Introduction to Gold-Plated Connectors
Gold-plated connectors are essential components in various electronic devices, offering superior conductivity, corrosion resistance, and durability compared to other connector types. These connectors are widely used in applications where reliable electrical connections are critical, such as in telecommunications, aerospace, and medical equipment.
What are Gold-Plated Connectors?
Gold-plated connectors are electrical connectors that have a thin layer of gold applied to their contact surfaces. The gold plating provides several benefits, including:
- Excellent conductivity
- Resistance to corrosion and oxidation
- Low contact resistance
- Improved signal integrity
- Enhanced durability and longevity
Advantages of Using Gold-Plated Connectors
Gold-plated connectors offer several advantages over other connector types:
- Reliability: Gold-plated connectors provide a more reliable electrical connection due to their resistance to corrosion and oxidation.
- Signal Integrity: The low contact resistance of gold-plated connectors helps maintain signal integrity, reducing signal loss and distortion.
- Durability: Gold-plated connectors can withstand frequent mating cycles and harsh environmental conditions, making them ideal for applications that require long-term reliability.
- Compatibility: Gold-plated connectors are compatible with a wide range of materials, including other precious metals and base metals.
Types of Gold-Plated Connectors
There are several types of gold-plated connectors available, each designed for specific applications and requirements.
Edge Connectors
Edge connectors are commonly used in printed circuit boards (PCBs) to establish electrical connections between the board and other components or devices. Gold-Plated Edge Connectors offer several benefits:
- Improved contact reliability
- Reduced insertion force
- Enhanced durability
- Resistance to corrosion and oxidation
Board-to-Board Connectors
Board-to-board connectors are used to establish electrical connections between two PCBs. Gold-plated board-to-board connectors provide several advantages:
- Low contact resistance
- High current carrying capacity
- Improved signal integrity
- Enhanced durability and reliability
Wire-to-Board Connectors
Wire-to-board connectors are used to establish electrical connections between wires and PCBs. Gold-plated wire-to-board connectors offer several benefits:
- Reliable electrical connections
- Resistance to corrosion and oxidation
- Improved signal integrity
- Enhanced durability and longevity
RF Connectors
Radio frequency (RF) connectors are used in high-frequency applications, such as telecommunications and wireless devices. Gold-plated RF connectors provide several advantages:
- Low insertion loss
- High isolation
- Improved signal integrity
- Enhanced durability and reliability
Gold Plating Processes
There are several gold plating processes used in the production of gold-plated connectors, each with its own advantages and disadvantages.
Electroplating
Electroplating is the most common method used for gold plating connectors. In this process, an electric current is applied to a gold solution, causing the gold ions to adhere to the surface of the connector. Electroplating offers several benefits:
- Uniform coating thickness
- High deposition rate
- Cost-effective for large-scale production
- Ability to plate complex shapes and geometries
Electroless Plating
Electroless plating is a chemical process that deposits a thin layer of gold onto the surface of the connector without the use of an electric current. This process offers several advantages:
- Uniform coating thickness, even on complex shapes
- No electrical contact required
- Ability to plate non-conductive surfaces
- Improved corrosion resistance
