copper areas on both sides are etched away using a chemical etching process.
6. Photoresist Removal
The remaining photoresist is removed from both sides using a chemical stripper.
7. Drilling
Holes are drilled through the PCB to accommodate through-hole components and provide electrical connections between the two layers.
8. Electroless Copper Deposition
To ensure electrical connectivity between the two layers, a thin layer of copper is deposited onto the walls of the drilled holes using an electroless copper deposition process.
9. Surface Finishing
A surface finish is applied to protect the exposed copper traces and enhance solderability, similar to the single-layer PCB process.
10. Solder Mask Application
A solder mask is applied to both sides of the PCB, leaving only the exposed pads and areas for component soldering.
11. Silkscreen Printing
The component labels, logos, and other markings are printed onto both sides of the PCB using silkscreen printing.
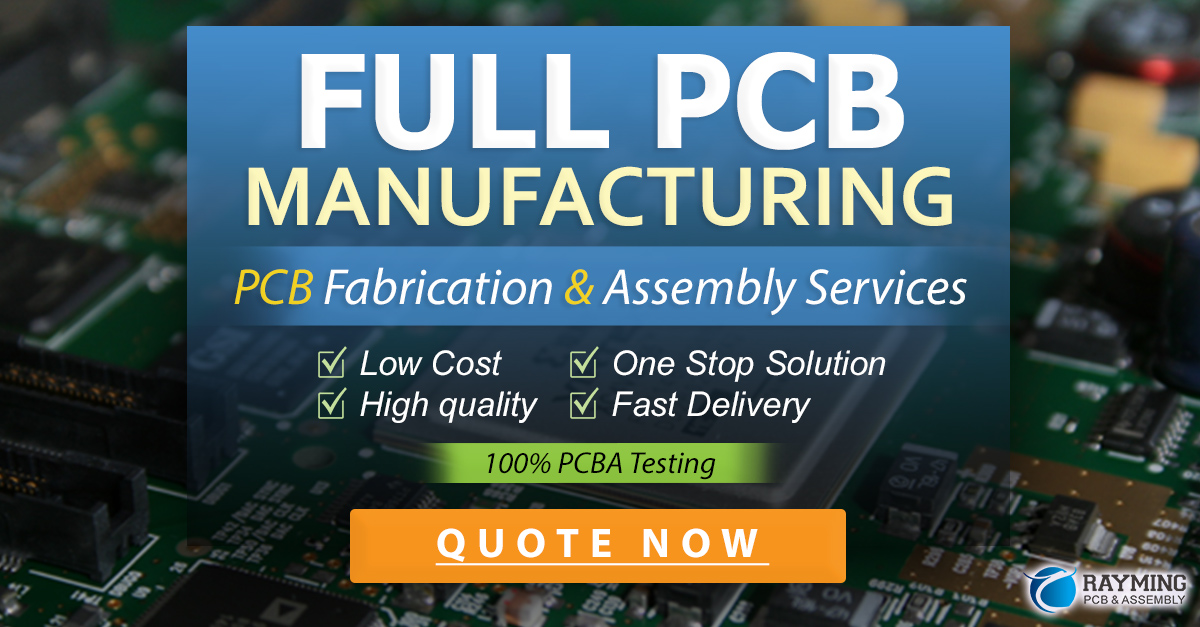
Multi-Layer PCB Production Process
Multi-layer PCBs consist of three or more conductive layers, allowing for higher component density and more complex circuit designs. The production process for multi-layer PCBs is more intricate and involves additional steps compared to single-layer and double-layer PCBs.
1. Inner Layer Production
The inner layers of the multi-layer PCB are produced separately, following a process similar to the single-layer PCB production. Each inner layer undergoes substrate preparation, copper cladding, photoresist application, exposure and development, etching, and photoresist removal.
2. Lamination
The inner layers are stacked and aligned with insulating layers, known as prepreg, between them. Copper foil is placed on the top and bottom of the stack to form the outer layers. The entire stack is then laminated together using heat and pressure in a lamination press.
