Introduction to Programmable IC Marking
Programmable integrated circuits (ICs) are widely used in various electronic applications due to their flexibility and customization capabilities. These ICs can be programmed to perform specific functions, making them versatile and adaptable to different design requirements. To ensure proper identification and traceability of programmable ICs, it is crucial to implement a standardized marking procedure. This article will discuss the procedure to define programmable IC marking, covering various aspects such as marking methods, content, and best practices.
Importance of Programmable IC Marking
Traceability and Quality Control
One of the primary reasons for implementing a standardized marking procedure for programmable ICs is to enable traceability and quality control. By applying unique identifiers to each IC, manufacturers can track the production process, identify batch numbers, and trace the origin of any issues or defects that may arise. This information is invaluable for root cause analysis and implementing corrective actions to improve product quality.
Inventory Management and Supply Chain Efficiency
Proper marking of programmable ICs also facilitates efficient inventory management and streamlines the supply chain process. With clear and consistent marking, IC manufacturers, distributors, and end-users can easily identify and track inventory levels, minimizing the risk of stockouts or excess inventory. This transparency in the supply chain reduces lead times, improves order fulfillment, and enhances overall operational efficiency.
Compliance with Industry Standards and Regulations
Many industries have specific standards and regulations that govern the marking of electronic components, including programmable ICs. These standards ensure consistency, interoperability, and safety across different applications and markets. By adhering to industry-specific marking requirements, IC manufacturers demonstrate compliance and gain access to broader market opportunities. Some examples of relevant standards include:
- JEDEC Solid State Technology Association Standards
- IPC-1752A: Materials Declaration Management
- IEC 61360: Standard data element types with associated classification scheme
- MIL-STD-130: Department of Defense Standard Practice for Identification Marking
Marking Methods for Programmable ICs
There are several methods used for marking programmable ICs, each with its advantages and considerations. The choice of marking method depends on factors such as IC package type, material, size, and the desired level of permanence and readability. Let’s explore some common marking methods:
Laser Marking
Laser marking is a popular and precise method for marking programmable ICs. It involves using a focused laser beam to create permanent marks on the IC package surface. Laser marking offers several benefits:
- High-speed and automated process
- Excellent readability and contrast
- Permanent and resistant to abrasion and chemicals
- Suitable for various package materials, including ceramic and plastic
- Enables marking of small and complex designs
However, laser marking requires specialized equipment and may have higher initial setup costs compared to other methods.
Ink Jet Marking
Ink jet marking utilizes a non-contact printing process to apply ink droplets onto the IC package surface. This method is known for its flexibility and cost-effectiveness. Key advantages of ink jet marking include:
- Fast and efficient marking process
- Ability to mark on various package materials and shapes
- Easy to change and update marking content
- Lower initial equipment costs compared to laser marking
Considerations for ink jet marking include the need for proper ink selection to ensure durability and the potential for smudging or fading over time.
Pad Printing
Pad printing is a contact-based marking method that transfers ink from an etched plate onto the IC package surface using a flexible silicone pad. This method is well-suited for marking on irregular surfaces and offers several benefits:
- Ability to mark on curved or recessed surfaces
- Consistent and high-quality prints
- Suitable for marking on various package materials
- Cost-effective for high-volume production
However, pad printing may have limitations in terms of minimum feature size and the need for periodic maintenance of the printing plates.
Labeling
Labeling involves attaching pre-printed labels or stickers onto the IC package surface. While this method is straightforward and cost-effective, it has some drawbacks:
- Limited durability and resistance to environmental factors
- Potential for labels to peel off or degrade over time
- May not be suitable for small IC packages or high-density designs
Labeling is often used for temporary marking or in applications where permanence is not a critical requirement.