Immersion Plating
Immersion plating is a simple process that involves immersing the connector in a gold solution, allowing the gold to adhere to the surface through a chemical reaction. Immersion plating offers several benefits:
- Low cost compared to other plating methods
- No electrical contact required
- Ability to plate non-conductive surfaces
- Uniform coating thickness
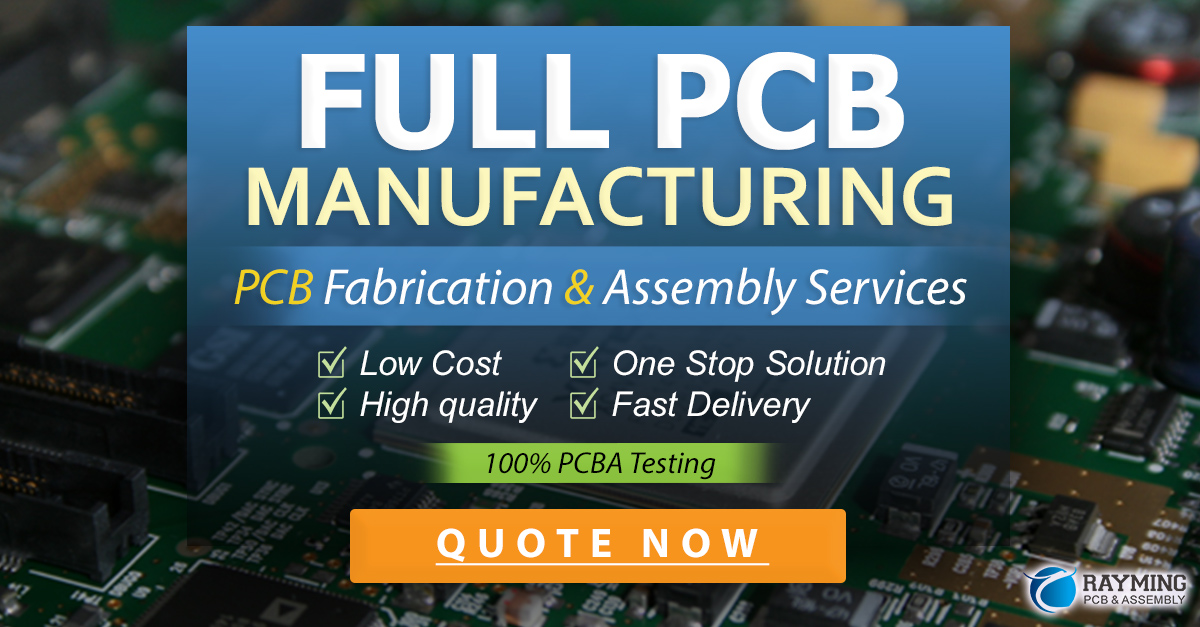
Gold Plating Thickness
The thickness of the gold plating on a connector is an essential factor in determining its performance and durability. The following table outlines the typical gold plating thicknesses used in various applications:
Application | Typical Gold Plating Thickness |
---|---|
Consumer electronics | 0.05 – 0.2 µm |
Industrial electronics | 0.2 – 0.5 µm |
Telecommunications | 0.5 – 1.0 µm |
Aerospace and military | 1.0 – 2.0 µm |
Extreme environments | 2.0 – 5.0 µm |
Factors Affecting Gold Plating Thickness
Several factors can affect the required gold plating thickness for a given application:
- Environmental conditions: Connectors exposed to harsh environments, such as high humidity, corrosive gases, or extreme temperatures, may require thicker gold plating for added protection.
- Mating cycles: Connectors subjected to frequent mating and unmating may require thicker gold plating to withstand wear and maintain reliable electrical connections.
- Signal integrity: Applications that demand high signal integrity, such as high-frequency or low-level signal transmission, may require thicker gold plating to minimize contact resistance and signal loss.
- Cost considerations: Thicker gold plating increases the overall cost of the connector, so a balance must be struck between performance requirements and cost-effectiveness.
Testing and Quality Control
To ensure the reliability and performance of gold-plated connectors, various testing and quality control measures are employed during the manufacturing process.
Visual Inspection
Visual inspection is the first step in quality control, involving a thorough examination of the connector for any visible defects or inconsistencies in the gold plating. This may include:
- Checking for uniform coverage and thickness
- Identifying any pinholes, cracks, or blisters in the plating
- Verifying the correct color and appearance of the gold plating
Adhesion Testing
Adhesion testing is performed to ensure that the gold plating is properly bonded to the base material of the connector. Common adhesion testing methods include:
- Tape test: A pressure-sensitive tape is applied to the plated surface and then removed, checking for any plating that adheres to the tape.
- Scratch test: A diamond-tipped stylus is used to create a scratch on the plated surface, and the adhesion is evaluated based on the width and appearance of the scratch.
- Heat test: The connector is subjected to elevated temperatures to check for any blistering or delamination of the gold plating.
Contact Resistance Testing
Contact resistance testing is conducted to measure the electrical resistance between the gold-plated contacts of the connector. Low contact resistance is essential for maintaining signal integrity and minimizing power loss. Contact resistance testing may be performed using a four-wire measurement technique or a specialized contact resistance tester.
Environmental Testing
Environmental testing is carried out to evaluate the performance and durability of gold-plated connectors under various environmental conditions. This may include:
- Temperature cycling: Connectors are subjected to alternating high and low temperatures to assess their ability to withstand thermal stress.
- Humidity testing: Connectors are exposed to high humidity levels to check for corrosion resistance and any changes in contact resistance.
