What is a Placer-CAM?
A Placer camera-assisted manual (CAM) pick and place machine, also known as a Placer-CAM, is a type of assembly machine used in electronics manufacturing to accurately place small electronic components onto printed circuit boards (PCBs). These machines combine the precision of computer vision with the flexibility of manual operation to enable efficient, high-quality placement of components.
Key Features of Placer-CAMs
- Camera-assisted alignment
- Manual operation
- Compact size
- Versatility
- Cost-effectiveness
Placer-CAMs utilize a camera system to provide a magnified view of the PCB and components, allowing the operator to precisely align and place parts. The camera feed is displayed on a monitor, often with overlay guides and digital zoom capabilities to assist with accuracy.
Unlike fully automated pick and place machines, Placer-CAMs rely on a human operator to manually pick up components and place them onto the PCB. This manual operation provides greater flexibility to handle a wide variety of part types, sizes, and packaging formats without the need for extensive programming or tooling changes.
Benefits of Using a Placer-CAM
1. Improved Accuracy
One of the primary advantages of using a Placer-CAM is the significant improvement in placement accuracy compared to purely manual methods. The camera system provides a clear, magnified view of the PCB and components, enabling the operator to precisely align parts with the solder pads or other reference markers.
Placement Method | Typical Accuracy |
---|---|
Manual placement (unaided) | ±0.5mm |
Placer-CAM assisted placement | ±0.1mm |
Fully automated pick and place | ±0.05mm |
As seen in the table above, Placer-CAMs offer a substantial improvement in accuracy over unaided manual placement, approaching the precision of fully automated systems.
2. Increased Efficiency
While Placer-CAMs require manual operation, they still offer significant efficiency gains compared to traditional hand placement methods. The camera-assisted alignment allows operators to work more quickly and confidently, reducing the time spent on each component.
Additionally, many Placer-CAMs feature built-in component feeders or trays, which organize and present parts to the operator in a convenient manner. This helps to minimize the time spent searching for and handling components, further boosting overall efficiency.
3. Versatility
Another key benefit of Placer-CAMs is their versatility. Unlike fully automated machines, which require specific programming and tooling for each unique part, Placer-CAMs can easily accommodate a wide range of component types and sizes without extensive setup time.
This flexibility makes Placer-CAMs particularly well-suited for low-volume, high-mix production environments, such as prototyping, small batch runs, or contract manufacturing. Operators can quickly switch between different components and PCBs without the need for time-consuming changeovers.
4. Cost-Effectiveness
Placer-CAMs offer a cost-effective solution for manufacturers who need to improve their assembly processes but may not have the volume or resources to justify investing in fully automated equipment.
Compared to manual placement, Placer-CAMs can significantly reduce labor costs by increasing operator efficiency and reducing the need for rework due to placement errors. At the same time, they are typically much less expensive than fully automated pick and place machines, making them an attractive option for smaller operations or those with limited budgets.
Applications of Placer-CAMs
Placer-CAMs are used in a variety of electronics manufacturing applications, including:
- Prototype and small batch PCB Assembly
- High-mix, low-volume production
- Contract manufacturing
- Educational and research institutions
- Hobbyist and DIY Electronics projects
Prototype and Small Batch PCB Assembly
Placer-CAMs are an ideal solution for prototyping and small batch PCB assembly, where the speed and setup time of fully automated machines may not be justified. The versatility and quick changeover capabilities of Placer-CAMs allow manufacturers to efficiently produce a variety of prototype designs or small production runs without extensive programming or tooling changes.
High-Mix, Low-Volume Production
In high-mix, low-volume production environments, manufacturers must be able to quickly adapt to changing product designs and component requirements. Placer-CAMs excel in these situations, as they can easily accommodate a wide range of part types and sizes without the need for time-consuming setup procedures.
This flexibility enables manufacturers to efficiently produce a diverse range of products in smaller quantities, meeting the demands of customers with rapidly changing needs or niche markets.
Contract Manufacturing
Contract manufacturers often face the challenge of balancing the diverse requirements of multiple clients while maintaining efficiency and profitability. Placer-CAMs can be a valuable tool in these situations, allowing contract manufacturers to quickly switch between different projects and component types without extensive downtime.