3. Drilling
Holes are drilled through the laminated stack to accommodate through-hole components and provide electrical connections between layers. The drilling process is carried out using computer-controlled drill machines.
4. Electroless Copper Deposition
Similar to double-layer PCBs, a thin layer of copper is deposited onto the walls of the drilled holes using an electroless copper deposition process to ensure electrical connectivity between layers.
5. Outer Layer Production
The outer layers of the multi-layer PCB undergo a process similar to the double-layer PCB production, including photoresist application, exposure and development, etching, and photoresist removal.
6. Surface Finishing
A surface finish is applied to protect the exposed copper traces and enhance solderability, as in the single-layer and double-layer PCB processes.
7. Solder Mask Application
A solder mask is applied to both sides of the multi-layer PCB, leaving only the exposed pads and areas for component soldering.
8. Silkscreen Printing
The component labels, logos, and other markings are printed onto both sides of the PCB using silkscreen printing.
Comparison of PCB Layers
The choice of PCB layers depends on various factors, such as circuit complexity, component density, electrical requirements, and cost considerations. The following table provides a comparison of different PCB layers:
PCB Layer | Advantages | Disadvantages |
---|---|---|
Single-Layer | – Simple design – Low cost – Quick production time |
– Limited routing options – Lower component density – Not suitable for complex circuits |
Double-Layer | – Increased routing options – Higher component density – Suitable for moderately complex circuits |
– Higher cost than single-layer PCBs – Longer production time than single-layer PCBs |
Multi-Layer | – High component density – Ideal for complex circuits – Improved signal integrity – Reduced electromagnetic interference |
– Higher cost than single-layer and double-layer PCBs – Longer production time – More complex manufacturing process |
Frequently Asked Questions (FAQ)
-
What is the difference between a single-layer and double-layer PCB?
A single-layer PCB has conductive copper traces on only one side of the board, while a double-layer PCB has conductive copper traces on both sides of the board. Double-layer PCBs offer increased routing options and higher component density compared to single-layer PCBs. -
How many layers can a multi-layer PCB have?
A multi-layer PCB can have three or more conductive layers. The number of layers depends on the complexity of the circuit design and the specific requirements of the electronic device. Common multi-layer PCBs can have four, six, eight, or even more layers. -
What materials are used in PCB production?
The most common material used for PCB substrates is FR-4, which is a flame-retardant glass-reinforced epoxy laminate. Other materials include polyimide, PTFE (Teflon), and high-frequency laminates like Rogers. Copper foil is used for the conductive layers, and solder mask and silkscreen inks are used for protection and marking. -
What is the purpose of surface finishing in PCB production?
Surface finishing serves two main purposes in PCB production. First, it protects the exposed copper traces from oxidation and corrosion, extending the lifespan of the PCB. Second, it enhances the solderability of the PCB, ensuring better electrical connections when components are soldered onto the board. -
How does the complexity of the circuit design affect the choice of PCB layers?
The complexity of the circuit design is a crucial factor in determining the choice of PCB layers. Simple circuits with fewer components and routing requirements can be adequately accommodated on single-layer or double-layer PCBs. However, as the circuit complexity increases, with higher component density and more intricate routing, multi-layer PCBs become necessary to ensure proper functionality and signal integrity.
Conclusion
The production process for different layers of PCB involves a series of precise steps and techniques to create reliable and functional printed circuit boards. From single-layer to multi-layer PCBs, each type has its own specific production process, advantages, and considerations. Understanding the differences between PCB layers and their production processes is crucial for designers, engineers, and manufacturers to make informed decisions when developing electronic devices.
By selecting the appropriate PCB layer configuration based on the circuit complexity, component density, and electrical requirements, manufacturers can ensure optimal performance, reliability, and cost-effectiveness of their products. As technology advances and electronic devices become more sophisticated, the importance of understanding and mastering the production process for different layers of PCB will only continue to grow.
Leave a Reply