- Salt spray testing: Connectors are exposed to a salt spray environment to evaluate their resistance to corrosion and oxidation.
- Vibration and shock testing: Connectors are subjected to mechanical stress to ensure they can maintain reliable electrical connections under dynamic conditions.
Applications of Gold-Plated Connectors
Gold-plated connectors find applications in a wide range of industries and devices, where reliable electrical connections and high performance are critical.
Consumer Electronics
Gold-plated connectors are used in various consumer electronic devices, such as:
- Smartphones and tablets
- Laptops and computers
- Gaming consoles and controllers
- Audio and video equipment
In these applications, gold-plated connectors help ensure reliable data transfer, charging, and audio/video connectivity.
Industrial Electronics
Industrial electronics often require connectors that can withstand harsh environments and maintain reliable performance over extended periods. Gold-plated connectors are used in:
- Industrial control systems
- Automation equipment
- Test and measurement devices
- Power electronics
The corrosion resistance and durability of gold-plated connectors make them well-suited for industrial applications.
Telecommunications
Gold-plated connectors are essential in telecommunications equipment, where high-frequency signal transmission and low signal loss are critical. Applications include:
- Base stations and antennas
- Fiber optic systems
- Satellite communications
- Networking equipment
The low contact resistance and high signal integrity provided by gold-plated connectors help ensure reliable and efficient telecommunications.
Aerospace and Military
Aerospace and military applications demand connectors that can withstand extreme environmental conditions and maintain reliable performance. Gold-plated connectors are used in:
- Aircraft avionics
- Satellite systems
- Radar and surveillance equipment
- Military communication devices
The enhanced durability and corrosion resistance of gold-plated connectors make them ideal for these demanding applications.
Medical Devices
Medical devices require connectors that are reliable, durable, and biocompatible. Gold-plated connectors are used in:
- Diagnostic equipment
- Patient monitoring systems
- Surgical instruments
- Implantable devices
The biocompatibility and corrosion resistance of gold make gold-plated connectors suitable for use in medical devices.
Frequently Asked Questions (FAQ)
- Q: What is the difference between gold-plated and gold-flashed connectors?
A: Gold-plated connectors have a thicker layer of gold, typically 0.5 micrometers or more, while gold-flashed connectors have a much thinner layer, usually less than 0.1 micrometers. Gold-plated connectors offer better durability, corrosion resistance, and performance compared to gold-flashed connectors.
- Q: Can gold-plated connectors be soldered?
A: Yes, gold-plated connectors can be soldered, but it is essential to use the correct soldering techniques and temperature to avoid damaging the gold plating. Excessive heat or prolonged exposure to high temperatures can cause the gold plating to dissolve or diffuse into the solder, leading to reduced performance and reliability.
- Q: How do I clean gold-plated connectors?
A: To clean gold-plated connectors, use a soft, lint-free cloth or a brush with soft bristles. Gently wipe the contacts to remove any dirt, dust, or debris. If necessary, you can use isopropyl alcohol to remove stubborn contaminants. Avoid using abrasive materials or excessive force, as this can damage the gold plating.
- Q: Can gold-plated connectors be used in high-voltage applications?
A: Gold-plated connectors can be used in high-voltage applications, but the thickness of the gold plating and the design of the connector must be appropriate for the specific voltage and current requirements. Thicker gold plating may be necessary to withstand the increased electrical stress and prevent damage to the contacts.
- Q: How long do gold-plated connectors last?
A: The lifespan of gold-plated connectors depends on various factors, such as the thickness of the gold plating, the environmental conditions, and the number of mating cycles. In general, gold-plated connectors can last for several years or even decades with proper maintenance and usage. However, in extreme environments or applications with frequent mating cycles, the gold plating may wear down over time, requiring the connectors to be replaced.
Conclusion
Gold-plated connectors are essential components in a wide range of electronic devices and applications, offering superior conductivity, corrosion resistance, and durability. By understanding the different types of gold-plated connectors, gold plating processes, and quality control measures, engineers and designers can select the most appropriate connectors for their specific requirements.
As technology continues to advance, the demand for reliable and high-performance connectors will only increase. Gold-plated connectors will continue to play a crucial role in ensuring the proper functioning and longevity of electronic devices across various industries, from consumer electronics to aerospace and medical applications.
Leave a Reply