The improved accuracy and efficiency provided by Placer-CAMs also help contract manufacturers to deliver high-quality products to their clients while controlling labor costs and minimizing the need for rework.
Educational and Research Institutions
Placer-CAMs are well-suited for use in educational and research settings, where students and researchers may need to assemble a variety of PCBs for projects or experiments. The ease of use and versatility of Placer-CAMs make them accessible to users with varying levels of experience, while the improved accuracy and efficiency help to ensure successful outcomes.
Additionally, the relatively low cost of Placer-CAMs compared to fully automated equipment makes them a more feasible investment for educational institutions and research laboratories with limited budgets.
Hobbyist and DIY Electronics Projects
For hobbyists and DIY enthusiasts, Placer-CAMs offer a way to significantly improve the quality and efficiency of their electronics projects. The camera-assisted alignment and magnified view of the PCB make it easier for hobbyists to work with small components and achieve professional-looking results.
Moreover, the compact size and relatively affordable price point of many Placer-CAMs make them a practical addition to a home workshop or electronics lab.
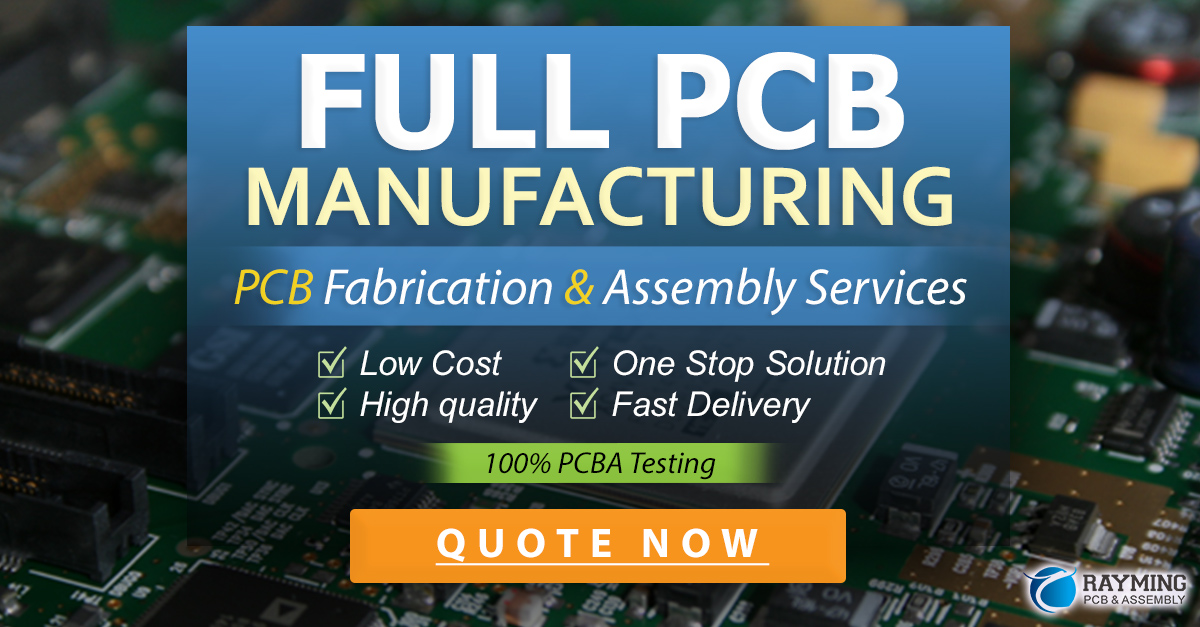
Choosing the Right Placer-CAM
When selecting a Placer-CAM for your manufacturing needs, consider the following factors:
- Camera system quality
- Magnification and field of view
- Lighting options
- Component handling capabilities
- Software features and ease of use
- Ergonomics and operator comfort
- Price and total cost of ownership
Camera System Quality
The quality of the camera system is a critical factor in the performance of a Placer-CAM. Look for machines with high-resolution cameras that provide clear, detailed images of the PCB and components. Some systems may also offer additional features, such as digital zoom, image capture, or video recording capabilities.