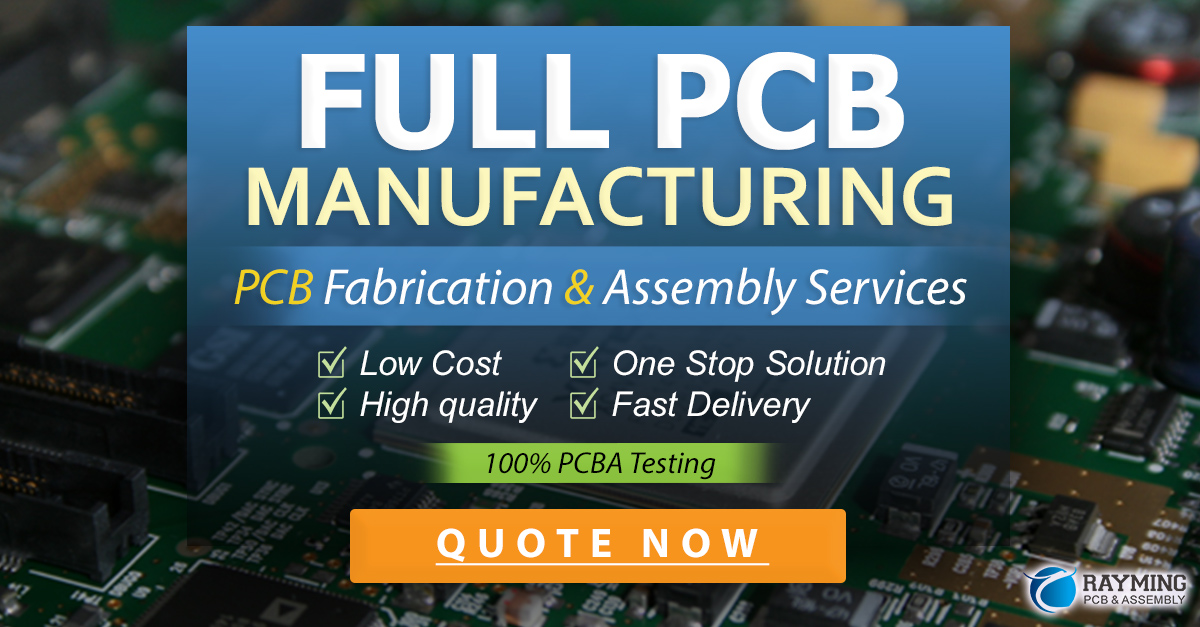
Marking Content and Format
When defining the marking content and format for programmable ICs, several key elements should be considered to ensure clarity, consistency, and compliance with industry standards. The following table outlines the recommended marking elements and their descriptions:
Marking Element | Description |
---|---|
Manufacturer Logo/Name | The logo or name of the IC manufacturer for brand identification |
Part Number | Unique identifier assigned by the manufacturer to designate the specific IC type and configuration |
Date Code | Indicates the manufacturing date of the IC, typically in the format YYWW (year and week) |
Lot Code | Identifier for the production batch or lot, enabling traceability |
Pin 1 Indicator | Designates the location of pin 1 for proper IC orientation during assembly |
Revision Code | Indicates the revision or version of the IC design |
Special Markings | Additional markings required by specific industries or applications, such as RoHS compliance or security features |
When designing the marking layout, consider the following best practices:
- Use clear and legible fonts with sufficient size for easy readability
- Ensure adequate spacing between marking elements to avoid confusion
- Follow industry-standard formats for date codes and lot codes
- Utilize machine-readable formats, such as barcodes or QR codes, for automated data capture
- Consider the available marking area on the IC package and optimize the layout accordingly
Quality Control and Verification
To maintain the integrity and reliability of programmable IC marking, it is essential to implement quality control measures and verification processes. Some key aspects of quality control include:
- Establishing standard operating procedures (SOPs) for the marking process
- Regularly calibrating and maintaining marking equipment
- Implementing automated vision systems for marking inspection and verification
- Conducting periodic audits to ensure compliance with marking standards and requirements
- Maintaining detailed records of marking data, including date codes, lot codes, and any deviations or non-conformances
By incorporating robust quality control measures, manufacturers can minimize the risk of marking errors, improve traceability, and ensure consistent marking quality across production batches.
Frequently Asked Questions (FAQ)
-
Q: What is the purpose of programmable IC marking?
A: The purpose of programmable IC marking is to provide clear identification and traceability of ICs throughout the product lifecycle. Marking enables quality control, inventory management, and compliance with industry standards and regulations. -
Q: Which marking method is best for programmable ICs?
A: The best marking method for programmable ICs depends on various factors, such as package type, material, size, and desired permanence. Laser marking is known for its precision and permanence, while ink jet marking offers flexibility and cost-effectiveness. The choice ultimately depends on specific application requirements and manufacturing constraints. -
Q: Are there any industry standards governing programmable IC marking?
A: Yes, several industry standards provide guidelines and requirements for IC marking, such as JEDEC standards, IPC-1752A, IEC 61360, and MIL-STD-130. These standards ensure consistency, interoperability, and compliance with specific industry regulations. -
Q: How can I ensure the quality and consistency of programmable IC marking?
A: To ensure the quality and consistency of programmable IC marking, implement robust quality control measures, including standard operating procedures, regular equipment maintenance, automated inspection systems, and periodic audits. Maintaining detailed records of marking data also helps in identifying and addressing any issues or non-conformances. -
Q: Can programmable ICs be remarked or relabeled?
A: Remarking or relabeling programmable ICs is generally not recommended, as it can compromise traceability and lead to confusion or errors. In some cases, such as product rework or counterfeit prevention, remarking may be necessary. However, it should be done in compliance with industry standards and with proper documentation to maintain the integrity of the marking information.
Conclusion
Defining a clear and standardized procedure for programmable IC marking is crucial for ensuring traceability, quality control, and compliance with industry standards. By selecting appropriate marking methods, defining comprehensive marking content, and implementing robust quality control measures, manufacturers can optimize their marking process and deliver reliable and traceable programmable ICs to their customers.
As technology advances and new applications emerge, the importance of programmable IC marking will only continue to grow. By staying informed about industry best practices and adapting marking procedures accordingly, manufacturers can stay competitive and meet the evolving demands of the market.
Leave a Reply