Magnification and Field of View
Consider the magnification level and field of view offered by the Placer-CAM’s camera system. Higher magnification levels allow for more precise alignment of small components, while a larger field of view can help to improve overall efficiency by reducing the need for frequent PCB movement.
Lighting Options
Proper lighting is essential for accurate component placement. Look for Placer-CAMs with adjustable lighting options, such as brightness control or selectable light colors, to ensure optimal visibility for a variety of component types and PCB Finishes.
Component Handling Capabilities
Evaluate the Placer-CAM’s component handling capabilities, including the types of feeders or trays available, the maximum and minimum component sizes accommodated, and the ease of loading and unloading components. Some machines may also offer features like vacuum pickup tools or adjustable grip pressure to handle delicate or irregularly shaped parts.
Software Features and Ease of Use
Consider the software features and user interface of the Placer-CAM. Look for systems with intuitive controls, customizable settings, and helpful features like on-screen guides or overlays. Some machines may also offer more advanced capabilities, such as data logging, performance tracking, or integration with other manufacturing software.
Ergonomics and Operator Comfort
Operator comfort is an important factor to consider, as it can impact both productivity and employee satisfaction. Look for Placer-CAMs with ergonomic features, such as adjustable workstation height, comfortable hand rests, or low-force placement mechanisms. Good ergonomics can help to reduce operator fatigue and minimize the risk of repetitive strain injuries.
Price and Total Cost of Ownership
Finally, consider the price and total cost of ownership when choosing a Placer-CAM. While the upfront cost is an important factor, also take into account the long-term costs, such as maintenance, consumables, and operator training. Look for machines that offer a balance of performance, durability, and value to ensure the best return on your investment.
Frequently Asked Questions (FAQ)
1. What is the difference between a Placer-CAM and a fully automated pick and place machine?
A Placer-CAM is a semi-automated machine that combines computer vision with manual operation. The operator manually picks and places components onto the PCB, using the camera system for precise alignment. In contrast, a fully automated pick and place machine uses robotic arms and pre-programmed commands to place components without human intervention.
2. Can a Placer-CAM handle all types of electronic components?
Placer-CAMs are highly versatile and can handle a wide range of component types and sizes, including through-hole and surface-mount devices. However, some machines may have limitations on the minimum or maximum component size they can accommodate. It’s important to review the specifications of a particular Placer-CAM model to ensure it meets your specific component handling requirements.
3. How much training is required to operate a Placer-CAM?
Placer-CAMs are generally easier to learn and operate compared to fully automated pick and place machines. Most operators can become proficient with a Placer-CAM after a short training period, typically ranging from a few hours to a few days, depending on their prior experience and the complexity of the machine.
4. What is the typical accuracy of a Placer-CAM?
Placer-CAMs typically offer placement accuracy of around ±0.1mm, which is a significant improvement over unaided manual placement. However, the actual accuracy achieved may vary depending on factors such as the quality of the camera system, operator skill, and component characteristics.
5. Are Placer-CAMs suitable for high-volume production?
While Placer-CAMs can significantly improve efficiency compared to manual placement methods, they are generally not as fast as fully automated pick and place machines. As a result, Placer-CAMs are best suited for low to medium-volume production, prototyping, or high-mix environments where flexibility is more important than raw speed.
Conclusion
Placer camera-assisted manual pick and place machines, or Placer-CAMs, offer a versatile and cost-effective solution for electronics manufacturers looking to improve the accuracy and efficiency of their assembly processes. By combining the precision of computer vision with the flexibility of manual operation, Placer-CAMs enable operators to place a wide range of components quickly and accurately.
Whether you’re involved in prototyping, small batch production, contract manufacturing, education, or hobby electronics, a Placer-CAM can be a valuable addition to your assembly lineup. When choosing a Placer-CAM, consider factors such as camera quality, component handling capabilities, software features, ergonomics, and total cost of ownership to ensure you select a machine that meets your specific needs and budget.
As technology continues to advance, it’s likely that Placer-CAMs will become even more capable and user-friendly, further cementing their role as an essential tool in the electronics manufacturing landscape.
Leave a Reply